Wie Roboter-Offline-Programmierung die Effizienz in Produktionslinien mit hoher Variantenvielfalt & niedrigen Stückzahlen steigert
Häufige Produktionsumstellungen und kleine Stückzahlen können die Produktion verlangsamen, aber es muss nicht so sein. Mit der Roboter-Offline-Programmierung (OLP) können Hersteller mit hoher Variantenvielfalt und geringen Stückzahlen (High-Mix, Low-Volume) Roboter zehnmal schneller programmieren, ohne die Produktion anzuhalten. Sehen Sie, wie Unternehmen OLP einsetzen, um mit der Nachfrage Schritt zu halten, Ausfallzeiten zu reduzieren und wettbewerbsfähig zu bleiben.
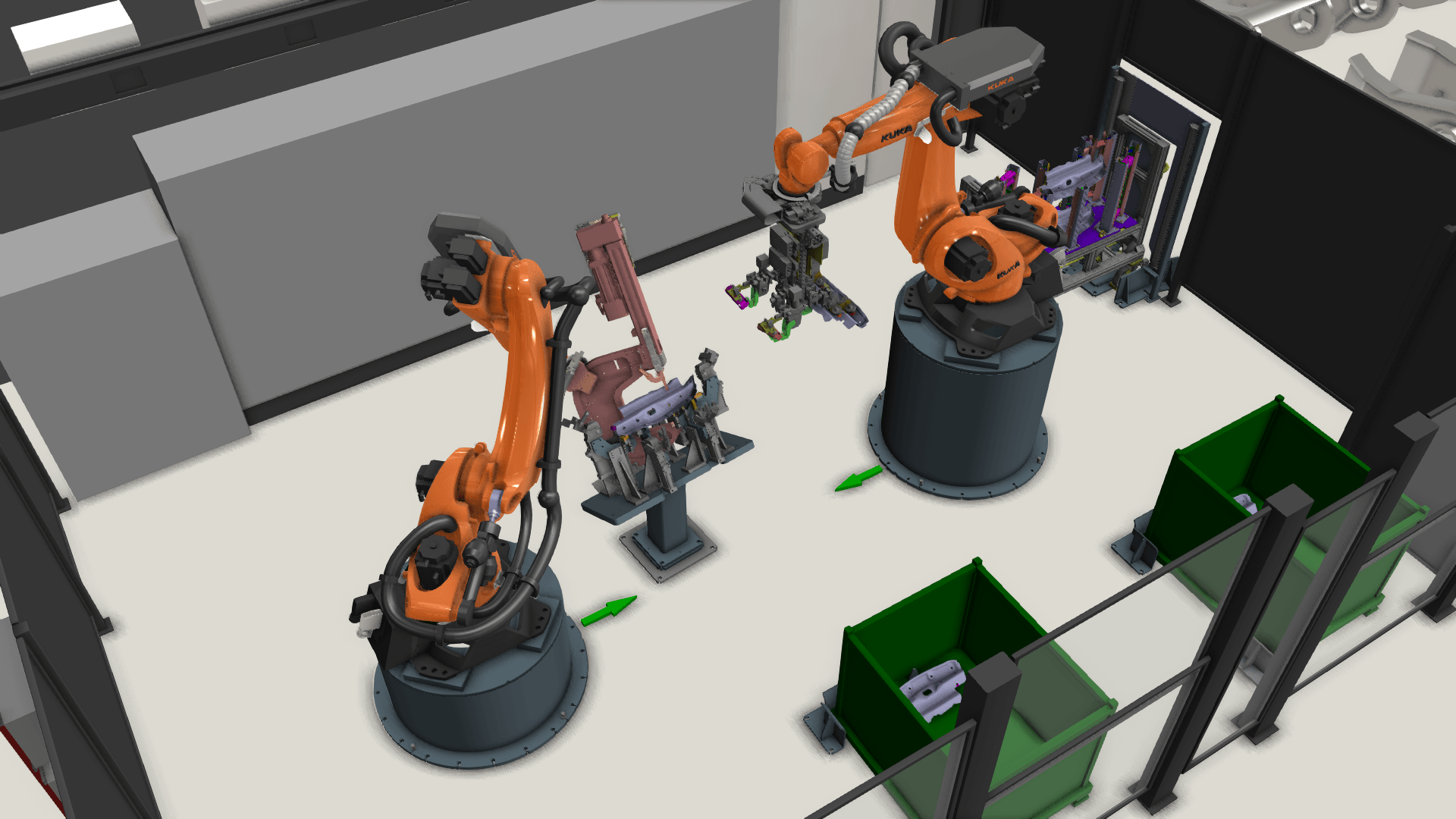
In der Produktion mit hoher Variantenvielfalt und geringen Stückzahlen (High-Mix, Low-Volume) kann schnelle Anpassungsfähigkeit den Ausschlag geben. Häufige Produktwechsel, unvorhersehbare Nachfrage und komplexe Arbeitsabläufe machen die herkömmliche Roboterprogrammierung langsam, teuer und schwer skalierbar. Hersteller benötigen eine Möglichkeit, den Betrieb reibungslos aufrechtzuerhalten, schneller auf neue Aufträge zu reagieren und ihre Ressourcen besser zu nutzen.
