Eine Einführung in die virtuelle Inbetriebnahme
Die virtuelle Inbetriebnahme verändert die Fertigungslandschaft durch den Einsatz von Computersimulationen zum Testen und Optimieren von Produktionssystemen, bevor diese physisch gebaut werden. Dieser Ansatz vereinfacht nicht nur den Einrichtungsprozess und senkt die Kosten, sondern steigert auch die Effizienz, erhöht die Qualifikation der Mitarbeiter und verbessert die Produktionsleistung. Im Folgenden erfahren Sie, was die virtuelle Inbetriebnahme beinhaltet und wie Sie diese Technologie nutzen können, um Ihre Produktionsabläufe zu verbessern.
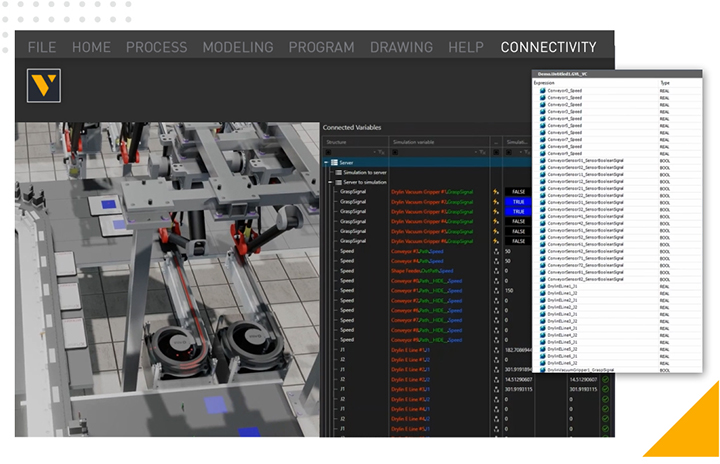
Die virtuelle Inbetriebnahme hilft den Herstellern nicht nur, den im Projektplan festgelegten Termin für die Werksabnahme (Factory Acceptance Test – FAT) einzuhalten, sondern stellt auch sicher, dass sie die FAT bestehen, und ermöglicht in einigen Fällen sogar die virtuelle FAT. Wenn der FAT-Termin nicht eingehalten wird, führt das oft zu kostspieligen Verzögerungen und Schuldzuweisungen. Das ist eine Situation, die alle Projektbeteiligten vermeiden wollen und die häufig längere Arbeitszeiten und Leistungsabstriche erforderlich macht.
Die Analyse der Verzögerungen bei diesen Projekten zeigt immer wieder, dass die Inbetriebnahme der Hauptgrund dafür ist. Das Problem ist, dass es in der Vergangenheit unmöglich war, die Steuerungssoftware zu testen und zu debuggen, bevor die Hardware physisch fertiggestellt war.
Moderne Fertigungssimulationstools liefern die Antwort. Hier erklären wir, was eine virtuelle Inbetriebnahme ist, wie man sie erfolgreich durchführt und welche Vorteile sie bietet. In diesem Artikel gehen wir auf die folgenden Punkte ein
- Software und Inbetriebnahme
- Die Vorteile der virtuellen Inbetriebnahme
- Ein schrittweiser Leitfaden zur virtuellen Inbetriebnahm
- Fallstudien
- Warum die virtuelle Inbetriebnahme die Zukunft ist
Software und Inbetriebnahme
Seit der Einführung der SPS in der Fertigungsumgebung verlassen sich Fertigungsmaschinen und automatisierte Anlagen auf sie. Die SPS liest Daten z. B. von Sensoren und löst Ausgänge aus, die z. B. mit einem Stellantrieb oder sogar einer Robotersteuerung verbunden werden können. Indem sie die Eingänge liest und die Ausgänge auslöst, führt die SPS die Maschine durch den gewünschten Arbeitsablauf.
Um das SPS-Programm vollständig zu testen, war schon immer eine Maschine erforderlich, auf der es laufen konnte. Erst nachdem ein Maschinenprototyp gebaut oder die echte Maschine physisch fertiggestellt wurde, kann der Prozess der Inbetriebnahme der Maschine beginnen. Wie immer bei Software gibt es Bugs, Fehler und Auslassungen sowie Zeitprobleme, die alle behoben werden müssen. Das braucht Zeit und ist im Projektplan nur schwer abzuschätzen. Es ist fast unvermeidlich, dass unerwartete Probleme auftreten und der Projektfortschritt ins Stocken gerät.
