Smart Factory Project, a successful collaboration between TEMEX and VSB-Technical University of Ostrava
Read how TEMEX, a Czech-based manufacturing technology specialist, brought the Smart Factory project, a robust teaching tool at the VSB-Technical University of Ostrava, from concept to reality using Visual Components 3D production simulation software.
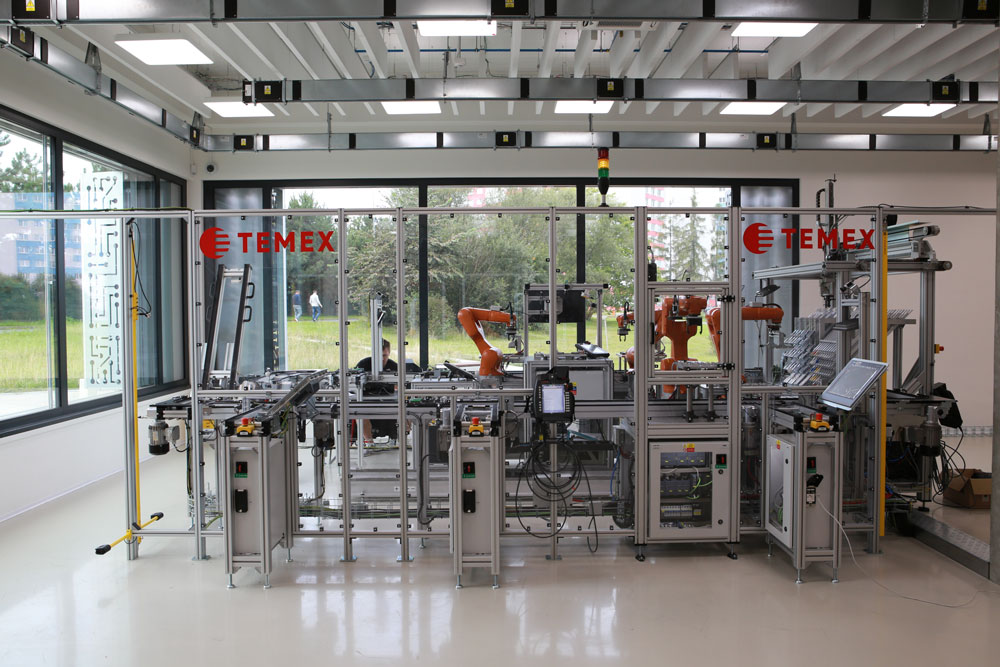
TEMEX is a Czech-based company specializing in developing and implementing technical solutions to increase production efficiency and improve overall working environments. Simply put, it’s a firm with a mission of creating new technologies to serve its global customer base, and it’s part of the reason it got involved with VSB-Technical University of Ostrava in the fall of 2019 on its “Smart Factory” laboratory supported by the European Regional Development Fund in „Platform of modern technology at FEI CPIT TL3“ project, reg. nr. CZ.02.2.67/0.0/0.0/16_016/0002467 within the Operational Programme Research, Development and Education. Designed to be a training assembly line for both the automated and manual assembly of products for its students of today and tomorrow, the project’s intent was to demonstrate the latest technologies and principles of Industry 4.0 in a real-world format.
TEMEX was tasked with completing automated assembly line delivery, including design, integration and delivery of the production environment for the assembly of products made from Legos, the Lego building base and electronic components. TEMEX had one year to develop this educational production line for the University’s new study programme , “Computer Systems for Industry of 21st Century.”
Read on for more about how TEMEX brought this Smart Factory project from concept to reality, and how Visual Components’ 3D production simulation software was able to help meet both deadlines and goals.