Manuelle Programmiermethoden sind diesen Herausforderungen oft nicht gewachsen, was zu Verzögerungen und Arbeitsunterbrechungen führt. Hier kommt die Roboter-Offline-Programmierung (OLP) ins Spiel, die einen schnelleren und flexibleren Ansatz bietet, mit dem Hersteller Roboter programmieren können, ohne die Produktion zu unterbrechen.
Herausforderungen für die manuelle Roboterprogrammierung in der Produktion mit hoher Variantenvielfalt und geringen Stückzahlen
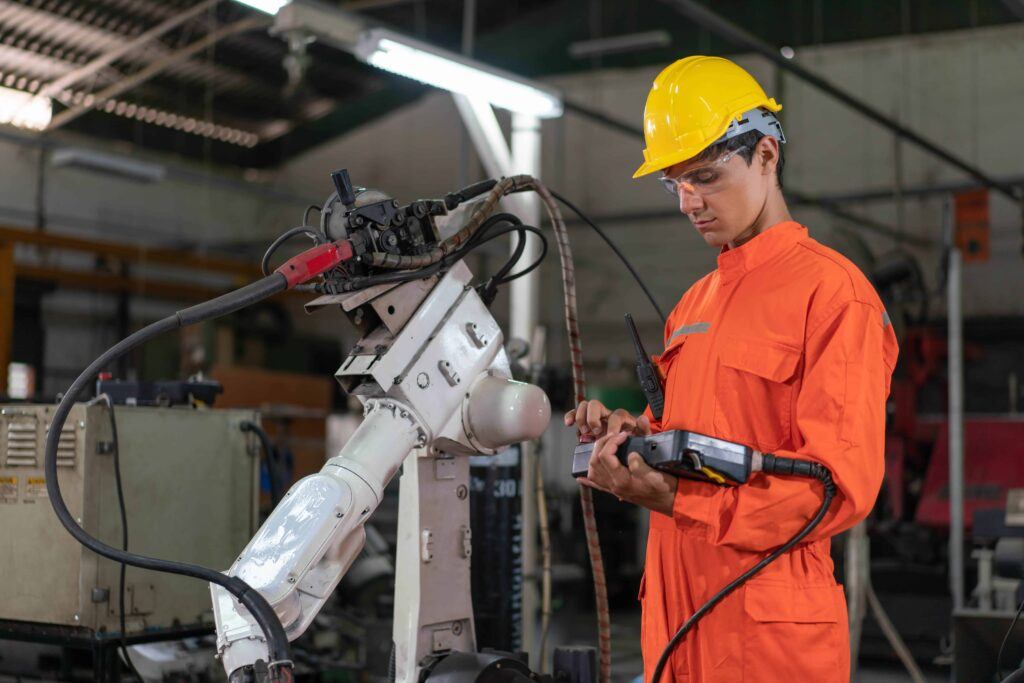
Die traditionelle Roboterprogrammierung ist zwar seit Langem der Industriestandard, hat jedoch Schwierigkeiten, mit den Anforderungen einer Produktion mit hoher Variantenvielfalt und geringen Stückzahlen Schritt zu halten. Hersteller in Branchen wie dem Maschinenbau, der Schweißtechnik und der Metallverarbeitung müssen Roboterprogramme häufig an neue Produktvarianten anpassen, doch manuelle Methoden sind langsam, kostspielig und ineffizient.