Die virtuelle Inbetriebnahme ordnet diese Reihenfolge neu und reduziert so die Auswirkungen der Inbetriebnahme auf den kritischen Pfad des Projekts. In diesem Abschnitt erklären wir, was virtuelle Inbetriebnahme ist. Dann erklären wir, wie sie mit der traditionellen Inbetriebnahme und dem Industrie 4.0-Konzept des digitalen Zwillings zusammenhängt.
Was ist virtuelle Inbetriebnahme?
In einem Lehrbuch wird es beschrieben als “das Einrichten, Testen und Validieren des Designs und des Betriebs eines Systems in einer virtuellen Umgebung auf einem Computer”. Eine praktischere Erklärung ist, dass es sich um den Einsatz von Software handelt, um die Steuerungssoftware zu testen und zu validieren, bevor die physische Maschine gebaut wird.
Damit soll sichergestellt werden, dass Software und Hardware richtig eingestellt sind und wie vorgesehen funktionieren, wenn sie in der realen Welt eingesetzt werden. Dadurch, dass die Inbetriebnahme vor dem Bau der Maschine erfolgt, wird der Großteil der Inbetriebnahmearbeiten aus dem kritischen Projektpfad entfernt, da sie parallel zum Bau oder sogar noch früher im Projekt stattfinden kann.
Die meisten Anbieter von Automatisierungslösungen haben immer noch eine Inbetriebnahmephase, um den Betrieb der Maschine zu testen. Ein großer Teil des Risikos und der Ungewissheit wird jedoch dadurch beseitigt, dass Softwareprobleme früher erkannt und behoben werden.
Erstellen der Maschine in Software
Eine statische Darstellung der Maschine wird mit 3D-CAD erstellt. Damit die Maschine jedoch so funktioniert, wie sie tatsächlich funktionieren wird, braucht sie zusätzlich eine Kinematik – die Bewegungen, die sie ausführen wird – und ein Steuerungssystem – die Eingänge, Ausgänge und das Timing oder die Abläufe.
Roboter stellen eine besondere Herausforderung für die kinematische Modellierung dar, da sie in der Regel fünf bis sieben Achsen haben und sich ohne die Einschränkungen von Führungen und Schienen durch den Raum bewegen können. Es gibt Software zur Robotersimulation, die bei diesen Herausforderungen hilft.
Virtuelle Maschine oder digitaler Zwilling?
Diejenigen, die mit digitalen Zwillingen vertraut sind, werden feststellen, dass dies wie die Beschreibung einer solchen virtuellen Maschine klingt. Es gibt jedoch einige wichtige Unterschiede:
- Die Maschine wurde nicht physisch gebaut, also gibt es nichts, was ein digitaler Zwilling sein könnte: Das virtuelle Modell steht allein
- Ein digitaler Zwilling hat Datenverbindungen zu dem physischen System, das er modelliert oder repräsentiert, so dass Werte aus der realen Welt in das virtuelle System einfließen können
- Das Ziel der virtuellen Inbetriebnahme auf einer virtuellen Maschine ist es, Fehler und Probleme zu finden, bevor die Maschine gebaut wird, während das Ziel eines digitalen Zwillings darin besteht, das physische System für Tests und die Bewertung von Szenarien zu replizieren.
Sobald die Maschine existiert und in Betrieb genommen wurde, ist es möglich, das virtuelle Inbetriebnahme-Layout in einen digitalen Zwilling umzuwandeln oder das digitale Modell als das Original und die physische Maschine als Zwilling oder Nachbildung des virtuellen Layouts zu betrachten. Dies würde die Rendite der investierten Zeit und Mühe erhöhen, da virtuelle Experimente und Tests noch besser möglich wären. Der digitale Zwilling könnte genutzt werden, um alternative Wege zur Einplanung eines Produkts zu testen oder verschiedene Verpackungsgrößen in einem System zu erproben. In unserem Blogbeitrag “Digitale Zwillinge und virtuelle Inbetriebnahme” findest du weitere Informationen.
