Manufacturing simulation: how it works and why you should do it?
Manufacturing simulation is the technology to model, experiment, and optimize your production process using digital models of your manufacturing environment.
Why simulate manufacturing processes?
When you physically reorganize your processes, add new equipment, or upgrade your workflow, you may disrupt production schedules, inflate expenses, and cause systematic disarray. Save time and production costs by addressing all the possible expensive mistakes you can where it should happen – on the planning table with manufacturing simulation!
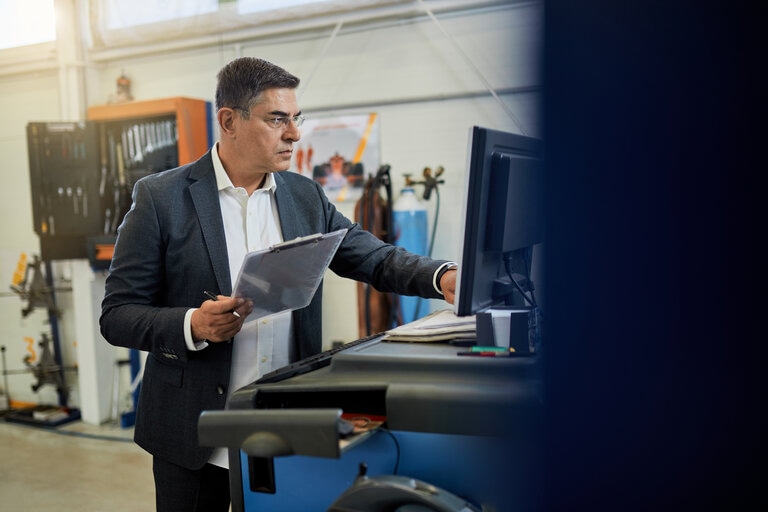
Eliminate decision fatigue for production managers
Get data-driven insights by analyzing the performance of various production scenarios under different conditions before implementing them.
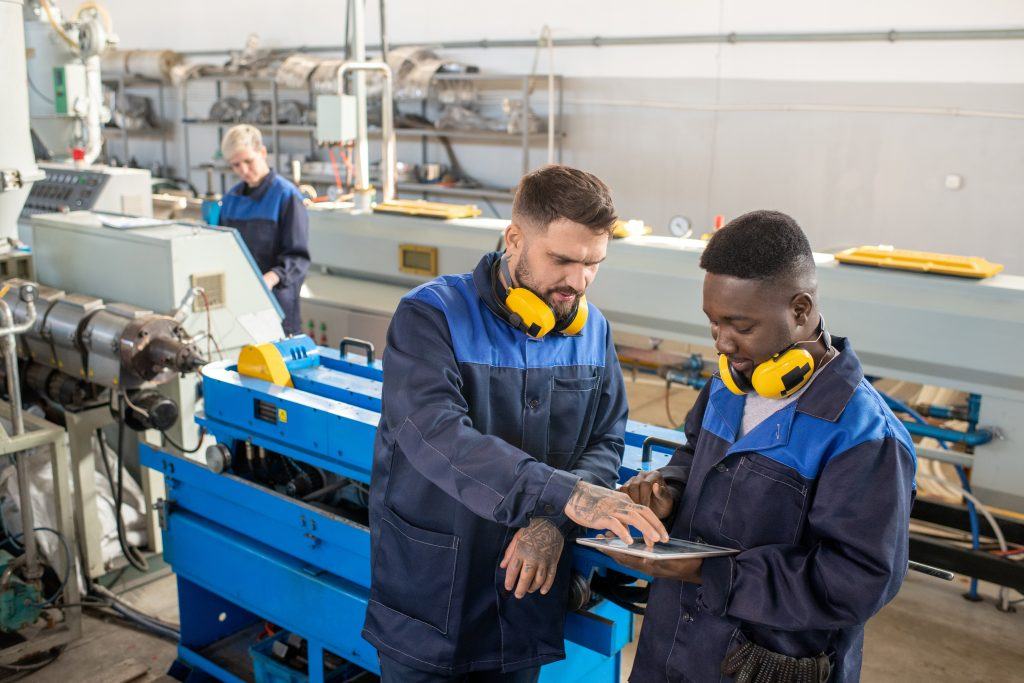
Avoid costly errors in your production processes
Test various scenarios (e.g. production process changes) without risking actual resources. If the simulation outcome shows defects or inefficiencies, you can tweak the processes until you find the optimal configuration.
