Lean Manufacturing 101 (Video Examples Included)
In this piece, we’ll introduce you to lean manufacturing. You’ll learn some key phrases, the history of this concept, 7 governing principles, and books to help you along the way.
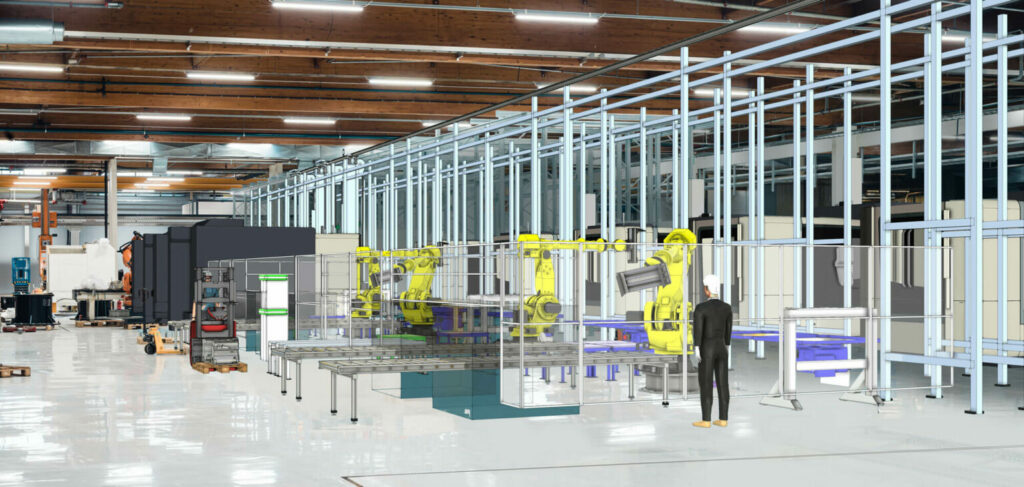
In the competitive world of manufacturing, businesses need to do anything to grow their market share. For many operations, that means implementing lean manufacturing. Before doing that, you’ll need to understand more about the concept of lean manufacturing.
This is what we will go through. You can also jump to the part that interests you the most.
- What Is Lean Manufacturing?
- Understanding Waste
- A Brief History of Lean Manufacturing
- 7 Lean Manufacturing Principles
- What Is “Just-In-Time” Manufacturing?
- Top 3 Lean Manufacturing Books
What Is Lean Manufacturing?
Lean manufacturing goes by a few different names:
- Lean production
- Six sigma
- Kaizen
Lean manufacturing is one of the mentalities used in manufacturing facilities. There are a few major principles with a common ultimate goal: to optimize a manufacturing process.
This means making things efficient, faster, more consistent, and producing at a higher level of precision.
Lean manufacturing can be used to design a future-proof factory that gives you a competitive edge over the others in your market.
One of the biggest focuses in lean manufacturing is eliminating waste during the process. To oversimplify the idea, you’re simply “trimming the fat” of your operation. Afterward, you’re left with a lean production facility.
When a plant wants to delve into lean manufacturing, it’ll analyze its full process. From the physical location and layout of equipment to the operational specs of their equipment. Even the workforce running the machines is a big focus.
Understanding Waste
It’s worth defining the term “waste”. This word is constantly used when people talk about lean manufacturing.
Waste is anything that doesn’t add value to your operation (from a customer’s perspective). An easy-to-understand example is when you discard contaminated or defective products. Another example is an employee who takes multiple breaks during their shift.
If something slows down your process and hurts your bottom line, then it can be considered waste. One of the most common examples is the transportation of products and people. When your product and workers are moving from one location to the next, waste is occurring since so much value is being added.
A Brief History of Lean Manufacturing
The history of lean manufacturing is interesting. The concept started in the early 1900s. During that time, the assembly line started gaining popularity and distribution was growing from local shops to national sales.
As a result, companies needed to get smarter about how they made, sold, and distributed products. In the name of competition, they had to find ways to manufacture and distribute products faster, more consistently, and with fewer mistakes.
This introduced a level of scientific study into different aspects of manufacturing. Once the studies were conducted, the actionable result was to implement these ideas of “lean manufacturing”.
Although it started in Ford’s factory, the ideas made their way to Toyota in Japan. A vast majority of lean manufacturing principles used today are due to Toyota’s furthering of Ford’s original ideas. That’s why you’ll find a lot of Japanese terminologies embedded in lean manufacturing.
