Wärtsilä Case Study
Find out how Wärtsilä uses Visual Components to support the complete lifecycle of new investment projects.
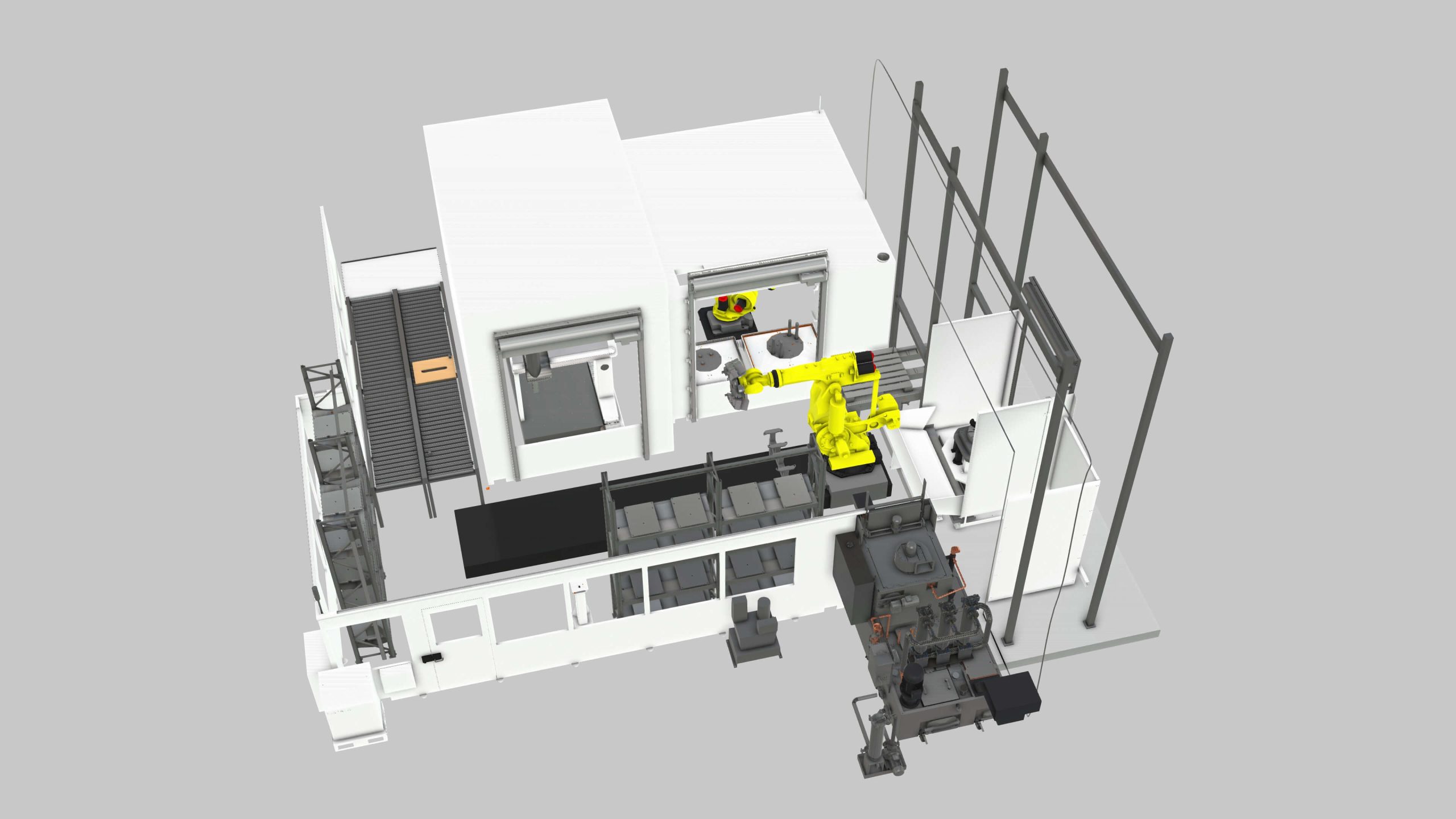
In search of an easy to use 3D simulation solution
Wärtsilä, a global leader in advanced technologies and complete lifecycle solutions for the marine and energy markets, was first introduced to Visual Components in 2008. Tero Kujamäki, Project Manager for Marine Solutions at Wärtsilä’s Delivery Centre Development (DCD), was working with the Seinäjoki University of Applied Science to create 3D simulations of an automated cylinder head assembly line with Visual Components software.