Die Vorteile der virtuellen Inbetriebnahme
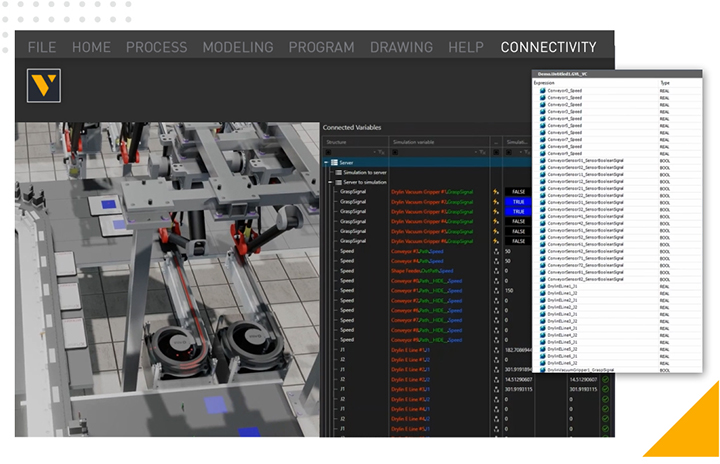
Wir haben bereits über die Gründe für eine virtuelle Inbetriebnahme gesprochen. Jetzt gehen wir näher auf die Vorteile für Maschinenbauer und Anbieter von Automatisierungslösungen ein. Dazu gehören:
- Früherkennung
- Verkürzte Vorlaufzeit
- Kosteneinsparungen
- Flexibilität bei der Gestaltung und Umsetzung
- Ausbildung
- Verbesserte Sicherheit
Früherkennung
Ein Sensor in der Maschine erkennt z.B. das Vorhandensein eines Teils mit einem True-Signal. Solange dies nicht der Fall ist, beginnt die Maschine nicht mit ihrem Zyklus. Die SPS könnte jedoch das Signal des Sensors beim Wechsel von Wahr->Falsch->Wahr verpassen, wenn der Abstand zwischen den Teilen zu gering ist. Die Maschine bleibt dann in einem “Wartezustand”, da sie das alte Teil beim Verlassen und das neue Teil beim Eintreten verpasst hat.
Ein Problem wie dieses wird bei der herkömmlichen Inbetriebnahme gefunden und behoben. Multipliziert man jedoch die Anzahl der Sensoren, Aktoren und Codezeilen, wird klar, dass es sehr viel Zeit in Anspruch nehmen kann, bis die Maschine voll einsatzfähig ist.
Die virtuelle Inbetriebnahme findet auch diese Art von Problem, aber die Zeit, die für die Änderung von Codezeilen benötigt wird, verzögert das Projekt nicht: Der Bau kann fortgesetzt werden, während der Programmierer eine Lösung findet und implementiert. Außerdem kann durch den Wegfall des Zeitdrucks eine bessere Lösung gefunden werden, die die Zykluszeit nicht verlängert.
Dieses einfache Beispiel verdeutlicht den Punkt: Die virtuelle Inbetriebnahme deckt Probleme früher auf, als es sonst der Fall wäre.
Ein komplexeres Beispiel ist ein Projekt, bei dem Roboter in einer Produktionslinie installiert werden. Eine kleine Fehlkalkulation bei der Platzierung des Roboters könnte dazu führen, dass seine Reichweite für die zugewiesene Aufgabe nicht ausreicht. Auch eine Änderung der Greiferkonstruktion könnte sich auf die Reichweite des Roboters auswirken, indem sie zum Beispiel in eine Richtung vergrößert, in eine andere aber verkleinert wird. In diesem Fall würde die Lösung des Problems umfangreiche Nacharbeiten und vielleicht einen neuen Roboter erfordern, was das Projekt verzögert und die Kosten erhöht. Die virtuelle Inbetriebnahme würde es jedoch ermöglichen, das Problem zu erkennen, bevor der Roboter überhaupt an der falschen Stelle installiert wurde.
Verkürzte Vorlaufzeit
Die Inbetriebnahme kann 25% der gesamten Projektdauer ausmachen. Die Vorlaufzeit kann verkürzt werden, indem ein Teil davon parallel zum Bau oder sogar früher durchgeführt wird, wenn die mechanische Konstruktion nur virtuell vorliegt. Außerdem wird durch die frühzeitige Erkennung und Lösung von Problemen die Ungewissheit der Projektvorlaufzeit erheblich reduziert, so dass die Bauherren die Fertigstellung genauer vorhersagen können.