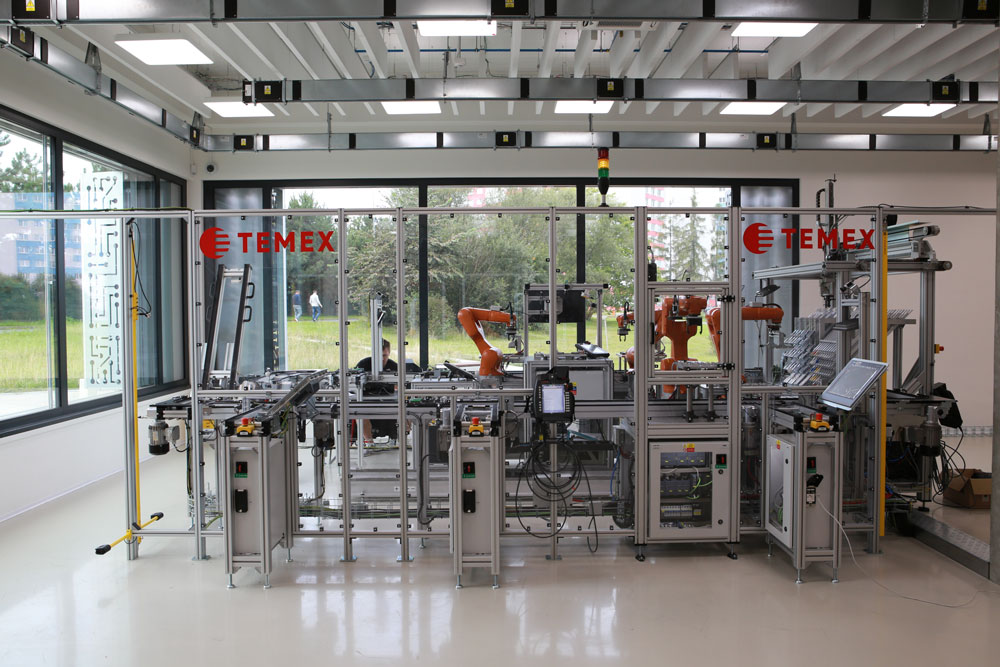
About the Smart Factory Project
The Smart Factory project was to develop a new educational assembly line for students of Faculty of Electrical Engineering and Computer Science and also students from other faculties. VSB-Technical University of Ostrava ‘s idea for its Smart Factory laboratory was conceived to demonstrate various Industry 4.0 principles such as interoperability, virtualization, decentralization, real-time operating, service orientation and modularity.
As noted in the previous section, the production system was conceived to carry out automated and manual delivery of Lego blocks created using a 3D printer. Configuration of both the product and production method is selected at the beginning of each production cycle using a graphical user interface on a tablet. Once this is configured, the assembly cycle begins by taking an empty product container from stock. The manipulator takes all parts of the selected product and then loads them into the product container. Once the container is confirmed to be holding the necessary parts, it is placed on the conveyor portion of the assembly line.
Each Lego base houses a memory identifier that contains all information about the individual parts of the product and operations that are designed to be carried out. A control system will pick the appropriate workplace with production capacity and assign processing to it accordingly. The operation follows. . If automation is selected, the robots are able to produce the defined product. If manual assembly is selected, containers with product parts are instead transported to an operator to carry out the task.
At the end of the production cycle, the line will automate the inspection of each product at the test station to report back product correctness and functionality. An MES (manufacturing execution system) is responsible for warehouse management.
Visual Components Simulation Software Provides Key Assist
Since the Smart Factory project was a first-of-its-kind endeavor for VSB-Technical University of Ostrava, the good news is that TEMEX didn’t have to incorporate the production line into any existing infrastructure. However, engineers were still challenged to come up with a system that incorporated the likes of 3D printers, robotic workstations and methods of line rearrangement. The system had to be robust and include augmented reality and assisted assembly technology.