“We were planning a new cylinder head assembly line and wanted to create a simulation model of the process,” said Tero. “We used Visual Components to create a simulation video of the automated line and validate our calculations for capacity and phase time.”
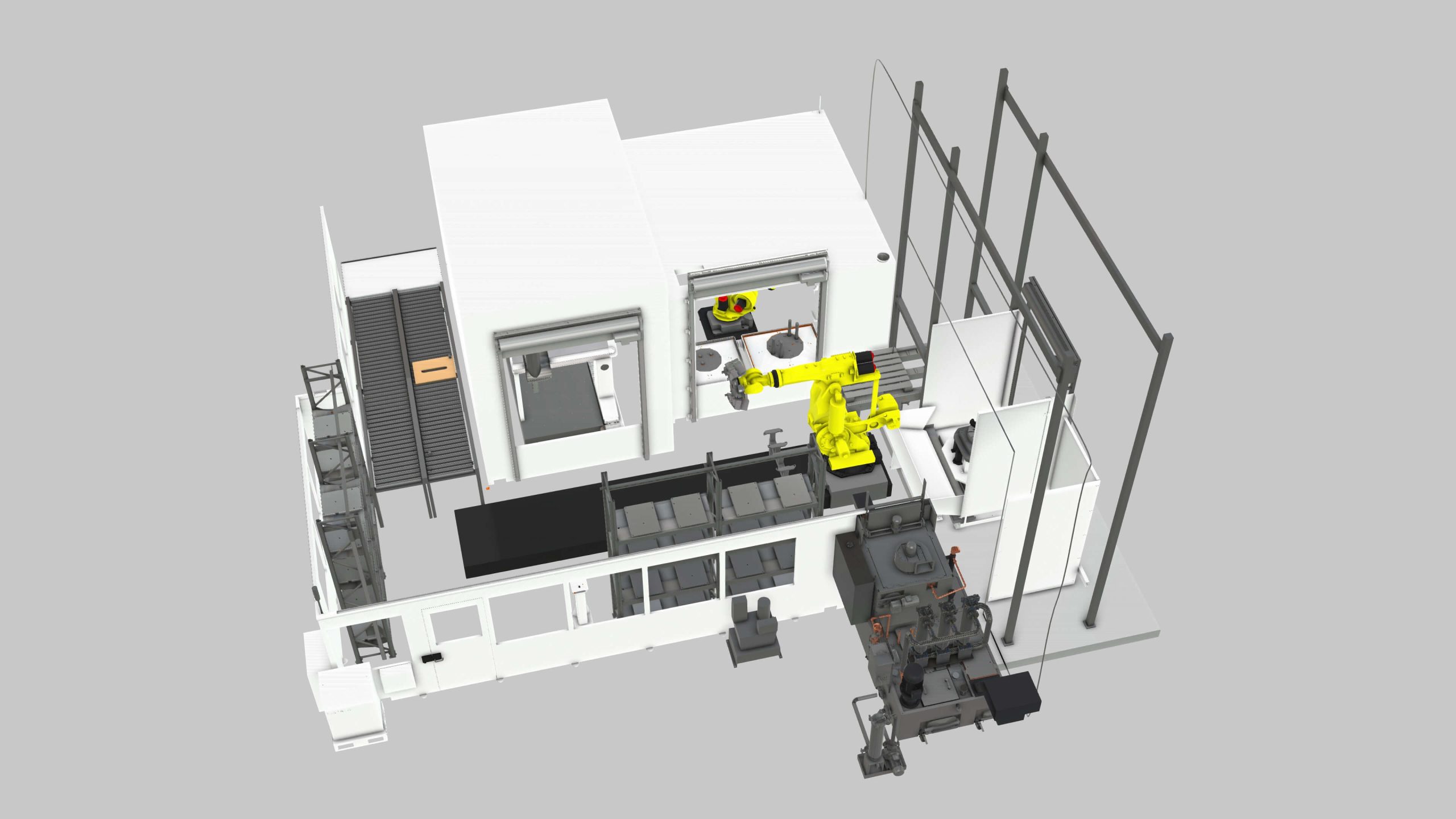
As the strategic planning arm of Wärtsilä’s Delivery Centre Vaasa (DCV), the DCD is responsible for planning DCV production development activities over 5-10 year periods. They investigate new production technologies and plan major investments in new production centers.
Tero and his team had previously evaluated other manufacturing simulation software solutions, but found them too complex and resource intensive. For an organization that’s constantly exploring new production solutions, they needed a solution that could keep up with their fast pace; a tool that could quickly create and simulate production concepts, but also be used for more in-depth analysis.
