Enhancing adaptive production systems with Visual Components at SDU
In this case study, we’ll take a look at a recent research project into adaptive production systems sponsored by The University of Southern Denmark (SDU) and the Danish RoboCluster and show you how SDU is using Visual Components for both academic research and classroom education.
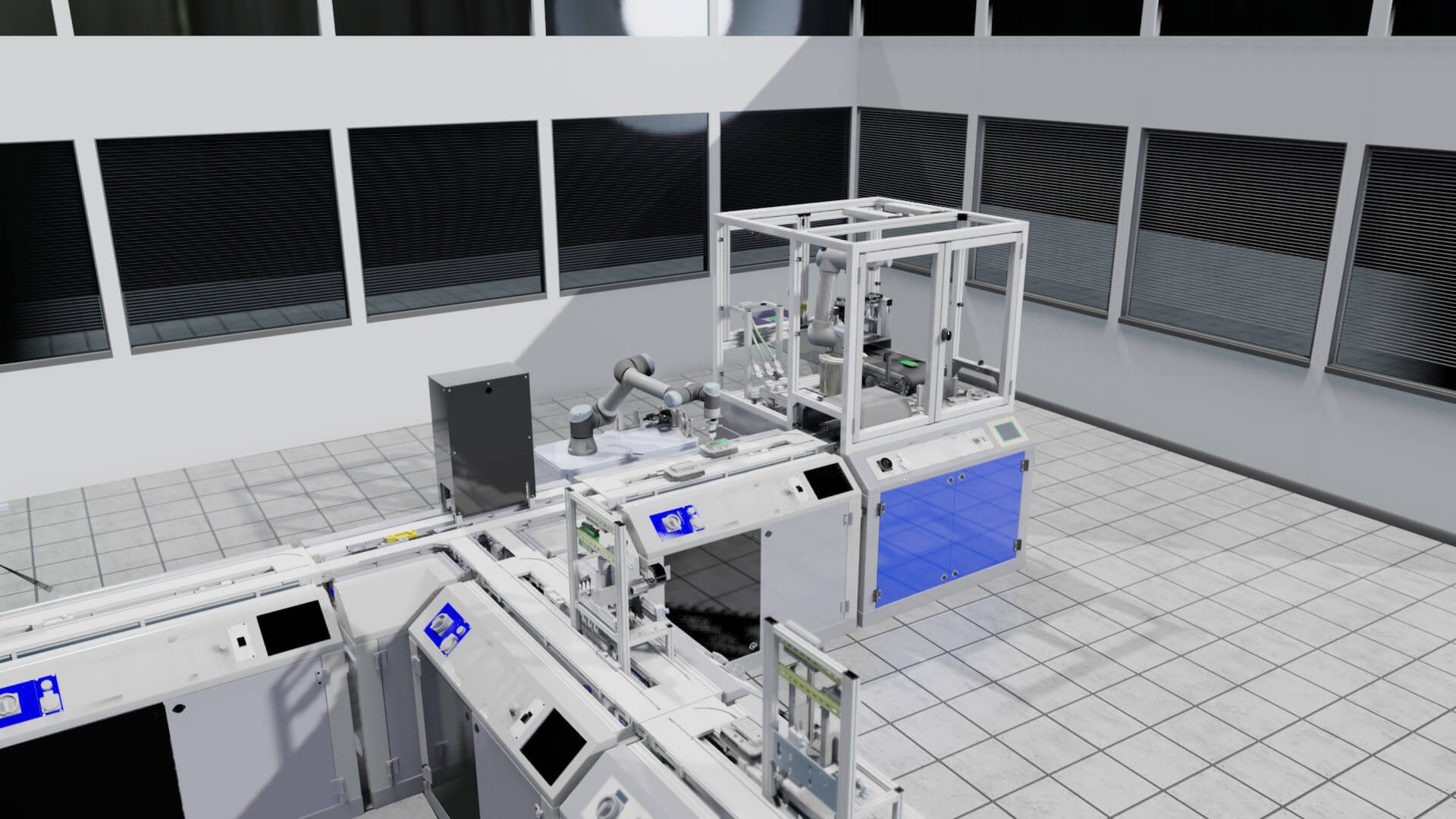
The University of Southern Denmark (SDU) is home to 27,000 students, with approximately 3,000 students enrolled in its engineering study programs. Its main campus is located in Odense, the center of robotics research and innovation in Denmark and birthplace of notable companies such as Universal Robots and Mobile Industrial Robots (MiR).
The Technology Entrepreneurship and Innovation section within SDU’s Mads Clausen Institute carries out extensive research within the area of digitalized production and is highly focused on developing intelligent, autonomous systems that can solve socially relevant issues. One area under active investigation is adaptive production systems.
In this case study, we’ll take a look at a recent research project into adaptive production systems sponsored by SDU and the Danish RoboCluster and show you how SDU is using Visual Components for both academic research and classroom education.