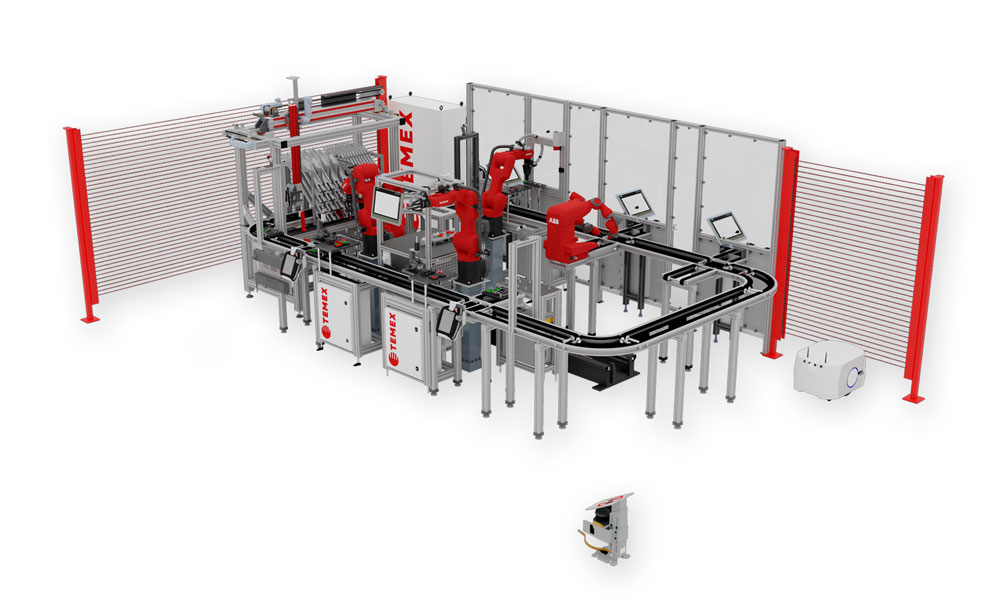
When it came to designing the line layout and incorporating all of these other necessities, TEMEX turned to Visual Components. The VC simulation software helped TEMEX engineers quickly prepare simulations of the line and the ongoing processes designed to take place on it. The VC platform also allowed TEMEX engineers the luxury of adjusting basic layouts into additional simulations of modular line layouts with ease. This all assisted with simulation in a near real-time environment to meet the University’s requirements and help keep the project on track for a summer 2020 completion.
“Preparing for this project was a great responsibility and, at the same time, a significant shift in terms of the scope of using Visual Components for simulations of the environment and all consecutive individual processes,” says Roman Vybiral, TEMEX CEO. “Thanks to this project, we realized that accurate simulations could draw attention to problems that may occur during the equipment’s commissioning. Using Visual Components prevents these problems in the functionality and throughput of the line in time and at a much lower cost.”
“Visual Components has become part of the preparation of some projects. It’s very useful to combine several interlocking elements and identify problems or weaknesses in production processes and flows in time.”
Roman Vybiral, TEMEX CEO
The End Result
The end result is a robust teaching tool that can help educate the next generation of creators and programmers at VSB-Technical University of Ostrava — for years to come.
“The ability to see the entire production line and verify its proper functionality in almost real conditions before its production using Visual Components translated to a huge savings of time, labor and costs for all those involved in its development and production”
Roman Vybiral, TEMEX CEO
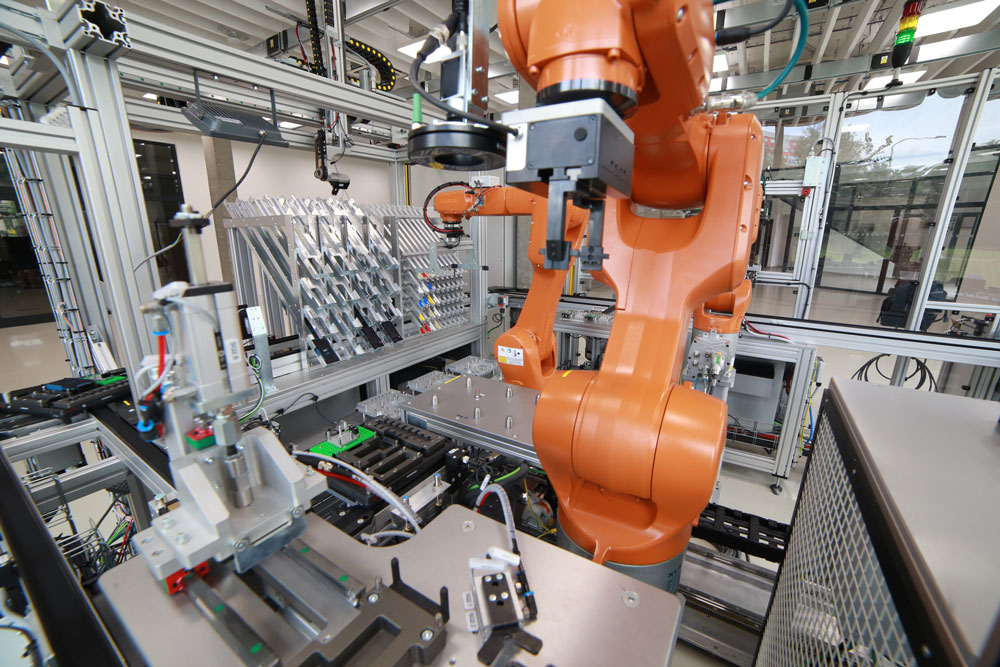
And for TEMEX, the Smart Factory project also opened up new possibilities for implementing Visual Components 3D production simulation software. As a firm that’s always striving to move its operations forward and push the envelope in what it can do technologically, it can now use the VC programs to create a digital twin of large-scale production lines, going beyond just using it for pure assembly equipment. Furthermore, TEMEX also sees an opportunity to use VC software in aluminum wheel manufacturing, palletizing and depalletizing lines, and more to continue to emerge as a technological leader in the Czech Republic.
