Produktionslinien auf intelligente Weise mit Simulation optimieren
Hersteller sind ständig auf der Suche nach Verbesserungsmöglichkeiten – sei es durch höheren Durchsatz, weniger Engpässe oder eine effizientere Ressourcennutzung. Ohne die richtigen Werkzeuge kann die Optimierung von Fertigungslinien jedoch kompliziert werden. Hier kommt die Simulation ins Spiel: Sie ermöglicht es Herstellern, Prozessänderungen in einer virtuellen Umgebung zu testen, zu verfeinern und zu kommunizieren, bevor sie in der Praxis umgesetzt werden.
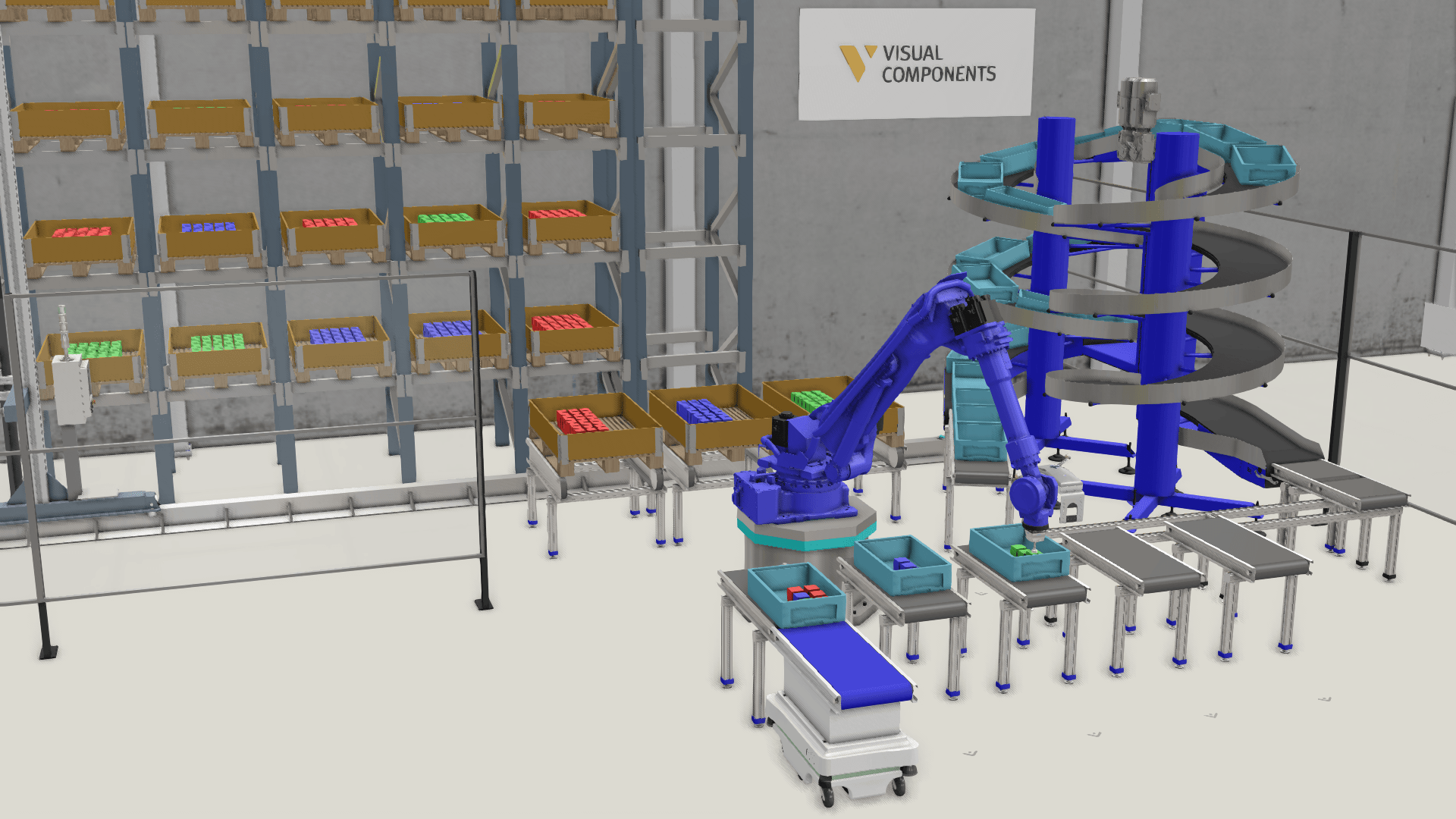
Produktionslinien auf intelligente Weise mit Simulation optimieren
Jeder Hersteller kennt den Druck, mehr zu produzieren, weniger zu verschwenden und einen reibungslosen Betrieb zu gewährleisten. Aber jeder, der schon einmal versucht hat, eine Produktionslinie zu optimieren, weiß, dass diese Aufgabe selten so einfach ist. Anpassungen fühlen sich oft wie ein Glücksspiel an: Eine Änderung, die eigentlich die Effizienz verbessern soll, kann stattdessen zu Engpässen, Ausfallzeiten oder Vorbehalten bei den Mitarbeitenden führen, die an die bestehenden Arbeitsabläufe gewöhnt sind.