7 Lean Manufacturing Principles
There are 7 major principles in lean manufacturing that help you improve your process. These are built into the fabric of six sigma and all date back to its origination. The principles are as follows:
- Eliminate waste
- Value your human elements
- Seek perfection
- Map the value stream
- Reduce and prevent mistakes
- Identify value
- Automatically find defects
Eliminate Waste
In the age of minimizing ecological damage, lean manufacturing helps a lot. One of the basic principles is to reduce or eliminate waste. This works well on two fronts.
Firstly, it reduces your impact on the Earth. Secondly, it helps your business save more money. Waste equates to money going down the drain.
For example, before ordering new equipment, AGCO run a simulation of its planned component machining system. This helped them decide if some pieces of equipment could be removed from the plans in case the simulation suggested that a smaller number was sufficient.
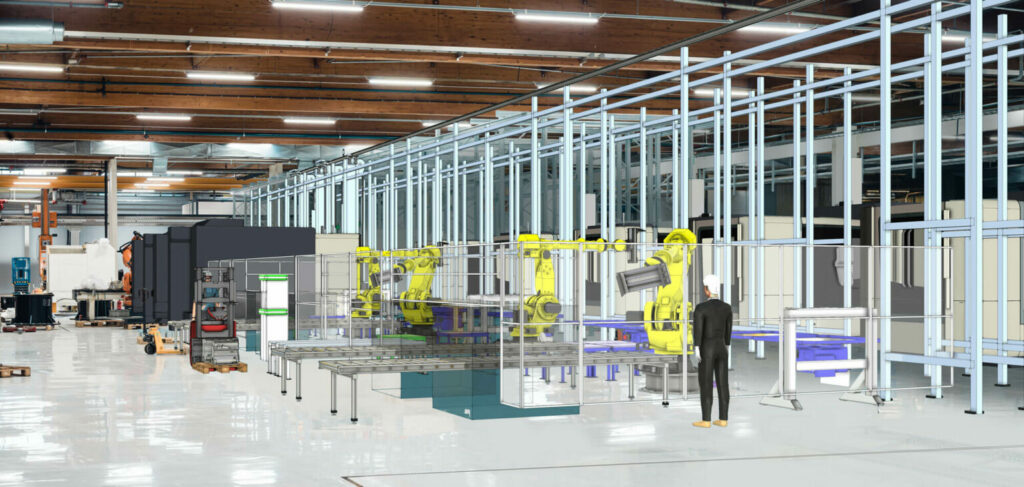
Value Your Human Elements
Lean manufacturing also puts a lot of effort into understanding and valuing your workers. Avoid overworking them, keep them accountable for their successes and failures, and show them what their tasks achieve.
With a strong group of workers, your product (and in turn, your company) can see a huge improvement in quality and manufacturing time.
Interestingly enough, this is a category that’s often overlooked in manufacturing companies. Getting the best machines and the most optimized process doesn’t amount to anything if the people running the process are undervalued and underappreciated.
For example, QING used 3D manufacturing simulation to set up a fully functional face mask factory to meet the high demand for face masks during the COVID-19 pandemic. The simulation technology helped ensure the safety of their employees by implementing social distancing in the simulations.
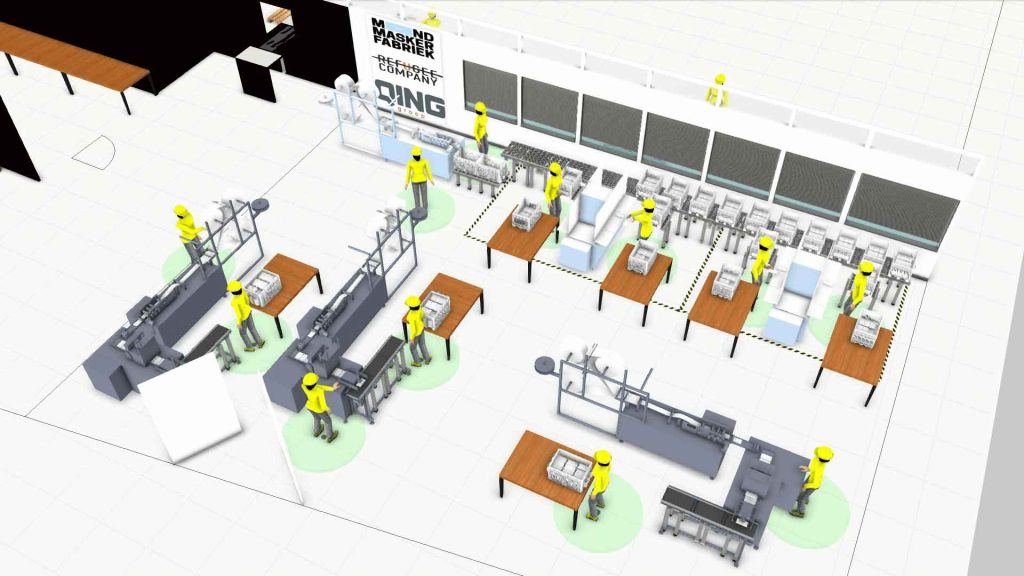
Seek Perfection
Lean manufacturing is all about seeking perfection. This means continually looking to improve your process. It also means making improvement a part of your office’s culture.