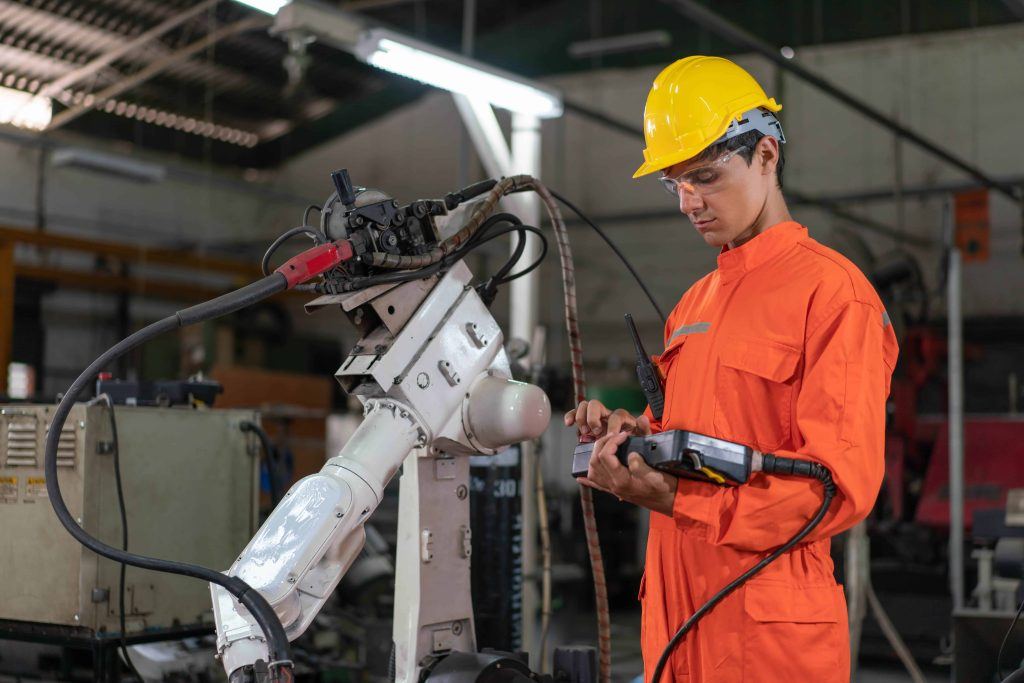
Save time and bridge data gaps for production engineers
When project specifications are subject to change, you can quickly adjust your models and assess the impacts without the need for time-consuming and costly physical trials.
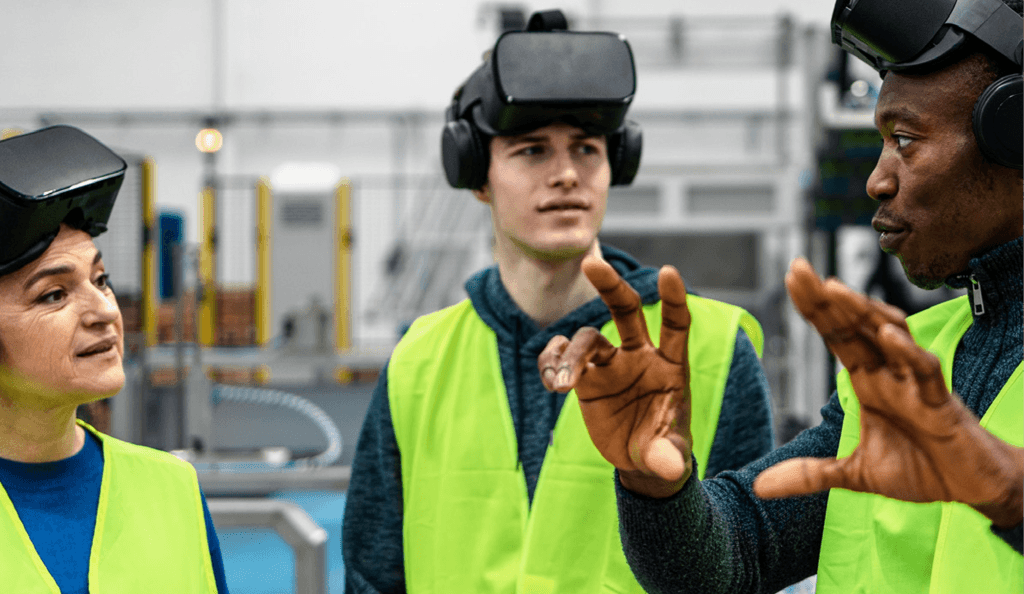
Optimize collaboration among stakeholders
All stakeholders in operations, engineering and business development can together simulate different manufacturing processes, explore different scenarios, and identify early on the potential design issues or challenges.