Traditionelle Ansätze wie Lean Manufacturing und Six Sigma bieten strukturierte Methoden zur Beseitigung von Ineffizienzen, sind jedoch nach wie vor auf die praktische Umsetzung angewiesen, wodurch immer ein gewisses Maß an Unsicherheit besteht. Die eigentliche Herausforderung besteht darin, Prozesse zu optimieren, ohne die Produktion zu stören oder kostspielige Fehler zu verursachen.
Hier kommt die Simulationstechnologie ins Spiel. Anstatt Prozesse durch Ausprobieren zu optimieren, können Hersteller Änderungen zunächst virtuell testen und Layouts, Arbeitsabläufe und Automatisierungsstrategien in einer digitalen Umgebung verfeinern, bevor sie Anpassungen in der realen Welt vornehmen.
Warum die Optimierung bestehender Prozesse nach wie vor so schwierig ist
Selbst mit den heutigen digitalen Tools verlassen sich viele Hersteller bei der Planung von Prozessverbesserungen noch immer auf statische, veraltete Methoden.
Betrachten wir ein gängiges Szenario: Die Installation eines neuen Förderbandsystems zum Transport von Materialien zwischen Arbeitsstationen. Wenn sich das Layout als ineffizient erweist, lässt sich das Problem nicht einfach durch Verschieben von Komponenten beheben. Möglicherweise musst du die Produktion anhalten, Steuerungssysteme neu verkabeln oder sogar strukturelle Elemente ändern. Der Aufwand ist hoch und Fehler können kostspielig sein.
Neben physischen Herausforderungen stehen Hersteller auch vor organisatorischen Hindernissen
- Unklarer ROI – Führungskräfte zögern oft, Prozessänderungen ohne klare Belege für messbare Vorteile zu genehmigen.
- Mangelnde Abstimmung – Ingenieure, Bediener und Management haben möglicherweise unterschiedliche Vorstellungen davon, wie „Optimierung“ aussieht, was zu widersprüchlichen Prioritäten führen kann.
- Widerstand gegen Veränderungen – Mitarbeitende, die seit Jahren mit denselben Prozessen arbeiten, stehen neuen Methoden möglicherweise skeptisch gegenüber, insbesondere wenn die Vorteile nicht sofort erkennbar sind.
Laut McKinsey & Company können Hersteller, die datengesteuerte Prozessoptimierung und -automatisierung erfolgreich implementieren und skalieren, erhebliche Verbesserungen erzielen, darunter eine Steigerung der Arbeitsproduktivität um bis zu 30 %. Viele Unternehmen haben jedoch Schwierigkeiten, über kleine Pilotprojekte hinauszukommen, da sie keine breite Beteiligung der Stakeholder erreichen können, was zu einer Stagnation der Initiativen führt.
Herkömmliche Methoden sind unzureichend
Seit Jahrzehnten verlassen sich Hersteller bei der Prozessplanung auf einige wenige Standardwerkzeuge:
- CAD-Zeichnungen und 2D-Schemas – Nützlich für die grobe Layoutplanung, jedoch ohne echte Interaktivität.
- PowerPoint-Präsentationen und Berichte – Werden häufig zur Kommunikation von Änderungen verwendet, vermitteln jedoch keinen praktischen Eindruck davon, wie ein Prozess funktionieren wird.