The idea of lean manufacturing entails always evolving and never getting complacent. There is always room for improvement, and it should be a recurring mission to seek perfection.
Talking about perfection:
Check out this video of the Smart Factory Project, a successful collaboration between TEMEX and VSB-Technical University of Ostrava. Planning a project like this from scratch in simulation to physical implementation is quite impressive considering that it is also integrated with MES system for warehousing. Both manual and automated assemblies are possible. The project is simply is impressive and almost perfectly fits into lean philosophy.
Map the Value Stream
The value stream refers to how a product is created in your facility. It’s a trackable map from raw material to the final product.
The best practice is to make a physical map that tracks the stream. One step has an arrow that goes to the next, and so on.
When the map is complete, take a close look at it and you’ll understand where your process can improve. This varies a lot from company to company, but there’s a lot of improvement that can be discovered just by mapping your process.
Lean manufacturing suggests that you take some time, review your value stream, and rework every area that will improve your business.
Take a look at this example of the full factory mapping — from raw material to final product.
Reduce and Prevent Mistakes
Mistakes are the antithesis of lean manufacturing. Mistakes result in wasted material, time, and money. While not all mistakes are avoidable, the best practice is to reduce them as much as possible.
If you commonly have contamination of air bubbles in your product, you might implement a project to find the root cause and eliminate it. The same is true for any potential human error.
Simply installing robotics to your line could prevent a certain mistake that makes up thousands of dollars worth of waste during a fiscal year.
If you bring in a lean manufacturing consultant, one of the first improvements they’ll probably make will revolve around preventing mistakes in your process.
For example, with the help of robot simulation, you can detect possible mistakes in time.
Identify Loss of Value
The “value” of your operation is determined by your customers. Things that go into the value are:
- Lead times (time to produce and deliver parts)
- Price point
- Color, material properties, and material used
- Functional and geometric requirements of your product
- Repeatability, accuracy, and precision of parts
To find a loss of value is pretty simple. It’s the act of taking a close look into your process. Where are some locations where the value isn’t being optimized? These are potential areas that you’re losing value.
For example, any extra process steps or unnecessary features will hurt your value. You might be doing more than your customer needs.
If your process has to be redone or transported long distances for no reason, then this is an example of loss of value.
You want to create a barebones process that achieves the goal in as few steps, as little time, and as low a cost as possible. Any extra steps might do nothing but hurt your product’s value.
Find these extras and determine if they’re truly adding the value that you think they are. After evaluating them, you might find some areas that your process can change.
Automatically Find Defects
When mistakes can’t be prevented, they should be automatically detected. This lean manufacturing principle revolves around either stopping your production line or removing defective material.
The first part of that is screening for defects. If ferrous metal contamination ruins your product, then installing strong magnets along your line will automatically find defects. Otherwise, smart sensors or cameras can be installed to do the same.
What Is “Just-In-Time” Manufacturing?
Just-in-time (or JIT) manufacturing was born to reduce waste. The idea is that a product or process is strictly done to meet demand, thus reducing WIP (work-in-progress) and capital and money bound to production.
By doing this, the potential for wasted products disappears. On the downside, there’s an added level of stress and longer lead times for customers since you’re only producing after an order is placed.
To successfully implement JIT manufacturing, you’ll need to work through the 7 principles discussed earlier. Your production line needs to be optimized to deal with the demand of JIT manufacturing.
Any delays or disruptions during manufacturing will hurt your lead times even more and can result in customers backing out of orders.
Top 3 Lean Manufacturing Books
If you’re looking for some more information, then these books should help you. These are the top lean manufacturing books that look at the history, some fundamentals, and how to implement lean manufacturing for your facility.
