Trends in der Automobilproduktion im Jahr 2022 und darüber hinaus
Wir betrachten vier wichtige Trends, die sich auf die Automobilfertigung auswirken.
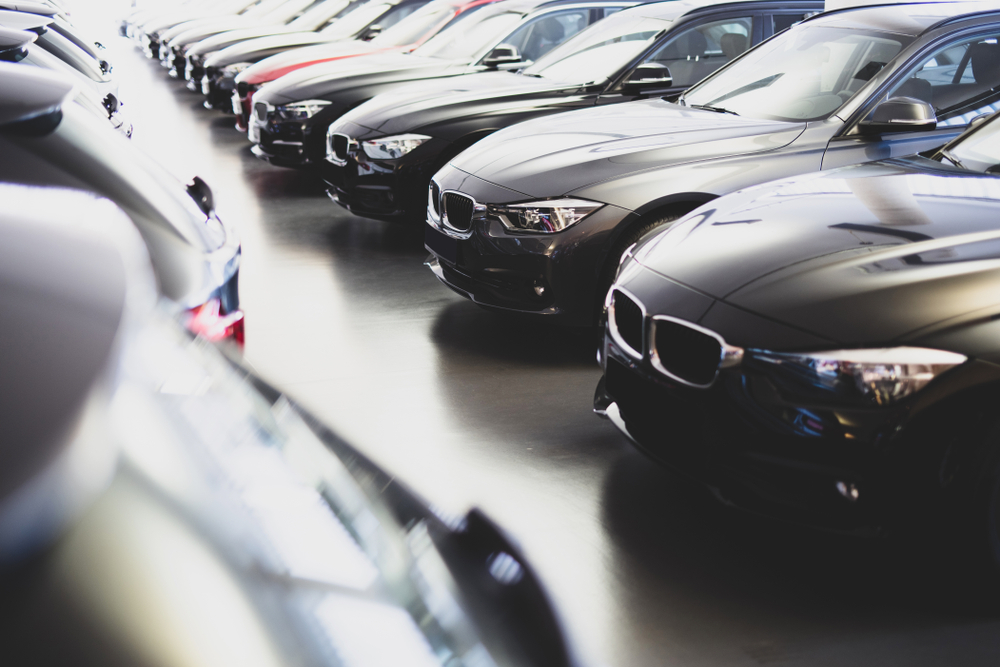
Wenn sich die Vorhersagen bewahrheiten, werden Autos und LKWs in zehn Jahren ganz anders aussehen als heute. Antriebssysteme verändern sich, Fahrzeuge werden „intelligenter“ und funktionieren möglicherweise schon bald ohne menschliches Einwirken. Vielleicht werden sie eher gemeinschaftlich genutzt, anstatt einen festen Eigentümer zu haben. Vielleicht aber auch nicht. Je nachdem, auf welche Experten man hört. Die asiatischen Automobilmärkte werden jene in Europa und Nordamerika in den Schatten stellen.
Für Fahrzeughersteller, Erstausrüster und ihre Zulieferer, Tier-1- und selbst Tier-2-Lieferanten sind diese Veränderungen mit Unsicherheit und Risiken verbunden. Montage- und Fertigungsstätten sollen Jahrzehnte fortbestehen. Ausrüstung wird in der Annahme eingekauft, dass sie 10 Jahre oder mehr eingesetzt wird. Dennoch beschleunigen sich die Lebenszyklen von Modellen, und tiefgreifende Veränderungen im Fahrzeugdesign sind schon heute zu sehen. Wie also kann man Maschinen und Produktionsanlagen angesichts der ungewissen Zukunft definieren und kaufen?
Visual Components kann das nicht beantworten. Wir können jedoch Tools anbieten, die Erstausrüstern, Tier-1- und Tier-2-Lieferanten sowie ihren Maschinenbauern und -integratoren bei der Bestimmung, wie die Antwort lauten könnte, helfen.
