Upskilling humans: harnessing automation and simulation for a future-ready workforce
Automation, manufacturing simulation, and the ideas surrounding industry 5.0 are very promising for manufacturing and industrial facilities across the globe. This new wave of technology can greatly help a human workforce, from upskilling the workers to boosting the overall throughput of your product.
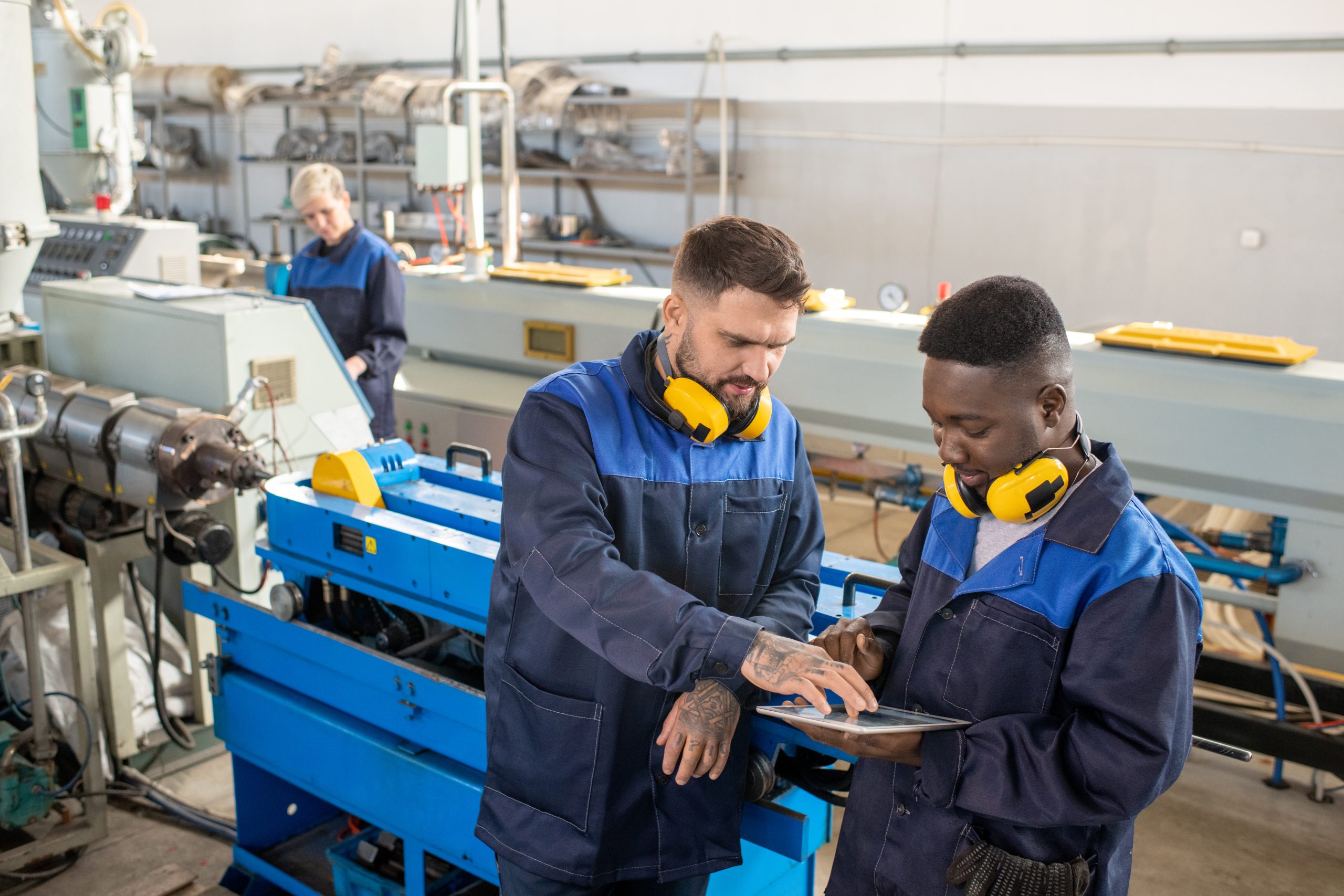
How automation can transform a human workforce
There is a common misconception that automation and robotics are going to take over and replace the human workforce, but that’s not true. Especially in the early stages, automation is going to be a very useful tool that can transform our human workforce.
In manufacturing and industrial facilities, automation has a number of benefits:
1. Reskilling repetitive jobs
There’s a good chance that a lot of steps in your process involve highly repetitive actions. Thinking about an automotive manufacturing facility, it’s easy to notice these repetitive tasks on the assembly line. One worker will repeatedly run a punch press all day, every day.