“We were not just looking for a powerful tool to simulate robot activities,” said Tero, “But something that could simulate the entire production chain.”
“For this, Visual Components was the best tool.”
The experience with Seinäjoki University left Tero and his team convinced that Visual Components fit their needs. The simulation videos and layouts they created of the assembly line were very impactful (the investment recommendation was approved), and Wärtsilä began using Visual Components shortly after.
We were not just looking for a powerful tool to simulate robot activities, but something that could simulate the entire production chain. For this, Visual Components was the best tool.
Tero Kujamäki, Project Manager for Marine Solutions – Wärtsilä’s Delivery Centre Development
Optimizing the project lifecycle with 3D manufacturing simulation
The DCD initially used Visual Components to design layouts and simulations of production lines – investment projects being considered by Wärtsilä. As Tero and his team explored the capabilities of Visual Components, they started using it for more applications, including robot cell simulation, design analysis, and creating training materials.
Wärtsilä now uses Visual Components to support the complete lifecycle of new investment projects, from ideation and concept design to technical validation and implementation. The main benefits that Tero and his team have seen with Visual Components are improvements in production performance, communications, and implementation.
“As a project manager, about 90% of my job is communication,” said Tero. “That’s why Visual Components is the perfect tool for us. We can easily and concretely show the effects of design changes to the overall process, and share that information with both technical and non-technical people.”
As a project manager, about 90% of my job is communication. That’s why Visual Components is the perfect tool for us. We can easily and concretely show the effects of design changes to the overall process, and share that information with both technical and non-technical people.
Tero Kujamäki, Project Manager for Marine Solutions – Wärtsilä’s Delivery Centre Development
Achieving bottom line impact
10 years later, Tero and his team have seen positive results since first introducing Visual Components to Wärtsilä, specifically in the areas of production design and project implementation.
The production solutions Wärtsilä builds are highly automated and use advanced equipment and robotics. While the machines on their factory floors are state-of-the-art, prior to using Visual Components, Tero and his team knew their production lines weren’t optimally designed. They were able to squeeze much more performance out of production solutions designed with Visual Components, leading to projects with much more financially attractive returns.
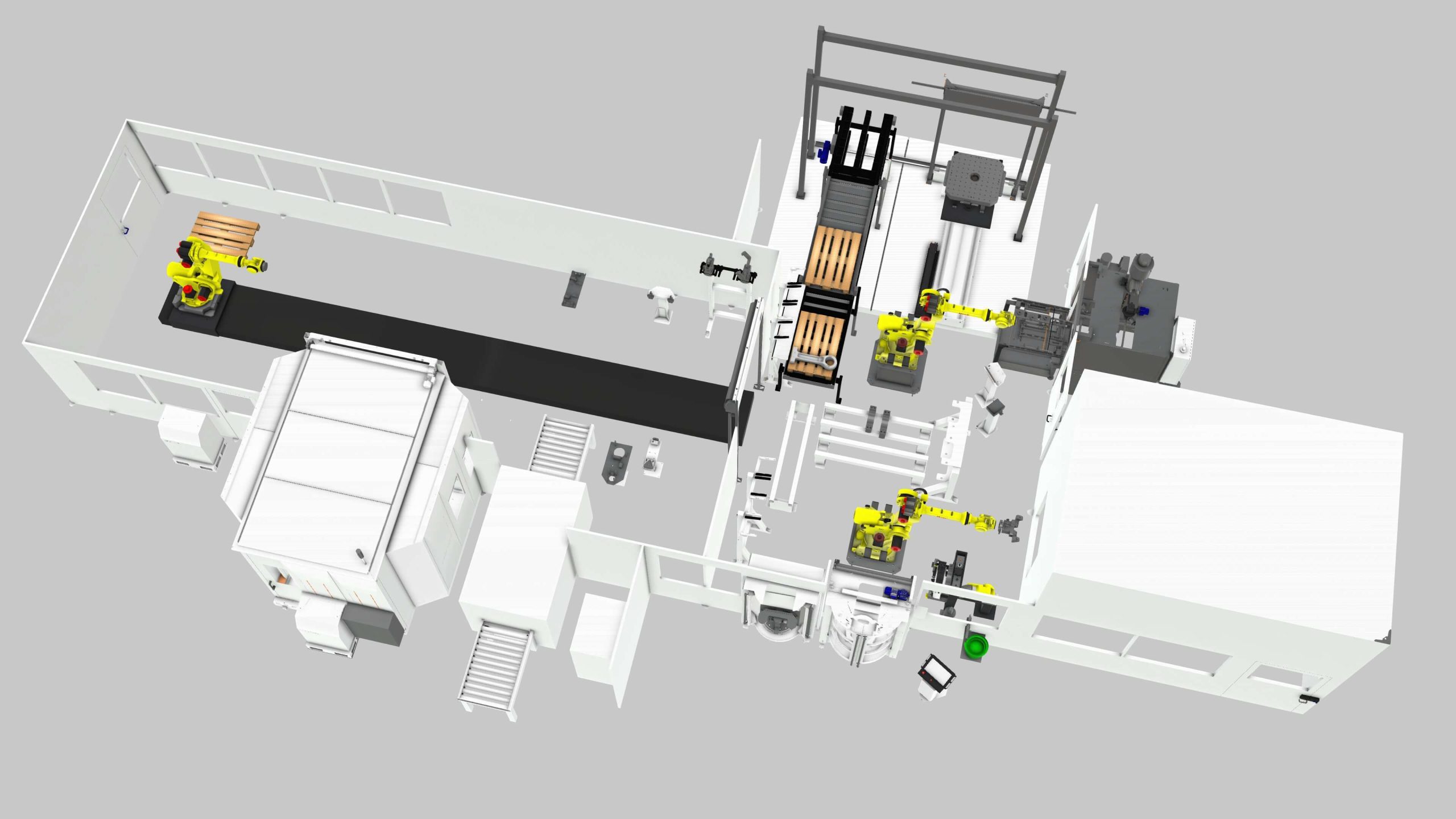
Once a project is approved, there is intense pressure for it to be delivered and commissioned quickly. There are always implementation challenges with projects of this scope and complexity; but with Visual Components, the DCD saw an opportunity to accelerate the ramp-up period of new projects. Tero and his team used Visual Components to plan and coordinate implementation with project stakeholders, using layouts, 3D models, and simulations to communicate project timelines, milestones, and end-states. This resulted in shorter ramp-up periods, faster delivery times, and significant cost savings for Wärtsilä.