Unsere Simulationstools bieten Benutzern diese Fähigkeiten. Darüber hinaus wollen wir Möglichkeiten erkunden, wie sie zur Gestaltung optimaler Fertigungslayouts und -vorrichtungen beitragen. Zunächst einmal betrachten wir jedoch die fünf wichtigsten Trends, die sich auf die Automobilproduktion auswirken. Das sind folgende:
- Elektrifizierung und Plattformen
- Konnektivität und Autonomie
- Das IIoT
- Kostensteuerung
Elektrifizierung und Plattformen
Getrieben durch die Ziele zur Emissionsreduzierung der Regierungen und den Druck durch bestimmte Verbraucher setzt die Branche zunehmend auf Elektrifizierung. Kurzfristig werden wahrscheinlich Hybridfahrzeuge dominieren, mit der Zeit werden sich jedoch rein elektrische Antriebe durchsetzen. Die Produktion von Elektrofahrzeugen scheint sich auf jeden Fall auf die Montagewerke von Erstausrüstern und Tier-1- und Tier-2-Lieferanten auszuwirken.
Die Batterieherstellung wird weltweit zur Massenproduktion. Gigantische Werke werden entstehen. Gleichzeitig drängen neue Unternehmen auf den Markt, die ausschließlich Plattformen für Elektrofahrzeuge für herkömmliche Hersteller fertigen. Dadurch wird der Trend hin zur Produktion vor Ort beschleunigt. Dabei basieren kleine Produktionszentren auf einem standardisierten Grundsatz der agilen Produktion. Dieser kann vielfach an verschiedenen Standorten repliziert werden, um Produkte in der näheren Umgebung zu vertreiben. Dadurch werden die mit der Transportlogistik sowie mit der Anlagengröße und -kapazität verbundenen Kosten reduziert.
Dies bringt drastische Veränderungen mit sich. Motorenmontagewerke und die Lieferketten, die diese unterstützen, werden schrumpfen oder sogar verschwinden. Die Fahrzeugmontage wird sich drastisch verändern – mit weniger Komponenten und Unterbaugruppen. Schon heute können wir sehen, dass Erstausrüster in die Batterie- und Motorherstellung investieren.
Konnektivität und Autonomie
Konnektivität hat vielfältige Auswirkungen auf Fahrzeuge. Fahrer erwarten zunehmend, dass sie in ihrem Auto über die gleiche Internetanbindung wie zu Hause verfügen. Gleichzeitig bewegt sich die Automobilbranche in Richtung einer Standardsoftware für jedes Fahrzeug mit der Möglichkeit, dass der Halter später jederzeit konfigurierbare Funktionen per WiFi oder 5G hinzufügen kann.
Die über die konstante Verbindung erfassten Daten bieten Herstellern viele Möglichkeiten, das Kundenerlebnis zu verbessern und neue Einnahmequellen zu erschließen, d. h. Optimierung des Fahrzeugdesigns, der Wartung, Services und Leistung sowie Vorschläge für neue, personalisierte Services und Anwendungen gemäß den Fahrgewohnheiten des Halters. Das ist einer der Gründe, warum Big-Tech-Unternehmen an Konnektivität im Fahrzeug interessiert sind.
Darüber hinaus ermöglicht Konnektivität die Kommunikation von Fahrzeug zu Fahrzeug (C2C) und von Fahrzeug zu Infrastruktur (V2I), die Unfälle reduziert und den Verkehrsfluss in zunehmend verstopften Städten verbessert.
Im Hinblick auf Autonomie gestaltete sich die Aufgabe, Fahrzeuge zu entwickeln, die sich durch unvorhersehbare Umgebungen steuern, bisher schwieriger als angenommen. Auch wenn es nennenswerte Ausnahmen gibt, scheinen die meisten Hersteller und Entwickler zu glauben, dass die Antwort in der Verbindung von Kameras und LIDAR mit künstlicher Intelligenz (KI) zu finden ist. Fahrerassistenzsysteme (FAS) wie automatisches Bremsen kommen bei Verbrauchern gut an. Die ersten Anwendungen für wirklich autonomes Fahren sind jedoch eine ganz andere Sache. Fahrten über große Strecken, Lieferdienste und vielleicht auch örtliche Transportshuttles sind mögliche Geschäftsszenarien.
Das IIoT
Das industrielle Internet der Dinge (IIoT) gilt als ein Grundpfeiler der 4. Industriellen Revolution und ermöglicht es Maschinenbauern und -integratoren, ihre Linien mit kostengünstigen Sensoren auszustatten, die Daten zu Analysezwecken in die Cloud streamen.
Die Daten bilden die Betriebsleistung bis auf Komponentenebene ab. Durch Kopplung dieser Daten mit einem digitalen Zwilling können Betriebe eine präzise Darstellung der Prozesse erzielen. Diese wiederum hilft bei der Lösung von Problemen, der fortlaufenden Verbesserung, Fernvisualisierung, flexiblen Planung und beim Änderungsmanagement.