- Manuelle Zeit- und Bewegungsstudien – Wertvoll für die Identifizierung von Ineffizienzen, jedoch arbeitsintensiv und oft unvollständig.
Diese Tools können zwar Verbesserungspotenziale aufzeigen, ermöglichen es den Herstellern jedoch nicht, sicher zu experimentieren oder Änderungen teamübergreifend effektiv zu kommunizieren. Aus diesem Grund setzen viele Unternehmen auf 3D-Fertigungssimulationen, mit denen sich Prozessänderungen testen, verfeinern und visuell demonstrieren lassen, bevor sie in der Praxis umgesetzt werden.
Einsatz von 3D-Simulationen zur Risikominimierung und Effizienzsteigerung
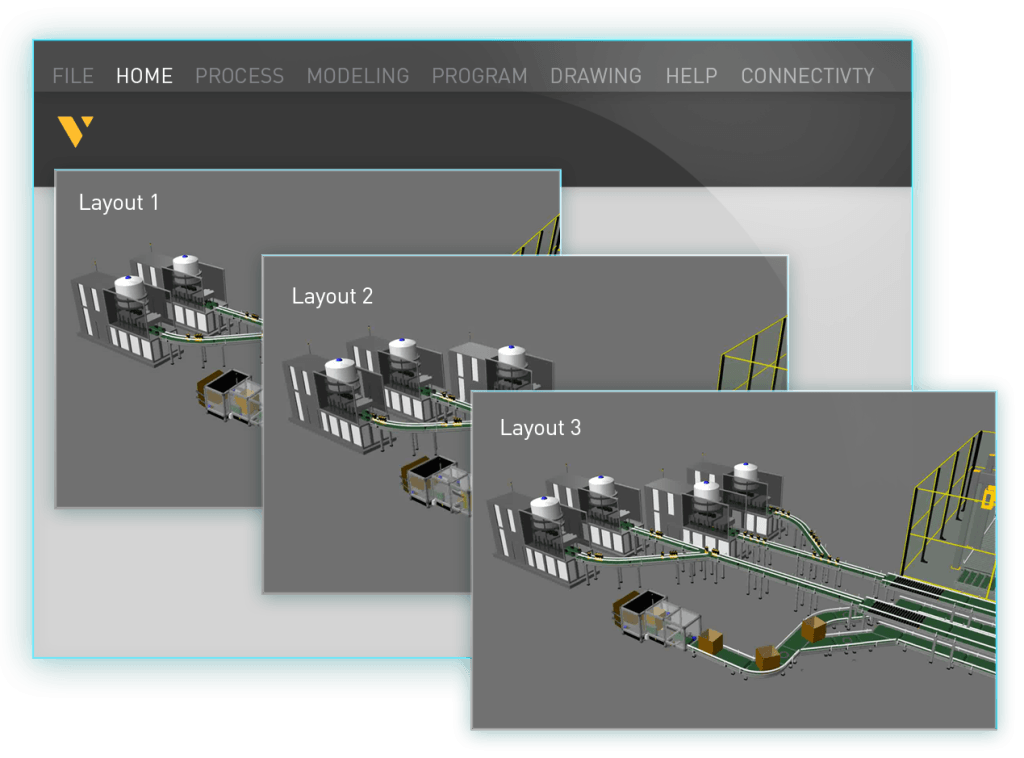
Anstatt Prozessänderungen mit Ungewissheiten vorzunehmen, können Hersteller mit einer 3D-Fertigungssimulation mehrere Szenarien in einer kontrollierten digitalen Umgebung bewerten und so sicherstellen, dass alle Beteiligten mit den vorgenommenen Änderungen vertraut sind. Die „virtuelle Inbetriebnahme“ mit Tools wie Visual Components geht noch einen Schritt weiter und ermöglicht es Herstellern, Automatisierungssysteme einschließlich SPS-Logik und Roboterprogrammen zu testen und zu validieren, bevor sie in der Fertigung eingesetzt werden. Ob es um das Testen eines neuen Produktionslayouts, die Integration von Automatisierung oder die Anpassung von Arbeitsabläufen geht – mit Simulationen lassen sich Ergebnisse vornehmen, bevor Anpassungen in der Praxis vorgenommen werden.
