Virtual Manufacturing Project Case Study: Driving Sales with 3D Simulation
In this case study, we’ll review a project they recently completed to drive sales of their lean manufacturing products, using the Visual Components Experience app.
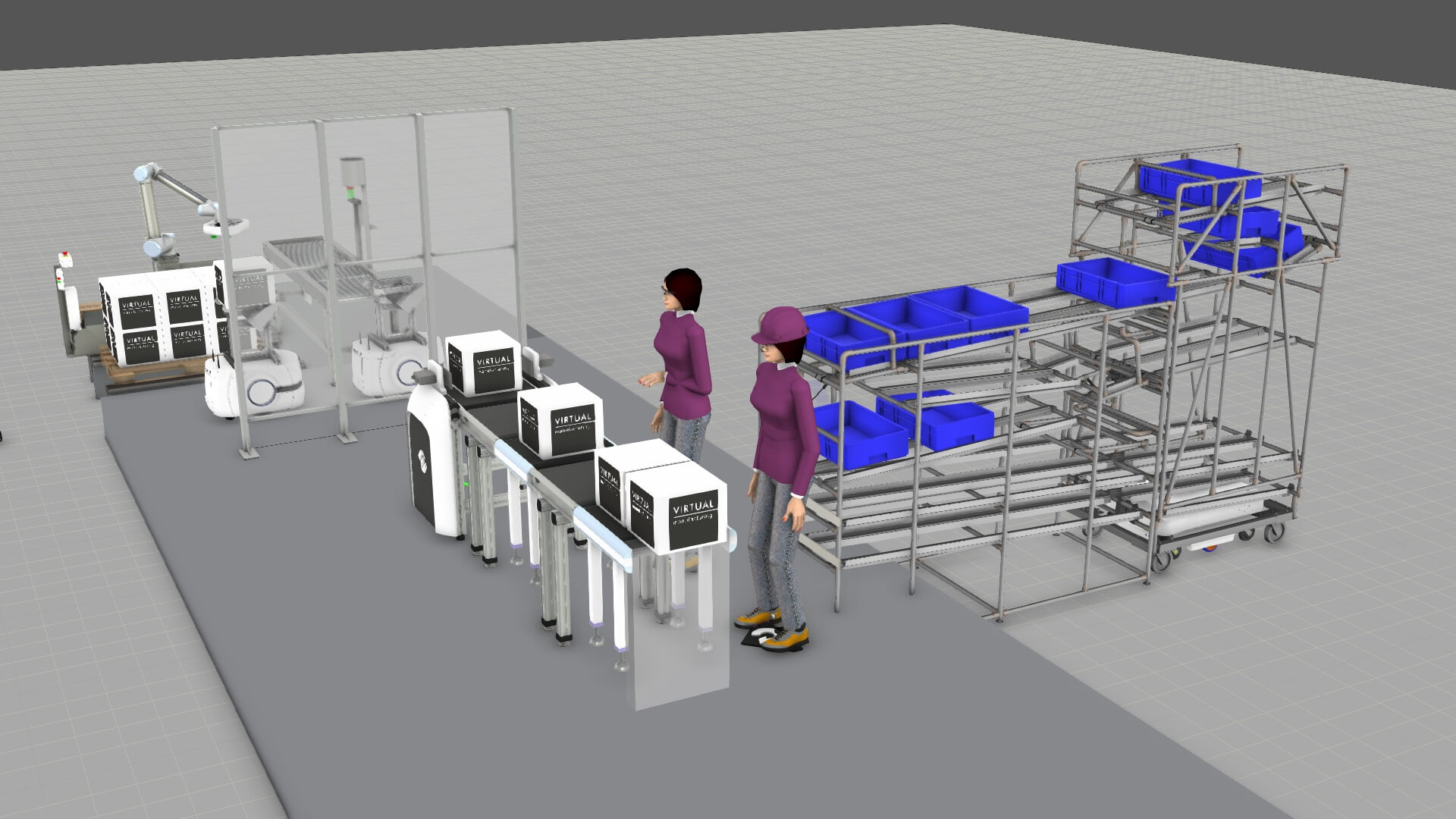
Virtual Manufacturing, a supplier of lean-based production development services, and value-added reseller of Visual Components solutions; understands the power of simulation in production.