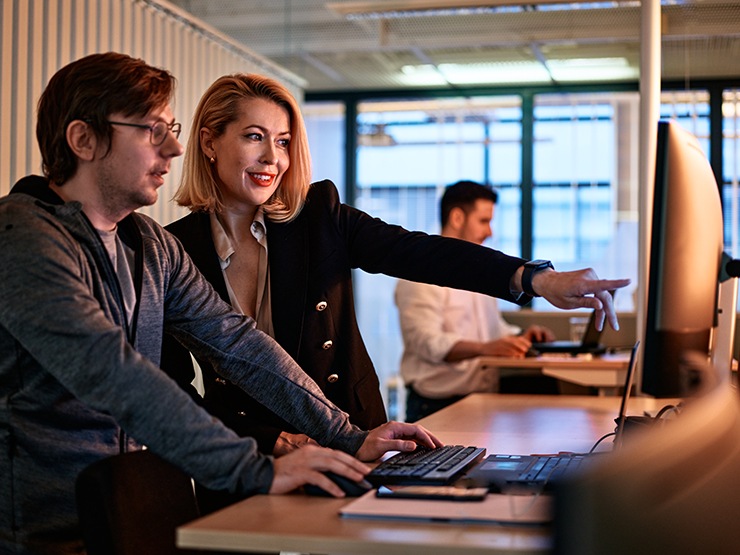
Enhance win rates and sales efficiency for system integrators
Quickly sketch and demonstrate your ideas in hours, instead of days. Your clients can see, rather than just imagine, the benefits and improvements your proposal will bring.
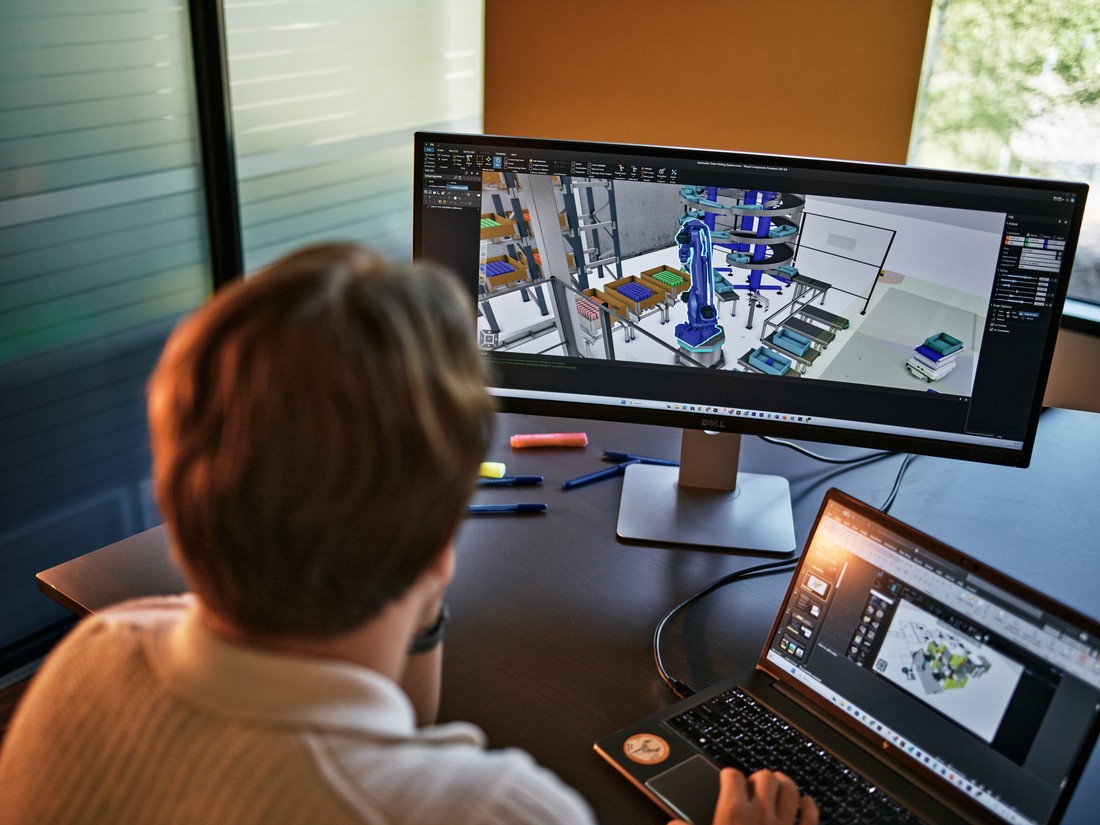
What is manufacturing simulation?