Ein zusätzlicher Vorteil für den Bauunternehmer ist, dass die Ausrüstung vor der FAT und dem Versand weniger Zeit auf dem Boden verbringt. Das erhöht die Kapazität, was, wenn es genutzt wird, deutlich höhere Gewinne bedeuten kann.
Kosteneinsparungen
Die Behebung von Problemen mit montierten Beschlägen ist immer teuer. Möglicherweise werden neue Teile benötigt und es werden Überstunden für deren Einbau gemacht. Wenn diese Probleme bereits in der Planungsphase angegangen werden, können erhebliche Kostenüberschreitungen vermieden werden. (Dadurch wird auch die Genauigkeit der Budgetierung verbessert, da weniger Mittel für “Unvorhergesehenes” aufgewendet werden müssen).
Flexibilität bei der Gestaltung und Umsetzung
Die virtuelle Inbetriebnahme erhöht die Chancen für Innovationen in der Produktion. So wird das möglich.
Bei der traditionellen Inbetriebnahme sieht das Team oft Möglichkeiten, wie die Konstruktion verbessert werden kann. Das kann die Verkürzung der Zykluszeit durch veränderte Greifabläufe sein, die Verlagerung von Komponenten, um die Aufstellfläche der Maschine zu verkleinern, oder ein besserer Zugang für die Einrichtung und Wartung. Da die Maschine jedoch bereits gebaut ist, wären solche Änderungen kostspielig und würden zu Verzögerungen führen.
Bei der virtuellen Inbetriebnahme ist die Auswirkung auf das Projekt viel geringer, wenn neue Ideen in den Entwurf aufgenommen werden. Sie werden wahrscheinlich zu einer verbesserten Leistung und/oder Wartungsfreundlichkeit führen und könnten sogar Kosteneinsparungen mit sich bringen.
Ausbildung
Um den ROI eines Investitionsprojekts zu maximieren, muss die Maschine oder Anlage so schnell wie möglich im Betrieb eingesetzt werden. Ein wichtiger Schritt, um dies zu erreichen, ist die Schulung der Ingenieure, des Wartungsteams und der Bediener, wie sie die Maschine oder das System nutzen und warten können.
Im traditionellen Verfahren findet diese Schulung statt, nachdem die Maschine in Betrieb genommen worden ist. (Normalerweise findet sie nach dem FAT statt.) Bei der virtuellen Inbetriebnahme kann die Schulung am digitalen Modell der Hardware beginnen. Eine praktische Schulung an der physischen Maschine ist zwar immer noch wünschenswert, aber wenn die Beteiligten mit den logischen Abläufen, den Positionen der Stellglieder, den Beschickungs- und Entladesystemen usw. vertraut sind, haben sie bereits einen großen Lernfortschritt erzielt.
Später, wenn das digitale Modell in einen digitalen Zwilling umgewandelt wurde, kann es für die Entwicklung von Fähigkeiten und das Onboarding neuer Mitarbeiter genutzt werden.
Verbesserte Sicherheit
Sich bewegende Geräte, insbesondere Roboter, können sehr gefährlich sein. Im Normalbetrieb sind die Beschäftigten durch Schutzvorrichtungen und Verriegelungen geschützt, aber bei der Inbetriebnahme müssen diese oft geöffnet und außer Kraft gesetzt werden, um Sicht und Zugang zu gewährleisten.
Indem wir die Bewegungspfade testen und die Abläufe, das Timing und die Behandlung von Ausnahmen virtuell überprüfen, müssen wir unter diesen Bedingungen weniger laufen und die Risiken werden reduziert.
Ein schrittweiser Leitfaden zur virtuellen Inbetriebnahm
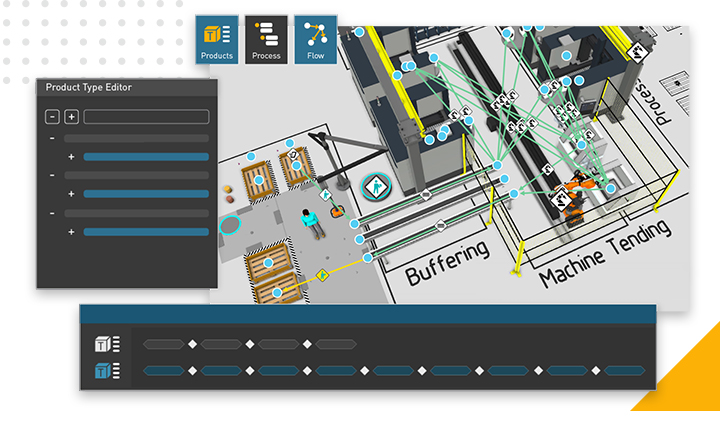
Nachdem wir uns mit der virtuellen Inbetriebnahme vertraut gemacht haben, schlagen wir vor, zehn Schritte zu durchlaufen.
