Turn production plans into project success
How can you avoid making costly mistakes when planning a new production line? Find out!
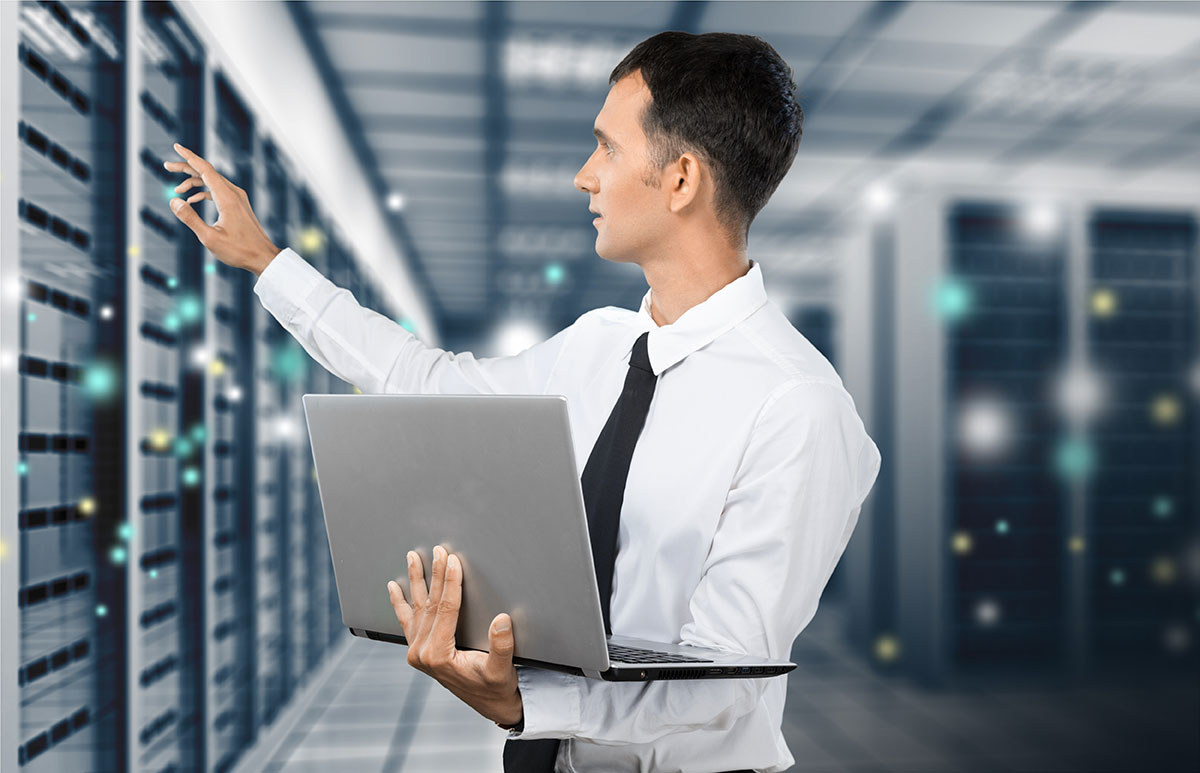
Any seasoned engineer can tell you stories of how reality got in the way of a beautiful model, drawing or calculation. A screw hole that couldn’t be accessed by a screwdriver, an assembly line that moves too fast for a worker, or even a plant wall that has to be moved so that an assembly line will fit in a building. Some of these anecdotes are humorous tales of the trade, making good teachable moments for junior engineers. Others led to less entertaining outcomes, causing significant overages in budget and schedule, and even costing some engineers their jobs. Unfortunately, many times these issues arise after an investment decision has been made or a contract has been won.
Projects typically go sideways due to mistakes or oversights made during the planning process. All the upfront planning and effort spent by engineers can turn in an instant as overlooked scenarios or off base assumptions catch up with them. Without proper planning, a small mistake can turn a profitable project into a huge loss or a minor annoyance into an enterprise wide disaster.Often, these troubles are avoidable if only the engineers were able to anticipate how those well laid plans would translate from linked cells in a database to moving parts and people on a production floor.
Proper and extensive planning is critical to ensuring you can turn your vision into a reality. To do it right, you need accurate data and information, the right analysis and assessment tools, and a way to clearly communicate your technical analysis with project stakeholders.
3D manufacturing simulation technology brings spreadsheets to life and highlights real world interactions while providing a unique way for engineers, planners, and sales teams to interact. By consolidating engineering data, including CAD layout files, CNC tool path data, and personnel utilization data, manufacturing simulation software offers organizations a way to analyze, visualize and optimize plans at the quoting or planning stage.
3D manufacturing simulation technology brings spreadsheets to life and highlights real world interactions while providing a unique way for engineers, planners, and sales teams to interact.
Combining Design Data To Enable Simulations
Layout of a production line is relatively easy, but getting the detailed designs of each component to integrate with one another is a huge pain. For a new production line, it is not uncommon to see a combination of design files from several different programs, ranging from PCB design modules and mechanical 3D parts to 2D plant layouts and 3D point clouds. Ask any experienced designer and they can explain how difficult it is to import, export, or transfer designs between formats.