There are a few risks to jobs like this — for one, there is a big safety risk to doing the same repeated job. It’s easy to lose focus and make a simple mistake. In addition, it’s stifling the ability of the worker if they’re forced to repeat the same process every day.
By replacing this job with an automated process, you’re able to reskill this worker and allow them to handle higher-value tasks that can grow their skillset and give them more freedom from day to day.
2. Removing human error
Another place for automation is in any task that has a high risk of human error. If the worker has to align a part perfectly into a jig and any variation will ruin the part, then you might consider automation.
A robot can repeat tasks and align parts with higher levels of precision than any human can. By strategically implementing automation, you can remove these potential issues from your product.
3. Increasing throughput
Another undeniable fact is that robots are much faster than humans. This applies to processing speeds, physical speed, time taken between tasks, and the need to take breaks. Barring maintenance tasks, a robot can run 24/7 all year without any breaks. But what does this mean for your process? Higher throughput and quicker turnaround times. It means more product made each year, which translates to more money hitting your bottom line. Add in the fact that the robot can do these tasks with lower rates of error, and you also have a higher yield percentage which adds even more money to your company’s pocket.
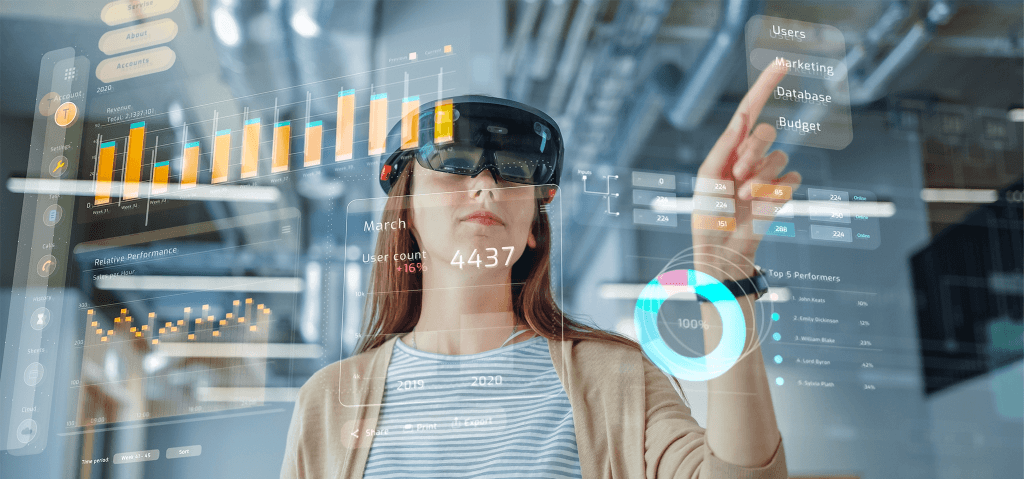
The connection between Industry 5.0 and human upskilling
As a whole, industry 5.0 is the idea that humans and advanced technology can work together. It’s the idea of humans, AI, robots, and automation working together on the same assembly line. Even if a robot can theoretically do the job of a human, there are a lot of roles and jobs that are better when they’re left to humans. This leaves us with an industry that needs to be highly connected between technology and human.
- The design needs to revolve around humans. The process designer needs to determine how automation fits around the humans working on the line. A common example is designing a robot that can run at room temperature instead of changing the temperature of the facility to 120°F, which would be very uncomfortable for the humans working there.
- Technology helps humans, not the other way around. The bottom line is that your production process will still be humancentric. Even if a robot helps during one of the steps, it is ultimately a team of humans that are responsible for the end product.
- New tech helps humans grow new soft skills. Since the workforce is integrated with technology, there’s a need for everyone to learn how to work with the tech. In other words, your workforce will learn more about critical thinking, how to quickly solve a problem, and how to creatively work through an issue.
Using manufacturing simulation to help
Another update to manufacturing facilities is manufacturing simulations. These simulations are powerful pieces of technology that can use real-world scenarios to come up with theoretical results that are all digital. You would use a computer to run the simulation before any actual manufacturing is done. These sims come with a lot of benefits. As a piece of automation, a manufacturing simulation will save you time and money during the prototyping phase. It can also improve legacy designs with very little effort on your part.
The same technology can also optimize your current process — you can find bottlenecks and identify parts of your process that need to be refined. By implementing these changes, you can save money and boost your production each year. Manufacturing simulations can also be used to upskill workers in blue-collar jobs. With a focus on quality and error prevention, a hands-on worker will develop soft skills that increase their daily throughput as well.