In a nutshell, a simulation is a model or representation that mimics a real-world situation or event.
A manufacturing simulation can be a digital model, digital shadow or digital twin of a real-world operation which allows evaluation of different production schedules and the impact of product mix and volume changes. It supports layout planning, bottleneck removal and continuous improvement efforts.
Let’s dive into the three top use cases for manufacturing simulation:
Remove the guesswork from designing or optimizing your factory layouts.
Detect early, resolve fast, enhance efficiency and commission virtually.
Accelerate deals, impress clients, and win more manufacturing projects or custom-built machine proposals.
What are manufacturing simulation use cases?
Manufacturing simulation is widely used across various industries, including:
Use one platform to design, simulate and emulate your production projects with powerful visuals.
Actively respond to new product introduction and production changes with simulation and adapt to lean production methods.
Quickly design and simulate your proof of concepts and accelerate the functional qualification of your production systems.
Simulate to improve your response to downtimes and increase your production efficiency.
Use hundreds of free-to-use automation equipment models from known global brands to set up realistic simulations of your automation projects.
Use simulation to invest smartly in your next production upgrade. Improve your chances to close the deals with a powerful sales acceleration tool.
Simulate to organize your warehouses and increase the functionality of your intralogistics setups with synchronized operations.
Accelerate your early design concepts with simulation, reduce the time to market and improve your responsiveness to new product introductions.
Simulate to add more flexibility to your production systems and respond faster to ever-changing consumer demands.
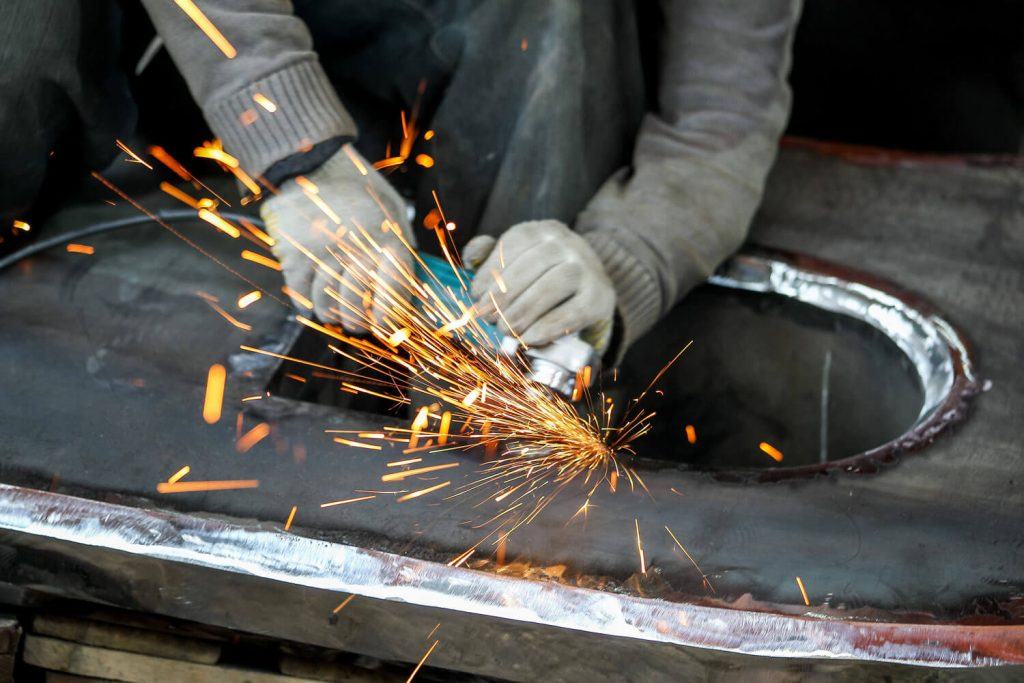
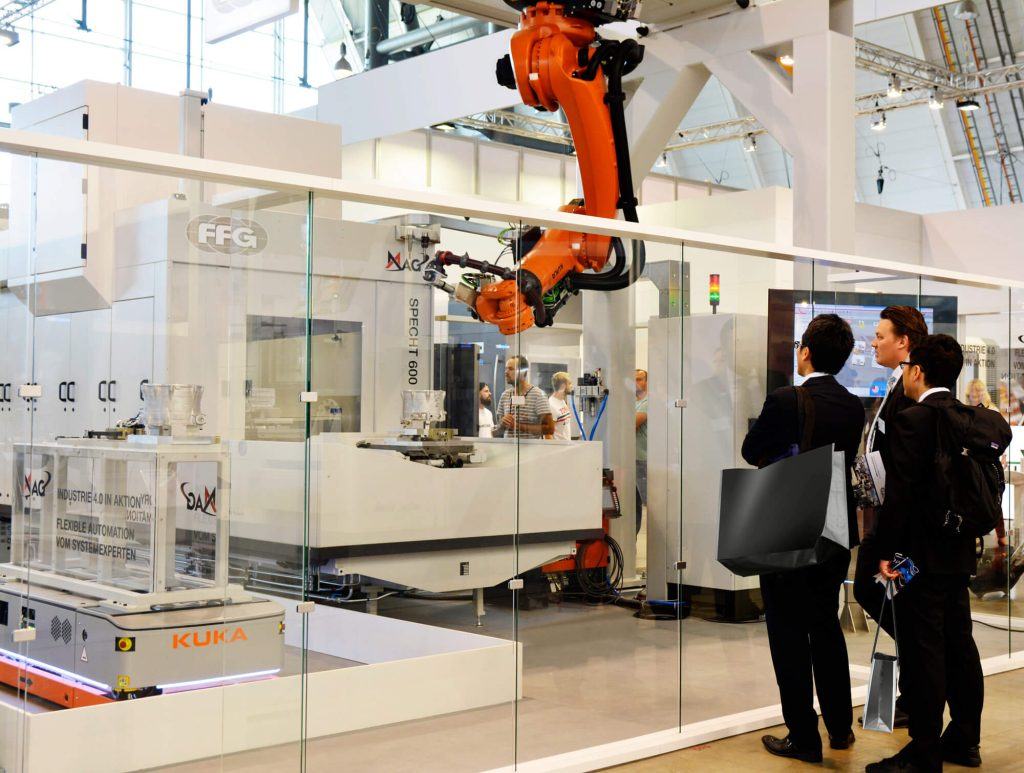
Which stakeholders benefit from manufacturing simulation?
Manufacturing simulation benefits a diverse range of organizations, such as:
Manufacturers are using manufacturing simulation to develop advanced production environments. Our simulation software helps you visualize and optimize every detail, ensuring your operations are prepared for future demands while running smoothly and efficiently.
System integrators are using manufacturing simulation to improve their planning, decision-making, and sales processes. Our simulation platform helps bring every detail to life, ensuring everything works together smoothly and efficiently.
Startups may get started with up to three licenses for three years at a discounted price and a training program that will help you benefit from our manufacturing simulation solution immediately.
Students, educators, and researchers are using our tailored solutions to enhance their learning, teaching, and research experiences. Our platform supports academic excellence by providing cutting-edge tools for simulation, analysis, and innovation.
