FILL-Fallstudie
Sehen Sie hier wie die Firma Fill Visual Components’ 3D Simulation nutzt um ihre Ressourcen zu optimieren und Kosten zu reduzieren.
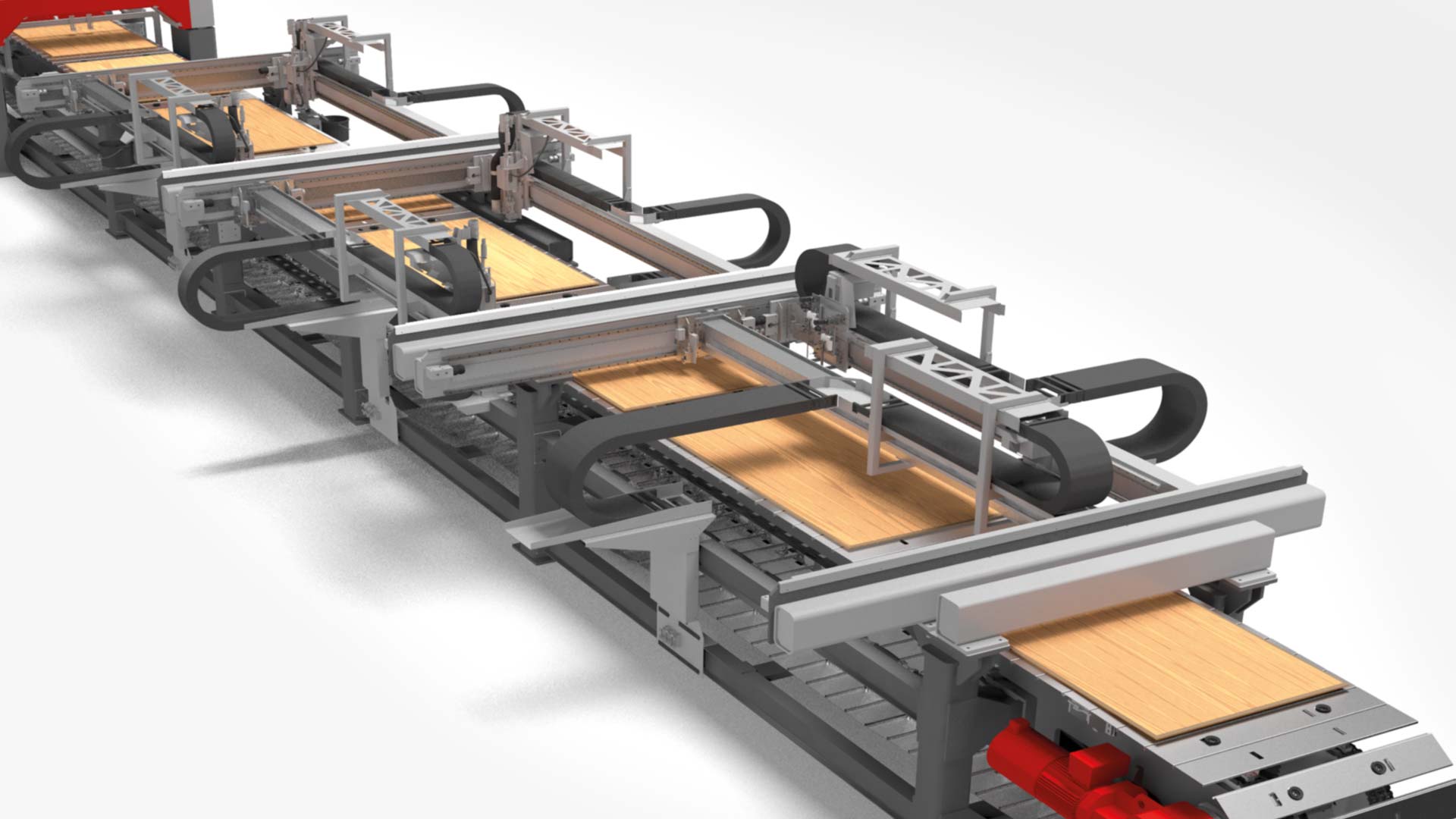
Visualisierung als zentrales Verkaufsargument
Die Fill GmbH ist ein globales Maschinen- und Anlagenbauunternehmen mit Sitz in Österreich. Seit 2009 setzt das Unternehmen die 3D-Simulationssoftare Visual Components im Vertrieb, in der Produktionsplanung und der Entwicklung ein.