The Toyota Way: 14 Management Principles from the World’s Greatest Manufacturer
This is the first written piece that explores the principles behind lean manufacturing. It specifically looks at Toyota’s success when they first solidified lean manufacturing in their plant. Like this article, this book will show you how your facility can roll out these principles.
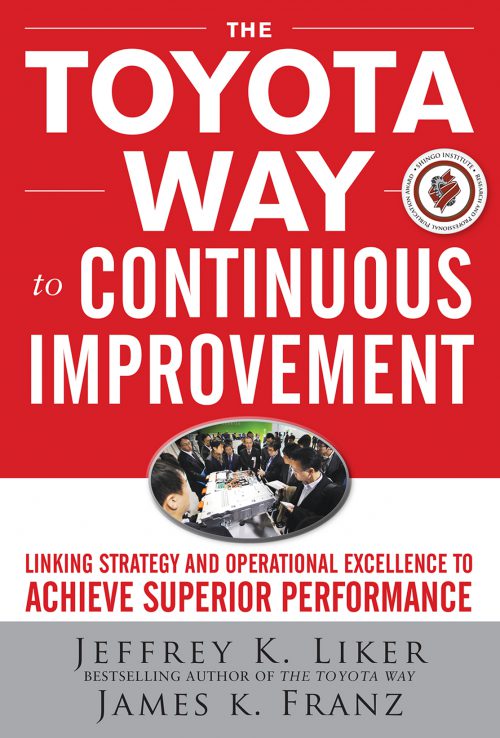
The Machine that Changed the World
This book was the first to use the phrase “lean manufacturing”. It also looks at Toyota’s facility and its methodology.
It also dives into the specific advantages of each lean principle, using Toyota’s figures as examples.
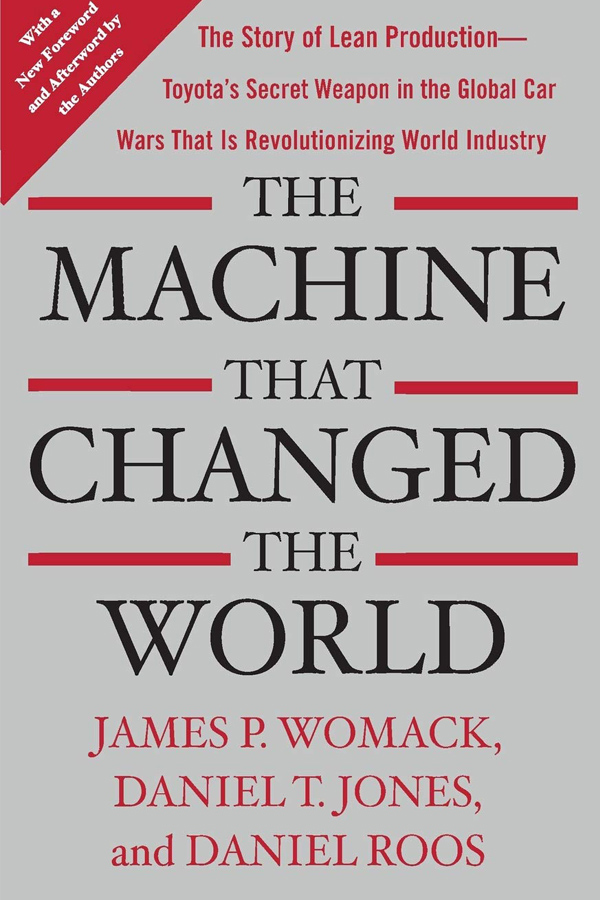
Kaizen Express: Fundamentals for Your Lean Journey
This book was written by a former Toyota employee. It served as a way to teach non-Japanese-speaking readers about lean manufacturing.
It acts as a workbook to help the reader understand kaizen principles and learn how to use them for their process.
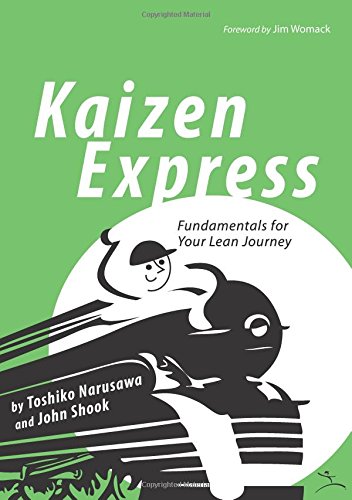
Wrapping up
You just got a closer look at lean manufacturing. This concept can help your business improve its profits and become a bigger player within your industry. If you want personalized help, then reach out to Visual Components today. Book a free consultation and let us show you how to improve your efficiency, reduce your waste, and increase your profit with lean manufacturing.