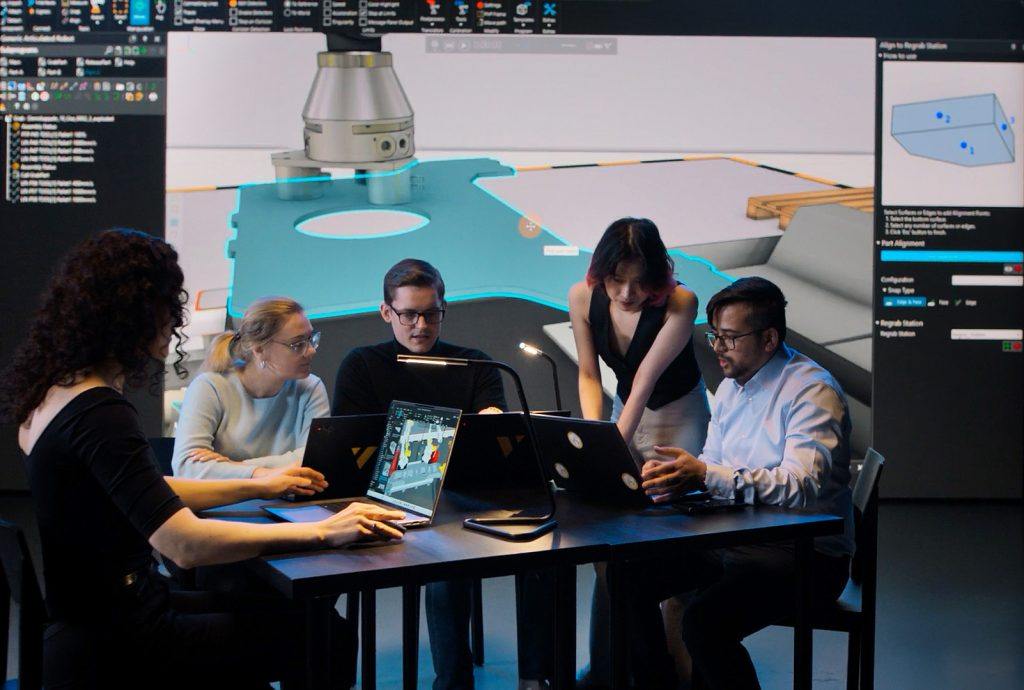
Evolution of manufacturing simulation
In the 1990s, manufacturing simulation began with basic 2D and evolved into 3D as computers got better. This was a real step up for engineers who were trying to model complex systems in a way that was accessible and easily understandable.
At first, these tools were slow and clunky, making some industry veterans skeptical. Fast forward to today, they have gotten so much faster, way easier to use, and they’re not just for the big players anymore. Even the smaller setups, like your local bakery, can benefit from manufacturing simulation. It turns out, manufacturing simulation has stuck around for a good reason – it’s super useful, no matter the size of your operation.
Manufacturing simulation alternatives
Excel
Pros:
- Effective for basic, linear calculations
- Capable of adjusting outputs based on inputs
Cons:
- Inadequate for simulating dynamic manufacturing environments
- Lacks insight into the complex, time-sensitive interplay of events in a production line
Manufacturing simulation brings these dynamics to life through visualizations and animations, offering a clear understanding of how different elements interact and affect each other over time.
CAD tools
Pros:
- Excellent for creating detailed static designs and layouts
- Can show where machines and robots will be placed
Cons:
- Lack the capability to demonstrate real-time operation and interaction of elements
Manufacturing simulation fills this gap by not only visualizing static layouts but also animating the operational flow and timing of processes within these layouts.
Manufacturing Simulation
Pros:
- Dynamic, time-based approach
- Provides a comprehensive and realistic understanding of manufacturing processes
- Offers visual and animated representations of complex interactions
- Enables accurate planning and optimization of production processes
- Helps foresee the outcomes of production processes
Cons:
- For those who enjoy a challenge, this might feel too straightforward and effortless.
- Its simplicity could make you nostalgic for the good old days of manual calculations.
