DHL: Erfolge durch 3D-Verpackungssimulation
Erfahren Sie, wie das weltgrößte Logistikunternehmen DHL die Fertigungssimulation von Visual Components nutzt, um im Zeitalter beschleunigter Digitalisierung auf Automatisierung zu setzen.
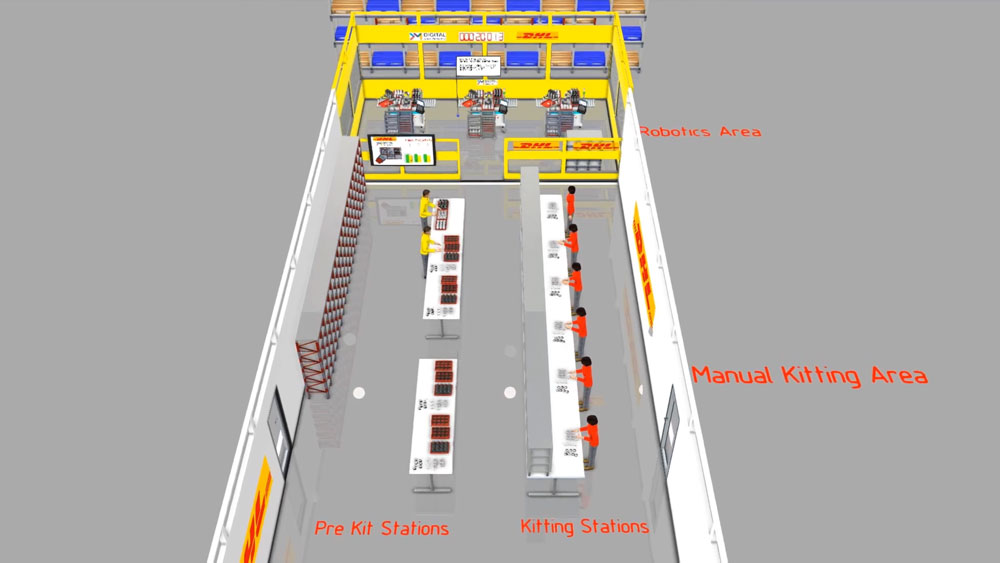
Als Adrian Dalsey, Larry Hillblom und Robert Lynn 1969 DHL gründeten, konnten sie nicht ahnen, dass sie damit die Welt der Logistik revolutionieren würden. Heute ist DHL das führende Logistikunternehmen der Welt. Mit mehr als 550.000 Mitarbeitenden in über 220 Ländern hilft es Unternehmen, grenzüberschreitend neue Märkte zu erschließen und weiter zu wachsen.
Digital Manufacturing fungiert innerhalb der Lieferkette von DHL als Innovations- und Technologieentwicklungszentrum für Robotik und Automatisierung, das für die Beschaffung, Fertigung und Integration von Robotiklösungen zuständig ist, durch die DHL robuste und nachhaltige Wettbewerbsvorteile erzielen kann.
Laden Sie hier die gesamte Fallstudie im PDF-Format herunter.
Die Herausforderungen
Digital Manufacturing ermittelte die folgenden Herausforderungen, vor die sich DHL im Verpackungsbereich typischerweise gestellt sieht:
- Customizing – Die Fähigkeit, unterschiedliche Verpackungslösungen vielschichtigen Kunden in unterschiedlichen Industriezweigen wie Gesundheitswesen, Pharmazie, Automobilherstellung, Finanzdienstleistungen und Lebensmittel & Getränke anzupassen.
- Strikte Verpackungsanforderungen – Hochkomplexe ausgelagerte Lieferketten erfordern ein hohes Maß an technischer Überwachung, um effizient und präzise zu funktionieren.
- Visualisierung – Die Fähigkeit, Kunden vor Augen zu führen, wie ihr Betrieb von DHL profitiert und wie DHL Effizienzgewinne, Kostensenkungen und eine vermehrte Automatisierung bei Verpackungsprozessen für sie erzielen kann.
Zu diesen Herausforderungen erklärte George Walsh, Product Development Engineer bei Digital Manufacturing, DHL: „Das ständig veränderliche Wesen und die Wettbewerbsintensität in Lieferketten und Logistik bedeutet, dass wir unsere Automationssysteme zeitnah und zu den niedrigstmöglichen Kosten entwickeln müssen.