The best manufacturing simulation programs use actual parts pulled in directly from their native programs, whether it’s Solidworks, Altium, AutoCAD or something else. Tool paths and CNC programming logic associated with a machine should also be included into the simulation, to provide realistic machine operations and timing steps.
Being able to model the actual part and plant geometries creates a more immersive planning experience, where everyone from front line sales to production line workers can provide insights and feedback, and project stakeholders can have more confidence in critical planning decisions. For example, when a facility manager or architect can share an AutoCAD .dwg for a plant floor with a machine vendor, they can ensure that support beams and low ceilings aren’t overlooked and that the equipment’s range of motion will not be compromised when installed.
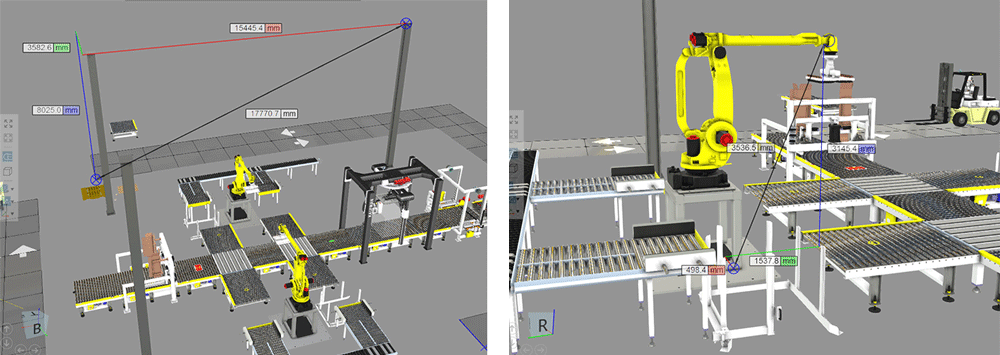
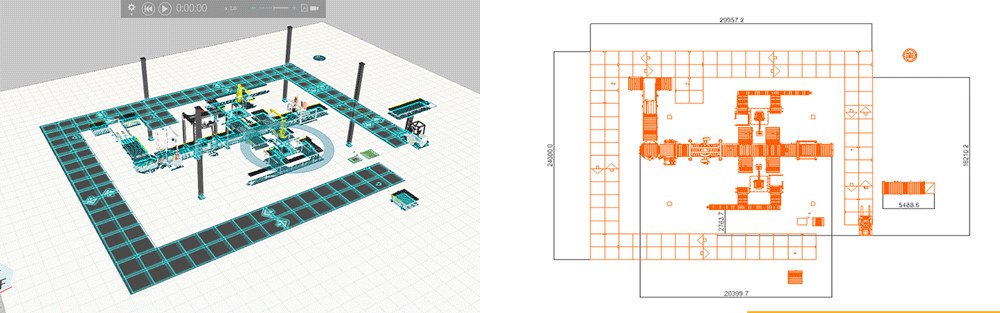
Modeling The Real World… Not A Spreadsheet
A creative designer dreams up a revolutionary innovation. They create a series of documents to showcase how it will be made and how inexpensive it will be. A spreadsheet confirms that the cycle time to create their new device will allow them to satisfy the overwhelming market demand. Now, it’s time to put this game changer into production. What could possibly go wrong?
As it turns out, a 10 second process sometimes takes 11 seconds, and sometimes 9 seconds. A three shift plant in a cold climate shuts down occasionally due to poor weather, and supply trucks delivering critical components are delayed 3% of the time, despite all the efforts of the operations team.
To accurately capture real world environments, a single process time may need to be dynamic. For a simulated action, such as an employee walking between workstations, a distribution can be used to highlight mean cycle times and accurately represent variations. A path across a plant floor may average out to 9 seconds of walking time, but simulating only a series of 9-second paths does not account for the times it takes 15 seconds.
With the ability to extend a simulation across a full shift, workweek, or year, the edge case scenarios can be captured. This unique modeling allows for a level of planning detail that is otherwise only captured deep into a project, when delays and issues can generate budget-breaking reactions.
Starting small, a simulation may begin with a single 8-hour shift, running at a 30:1 speed, to measure machine utilization. Expanding to longer time periods and integrating dynamic data such as a mean time between failures and average time for repairs enhances your ability to predict long-term impacts of design decisions. For the most important projects, variables can be added with almost no limit to ensure what is shown is as close to a real world scenario as possible.
With a visual simulation, critical assumptions aren’t hidden away in spreadsheets, and minor issues can be brought to light before they become major disruptions. Simple process reconfigurations can be executed on the fly and scenario planning can be used to monitor the impacts of worker absences, configuration changes, and demand fluctuations.
Looking back at the previous example, this could mean identifying those occasions when the employee has to wait for their path to clear, causing the slower transitions between workstations. Reconfiguring a layout to remove this anomaly may increase the average time marginally while eliminating the edge case of a 50% slowdown.