Wesentliche Vorteile der 3D-Fertigungssimulation
- Verbesserte Zusammenarbeit – Ingenieure, Anlagenbediener und das Management können Änderungen gemeinsam visualisieren und so vor der Implementierung aufeinander abstimmen.
- Minimiertes Produktionsrisiko – Tests finden in einer virtuellen Umgebung statt, wodurch kostspielige Unterbrechungen des Live-Betriebs vermieden werden.
- Datengestützte Entscheidungen – Prozessänderungen werden anhand realer Leistungskennzahlen und nicht nur anhand von Intuition evaluiert.
- Schnellere Iterationen und Experimente – Teams können Layouts schnell ändern, Automatisierungen einführen und Workflows optimieren, ohne die Verzögerungen und Risiken, die es bei physische Änderungen gibt.
Für Hersteller, die bisher gezögert haben, umfangreiche Prozessverbesserungen einzuführen, weil sie kostspielige Fehler befürchten, bietet die Simulation einen risikoarmen und hochpräzisen Ansatz für die Entscheidungsfindung.
Vom Konzept zur Realität, ohne Rätselraten
Die wahre Kraft der Simulation liegt in ihrer Fähigkeit, die Lücke zwischen Konzept und Realität zu schließen. Anstatt sich auf theoretische Modelle oder Vermutungen zu verlassen, können Hersteller realistische digitale Modelle erstellen, die ihre tatsächlichen Produktionsumgebungen widerspiegeln.
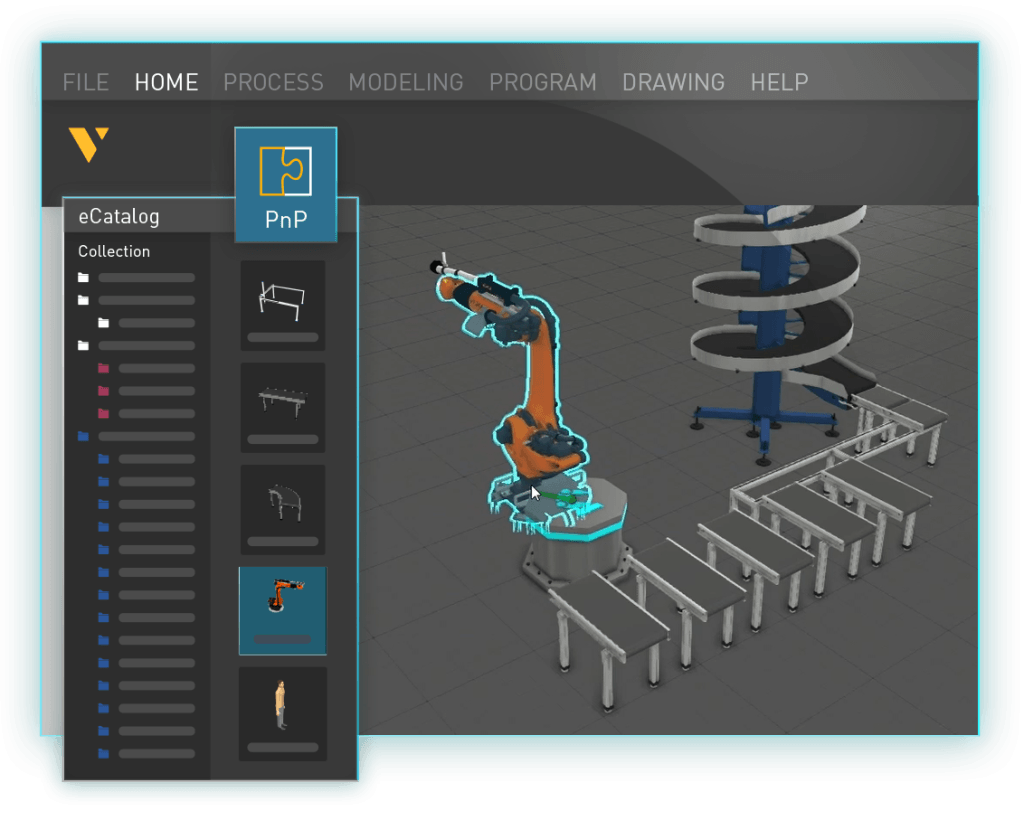
Mithilfe vorgefertigter Bibliotheken (wie dem Visual Components eCatalog) von Industrierobotern, Maschinen und Automatisierungskomponenten können Teams virtuelle Produktionsszenarien erstellen und verschiedene Konfigurationen innerhalb weniger Minuten testen. Anhand dieser Simulationen können Hersteller sehen, wie Geräte zusammenwirken, potenzielle Engpässe identifizieren und Prozesse optimieren, bevor sie in physische Änderungen investieren.