Flexible und robuste Lösungen sind wesentlich für den nahtlosen Service, den DHL bietet. Simulation und Visualisierung der Herausforderung sind hierbei der Schlüssel zu unserem Erfolg. Durch Simulationssoftware und Prozessmodellierung können wir unseren Kunden zeigen, wie wir ihr Geschäft optimieren können, ohne dass es zu Unterbrechungen in ihren Abläufen kommt. Durch Simulation lässt sich die Automatisierung verbessern, um Effizienzgewinne zu erzielen.“
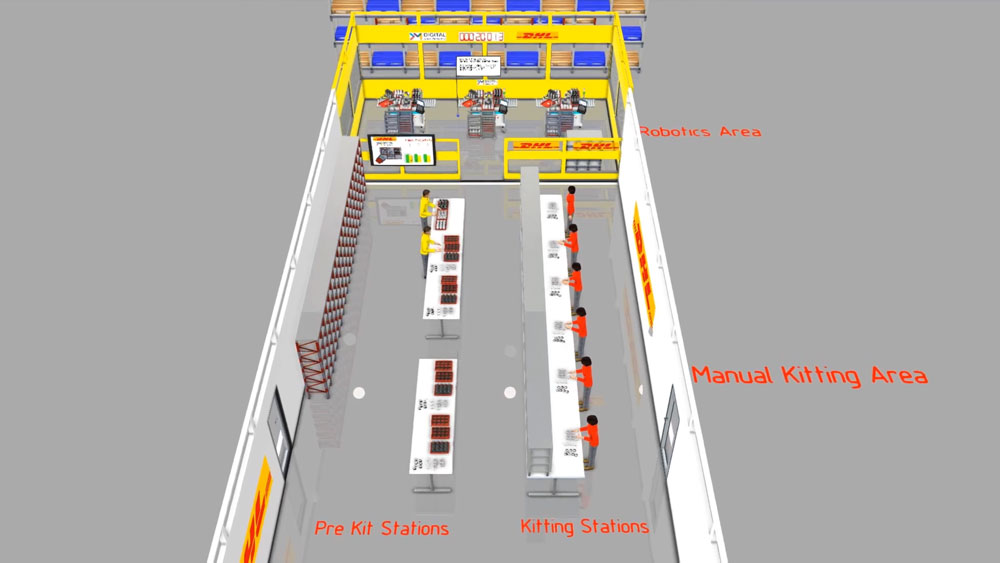
Warum hat sich DHL für Visual Components entschieden?
Es gab mehrere Gründe, warum Visual Components als Simulationstool für DHL-Projekte gewählt wurde. Digital Manufacturing nennt beispielsweise folgende:
- Visual Components ist eine fortschrittliche Plattform, die für unterschiedlichste Zwecke von der Modellbildung und Layoutplanung bis hin zur Geräteverifizierung und Prozessoptimierung eingesetzt werden kann.
- Einfache Handhabung und unkomplizierte Arbeitsabläufe erleichtern die Modellierung von Verpackungslösungen und Prozessen.
- Eine umfangreiche Bibliothek von parametrischen und wiederverwendbaren Modellen im E-Katalog von Visual Components spart Zeit beim Simulationsaufbau.
- Es ermöglicht eine schnelle und einfache Modellierung von kundenspezifischen Geräten, die für Simulationen mit realem Verhalten genutzt werden können.
- Hochwertige Grafiken und die Möglichkeit zum Export von Inhalten machen es zu einem visuellen Kommunikationstool.
