Maximizing efficiency and ROI from day 1: Duun Industrier pre-programs a welding robot cell with Visual Components OLP
Duun Industrier, a leading Norwegian heavy machinery manufacturer, installed the Nordics’ largest robotic welding station in 2013. Utilizing Visual Components for robot programming since 2014, they commissioned a new robot station in 2024 for smaller workpieces. By pre-programming with Visual Components OLP software, the welding robot cell was operational from day one with minimal rework, ensuring a rapid ROI and maximizing the value of both hardware and software.
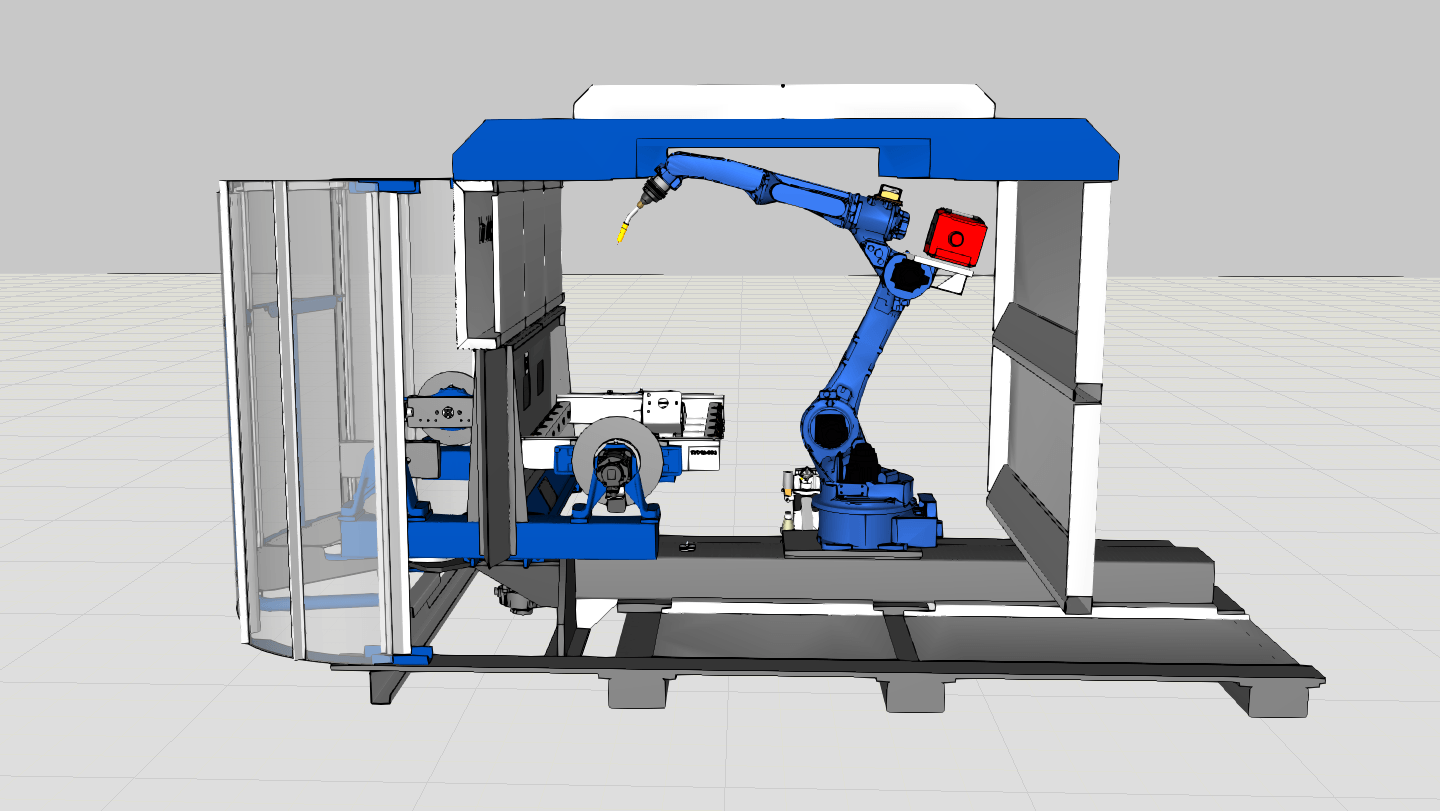
Quality, innovation and efficiency: Crafting extraordinary solutions since 1956
Operating from a 9,000 sq. m. (96,875 sq. ft.) facility, Duun Industrier focuses on developing, designing and manufacturing high-quality products in-house. They demonstrated their commitment to innovation in 2013 when they installed the largest robotic welding station in Norway and the Nordics. This station costs €1.46M ($1.6M) and features a portal with two Yaskawa welding robots, each equipped with eleven servo-controlled axes and two-piece handling machines.