Conclusion
Now you see how powerful automation, industry 5.0, and manufacturing simulation are. These aren’t pieces of technology that will replace a human workforce, but they can be used in junction with your staff to greatly improve your overall process. You can make more money, save time, and avoid issues by combining technology with human staff.
To get started, consider Visual Components. We have a full suite of simulation tools that can boost your current operation. Allow us to jump-start your integration into Industry 5.0, and start seeing results today. Explore our website for more content like this, or reach out to learn more.
Further reading
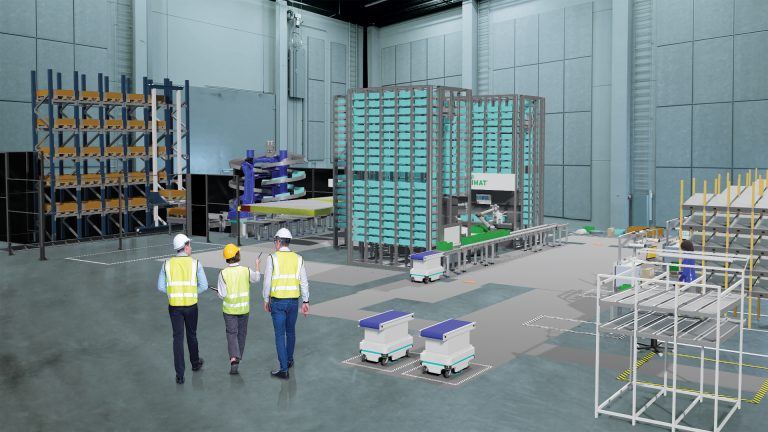
The future of automated manufacturing (and why humans still matter)
Automation in manufacturing has been evolving for decades, but its true impact isn’t in replacing people, it’s about making them more capable. We spoke with Mika Anttila, one of Visual...
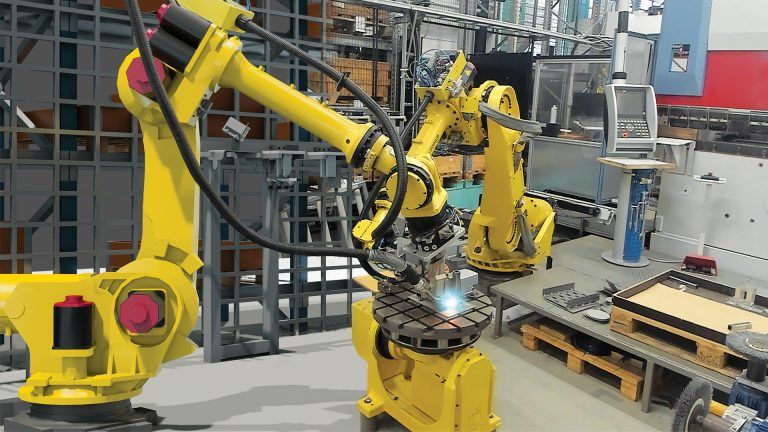
Understanding digital twins in manufacturing
Digital twins go far beyond static models or simulations. They bridge the gap between virtual and physical systems, offering real-time insights and control. But with so many definitions floating around,...
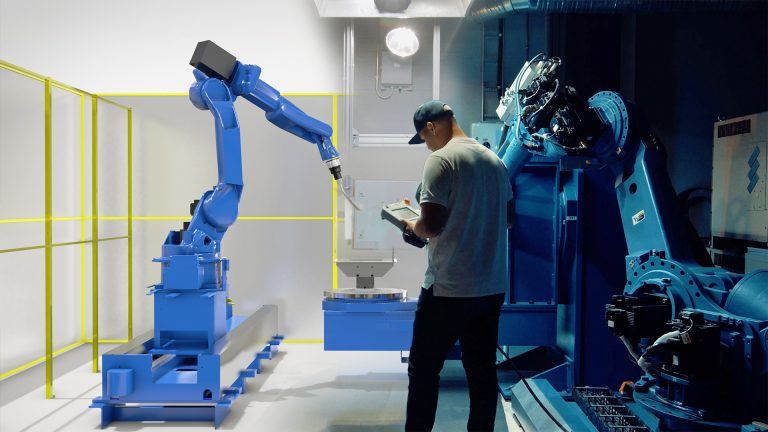
Tackling the manufacturing skills shortage with simulation and robot offline programming
The manufacturing industry is grappling with a significant skills shortage, exacerbated by the pandemic and an aging workforce. According to The Manufacturing Institute, 78% of companies are concerned about this...