In this case study, we’ll review a project they recently completed to drive sales of their lean manufacturing products, using the Visual Components Experience app.
About Virtual Manufacturing
“Our goal is to improve the customer’s production system,” explained William Falkenström, a consultant with the Assembly and Production Flow team at Virtual Manufacturing. “This can range from corporate cultural transformation to robotic simulation and programming.
The Swedish-based company employs about 70 workers and consists of four divisions: Industrial Management, Assembly & Production Flow, Robotics & Automation, and Lean Manufacturing Products (LMP).
Virtual Manufacturing uses simulation frequently in client engagements. Whether the project is to design a new robot cell or optimize a business process, 3D manufacturing simulation software plays an essential part in their consulting toolkit.
“We believe that in order to bring value in production, we need to be working in a 3D environment to increase understanding and communicate concepts,” said William.
Virtual Manufacturing doesn’t just use this technology for client engagements; they also use it to market their own solutions. William was recently involved in a project to improve communication and sales of shooter wagons, a product distributed by the LMP division. LMP, which manufactures and sells customer specific solutions for lean production systems, wanted the ability to present a 3D simulation of their shooter wagons from their mobile devices.
We believe that in order to bring value in production, we need to be working in a 3D environment to increase understanding and communicate concepts.
William Falkenström, Consultant with the Assembly and Production Flow team at Virtual Manufacturing
About the Project
William and his team were asked to create a simulation that demonstrated the functions and benefits of shooter wagons. It needed to be easy to understand and help their users – the LMP sales team – to communicate the benefits of this material handling solution to prospective customers.
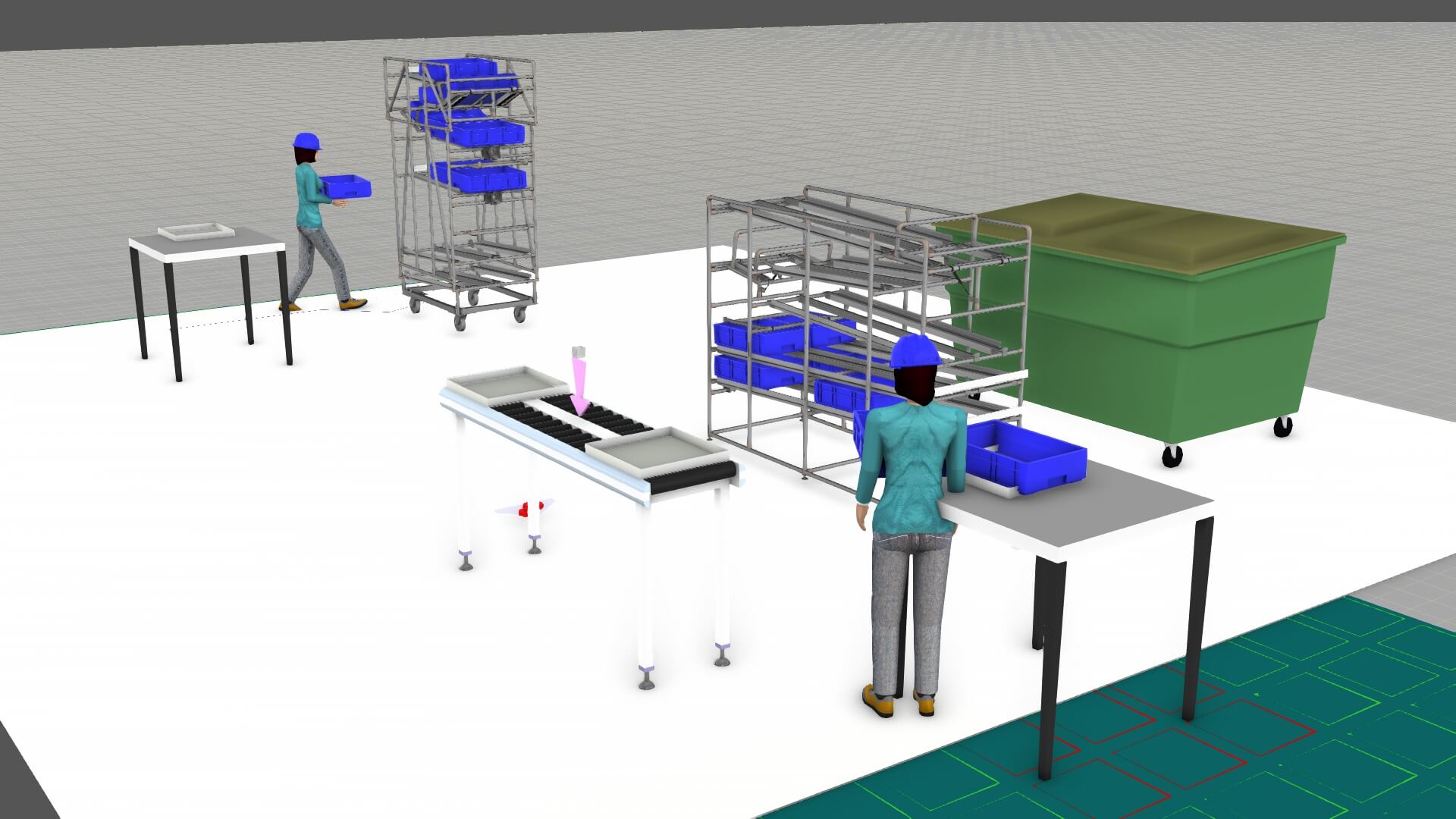
Visual Components had just released Visual Components Experience, a mobile app that allows users to play, navigate, and explore simulations from their Android and iOS enabled devices. After an evaluation of the Visual Components Experience app, William and his team decided it met the needs of their users, and proceeded to create a demonstrator.
“Visual Components Experience makes it so much more fun and informative to show potential customers a 3D animation of the product, and how it moves and functions without building a real-world prototype,” said William. “It’s easy to create, show, and navigate the 3D animation, and it’s a very convenient alternative if you don’t have your laptop.