Vor Einführung von Visual Components hatte das Unternehmen im Rahmen umfangreicher Tests 69 verschiedene Simulationswerkzeuge geprüft. Aufgrund seiner nachweislichen Erfolgsgeschichte und hervorragenden Partnerbetreuung fiel die Wahl schließlich auf Visual Components.
Der erste Eindruck unserer Kunden von den Simulationen war stets vor allem positiv.
Alois Wiesinger, M.Sc. (Tech.), Produktentwickler bei Fill
3D-Simulation – die Implementierungsphase
In der neunmonatigen Implementierungsphase erstellte das Projektteam die ersten Simulationen und die Parallelmodelle für eine standardisierte Komponentenbibliothek. Die Standard-Industriekomponenten, wie Förderbänder und Roboter, konnten der Komponentenbibliothek von Visual Components entnommen werden. Zahlreiche Spezialkomponenten wurden dagegen jeweils von dem Partner DUALIS modelliert.
Bereits die ersten 3D-Simulationen fanden bei den Fill-Kunden große Resonanz.
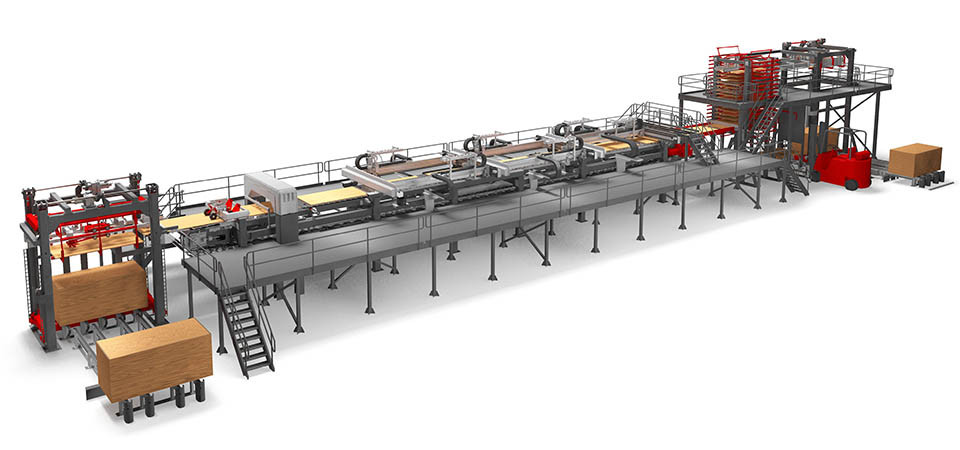
Über die Simulation zur Systemoptimierung
Von der Simulation profitieren nicht nur Marketing und Vertrieb, sondern auch das Werksdesign selbst. Die Simulation leistet einen Beitrag zur Optimierung und hilft insbesondere, im Vorfeld Fehler zu vermeiden.
Ein praktisches Beispiel aus der Holzindustrie: Erste Berechnungen ergaben eine Produktionsleistung von 500 Brettern pro Stunde für die Produktionslinie. Die Simulation zeigte jedoch, dass aufgrund von Fehlern im Antrieb und der infolgedessen reduzierten Vorschubgeschwindigkeit die Leistung tatsächlich nur bei 400 Brettern pro Stunde lag.
Mit Hilfe der Simulation wurde der entscheidende Engpass entdeckt. Die Projektplaner optimierten daraufhin die Prozesse und steigerten die Leistung einiger Ressourcen. Nach Abschluss des Verfahrens konnte die Produktionsleistung auf 500 Bretter pro Stunde gesteigert werden.
„Ausschlaggebend für die frühzeitige Aufdeckung der Schwachstellen im System waren die Ergebnisse der Simulation und die realistische Modellierung dynamischer Wechselbeziehungen. Nur so konnten wir am Ende die Vorgaben zur vollsten Zufriedenheit für alle Beteiligten erfüllen“, sagt Alois Wiesinger.
Das Beispiel zeigt, dass die Simulation für die Erreichung der Zielvorgaben einer Produktionslinie von unschätzbarem Wert ist.