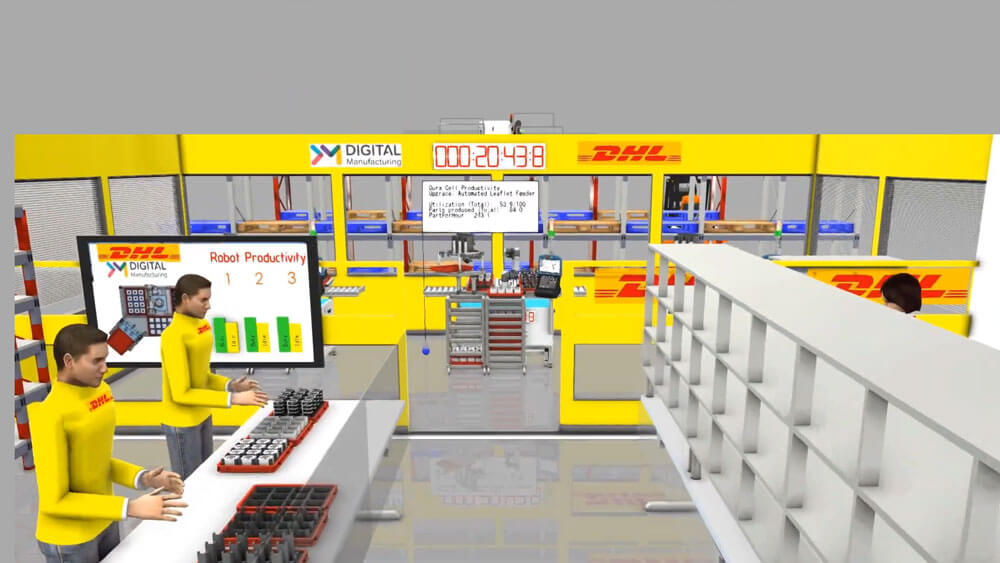
Digital Manufacturing berichtete über verschiedene Fallstudien, bei denen die Simulation mit Visual Components zur Straffung von Abläufen und Verbesserung der Prozesseffizienz in unterschiedlichen Situationen beigetragen haben.
Verpackungssystem in der Gesundheitsbranche – Steigerung der Prozesseffizienz um 35%
In dieser Fallstudie geht es um ein Produktionssystem in der Gesundheitsbranche, bei dem manuelle Verpackungsprozesse an vielen individuellen Arbeitsstationen in ganz Großbritannien ausgeführt wurden. Digital Manufacturing sah die Gelegenheit, durch die Automatisierung nicht wertschöpfender Aufgaben und durch beste Praktiken im Bandabgleich die Effizienz der Produktionsanlage zu verbessern. Durch die Umstellung von einzelnen Arbeitsstationen auf eine balancierte Fließfertigung ermöglichte Visual Components validierte Effizienzverbesserungen in Höhe von 35%.
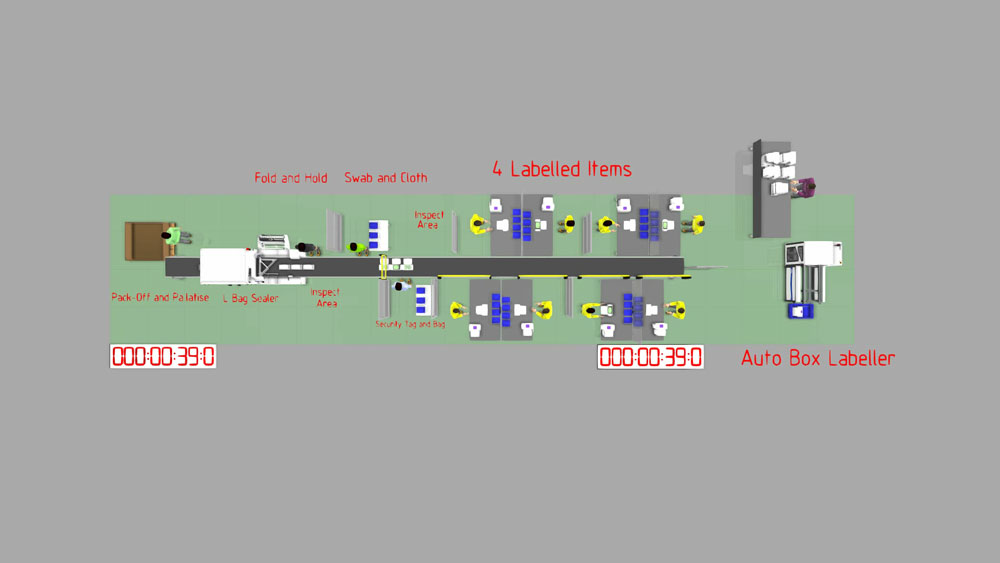
Dank der Simulation konnte die Funktionalität des Prozesses dem Kunden visuell nahegebracht werden, was die Entscheidungsfindung und Umsetzung beschleunigte. Zwischen dem ersten Konzept nach Beobachtung des manuellen Betriebs und der Erstellung der ersten Simulation vergingen nur drei Wochen – und von der Präsentation der Simulation bis zur Bestätigung des Projekts weitere drei Wochen. Nur zwei Wochen nach der Entscheidung wurde die erste Anlage gebaut. Die Simulation mit Visual Components ermöglichte nicht nur eine realistischere Demonstration des gesamten Prozesses mit tatsächlichen Produkten und Aufgaben, sondern schuf beim Kunden auch das nötige Vertrauen, um Produktionsentscheidungen schneller zu treffen, als dies ohne Simulation für gewöhnlich der Fall ist.