“Due to our experience in flow simulation and the capabilities of Visual Components, it was a no-brainer for us to use this software to create this product demonstrator.”
William and his team used Visual Components to create a demonstrator that showed the shooter wagons in a simple material-handling example.
Visual Components Experience makes it so much more fun and informative to show potential customers a 3D animation of the product, and how it moves and functions without building a real-world prototype. It’s easy to create, show, and navigate the 3D animation, and it’s a very convenient alternative if you don’t have your laptop.
William Falkenström, Consultant with the Assembly and Production Flow team at Virtual Manufacturing
About Shooter Wagons
Shooter wagons are a type of gravity-flow rack, combining storage and material handling in one system. They operate via a first-in, first-out racking order, meaning boxes move to the forefront only after the preceding one is removed. Shooter wagons are cost efficient and help companies to maximize space and efficiency while saving time, space, and manpower. They’re ideal for lean manufacturing environments and used in many applications, including material handling, storage, picking, and assembly lines.
Shooter wagons are a viable material handling solution based on several properties they exhibit:
- They’re easy to dock.
- They automatically pass off full boxes and receive empty boxes after docking.
- Compared to manual solutions, shooter wagons load and unload much faster.
- And lastly, these wagons are inexpensive and simple to maintain compared to pneumatic and electric systems.
Shooter wagons are a type of karakuri device, meaning they’re mechanically powered and don’t require electric, pneumatic, or hydraulic power to operate. They use gravity to process boxes.
“Shooter wagons are an ideal solution for any business looking to enhance productivity, improve workplace safety and save money,” explained William. “While they’re a simple and cost-effective solution, they’re not very well understood. This was a driving reason to use simulation, to show how they work.”
Due to our experience in flow simulation and the capabilities of Visual Components, it was a no-brainer for us to use this software to create this product demonstrator.
William Falkenström, Consultant with the Assembly and Production Flow team at Virtual Manufacturing
The Shooter Wagon Animation
To illustrate the functions and benefits of shooter wagons, William and his team created an animation to demonstrate the mechanics and ingenuity of the karakuri devices. The animation, demonstrates the shooter wagon concept in a simple material-handling example:
“In the demo, the material handler prepares the kit in boxes and places them on the gravity roller tracks on the top level of the shooter,” explained William. “These are basically angled tracks that allow the boxes to slide down using gravity.”