Hersteller suchen genau wie bei den von ihnen produzierten Fahrzeugen nach intelligenteren, agilen, vielfältig konfigurierbaren Lösungen, um die Autonomie und Effizienz des Alltäglichen besser an zukünftigen Änderungen auszurichten, Störungen und Kosten zu minimieren und gleichzeitig das Leistungspotenzial von Assets zu maximieren.
Kostensteuerung und Änderungsmanagement
Zwei Kostenkomponenten, auf die sich Hersteller stärker konzentrieren, sind Kapazitätsauslastung und Garantiekosten.
Die Kapazitätsauslastung spielt eine wichtige Rolle, da die Fahrzeugmontage enorm kapitalintensiv ist, genau wie die Fertigung von Untersystemen und Komponenten. Zur Maximierung der Rendite ist eine hohe Auslastung der Fertigungslinien und Maschinen erforderlich. Bei dieser Praktik geht es letztendlich darum, „das Maximum aus Wirtschaftsgütern herauszuholen“. Dadurch rücken Leistungskennzahlen wie die Gesamtanlageneffektivität und eine genaue Aufmerksamkeit auf Verschwendung und Materialausnutzung weiter in den Fokus.
Um die Leistung optimieren zu können, bedarf es minutengenauer Daten zum Geschehen. Demnach werden Vorrichtungen mit Kameras und anderen Sensoren zur Überwachung und Erfassung der Produktion ausgestattet. Zugleich unterstützen Nachverfolgungstechnologien, die eine vollständige Historie einer jeden Fahrzeugkomponente erstellen, die Ursachenanalyse im Falle von Feldausfällen oder Garantieansprüchen.
Folgen für die Automobilproduktion
Autos verändern sich offensichtlich, genau wie die Art und Weise, wie sie und ihre Bestandteile gefertigt werden. Die Unternehmen in der Branche, die sich am besten darauf vorbereiten, sind auch die, die am meisten profitieren. Drängt sich die Frage auf: welche Herausforderungen müssen sie erforschen und angehen? Die wichtigsten drei aus Fertigungsperspektive sind wohl:
- Integration von Produktionsflexibilität für sich ändernde Volumen und neue Funktionen
- Steigerung der Maschinenauslastung und Reduzierung von Verschwendung
- Einbindung neuer Maschinen und Linien in ältere Vorrichtungen in Anlagen, die schon seit Jahrzehnten bestehen
Seit Einführung der Fließmontage hat sich die Branche zunächst auf die Mechanisierung und dann auf die Automatisierung konzentriert, um Personalkosten zu minimieren und die Ergebnisse zu standardisieren. Eine derartige fest zugeordnete oder auch „harte“ Automatisierung ermöglicht oftmals hohe Produktionsvolumen, ist jedoch meist nicht flexibel genug. Jedes neue Produktmerkmal macht eine umfassende Umrüstung erforderlich, d. h. die Linie oder Maschine muss für eine Weile außer Betrieb genommen werden.
Dies lässt sich mit Robotik umgehen. Roboter lassen sich schnell umprogrammieren, um den Änderungen am montierten Produkt gerecht zu werden. Sie haben jedoch Beschränkungen in Sachen Geschwindigkeit: Roboterfertigung ist selten so schnell wie eine spezielle Transferstraße. Darüber hinaus kann ein hochmodernes Robotersystem mehr als zweckbestimmte Ausrüstung kosten.
Hersteller müssen sich also entscheiden, wie viel Flexibilität sie sich wünschen und leisten können. Hybride Ansätze können unter bestimmten Umständen geeignet sein. Aufgrund der Unsicherheit in Bezug auf den Inhalt von Fahrzeugen der Zukunft ist diese Entscheidung jedoch zunehmend riskant und schwierig.
Angesichts der hohen Kapitalkosten von Fertigungsanlagen ist die Maximierung der Auslastung zwingend erforderlich. Ein zentrales Hilfsmittel dabei ist die Wartung, dank derer ungeplante Stillstände verhindert werden. Ohne genaue Daten über die Maschinen besteht jedoch die Gefahr, dass mehr Wartung als nötig und vielleicht auch die falsche Wartung durchgeführt wird.