Verpackung elektronischer Waren – Erhöhung der Produktivität um 35% bei unveränderten Kosten.
Der Kunde wollte verstehen, welche Auswirkungen die Erweiterung von bislang einer auf drei parallel betriebene robotergestützte Fertigungslinien bei minimalem Bedienereingriff haben würde. Visual Components ermöglichte es dem Digital Manufacturing-Team, mit Automatisierungskonzepten für die Fertigungslinie zu experimentieren und so ein ausgewogenes Gleichgewicht aus Kosten, Skalierbarkeit und Leistung zu finden. Mittels Simulation ließ sich die Produktivität der einzelnen Konzepte in der Entwicklungsphase berechnen. Dies erleichterte die Auswahl des optimalen Szenarios anhand datengestützter Fakten. Das gewählte Produktionskonzept verbessert die Produktivität der einzelnen Robotersysteme um 34%, verlängert die Abstände zwischen den Bedienereingriffen von 7 auf 50 Minuten und reduziert die Gesamtbedienungszeit um die Hälfte auf 9 Minuten.
Projektziele übertroffen
Mit Hilfe von Visual Components konnte DHL erhebliche betriebliche Verbesserungen und Kosteneinsparungen erzielen, von denen seine ausgelagerten Kunden profitierten. Der hieraus resultierende Wettbewerbsvorteil ermöglichte DHL die Gewinnung weiterer Kunden. Hier sind einige der wichtigen Vorteile und Fakten, die DHL anführte:
1. Visuelles Kommunikationstool
Mit Hilfe der Software konnte der Kunde von DHL verstehen, wie sich die von DHL vorgeschlagenen Veränderungen (mittels Automatisierung) auf die Effizienz der Fertigungslinie auswirken würde. Dies half, den Kunden zu überzeugen.
2. Effizienzgewinne
Die Umstellung von einzelnen Arbeitsstationen auf eine balancierte Fließfertigung ermöglichte validierte Effizienzverbesserungen in Höhe von 35%.
3. Bessere Grundrissdisposition
Der benötigte Flächenbedarf nahm um 33% ab, während die Produktionseffizienz um 35% stieg.
4. Frühzeitige Erkennung möglicher Probleme
Die Simulation ermöglichte eine Verbesserung der Automatisierung und des Prozessflusses und eine Zentralisierung der Arbeitsteilung am Fließband. Damit konnte die Mitarbeiterzahl von 39 VZÄ auf 13 VZÄ reduziert werden, ohne dass Einbußen in Bezug auf Durchsatz, Qualität oder Arbeitsfluss entstanden.
5. Schnelle Iteration verschiedener Konzepte
Mehrere Simulationsszenarios werden dazu verwendet, den optimalen Produktionsfluss und Robotereinsatz im Vergleich zum menschlichen Betrieb zu berechnen. Hierdurch verbessert sich die Roboterproduktivität um 14%, während Bedienereingriffe statt alle 7 Minuten nur noch alle 50 Minuten erforderlich sind und sich die Gesamtbedienungszeit um die Hälfte verkürzt.
Zur Rolle von Visual Components in verschiedenen industriellen Bereichen erklärte George Walsh:
Durch Visual Components ist es uns gelungen, vermehrte Effizienzgewinne zu erzielen und die Verpackungs- und Verarbeitungskosten zu senken. Gleichzeitig konnten wir unseren Kunden vor Augen führen, wie die Automatisierung insgesamt zu höheren Effizienzgewinnen in der Produktion beitragen würde. Dies ist ein Game Changer.