What our customers say
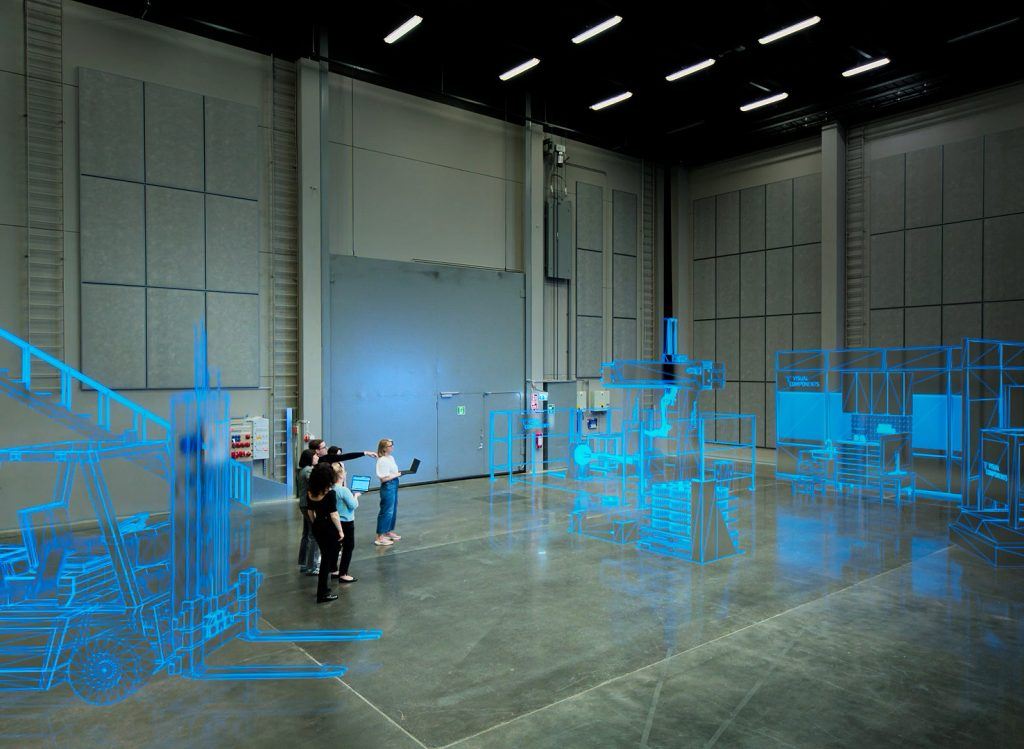
What is the future of manufacturing simulation?
The future of manufacturing simulation is shaped by three key developments, focusing on collaborative digital models. This evolution marks a transition for manufacturing simulation from being a stand-alone tool to a collaborative framework where digital models are central to how teams work together.
As computers become faster, simulations can run more complex scenarios in less time. The evolution of algorithms and AI, such as machine learning and genetic algorithms, will automate the optimization process. More than just finding the best mix of machines and workers, AI can assist users in the whole design workflow.
The shift towards cloud-based environments means simulations can be more accessible and collaborative. Users can create models on a web interface and send them for computation on powerful remote servers. This allows for real-time monitoring and adjustments by multiple users.
Beyond the creation and computation of models on powerful remote servers, the future lies in providing digital model “components”. Companies will likely offer these components to allow potential customers to test products beforehand, facilitating a seamless integration into existing workflows. This move towards ready-made components supports platforms that provide quality content like Visual Components. These models will be as integral to teamwork and decision-making as traditional office tools.
With better computers, simulations can show even small details of production very clearly, catching every tiny change and its effects. The integration of AI not only automates layout designs and process optimizations but also makes simulations a integral part of daily operations.
The trend towards more detailed and integrated simulations is also driven by how companies now have much of their data readily available for use in simulations and machine learning. This signifies a future where simulations are not just tools but foundational elements in manufacturing, offering real-time, automated insights and solutions.