- Verstehen, warum ein genaues Modell benötigt wird – Das Team muss verstehen, warum die Modellgenauigkeit so wichtig ist, und sich verpflichten, die erforderlichen Informationen zu liefern. Fehler oder Unstimmigkeiten werden dazu führen, dass die virtuelle Inbetriebnahme weniger nützliche Informationen liefert. In einer solchen Situation könnten alle Schlussfolgerungen nicht anwendbar oder irreführend sein, wenn sie auf die reale Welt übertragen werden.
- Systemanalyse und -definition – Beginne damit, dir ein klares Bild über die Ziele und Funktionen des Produktionssystems zu machen. Dann alle verfügbaren technischen Unterlagen, Spezifikationen und Anforderungen an die Maschinen und Steuerungssysteme.
- Modellbau – Erstelle ein genaues 3D-Modell des Produktionssystems mit einer Kombination aus CAD-Daten und Modellen aus dem Visual Components e-Catalog. (In unserem Visual Components e-Catalog sind mehr als 3.000 Komponenten verfügbar.) Integriere dann kinematische, elektrische und andere relevante Daten, um eine detaillierte digitale Darstellung der geplanten Maschine oder Anlage zu erstellen.
- Integration der Steuerlogik – Verbinde die SPS und die Robotersteuerung mit dem digitalen Modell. Dies ermöglicht das virtuelle Testen von Steuerungssequenzen, Reaktionen und dem gesamten Systemverhalten. (In Visual Components bieten wir Konnektivität zu den gängigsten Robotermarken und SPS-Systemen, wie KUKA, DOOSAN Robotics, ABB, Fanuc, OPC UA, Beckhoff, Siemens SIMIT und Siemens S7).
- Simulieren und teste – Lasse das Modell in verschiedenen Betriebsszenarien durchlaufen, um seine Leistung zu testen und, wenn möglich, mit realen Daten zu validieren. Dabei sollten sowohl der reguläre Betrieb als auch Ausnahme- oder Fehlersituationen getestet werden, um sicherzustellen, dass das System mit unerwarteten Problemen umgehen kann.
- Verfeinerung – Nutze die Ergebnisse der Simulationsläufe, um Unstimmigkeiten oder Ineffizienzen in der Steuerungslogik zu erkennen und zu beheben. Führe dann die Tests erneut durch, um zu überprüfen, ob das Modell genauer ist. Wiederhole den Vorgang, bis das virtuelle Modell die gewünschte Leistung erbringt.
- Sicherheits- und Konformitätsprüfungen – Stelle sicher, dass die Steuerungslogik und das Systemdesign wie erforderlich funktionieren und die relevanten Industrienormen und Sicherheitsvorschriften erfüllen. (Die Sicherheit von Robotern ist ein Bereich, der besonders viel Aufmerksamkeit erfordert). Diese Kontrollen und Tests sind besonders wichtig in Branchen mit strengen Sicherheits- und Compliance-Anforderungen.
- Physische Inbetriebnahme – Auch wenn die virtuelle Inbetriebnahme diesen Schritt drastisch verkürzt, ist er dennoch notwendig. Die Aufgaben hier sind: Übertrage die getestete und verifizierte Steuerungslogik vom Modell auf das reale System; Überwache das System bei der Inbetriebnahme genau, um sicherzustellen, dass es sich wie erwartet verhält.
- Kontinuierliche Verbesserung – Nachdem das physische System eine Weile gelaufen ist, sammelst du Rückmeldungen und Betriebsdaten. Vergleiche diese mit den Vorhersagen aus der virtuellen Inbetriebnahme und führe eine Überprüfung nach der Implementierung durch, um eventuelle Lücken oder verbesserungswürdige Bereiche zu identifizieren. Nutze die gewonnenen Erkenntnisse, um das Modell/den digitalen Zwilling und die Steuerungslogik weiter zu verfeinern.