Further reading
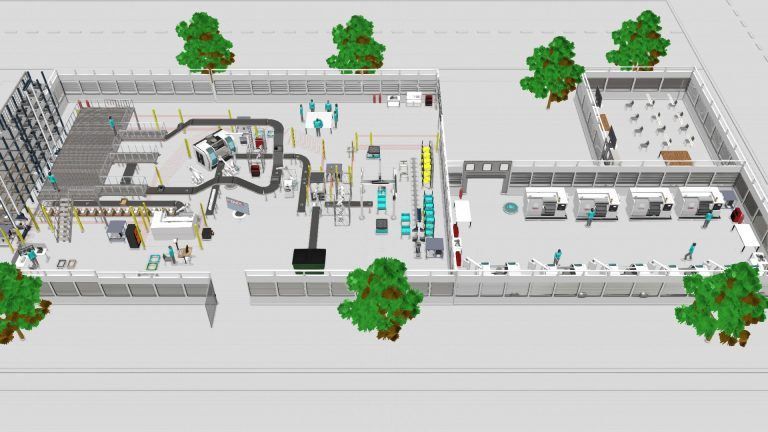
International robotics and simulation competition in China, and smart factory project
This case is about a large-scale international competition where hundreds of students participated in designing the digital twin of smart factories using Visual Components-based powerful simulation technology. Read more about...
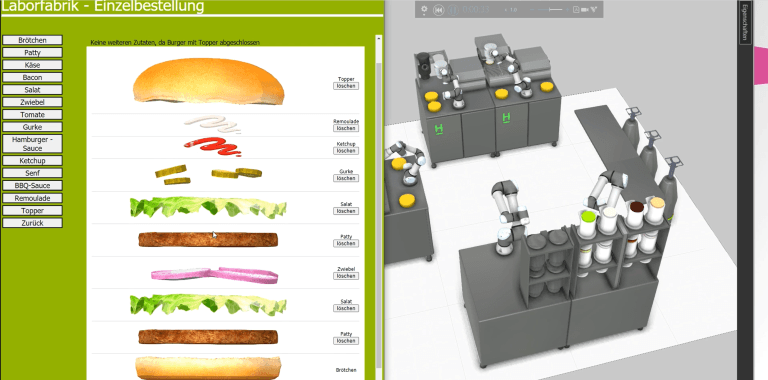
Helping students accurately simulate production environments in real-time
How can simulating an automated restaurant-like environment help students understand the power of simulation?
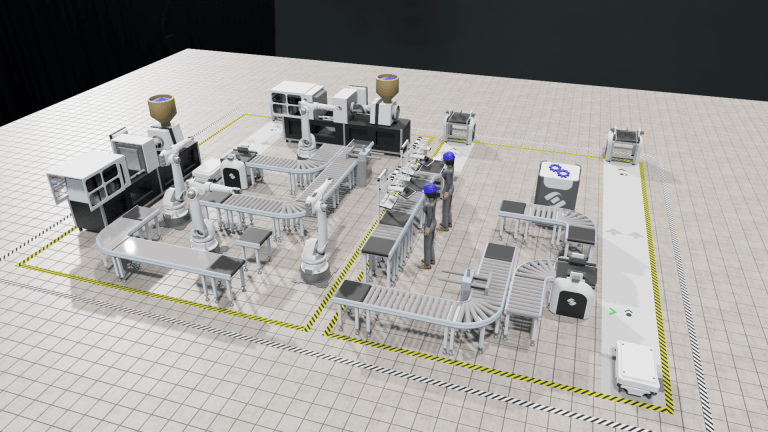
CU Coventry Case Study: Sparking Students’ Creativity When Designing Real-life Industrial Scenarios
A look at how students in Coventry University's Electro-Mechanical Engineering use Visual Components' 3D simulation software to carry out factory floor simulation.