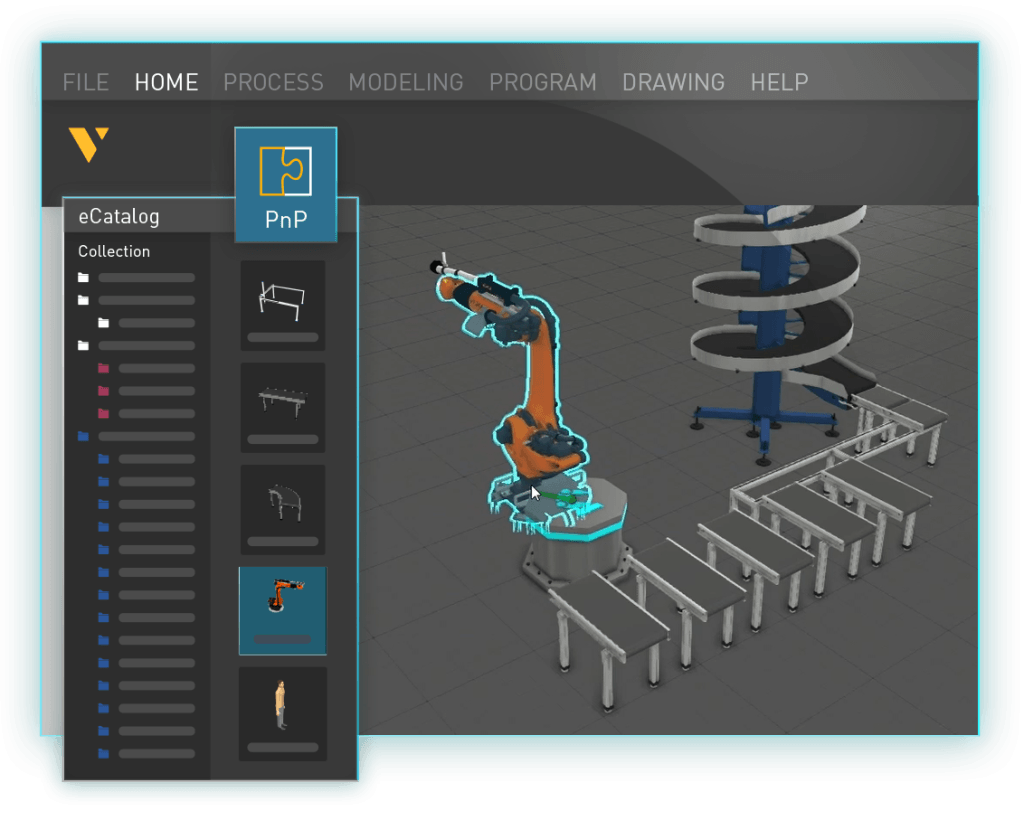
Explore the best manufacturing simulation software
Simple. Visual. Powerful. Designed for manufacturing professionals and built on a powerful, flexible and easy-to-use platform. Design and validate new production solutions confidently with Visual Components.
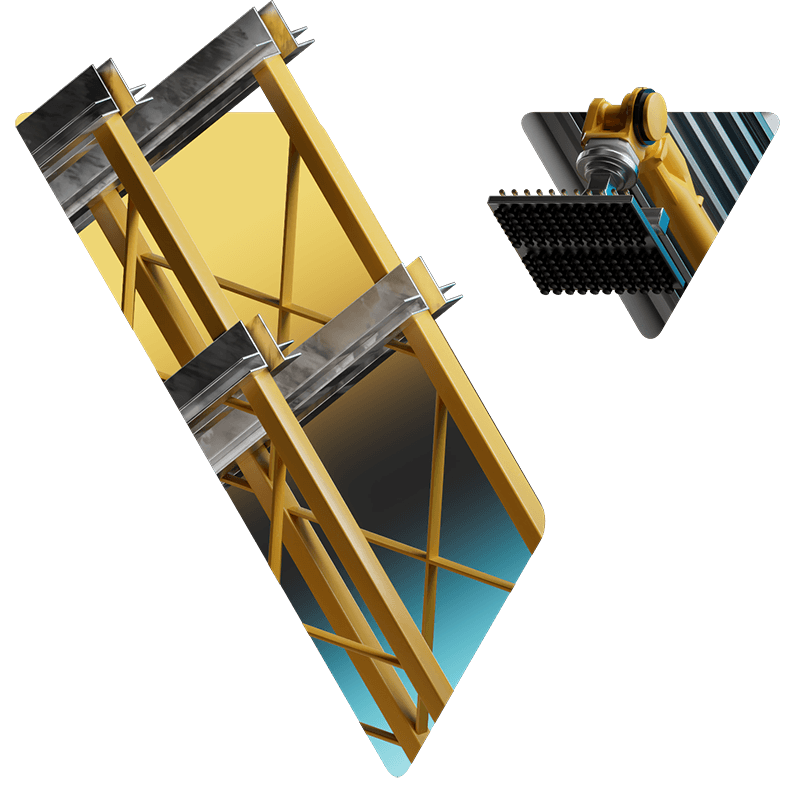