George Walsh, Product Development Engineer bei Digital Manufacturing, DHL
Zusammenfassung
DHL verwendete Visual Components, um seine Verpackungsproduktion zu verbessern, seine Verpackungskosten zu senken und im Verpackungsprozess für seine ausgelagerten Kunden eine vermehrte Automatisierung zu implementieren – und um durch den damit einhergehenden Wettbewerbsvorteil neue Kunden zu gewinnen. Bei den meisten DHL-Fällen, in denen Simulationen zum Einsatz kommen, geht es um Folgendes:
- Gestaltung, Optimierung und Verifizierung von Verpackungsprozessen und der produktionstechnischen Machbarkeit
- Erhöhung der Kapazität und Flexibilität durch Automatisierung
- Dynamische Präsentation von Lösungen gegenüber den Führungsverantwortlichen von Kunden und Projekt-Stakeholdern
- Schnelle Abwicklung durch Entwurf und Erstellung von Simulationsmodellen
Zum Weiterlesen
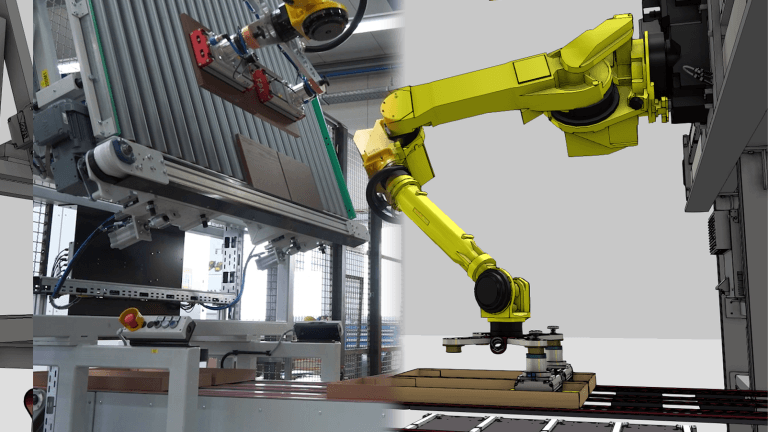
Verpackung in Perfektion: Wie Wächter Packautomatik mit Visual Components die Variationen bei Möbelverpackungen bewältigt
Möbel waren früher überwiegend teure, handwerklich hergestellte Einzelstücke, die teilweise über Generationen genutzt wurden. Heute werden die meisten Möbel in Massen- und Serienproduktion aus MDF- oder Spanplatten hergestellt, oft auch...
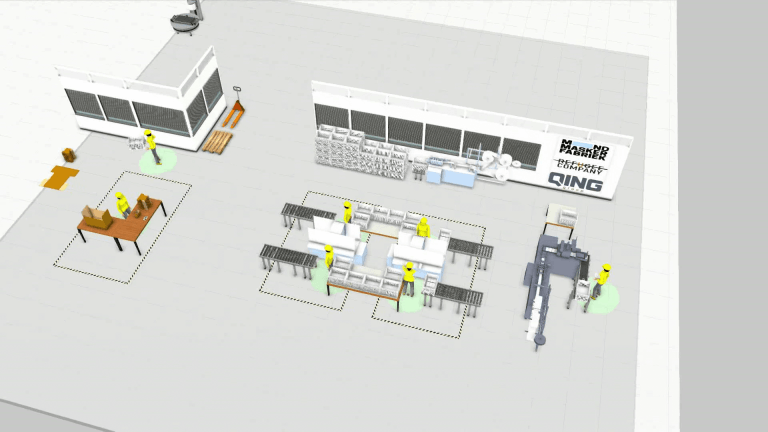
Fallstudie QING: Einsatz von 3D-Simulationstechnologie zum Aufbau einer Fabrik für Gesichtsmasken während der COVID-19-Pandemie
In dieser Fallstudie betrachten wir, wie QING mithilfe von 3D-Fertigungssimulation innerhalb weniger Wochen eine voll funktionsfähige Fabrik für Gesichtsmaskenfabrik in den Niederlanden errichtete, um die hohe Nachfrage nach Gesichtsmasken während...
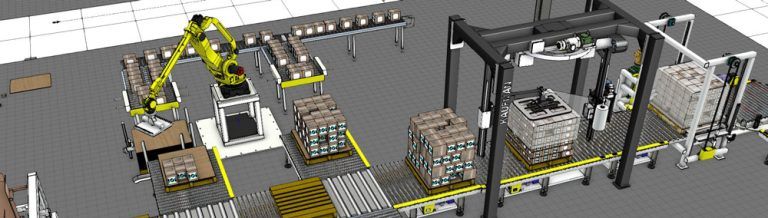
Kaufman-Fallstudie
Kaufman Engineered Systems aus Waterville, Ohio (USA) ist seit über 70 Jahren führend in der Automatisierung von Fertigungs- und Verpackungsstraßen.