To further enhance their manufacturing capabilities, Duun Industrier has utilized Visual Components to program their robot cells since 2014. In 2024, they expanded their operations by commissioning a new robot station to handle smaller workpieces.
Targeting day-one operation for the new welding robot cell
Faced with the challenge of needing their new welding robot cell operational immediately upon delivery, Duun Industrier turned to Visual Components robot offline programming (OLP) software.
It is important for us to get started as soon as possible with programming for this new robot cell and not to disturb the existing robot cell system. The physical robot will be delivered here in about one month and we have a desperate need to start programming the Yaskawa ArcWorld robot cell, so it is up and running from day one.
Rolf Even Duun, CTO at Duun Industrier
Traditionally, robot programming would begin only after installation, causing delays and extended production lead times. But with Visual Components OLP, Duun Industrier could start robot programming before the physical installation, ensuring a seamless transition to production. This was critical to ensure that the robot cell could commence operations immediately upon delivery, thereby minimizing downtime and maximizing efficiency.
Using a virtual model of the welding cell, they simulated, tested and refined the welding programs well in advance before the robot arrived. By understanding the kinematic structure of the robot cell, including zero positions and rotating directions of all robot and workpiece positioner joints, they set up an accurate layout in the software. This allowed them to create precise and effective robot programs, ensuring a smooth transition from virtual to physical operations.
Immediate robot operation and enhanced ROI with pre-installation programming
Upon delivery of the physical robot cell, only minor calibrations were needed to align the virtual model with the physical setup. These final adjustments enabled the robot to start welding almost immediately, with minimal touch-ups required. As a result, the ROI for the physical hardware began right away, while the ROI for the Visual Components software had already started with the first robot programming tasks.
On welding robot programming, one of the goals is to remove or significantly reduce the need for touch-up.
Rolf Even Duun, CTO at Duun Industrier
The offline programming approach drastically reduced the time needed to launch the new robotic system. By programming the robot before installation, Duun Industrier eliminated production stoppages typically associated with traditional programming methods. The new robot programs, verified through simulation, were ready for immediate use as soon as the welding of new products started.