Über die einfache Visualisierung hinaus ermöglicht die Prozessmodellierung Teams Folgendes:
- Arbeitsabläufe und Materialflüsse planen.
- Regeln und Einschränkungen für automatisierte Systeme festlegen.
- Bewegungen und Interaktionen innerhalb der Produktionslinie simulieren.
Außerdem können Ingenieure mit Tools für die Fabrikplanung 2D-Zeichnungen, Punktwolkendaten und CAD-Modelle importieren, um supergenaue digitale Zwillinge von Produktionsräumen zu erstellen. Das verbessert die Raumplanung und die Zuweisung von Ressourcen und sorgt dafür, dass Änderungen nahtlos in die bestehende Anlage passen.
Daten in Taten umsetzen
Bei der Simulation geht’s nicht nur darum, Änderungen zu zeigen, sondern auch, ihre Auswirkungen zu messen. Durch das Erfassen und Analysieren wichtiger Leistungskennzahlen können Hersteller fundiertere, datengestützte Entscheidungen zur Prozessverbesserung treffen.
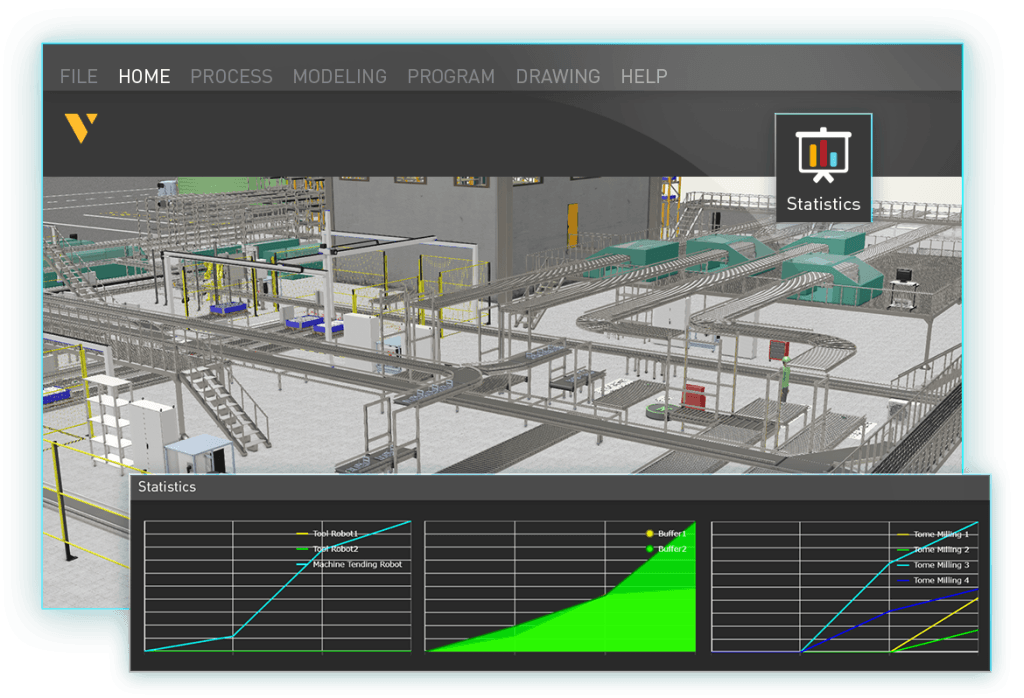
Zu den nützlichsten Einblicken, die Simulationen liefern, gehören:
- Durchlaufzeiten – Wie lange dauert jeder Schritt im Prozess?
- Engpässe – Wo gibt es Verzögerungen und wie kann man sie beheben?
- Ressourcenauslastung – Werden Maschinen und Mitarbeiter effizient eingesetzt?
Durch mehrere Simulationen können Hersteller verschiedene Konfigurationen vergleichen und die beste Lösung finden, ohne die Risiken und Kosten von Testläufen in der Praxis.