“When the shooter is full, it is transported to the production area, either manually or by an automated guided vehicle (AGV).”
At production, the shooter trolley is docked at the material shelf. Upon docking, the shooter automatically gives the prepared kit boxes to production while receiving empty ones. After the exchange, the shooter trolley goes back to the kitting area to be filled again.
In addition to demonstrating the concept, the animation provides a very detailed visualization of the inner workings of the shooter wagons.
“You’ll notice that when the boxes hit a mechanical stop, they’re waiting to be transported down a level,” said William. “The weight of a box at this mechanical stop is used to signal a raise of the tilt-elevator up one level. When the tilt is raised, it hits a mechanical switch, allowing the box to slide in. The weight of the box is heavier than the counterweight, and the tilt shifts downward.”
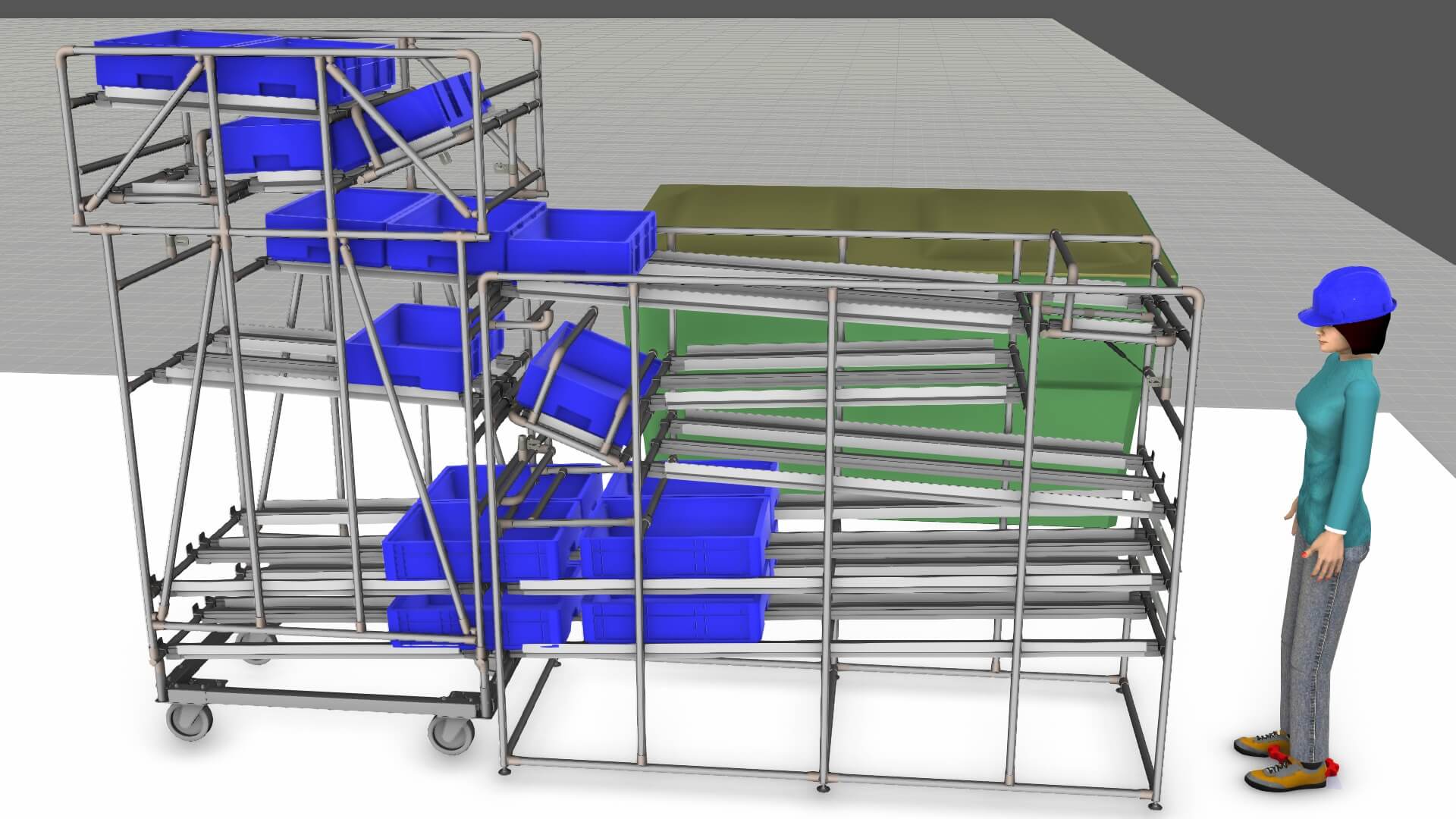
When the wagon comes together with the material shelf in production, a mechanical sprint is lifted, allowing boxes to flow between the gravity rollers of the shooter and the shelf. The exchange is performed automatically, using nothing but gravity.