Jedes neue Teil oder Variante erfordert eine neue Programmierung, die oft Stunden oder sogar Tage in Anspruch nimmt. Da die Roboter für die Programmierung außer Betrieb genommen werden müssen, summieren sich diese Verzögerungen, stören den Arbeitsablauf und verzögern die Lieferungen. Die Skalierung der Produktion ist eine weitere Herausforderung, da Hersteller oft nur über eine begrenzte Anzahl qualifizierter Programmierer verfügen, was zu Engpässen führt, die die Flexibilität beeinträchtigen.
Darüber hinaus wird die manuelle Programmierung mit jeder weiteren Produktentwicklung immer zeitaufwändiger. Die Anpassung von Bahnen und Parametern der Roboter an neue Layouts oder Produktänderungen kann zu Produktionsausfällen, Umsatzverlusten und höheren Arbeitskosten führen.
Um diese Ineffizienzen zu überwinden, setzen Hersteller digitale Lösungen wie die Roboter-Offline-Programmierung ein, um die Roboterprogrammierung zu optimieren, die Automatisierung zu verbessern und in einem sich schnell entwickelnden Markt wettbewerbsfähig zu bleiben.
Wie die Roboter-Offline-Programmierung die Produktion mit hoher Variantenvielfalt und geringen Stückzahlen verändert
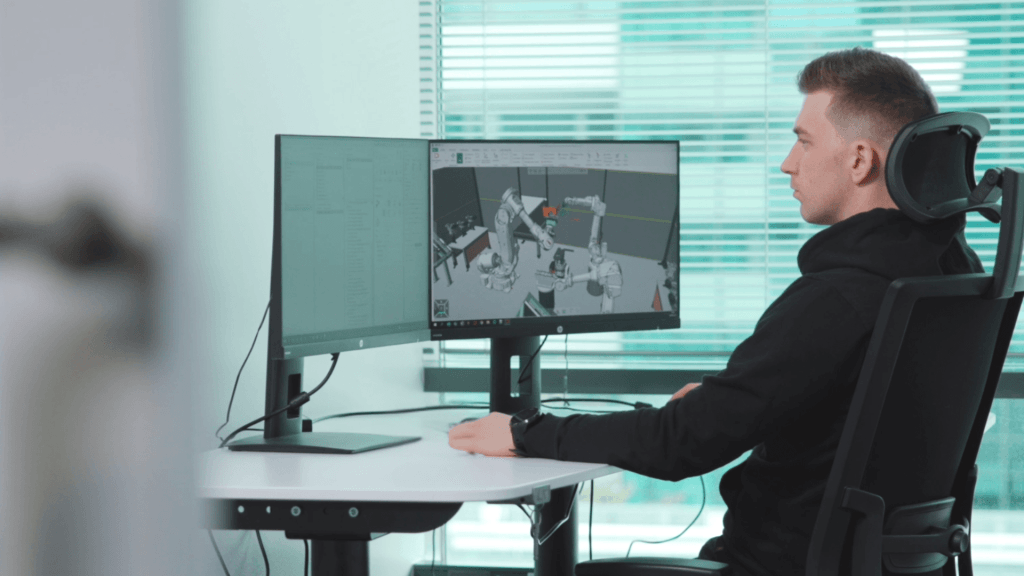
Die Roboter-Offline-Programmierung (OLP) ermöglicht es Herstellern, Roboterprogramme in einer virtuellen Umgebung zu entwickeln, zu testen und zu verfeinern, ohne die Produktion anzuhalten – daher auch der Begriff „offline“. Im Gegensatz zu herkömmlichen Programmiermethoden, bei denen Roboter manuell in der Produktionsstätte programmiert werden, verlagert OLP den Prozess in einen digitalen Raum, sodass Hersteller Roboterprogramme erstellen und validieren können, bevor sie diese einsetzen.
Durch die Simulation realer Produktionsbedingungen hilft OLP Herstellern, Roboterbahnen zu optimieren, potenzielle Probleme wie Kollisionen frühzeitig zu erkennen und die konsistente Qualität der Produktion sicherzustellen. Dies verbessert die Genauigkeit bei Anwendungen wie Schweißen, Montage und Materialhandhabung und erleichtert die Aktualisierung von Roboterprogrammen für neue Produktdesigns, Prozessverbesserungen oder Layoutänderungen.