Exploring the potential of robot assistants in adaptive production
“Today’s industrial assembly systems are required to rapidly adapt their facilities to meet fast-changing customer requirements,” said Elias Ribeiro da Silva, an Assistant Professor at SDU. “To explore the potential of using robot assistants to help meet these changing requirements, we developed a full assembly process demonstration of a mobile phone-like product, combining the physical and digital systems while continuous simulations were used to evaluate its feasibility.”
The project involved multiple partners in Danish industry and academia, which contributed different resources and expertise. Aalborg University was responsible for creating the physical setup and integrating the Festo modules and different robots. SDU was responsible for using continuous simulation to test and show different scenarios using robot assistants in the production system. Integrate DK was responsible for using discrete event simulation to statistically analyze the potential for the different scenarios developed. 4Tech Apps was responsible for setting up the quick tool changers for the robots. Plus Pack supported the setup of the packaging process in the production system.
Combining the physical and digital systems
The first step in the demonstration was the creation of a modular production setup, that could accommodate robot assistants and human workers joining the operations. The robot assistants were composed of a collaborative robot on a mobile trolley and equipped with a quick tool changer and three tools.
Based on the variant of the product being assembled, a configuration or scenario for the production system was automatically chosen by the Manufacturing Execution System (MES). The MES had the ability to request different tools in the robot. Then, based on the MES, the robot knew where to position itself and what process needed to be performed.
The baseline scenario for this demonstration was a fully automated line, with no humans or robot assistants, and where all the operations occurred in the robot cells. In other scenarios, where additional processes were required (i.e. placing fuses or glueing pieces together), the MES system divided the tasks to be performed by robot assistants and human workers side-by-side. The project team evaluated five main production scenarios.
- Scenario 1: Fully automated with 1 robot assistant
- Scenario 2: Fully automated with 2 robot assistants
- Scenario 3: Semi-automated with 1 human and 1 robot assistant
- Scenario 4: Partially manual with robot cell and 1 human
- Scenario 5: Fully manual (no robots)
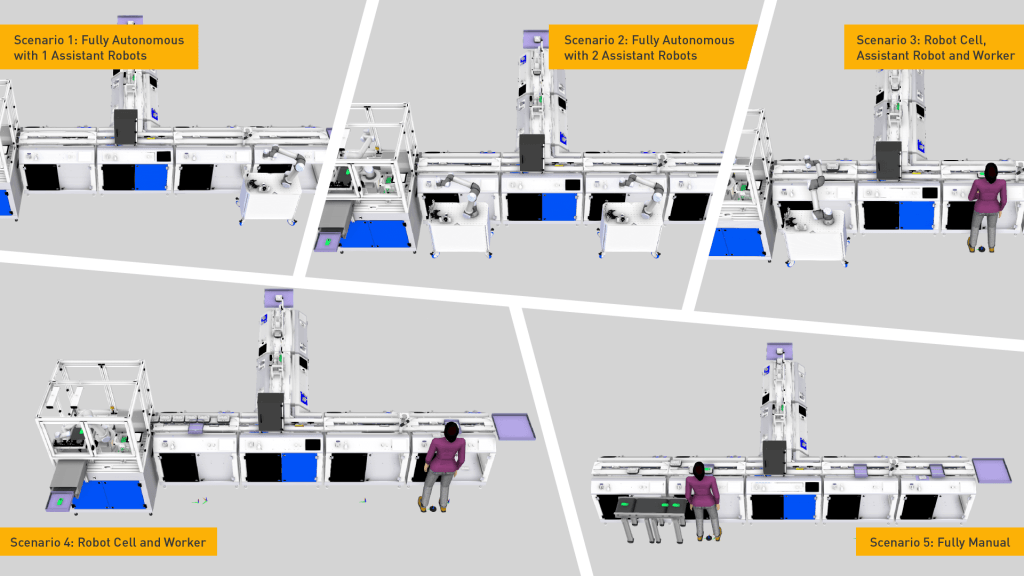
SDU used Visual Components to create a digital twin of the physical production setup at Aalborg University and ran continuous simulations of the different scenarios to plan, optimize, and evaluate each configuration. They also used the software to help visualize what was happening.
“Visual Components produces high-quality 3D visualizations, which helped us to develop, explain, demonstrate, and visualize each scenario,” said Elias. “We also used Visual Components to show the project’s stakeholders in a visual and intuitive way the purpose of each scenario. This made it easier for them to understand the results and the feedback was quite positive.”
Visual Components produces high-quality 3D visualizations, which helped us to develop, explain, demonstrate, and visualize each scenario. We also used Visual Components to show the project’s stakeholders in a visual and intuitive way the purpose of each scenario. This made it easier for them to understand the results and the feedback was quite positive.
Elias Ribeiro da Silva, Assistant Professor at SDU
A viable alternative to scale up production
Results of the project were presented at Aalborg University in March 2020. “The goal of this demonstration was to show the potential of adaptive production systems in industry, and specifically how robot assistants with quick tool changers could seamlessly join a production system to provide additional capacity or perform different tasks,” said Elias. “I think we achieved that.”