“Previously, we used 2D drawings or Excel spreadsheets to map and describe our processes, which wasn’t always easy for us to communicate to others,” said Tero. “We now use 3D models and simulations, which helps stakeholders more quickly understand our technical proposals, and saves us time from having to explain complex calculations.”
“Visual Components is now our standard when planning projects and processes.”
Visual Components is now our standard when planning projects and processes.
Tero Kujamäki, Project Manager for Marine Solutions – Wärtsilä’s Delivery Centre Development
Exploring the digital and virtual frontiers
Wärtsilä continues to work on exciting projects that advance their marine and energy production capabilities. The next big thing: factory digitalization. Tero and his team are exploring how to digitize Wärtsilä’s production operations. The DCD sees significant opportunity in factory digitalization, specifically with the ability to create a digital twin of their factories, to simulate changes and upgrades to production lines before deploying them. Considering the scale and complexity of their factories, Tero expects this would save Wärtsilä significant time and expense in planning and implementation of future projects.
“As production development is one of our key areas at the Vaasa factory, we have to explore new tools and methods that can help us take the next steps in all of our development areas,” said Tero. “Pre-digitalization has been an active development area for us the past 10 years and we understand the benefits for this quite well.”
“We already have a partial environment for factory digitalization that’s working, we now need to achieve integration between existing tools at scale.”
As an early user of Visual Components Virtual Reality (VR), Wärtsilä also sees a lot of potential in VR for their planning projects. In addition to being able to experience new production concepts in full-scale, Tero and his team are excited about how it will enable a much richer training experience, and how it can improve stakeholder engagement and collaboration on future projects.
“We’re excited about how VR will allow us to better support the end-users of our production solutions before they’re commissioned,” said Tero. “We think there’s great potential for training end-users and operators in a VR environment so we can further reduce ramp-up time for new projects.”
We’re excited about how VR will allow us to better support the end-users of our production solutions before they’re commissioned.
Tero Kujamäki, Project Manager for Marine Solutions – Wärtsilä’s Delivery Centre Development
ABOUT Wärtsilä
Wärtsilä is a global leader in advanced technologies and complete lifecycle solutions for the marine and energy markets. By emphasizing sustainable innovation and total efficiency, Wärtsilä maximizes the environmental and economic performance of the vessels and power plants of its customers. In 2016, Wärtsilä’s net sales totaled EUR 4.8 billion with approximately 18,000 employees. The company has operations in over 200 locations in more than 70 countries around the world.