Durch die optimale Auslastung der Roboter verbessert die Roboter-Offline-Programmierung die Produktivität, senkt die Kosten und macht die Produktion mit hoher Variantenvielfalt und geringen Stückzahlen in einer sich schnell verändernden Fertigungsumgebung skalierbarer und effizienter.
Praktische Anwendungen der Roboter-Offline-Programmierung
Hersteller auf der ganzen Welt nutzen die Visual Components OLP-Software, um die Effizienz bei der Produktion mit hoher Variantenvielfalt und geringen Stückzahlen zu steigern. Hier sind einige Erfolgsgeschichten:
Duun Industrier hat eine Roboterzelle im Voraus programmiert, um die Effizienz zu maximieren
Duun Industrier, ein norwegischer Hersteller von schweren Maschinen, programmiert seine Schweißroboterzellen mit der OLP-Software von Visual Components im Voraus. So konnten sie dafür sorgen, dass ihre neue Roboter-Schweißstation vom ersten Tag an mit minimalem Aufwand in Betrieb genommen werden konnte und sich schnell bezahlt gemacht hat.
Es ist wichtig, dass wir so schnell wie möglich mit der Programmierung dieser neuen Roboterzelle beginnen, ohne das bestehende Roboterzellensystem zu unterbrechen. Der physische Roboter wird in etwa einem Monat hier eintreffen und wir müssen unbedingt mit der Programmierung der Yaskawa ArcWorld-Roboterzelle beginnen, damit sie vom ersten Tag an voll einsatzfähig ist.
Rolf Even Duun, CTO bei Duun Industrier
AMI Attachments hat die Programmierzeit um 70 % verkürzt
AMI Attachments, ein nordamerikanischer Hersteller von Anbaugeräten für schwere Maschinen, hat mit der OLP-Software von Visual Components die Programmierzeit um 70 % reduziert, die Produktionseffizienz gesteigert und gleichzeitig den Arbeitskräftemangel ausgeglichen.
Die Erstellung und Überprüfung eines Programms von Grund auf in der Fertigung würde mindestens zwei Wochen dauern. Ich kann das offline in ein paar Tagen erledigen. Nach dem Einreichen zur Überprüfung und Überarbeitung benötigen wir insgesamt etwa vier Tage. Das bedeutet, dass wir etwa eineinhalb Wochen gewinnen. Es ist viel reproduzierbarer, präziser und effizienter. Das Programm ist sauber, für jeden leicht lesbar und alles ist viel klarer und einfacher zu handhaben.
PJ Muker, Robotics Supervisor und leitender Programmierer bei AMI
Bunorm Maschinenbau hat die Qualität und Effizienz beim Schweißen verbessert
Bunorm Maschinenbau, ein Full-Service-Schweißdienstleister, nutzt die Visual Components OLP-Software, um komplexe Teile vor der Produktion zu programmieren und zu optimieren. Das sorgt für eine schnellere Programmierung und bessere Schweißqualität, auch bei kleinen Chargen.
Du siehst, dass ich mit diesen drei Anweisungen gerade 41 Programmzeilen erstellt habe. Ohne Visual Components OLP würden wir das nicht als effizient genug für den Roboter erachten, wenn wir es von Hand auf dem Controller programmieren müssten.
D’Angelo Michael, Strategic Welding Solutions Manager bei Bunorm Maschinenbau
Berlin Gardens hat die Effizienz um 80 % gesteigert
Berlin Gardens hat die OLP-Software von Visual Components eingeführt, um das Roboterschweißen zu optimieren. Dadurch konnte die Programmierzeit um 80 % reduziert und gleichzeitig die Qualität und Genauigkeit verbessert werden.
Der größte Unterschied war die Anzahl der Punkte, die man durch einfaches Auswählen eines Gelenks in der Software programmieren konnte. Vorher war die Punkt-zu-Punkt-Programmierung mit dem Handbediengerät sehr repetitiv. Mit der Software können wir jede Bewegung immer wieder mit den gleichen Einstellungen steuern.
Derrick Yoder, Aluminum Production Manager bei Berlin Gardens
Ponsse hat die Roboterprogrammierung um das Zehnfache beschleunigt
Ponsse, ein finnischer Marktführer in der Forstwirtschaft, hat die Roboterprogrammierung mit der OLP-Software von Visual Components von zehn Tagen auf einen Tag verkürzt und so die Produktivität deutlich gesteigert.