High-quality, efficient and on-time production powered by a collaborative knowledge database
Robot offline programming took Duun Industrier’s productivity to the next level while keeping welding quality consistent and high. This is especially important for seasonal products like snow plows that need to hit the market right on time. With offline programming, new welding robot programs were developed and tested outside of production, then smoothly transferred to the robot cell, all without any downtime.
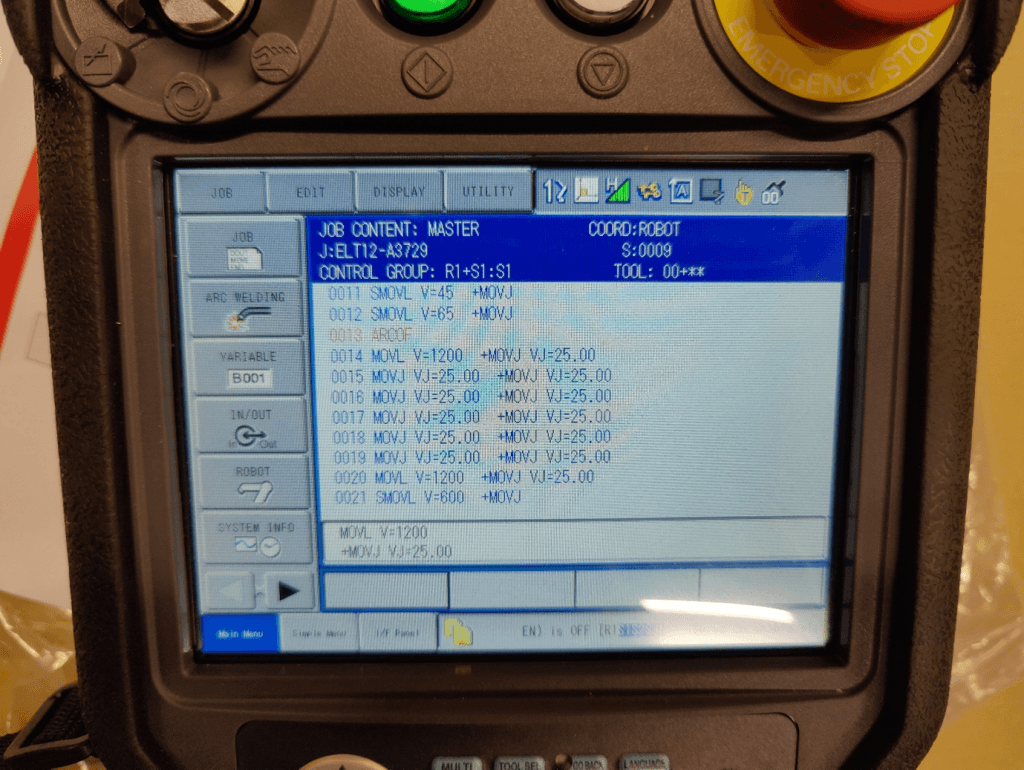
Duun Industrier’s commitment to top-notch welding quality is supported by a custom database built with Visual Components OLP. This database stores optimized welding procedures in a Welding Procedure Specification (WPS) library, making it easy to replicate best practices across different products.
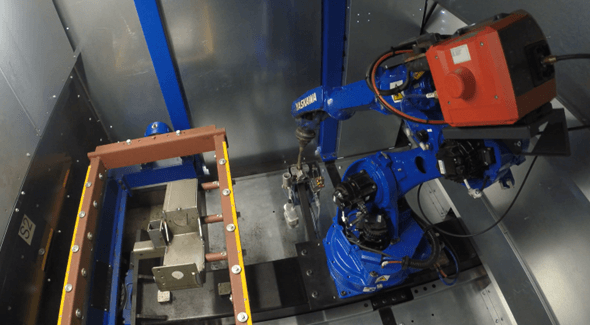
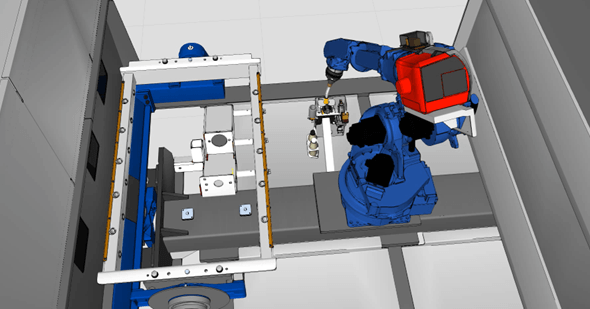
But it’s more than just a database. It’s a collaborative tool for skilled operators to share knowledge and continuously improve. This teamwork, supported by the database, has been key to the success of Duun Industrier’s robot offline programming. The operators’ shared expertise and dedication to continuous improvement are essential to maintaining the company’s high standards in welding.
By integrating Visual Components OLP software into their operations, Duun Industrier has not only streamlined their production processes but also reinforced their commitment to quality and innovation. This strategy maximized efficiency, minimized downtime and ensured a rapid return on investment, all while keeping their products market-ready on time. The use of offline programming has also fostered continuous improvement, empowering their team to consistently enhance quality and drive ongoing success as a leader in the heavy machinery and equipment manufacturing industry.
About Visual Components
Founded by a team of simulation experts and amassing over 20 years in business, Visual Components is one of the pioneers of the 3D manufacturing simulation industry. The organization is a trusted technology partner to a number of leading brands, offering machine builders, system integrators and manufacturers a simple, quick and cost-effective solution to design and simulate production processes and offline robot programming (OLP) technology for fast, accurate and error-free programming of industrial robots.
Want to learn more about the benefits of our solutions for your business? Contact us today!