Further reading
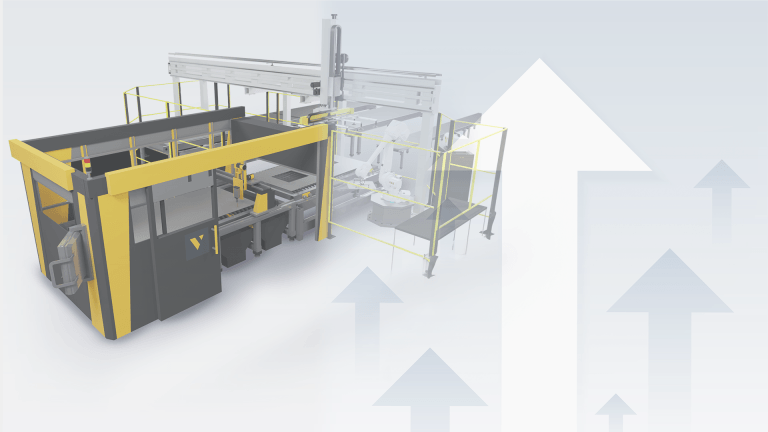
Boosting production line efficiency: a guide on improving production output
Production efficiency is the cornerstone of success in manufacturing. It measures the effectiveness of resource utilization in the manufacturing process, aiming to maximize output while minimizing costs and waste. The...
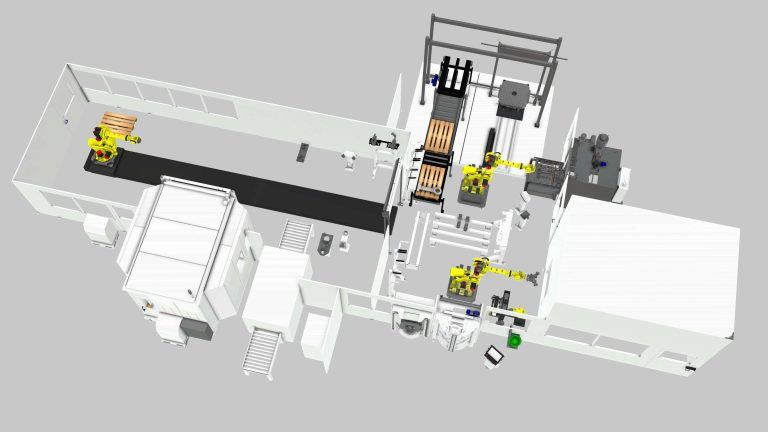
An introduction to virtual commissioning
Virtual commissioning is reshaping the manufacturing landscape by employing computer simulations for testing and optimizing production systems before they're physically built. This approach not only simplifies the setup process and...
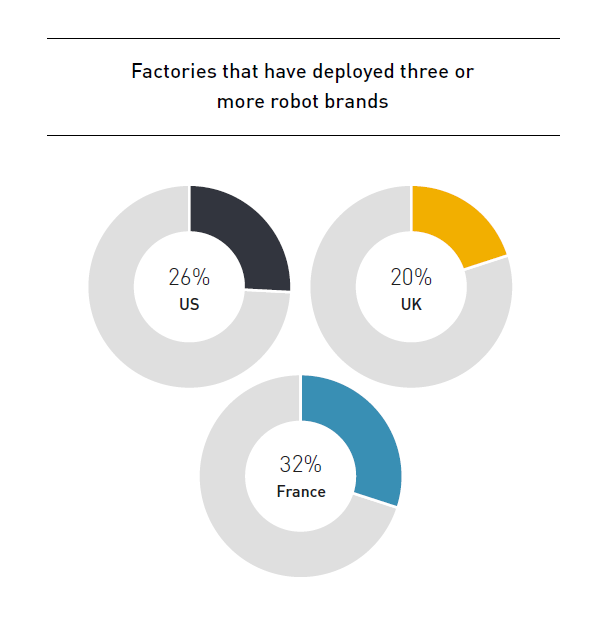
Are manufacturers really ready for the digital era? (survey results)
Legacy equipment and outdated practices can seem like relics from another age, especially as the world zooms ahead with digital innovations. Yet, they're more prevalent in the manufacturing sector than...