Hier kommt die vorausschauende Wartung ins Spiel. Diese Lösung wird von immer mehr Herstellern, Maschinenbauern und -integratoren genutzt. Dabei senden IIoT-Sensoren Daten zur Temperatur, zum Flüssigkeitsstand, zur Viskosität, zu Vibrationen und anderen Indizien für den Zustand einer Maschinen in die Cloud. Dort werden sie analysiert, um Empfehlungen zu Wartungsarbeiten auszugeben, die durchzuführen sind, wenn es die Zeit erlaubt.
Ein weiterer Aspekt ist der Fernzugriff auf Maschinen. Anstatt Zeit und Geld für den Besuch einer Anlage aufzuwenden, kann ein Integrator aus der Ferne zugreifen, Fehler suchen und sogar ein Software-Upgrade durchführen.
Simulationen zur Optimierung der Zukunft
Wenige Hersteller kommen in den Luxus, neue Anlagen von Grund auf zu gestalten. Vielmehr müssen Maschinen und Linien für neue Ausrüstung in den vorhandenen Raum eingepasst werden und oftmals mit älteren Maschinen funktionieren. Dies bringt eine Vielzahl von Herausforderungen in Bezug auf das Layout und die Abstimmung/Optimierung des Durchsatzes mit sich. Trotz umfangreicher Verwendung von CAD und Digitalisierung ist es nach wie vor schwierig, in einer digitalen Umgebung alles richtig zu machen.
Angesichts der Vielzahl möglicher Konfigurationen und Layouts erfordert eine gründliche Prüfung der einzelnen Optionen mehr Zeit als verfügbar ist. Prüft man jedoch nicht jede einzelne Option oder sieht sich nur einige genauer an, besteht die Gefahr, dass die letztendliche Lösung suboptimal ist.
Wurde der optimale Ansatz bestimmt, müssen die Entscheidungsträger überzeugt werden. Tabellen und Diagramme haben wenig Effekt, und die Zahlen können überwältigen. Zudem ist es schwierig, mehr als nur ein paar geprüfte Alternative zu präsentieren, und Antworten auf „Was wäre wenn“-Fragen zu finden, ist gelinde gesagt eine Herausforderung.
Hier hilft 3D-Simulation.
3D-Simulation ermöglicht die Erstellung eines digitalen Zwillings der Fabrik, Linie oder Maschine. Anhand dieses Zwillings können dann die Folgen von Änderungen für den Produktionsablauf beurteilt, Engpässe ermittelt und die größten Auswirkungen der Änderungen bestimmt werden.
Ferner dient dieser digitale Zwilling der Unterstützung von Bestrebungen zur Datenerhebung für die Wartung und eine höhere Auslastung. So lässt sich erkennen, wo Instrumentierung die größten Verbesserungen und Erträge bringt.
Die Geschwindigkeit der Veränderungen in der Automobilbranche nimmt aufgrund von technologischen Entwicklungen und Umweltfaktoren zu. Dadurch müssen Hersteller aller Ebenen, Erstausrüster sowie Tier-1- & Tier-2-Lieferanten die Änderungen in den Fertigungsprozessen und -techniken unterstützen. Digitalisierungstools wie Simulation, digitale Zwillinge und virtuelle Inbetriebnahme bieten die Möglichkeit, aktuelle und zukünftige Lösungen zu visualisieren und validieren und so die Kosten für die Beurteilung, Implementierung und Nutzung trotz Anpassung an Veränderungen zu reduzieren.
Steven Robbie, Betriebsleiter – PR automation
Simulation ist ein Werkzeug für die Beurteilung von Alternativen. Das Abwägen der konkurrierenden Ziele hinsichtlich Kosten und Flexibilität umfasst viele Optionen: Simulation ermöglicht das Erstellen einer unbegrenzten Anzahl an Modellen. In jedes können die gleichen Produktionspläne und Herausforderungen gespeist werden. Die Leistung der einzelnen Modelle wird dann unter Berücksichtigung der anfallenden Kapitalkosten beurteilt.
Simulation hilft auch bei der Vermittlung von Lösungsvorschlägen. Die Beobachtung von Arbeitsabläufen ist nicht nur überzeugender als die Betrachtung von Diagrammen und Tabellen, sondern auch verständlicher. Mit einem VR-Headset erzielen Sie einen zusätzlichen Effekt, da der Betrachter in den digitalen Zwilling der vorgeschlagenen Linie „eintauchen“ kann.