- Dokumentation– Dokumentiere jeden Schritt der virtuellen Inbetriebnahme, vom ersten Entwurf bis zur endgültigen Implementierung. Das hilft bei der Fehlersuche, bei zukünftigen System-Upgrades oder bei der Skalierung.
Fallstudien
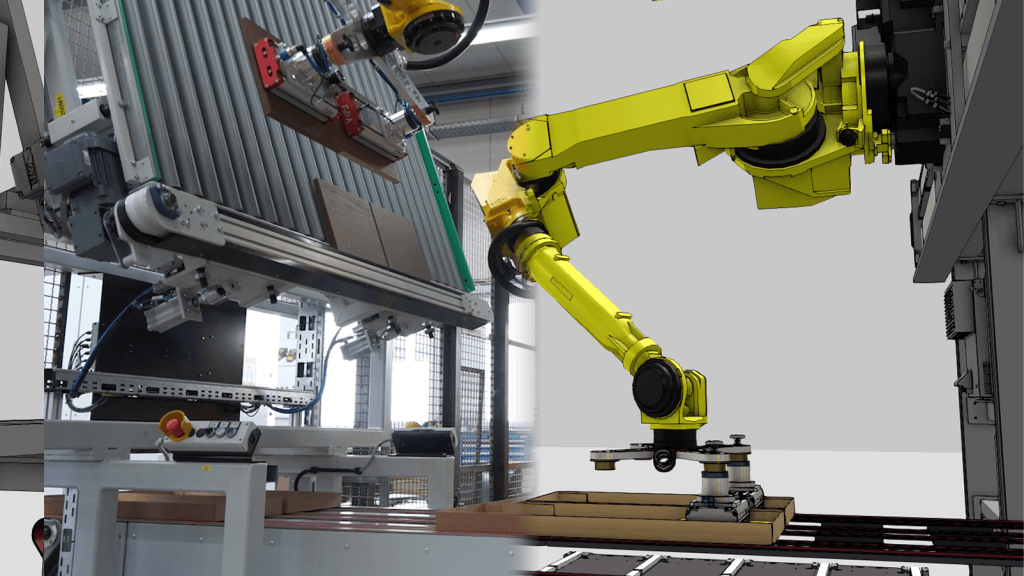
Wenn du mehr darüber erfahren möchtest, findest du hier vier Beispiele aus der Praxis von Unternehmen, die die virtuelle Inbetriebnahme mit Visual Components erfolgreich umgesetzt haben.
- Einsatz von Simulationen zur Ermittlung von Automatisierungsmöglichkeiten bei der Herstellung von Drive-Thru-Fenstern
- Erstellung eines genauen digitalen Modells einer Fabrik
- Bau eines digitalen Modells einer automatisierten Zelle
- Verpackungsvorgänge simulieren
Warum die virtuelle Inbetriebnahme die Zukunft ist
In der Produktion ist ein digitaler Wandel im Gange, und das betrifft auch die Art und Weise, wie Maschinen und Anlagen entwickelt und eingesetzt werden. Sensoren, Steuerungen und Software sind ein wesentlicher Bestandteil dieses Industrie 4.0-Fortschritts und werden die Maschinen der Zukunft schneller, genauer, wiederholbarer und vielseitiger machen.
Da diese Funktionen der nächsten Generation den Herstellern die Möglichkeit bieten, Verschwendung zu reduzieren und ihre Gewinnspannen zu erhöhen, wird der Druck auf eine schnellere Umsetzung nur wachsen. Die virtuelle Inbetriebnahme ist daher ein Schlüsselelement, um der Konkurrenz einen Schritt voraus zu sein und den ROI der Investitionen zu maximieren.
Wenn du bereits digitale Zwillinge erstellst, diese Arbeit aber nicht für die virtuelle Inbetriebnahme verwendest, ist es vielleicht an der Zeit, umzudenken. Wenn du immer noch auf der Baustelle in Betrieb nimmst und die FAT-Fristen nicht einhältst, ist es definitiv an der Zeit, dein Vorgehen zu überdenken.