Further reading
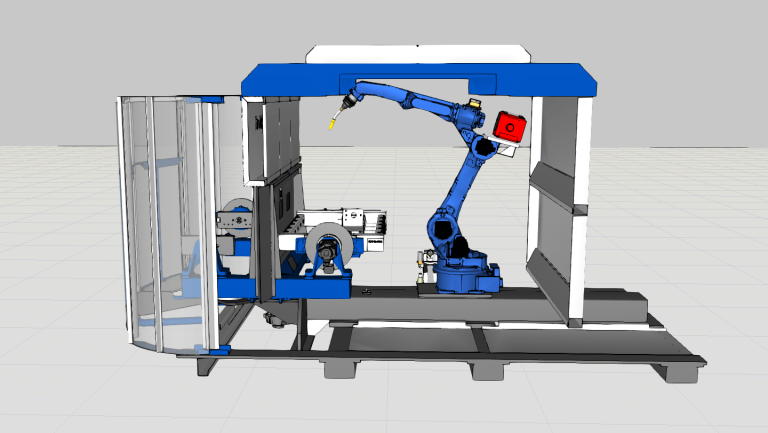
Maximizing efficiency and ROI from day 1: Duun Industrier pre-programs a welding robot cell with Visual Components OLP
Duun Industrier, a leading Norwegian heavy machinery manufacturer, installed the Nordics’ largest robotic welding station in 2013. Utilizing Visual Components for robot programming since 2014, they commissioned a new robot...
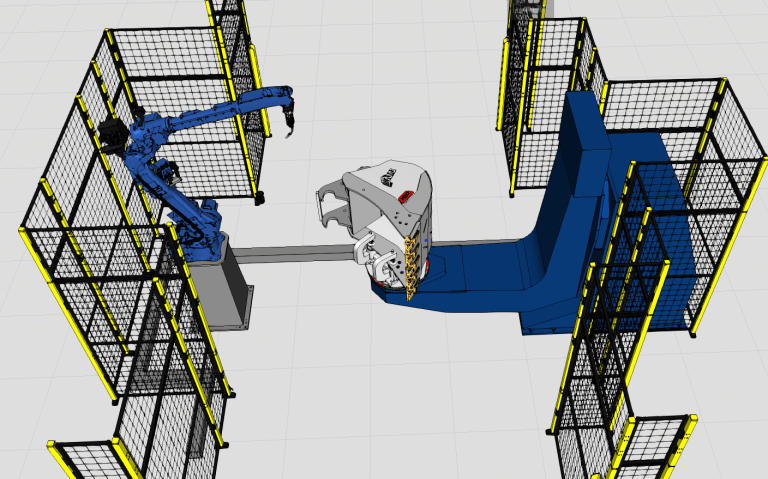
Combatting the welder shortage: how AMI Attachments enhances production efficiency with Visual Components OLP
AMI Attachments, a leading North American manufacturer of heavy equipment attachments, sought to improve product throughput and meet evolving market demands while navigating a welder shortage. By implementing Visual Components...
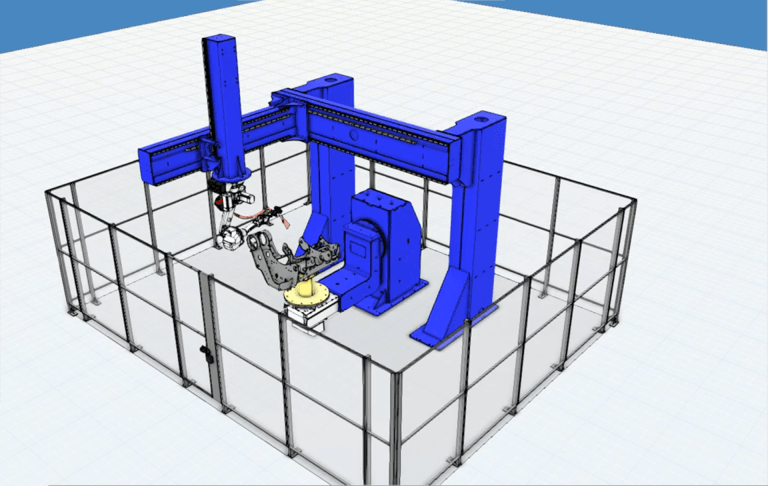
Ponsse is driving forest machine innovation and improving productivity with Visual Components Robotics OLP
Ponsse Plc., a global leader in forest machine manufacturing, has transformed its production process by leveraging Visual Components Robotics OLP.