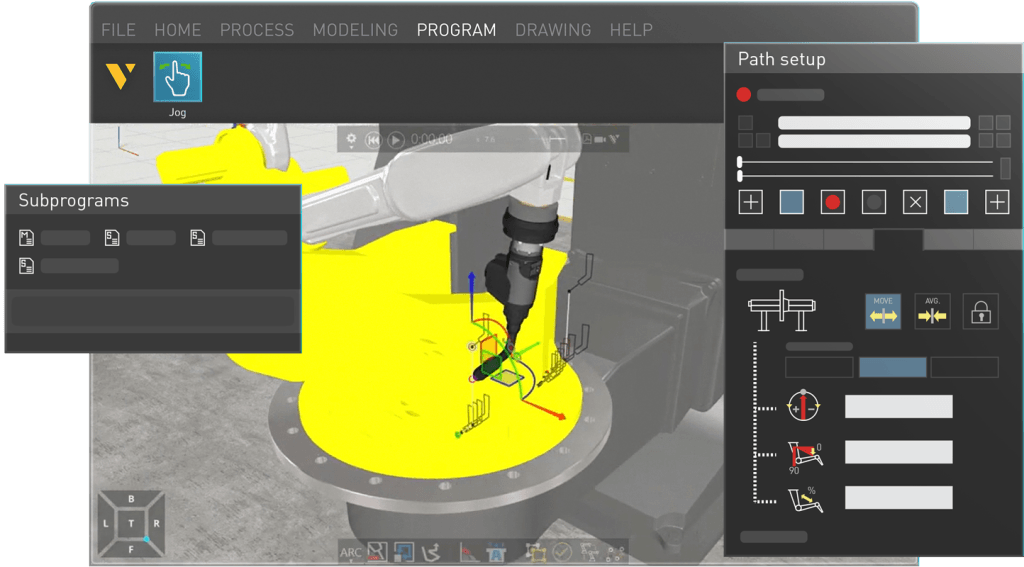
Für Hersteller, die Automatisierung und Robotik einsetzen, ist die Roboter-Offline-Programmierung (OLP) ein weiterer Schritt in Richtung der praktischen Umsetzung. Anstatt Roboter direkt in der Fertigung zu programmieren, wo Fehler zu Ausfallzeiten führen können, können Hersteller mit OLP die Roboterabläufe zunächst in einer virtuellen Umgebung optimieren. Das sorgt für eine schnellere und genauere Programmierung mit minimalen Unterbrechungen.
Simulation als smarterer Ansatz zur Prozessoptimierung
Von Henry Fords Fließband bis zu den automatisierten Smart Factories von heute – die Effizienz in der Fertigung hängt schon immer von kontinuierlichen Verbesserungen ab. Traditionelle Optimierungsmethoden haben zwar geholfen, aber oft hapert es an Vorhersagbarkeit, Geschwindigkeit und Risikomanagement.
Simulation macht Schluss mit dem Rätselraten bei der Prozessoptimierung. Sie sorgt dafür, dass jede Änderung auf Daten basiert, in einer virtuellen Umgebung getestet und abteilungsübergreifend abgestimmt wird. Das bringt Herstellern folgende Vorteile:
- Verbesserungen planen und testen, ohne dass die Produktion stillsteht.
- Automatisierungsstrategien optimieren, bevor sie eingesetzt werden.
- Prozessänderungen mit Zuversicht vornehmen, weil man weiß, dass die Ergebnisse auf echten Daten basieren.
Für Hersteller, die wettbewerbsfähig bleiben wollen, geht es nicht darum, ob sie Simulation einsetzen sollen, sondern wann sie damit anfangen können.
Bereit, die Vorteile der Simulation zu erleben?
Wenn du wissen willst, wie Simulationen deinem Unternehmen helfen können, zeigen wir dir gerne praktische Anwendungen und den möglichen ROI. Kontaktiere uns noch heute, um mehr zu erfahren.