Zum Weiterlesen
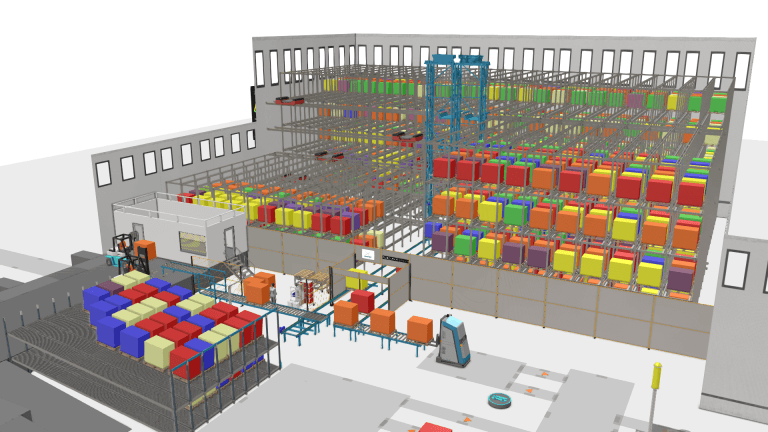
Effiziente Lagerplanung: Wie Simulationen helfen, Lagerprozesse zu optimieren
Wie können Unternehmen Lagerhäuser so gestalten, dass sie vom ersten Tag an effizient arbeiten und gleichzeitig die Arbeitskosten und andere Ausgaben im Zaum halten? Der Schlüssel liegt in einer intelligenten...
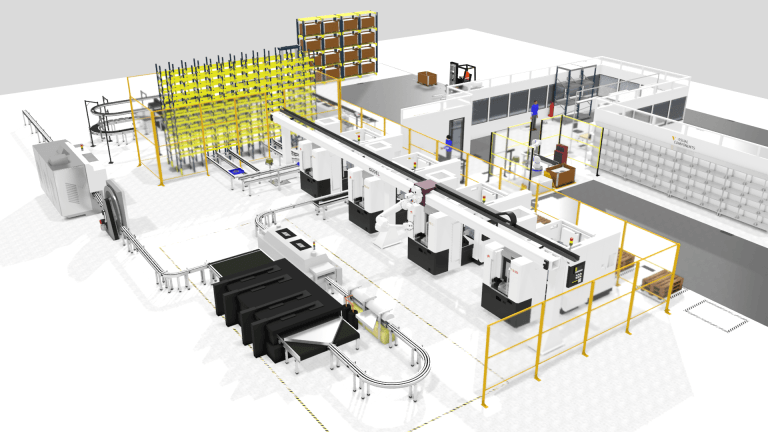
Umfassender Leitfaden zu Eingabedaten für die 3D-Fertigungssimulation
Wenn Sie neu in der 3D-Fertigungssimulation sind, sind Sie hier genau richtig. Dieser umfassende Leitfaden hilft Ihnen, die wesentlichen Eingabedaten zu verstehen, die für die Erstellung effektiver Simulationsmodelle erforderlich sind....
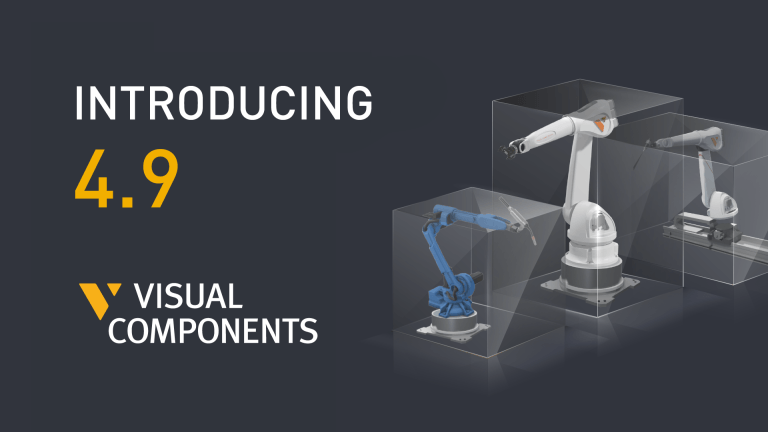
Visual Components 4.9: Gestalten mit Klarheit
Visual Components 4.9 bringt mehr Klarheit in die Produktionsplanung und -optimierung in der Fertigung. Mit mehr Klarheit können unsere Anwender mehr erreichen, einfacher und mit größerem Verständnis, besonders wenn sie...