The project team found that robot assistants utilizing quick tool change can help to improve the productivity and flexibility of production lines, especially high-mix, low-volume production. Comparing Scenario 2 (fully automated with 2 robot assistants) to Scenario 5 (fully manual, no robots), the productivity of Scenario 2 was shown to be 18% higher.
They also showed that robot assistants are a viable alternative to slightly scale up production in a fast and flexible way, and that collaborative robots can be utilized in adaptive production systems.
“Small and medium-sized companies that use these types of production systems typically design them so that the processes are happening in the robot cell instead of being shared by different robots, making them not very flexible or scalable,” said Elias. “We showed that it’s possible to design an assembly system to accommodate on-demand resources, such as robot assistants, and that these resources could be automatically scheduled, summoned, and tasked by the MES.”
Educating the next generation of engineers
In addition to his research interests, Professor Ribeiro da Silva also teaches courses to graduate and undergraduate students at SDU. Two courses at SDU – an undergraduate course in Operations Management and a graduate course in Automation and Digitalization, incorporate Visual Components as part of their curriculums.
Visual Components is quite easy to start working with and we’ve found it to be an amazing tool for the academic environment. In only a few hours, our students are able to create different scenarios in Visual Components and discuss different aspects of production systems, which is much faster compared to other factory simulation products we’ve tested in the past.
Elias Ribeiro da Silva, Assistant Professor at SDU
Further reading
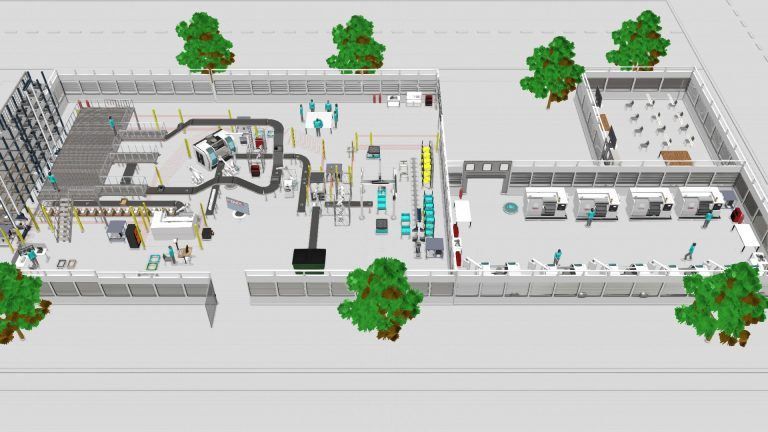
International robotics and simulation competition in China, and smart factory project
This case is about a large-scale international competition where hundreds of students participated in designing the digital twin of smart factories using Visual Components-based powerful simulation technology. Read more about...
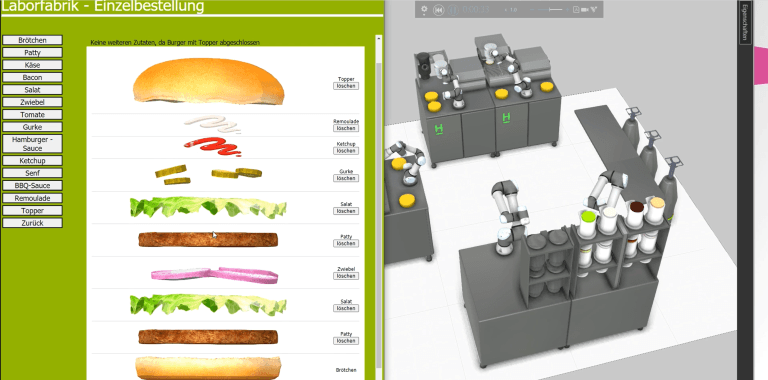
Helping students accurately simulate production environments in real-time
How can simulating an automated restaurant-like environment help students understand the power of simulation?
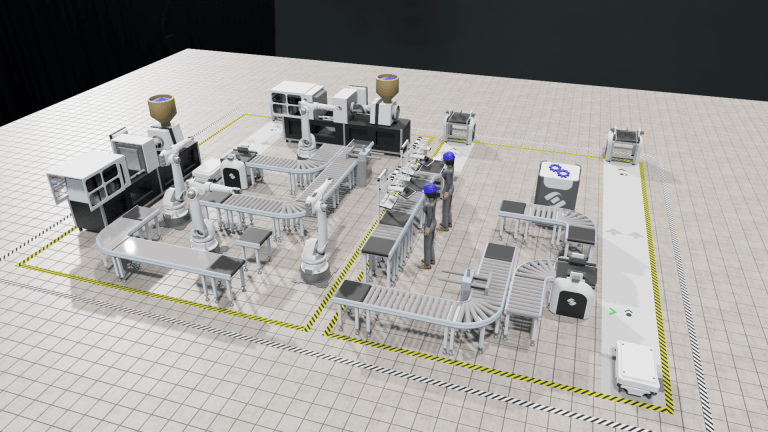
CU Coventry Case Study: Sparking Students’ Creativity When Designing Real-life Industrial Scenarios
A look at how students in Coventry University's Electro-Mechanical Engineering use Visual Components' 3D simulation software to carry out factory floor simulation.