Zum Weiterlesen
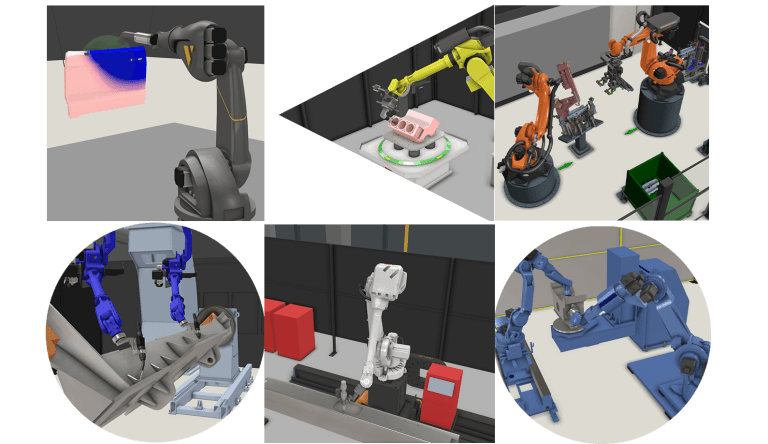
Roboterprogrammierung für industrielle Prozesse mit Visual Components OLP Software
Die Offline-Programmierung treibt die Roboterprogrammierung voran, indem sie es Herstellern ermöglicht, Roboteraufgaben virtuell zu optimieren, ohne die Produktion zu unterbrechen. Dadurch werden Ausfallzeiten minimiert, die Genauigkeit verbessert und Prozesse wie...
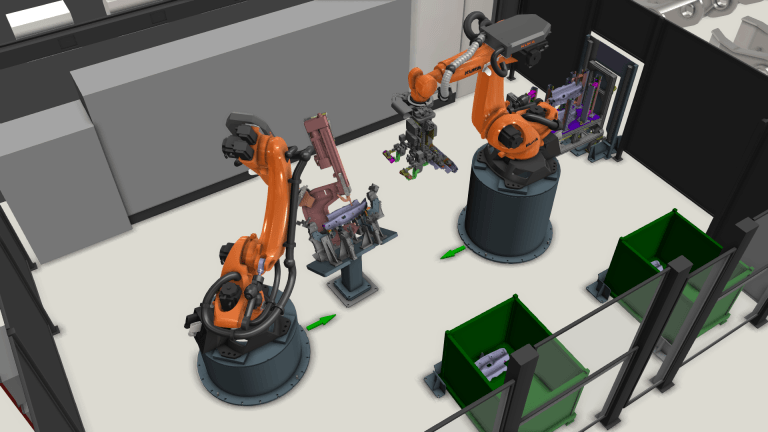
Wie Roboter-Offline-Programmierung die Effizienz in Produktionslinien mit hoher Variantenvielfalt & niedrigen Stückzahlen steigert
Häufige Produktionsumstellungen und kleine Stückzahlen können die Produktion verlangsamen, aber es muss nicht so sein. Mit der Roboter-Offline-Programmierung (OLP) können Hersteller mit hoher Variantenvielfalt und geringen Stückzahlen (High-Mix, Low-Volume) Roboter...
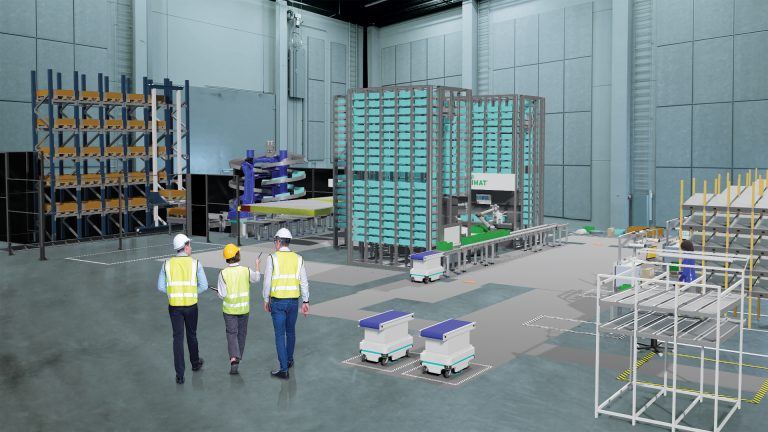
Die Zukunft der automatisierten Fertigung (und warum Menschen weiterhin wichtig sind)
Die Automatisierung in der Fertigung entwickelt sich seit Jahrzehnten weiter, aber ihr eigentlicher Einfluss liegt nicht darin, Menschen zu ersetzen, sondern sie leistungsfähiger zu machen. Wir haben mit Mika Anttila,...