With a visual simulation, critical assumptions aren’t hidden away in spreadsheets, and minor issues can be brought to light before they become major disruptions.
Turn Production Plans Into Project Success
Advanced 3D manufacturing simulation software is designed to capture all of the available layouts, designs, and information needed to produce a useful and accurate visual simulation. By integrating this real input data, manufacturing simulation software is able to create a visual display that shows a production facility, not a series of spreadsheet cells.
Opening a simulation to a visual display makes reviewing a project plan more intuitive. Even non-technical stakeholders are able to quickly understand the impact a change can make. When presenting detailed analysis to other management, or collaborating across departments, this facilitates more open discussion and feedback.
3D manufacturing simulation software is a powerful tool for manufacturing planning teams that need to design, test, and communicate complex designs and concepts to multiple levels of stakeholders. To help you better understand how this technology can improve your organization’s production planning, we’ll be publishing a series of articles dedicated to manufacturing simulation software for production planning teams. Thanks for reading and stay tuned for more!
Further reading
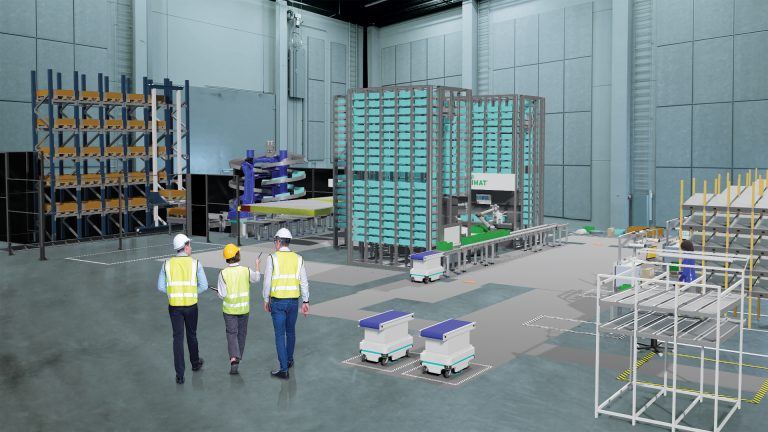
The future of automated manufacturing (and why humans still matter)
Automation in manufacturing has been evolving for decades, but its true impact isn’t in replacing people, it’s about making them more capable. We spoke with Mika Anttila, one of Visual...
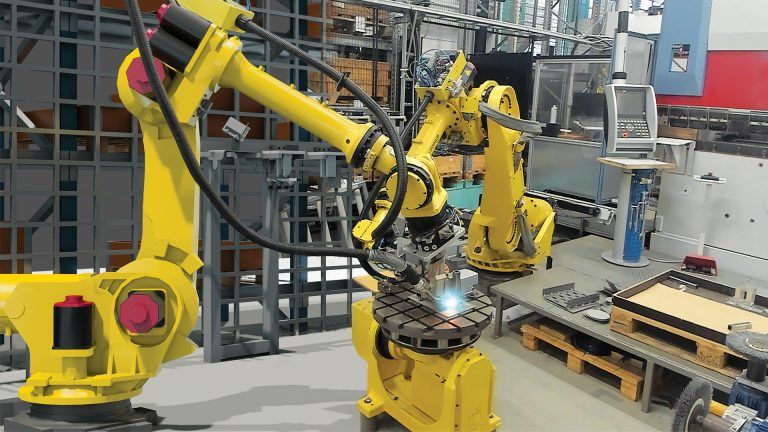
Understanding digital twins in manufacturing
Digital twins go far beyond static models or simulations. They bridge the gap between virtual and physical systems, offering real-time insights and control. But with so many definitions floating around,...
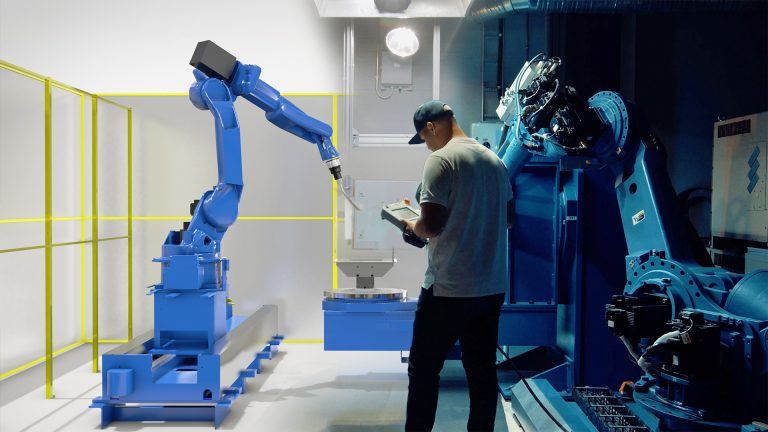
Tackling the manufacturing skills shortage with simulation and robot offline programming
The manufacturing industry is grappling with a significant skills shortage, exacerbated by the pandemic and an aging workforce. According to The Manufacturing Institute, 78% of companies are concerned about this...