In beiden Fällen hat Visual Components die Werkzeuge und das Know-how, das du brauchst. In unserem Lernpfad “Visual Components für die virtuelle Inbetriebnahme nutzen” findest du ausführliche Informationen, oder kontaktiere uns, um mehr zu erfahren
Zum Weiterlesen
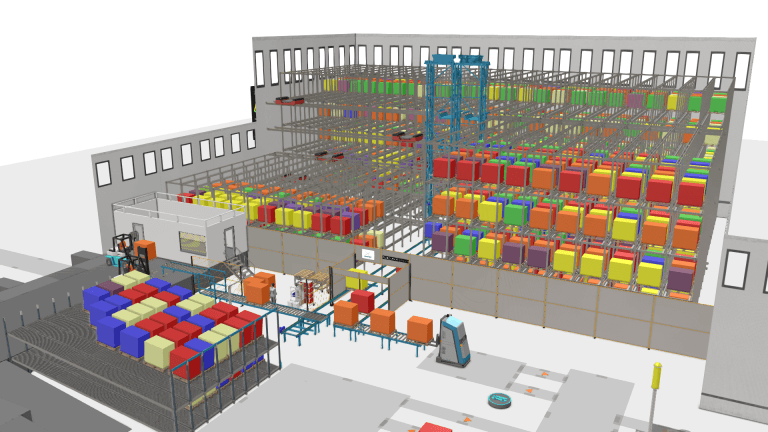
Effiziente Lagerplanung: Wie Simulationen helfen, Lagerprozesse zu optimieren
Wie können Unternehmen Lagerhäuser so gestalten, dass sie vom ersten Tag an effizient arbeiten und gleichzeitig die Arbeitskosten und andere Ausgaben im Zaum halten? Der Schlüssel liegt in einer intelligenten...
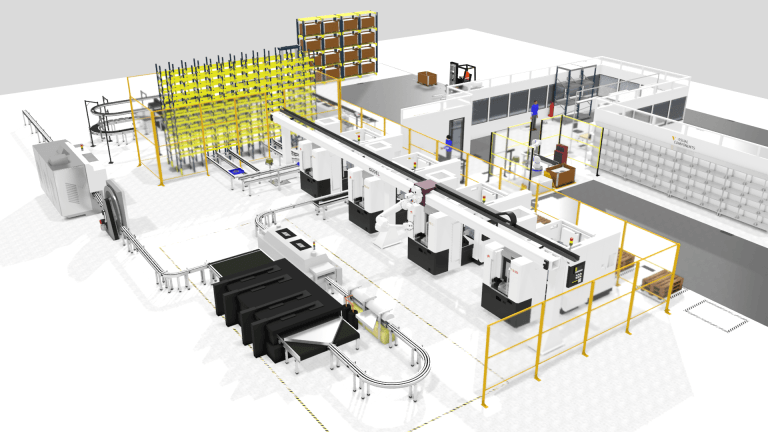
Umfassender Leitfaden zu Eingabedaten für die 3D-Fertigungssimulation
Wenn Sie neu in der 3D-Fertigungssimulation sind, sind Sie hier genau richtig. Dieser umfassende Leitfaden hilft Ihnen, die wesentlichen Eingabedaten zu verstehen, die für die Erstellung effektiver Simulationsmodelle erforderlich sind....
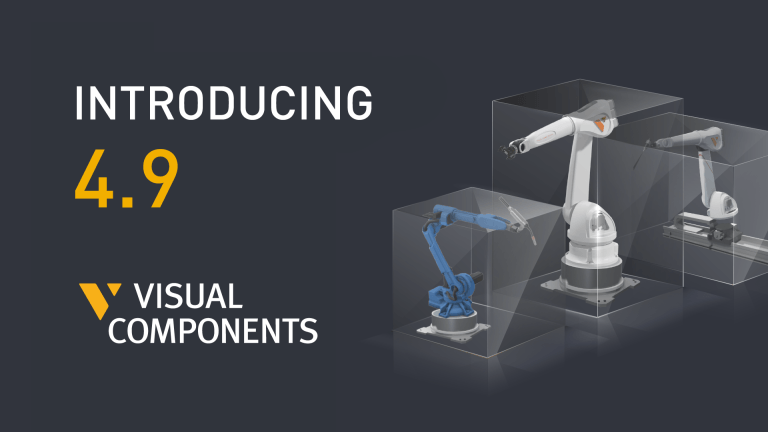
Visual Components 4.9: Gestalten mit Klarheit
Visual Components 4.9 bringt mehr Klarheit in die Produktionsplanung und -optimierung in der Fertigung. Mit mehr Klarheit können unsere Anwender mehr erreichen, einfacher und mit größerem Verständnis, besonders wenn sie...