Die Offline-Programmierung macht die Roboterprogrammierung viel schneller und einfacher, weil sie außerhalb des Produktionssystems und ohne Produktionsunterbrechung durchgeführt werden kann. Früher mussten wir die notwendigen Anpassungen am Wochenende vornehmen, bevor die Produktion am Montag wieder aufgenommen werden konnte.
Asko Haataja, Head of Robotics Team bei Ponsse
VOLVO Construction Equipment erhöht die Flexibilität in der Fertigung mit vorrichtungslosem Roboterschweißen (Jigless Welding)
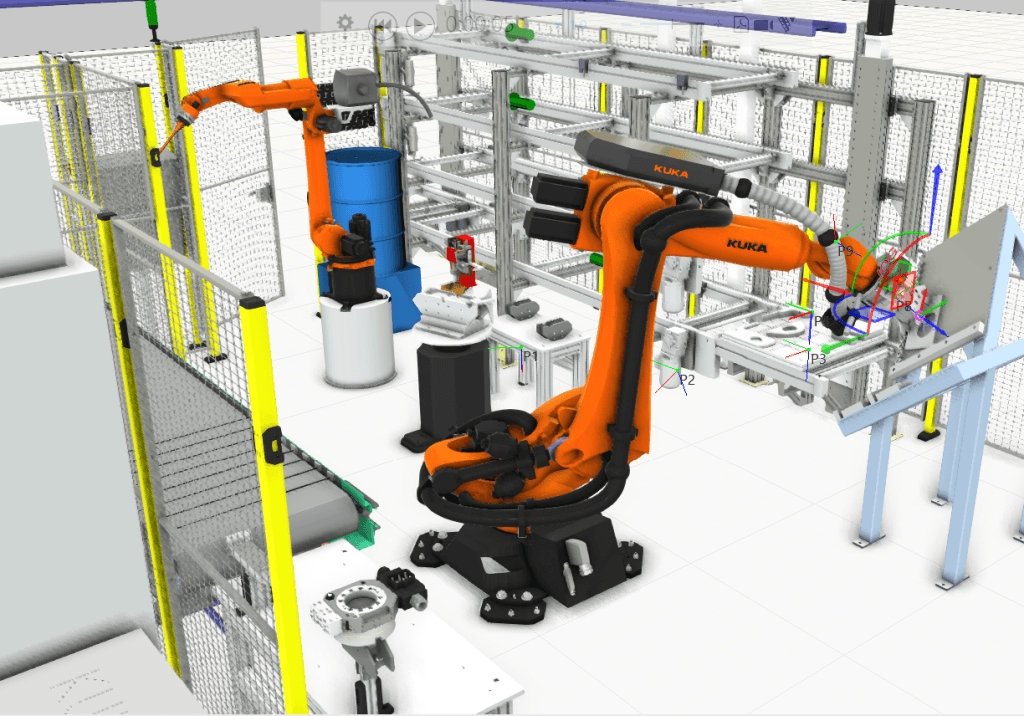
VOLVO Construction Equipment nutzt die OLP-Software von Visual Components, um schnell Roboterprogramme zu erstellen, die das vorrichtungslose Roboterschweißen (Jigless Welding) von 30 Kleinserienartikeln in einem kontinuierlichen One-Piece-Flow ermöglichen.
Wir wollten die beste technische Lösung und Software, die mit möglichst vielen Robotermarken funktioniert. Die OLP-Software von Visual Components ist sehr übersichtlich und lässt sich intuitiv programmieren.