Project Outcomes and Benefits
The LMP sales team now has a tool to more clearly and convincingly present the functions and benefits of shooter wagons. With the Visual Components Experience app, they have the ability to present interactive and 3D animations of their offerings, right from their mobile devices, wherever they are. They’ve since created more demonstrators, such as this palletizing animation, which show shooter wagons in difference contexts.
“It is helping LMP to profile itself as using market leading demo tools and technology,” said William. “This can be done during customer visits but also fairs, conferences, and trade shows. Other suppliers are opening catalogues and print brochures to showcase their products. LMP is now able to show a detailed animation of how the shooter wagons work in a manufacturing environment. It’s easy to see which method is more effective and impactful for the customer.”
Further reading
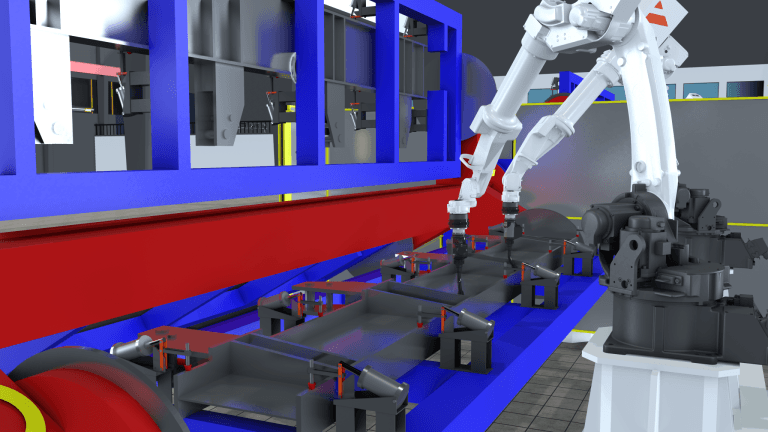
BENTELER rolls out the production technology of tomorrow with the help of Visual Components
Together with BENTELER Automobiltechnik, Karlsruhe Institute of Technology uses modern factory planning software from Visual Components to develop innovative production technologies.
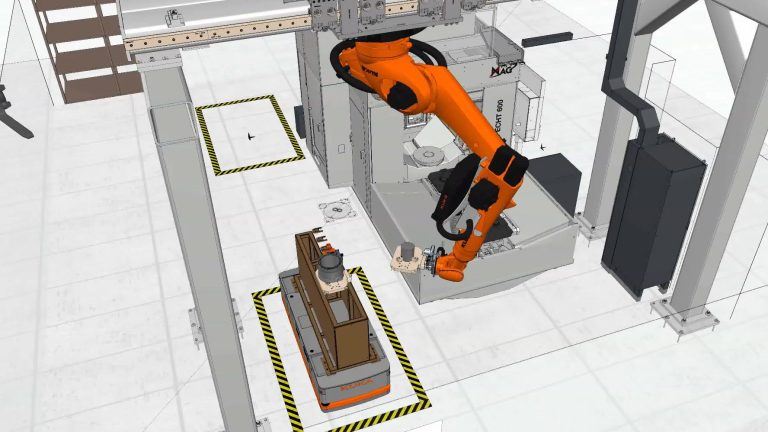
Optimizing flexible manufacturing systems with Visual Components at MAG
In this case study, we’ll show you how MAG’s Factory Automation department used Visual Components to design and optimize a flexible manufacturing system for unmanned or reduced-manning production.