Further reading
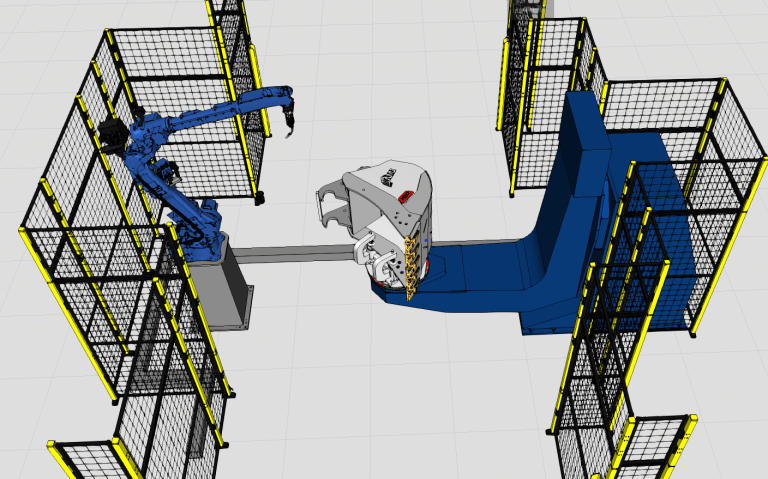
Combatting the welder shortage: how AMI Attachments enhances production efficiency with Visual Components OLP
AMI Attachments, a leading North American manufacturer of heavy equipment attachments, sought to improve product throughput and meet evolving market demands while navigating a welder shortage. By implementing Visual Components...
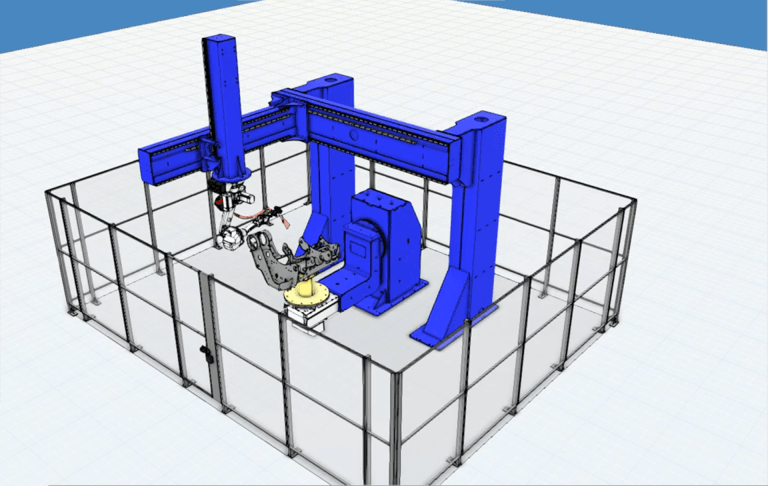
Ponsse is driving forest machine innovation and improving productivity with Visual Components Robotics OLP
Ponsse Plc., a global leader in forest machine manufacturing, has transformed its production process by leveraging Visual Components Robotics OLP.
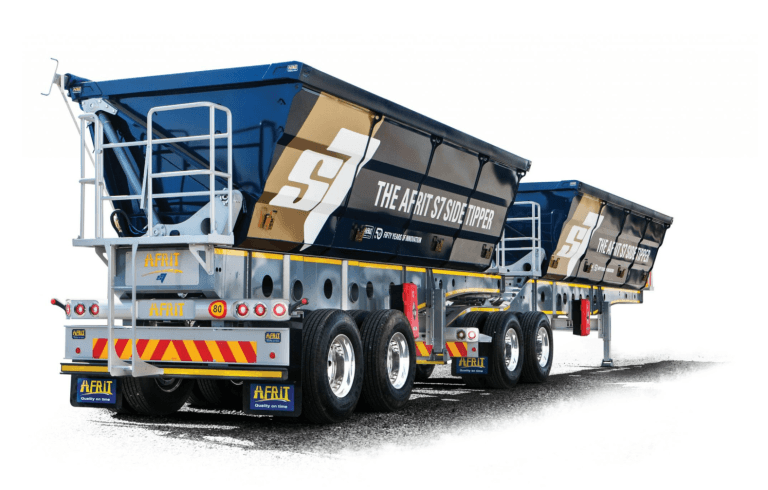
AFRIT production runs faster than ever, thanks to Visual Components Robotics OLP
Read how a trailer manufacturer from South Africa improved the manufacturing efficiency by using Delfoi Robotics Offline Robot Programming solution (Now known as Visual Components Robotics OLP).