Erik Åstrand, Welding Optimization Specialist bei VOLVO Construction Equipment
HT Laser steigert die Produktivität in der komplexen Metallfertigung mit hoher Variantenvielfalt
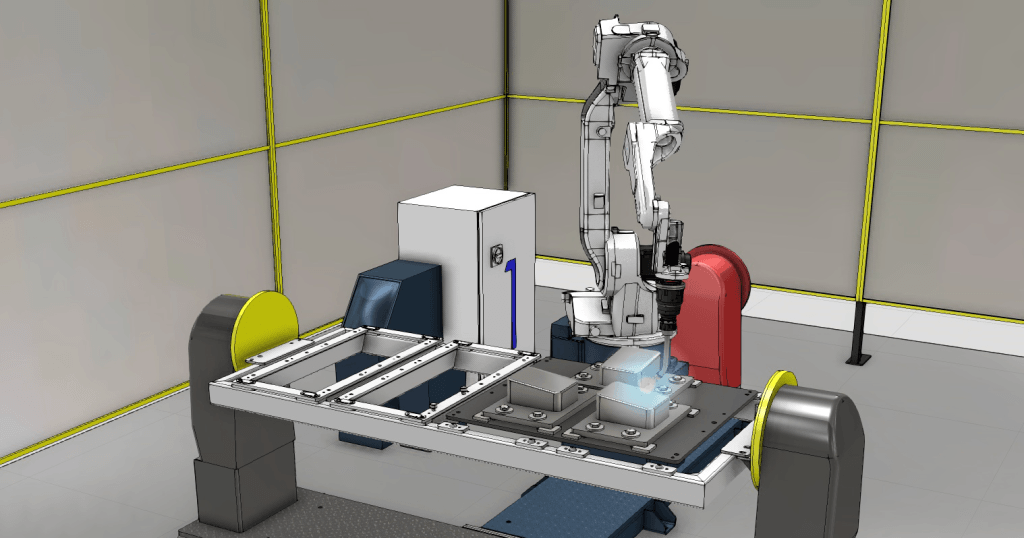
HT Laser konnte mit der OLP-Software von Visual Components erhebliche Zeitersparnisse erzielen, Produktionsstillstände vermeiden und sicherere, effizientere Schweißvorgänge ermöglichen.
Der größte Vorteil ist die Zeitersparnis, da die Programmierung ohne Unterbrechung der Produktion und ohne teure Maschinen durchgeführt werden kann. Zeitsparend sind auch bestimmte Softwaremakros, die den Programmiervorgang beschleunigen. Die Offline-Programmierung löst auch das Problem, wenn das zu schweißende Teil groß ist oder sich an einer Stelle befindet, die schwer oder gefährlich zu erreichen ist.
Janne Tuominen, Product Development Manager bei HT Laser
AFRIT hat die Produktion verdoppelt
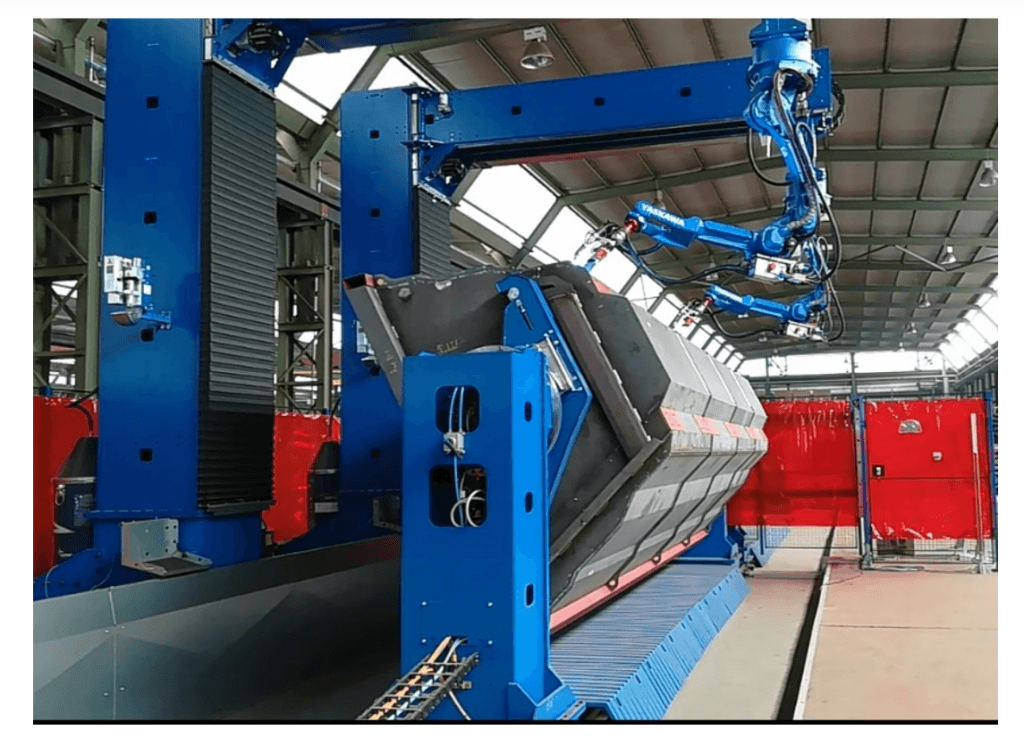
AFRIT, ein südafrikanischer Anhängerhersteller, reduzierte den manuellen Programmieraufwand um 80 % und steigerte die Produktion von 8 auf bis zu 20 Behälter pro Tag durch den Einsatz der OLP-Software von Visual Components.
Unsere Teile sind einheitlicher und die Wiederholgenauigkeit beim Schweißen hat sich erheblich verbessert. Da wir keine manuelle Programmierung und Nachbesserungen an der Programmierung mehr vornehmen müssen, haben wir mehr Zeit, um das Schweißen und andere Systeme zu optimieren.
Ferdi Beukes, Mechatronic Engineer bei Afrit
Warum OLP die Zukunft der Produktion mit hoher Variantenvielfalt und geringen Stückzahlen ist
OLP ist nicht nur ein Werkzeug, um Ausfallzeiten zu reduzieren, sondern spielt auch eine wichtige Rolle bei der Verbesserung der allgemeinen Produktionsanpassungsfähigkeit im weiteren Sinne. Durch die Integration von OLP in Fertigungsabläufe können Unternehmen einen optimierten, datengesteuerten Ansatz für die Automatisierung schaffen, der über die Programmierung hinausgeht.
Ein wesentlicher Vorteil ist die bessere Zusammenarbeit zwischen den Ingenieuren und den Produktionsteams. Da die OLP-Software die Entwicklung und Validierung von Programmen in einer virtuellen Umgebung ermöglicht, können Ingenieure gemeinsam an Roboteraufgaben arbeiten, bevor diese in die Fertigung gelangen. Dadurch werden kurzfristige Anpassungen reduziert und sichergestellt, dass die Roboterabläufe mit den Produktionsplänen übereinstimmen, wodurch Störungen minimiert werden.
OLP unterstützt auch datengestützte Entscheidungen. Viele moderne Offline-Programmierungswerkzeuge lassen sich mit Simulations- und Analysesoftware integrieren und bieten Einblicke in die Roboterleistung, Durchlaufzeiten und Prozesseffizienz. Anhand dieser Daten können Hersteller Roboterabläufe optimieren, Arbeitslasten ausgleichen und Verbesserungspotenziale identifizieren, bevor Probleme die Produktion beeinträchtigen.
Ein weiterer Vorteil ist die Möglichkeit, die Automatisierung effizienter zu skalieren. Wenn Hersteller neue Produktlinien einführen oder ihre Produktionskapazitäten ausbauen, erleichtert OLP die Inbetriebnahme zusätzlicher Roboter ohne langwierige Programmierverzögerungen. Dank standardisierter und wiederverwendbarer Roboterprogramme können Unternehmen bewährte Prozesse in mehreren Werken oder Produktionszellen replizieren und so Konsistenz in großem Maßstab gewährleisten.
Außerdem ist OLP eine Ergänzung zu anderen digitalen Fertigungstechnologien wie KI-gesteuerter Optimierung und IoT-fähiger vorausschauender Wartung. Durch die Integration der Offline-Programmierung in die Echtzeit-Produktionsüberwachung können Hersteller den Roboterbetrieb auf Basis tatsächlicher Leistungsdaten kontinuierlich optimieren und so die langfristige Effizienz und Zuverlässigkeit verbessern.
Durch die Einführung von OLP als Teil einer umfassenderen Automatisierungsstrategie lösen Hersteller nicht nur unmittelbare Herausforderungen bei der Programmierung, sondern schaffen auch eine agilere, skalierbare und datengesteuerte Produktionsumgebung. Dies hilft Unternehmen, in der Produktion mit hoher Variantenvielfalt und geringen Stückzahlen wettbewerbsfähig zu bleiben und sich gleichzeitig auf zukünftige Fortschritte in der Robotik und digitalen Fertigung vorzubereiten.
Möchtest du deine Produktion effizienter gestalten? Kontaktiere uns, um mehr über die Implementierung von OLP in deinen Produktionsablauf zu erfahren.
Zum Weiterlesen
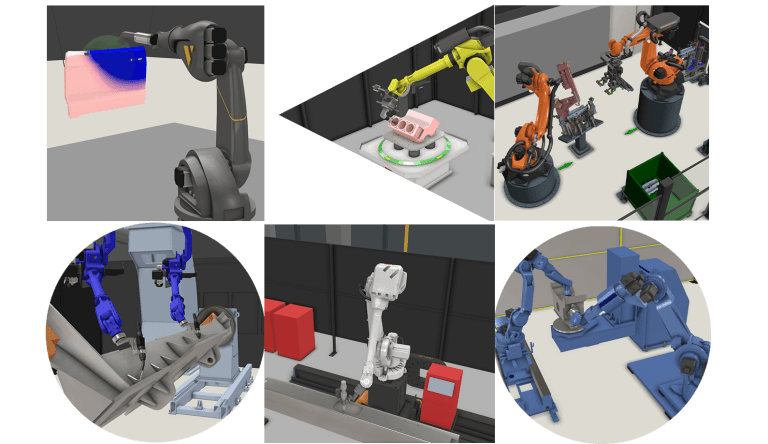
Roboterprogrammierung für industrielle Prozesse mit Visual Components OLP Software
Die Offline-Programmierung treibt die Roboterprogrammierung voran, indem sie es Herstellern ermöglicht, Roboteraufgaben virtuell zu optimieren, ohne die Produktion zu unterbrechen. Dadurch werden Ausfallzeiten minimiert, die Genauigkeit verbessert und Prozesse wie...
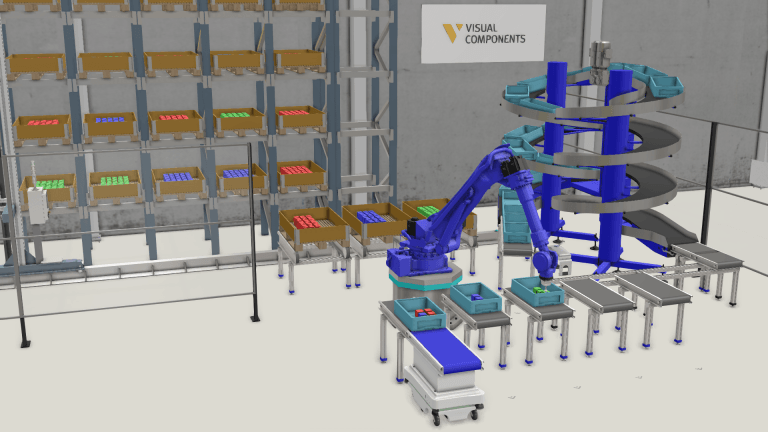
Produktionslinien auf intelligente Weise mit Simulation optimieren
Hersteller sind ständig auf der Suche nach Verbesserungsmöglichkeiten – sei es durch höheren Durchsatz, weniger Engpässe oder eine effizientere Ressourcennutzung. Ohne die richtigen Werkzeuge kann die Optimierung von Fertigungslinien jedoch...
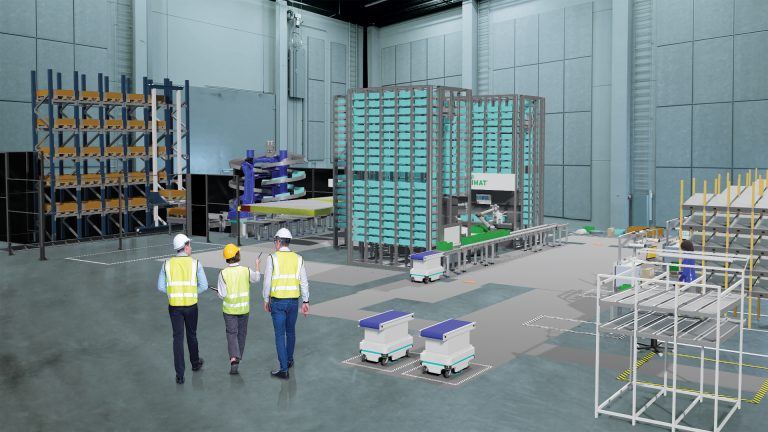
Die Zukunft der automatisierten Fertigung (und warum Menschen weiterhin wichtig sind)
Die Automatisierung in der Fertigung entwickelt sich seit Jahrzehnten weiter, aber ihr eigentlicher Einfluss liegt nicht darin, Menschen zu ersetzen, sondern sie leistungsfähiger zu machen. Wir haben mit Mika Anttila,...