International robotics and simulation competition in China, and smart factory project
This case is about a large-scale international competition where hundreds of students participated in designing the digital twin of smart factories using Visual Components-based powerful simulation technology. Read more about this event with details about one of the winning projects.
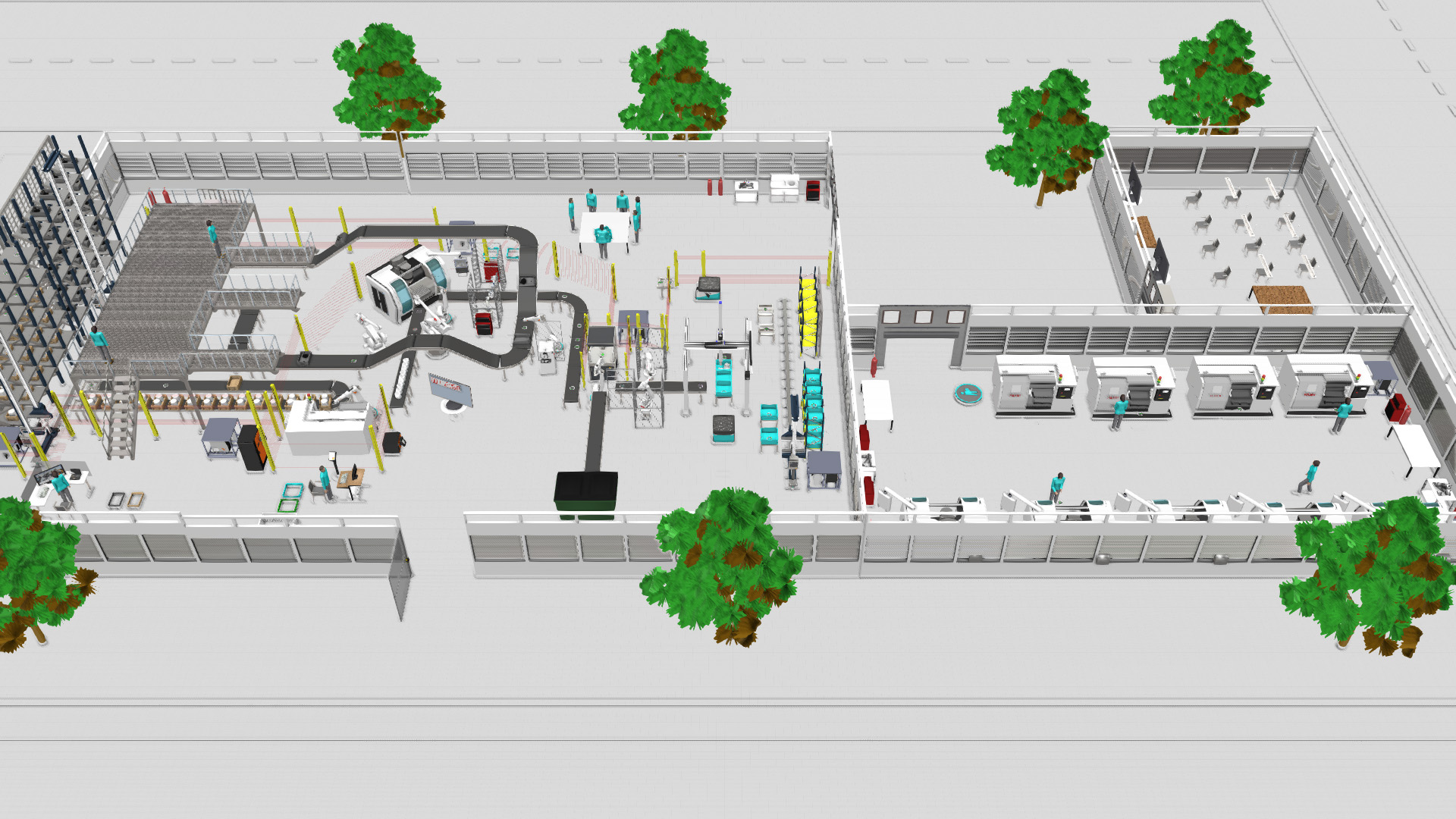
MeiCloud is a full value chain AIoT (Artificial Intelligence of Things) service provider specializing in appliances and industrial applications. Their simulation solution is based on the Visual Components software for industrial digital transformation, smart manufacturing, and automation projects.
This case is about an international technology competition held in China where over 7000 students participated in enhancing their skills in modern industry technologies for robotics, automation, and digital twin using Visual Components-based simulation solution. The ease of use and wide industrial application of the Visual Components solution gave MeiCloud an advantage over other simulation software to be chosen as the only solution provider for this competition. The students participating received active training and technical support from MeiCloud’s team throughout the competition.
15th International Advanced Robot and Simulation Technology Competition
The International Advanced Robot and Simulation Technology Competition is the first and only high-end discipline competition initiated by Chinese universities. Students from all over the world including countries such as the United States, the United Kingdom, Germany, the Netherlands, Australia, Norway, South Korea, etc. participate in this event together with their Chinese counterparts.
The main goal of this kind of competition is to promote simulation technology in colleges and universities, attract more talent to simulation and increase the skills of students by using manufacturing simulation tools together with theoretical knowledge. With the use of simulation, the students start to understand the real-life challenges of industries and learn to solve them by designing the smart factories of the future.
This was the 15th series of this competition which was held from the 1st to the 30th of November 2022. In total, 1510 teams participated in this competition from 369 schools. Each Team on average comprised 5-6 students. In the Online Competition, 190 teams won the first prize, 275 teams won the second prize and 320 teams ended up winning the third prize depending on the level of simulation, production knowledge, and execution of the designs.
Over the years, the competition has become an important stage for students from around the world to show their skills in robot research and development, production, and application, and build a bridge for mutual learning and knowledge exchange.
Project description
The layout below is from one of the winning teams of the competition coming from the North China Institute of Science and Technology. This team designed a smart factory that manufactures impellers, which are typically used in pumps for turbomachines.
The students used simulation technology to create a working model of a smart factory that could be used by other universities. These are the systems that are connected to the simulation model at the core of this project,
1. They used the existing university laboratory and factory of the school and built a connection with the MES (Manufacturing Execution System).
2. They Used 5G technology to collect operational data and monitor the production process of the factory.
3. Additionally, they had a central control system that displayed real-time pictures of the entire production line with workpieces flowing through each station together with real-time machine data.
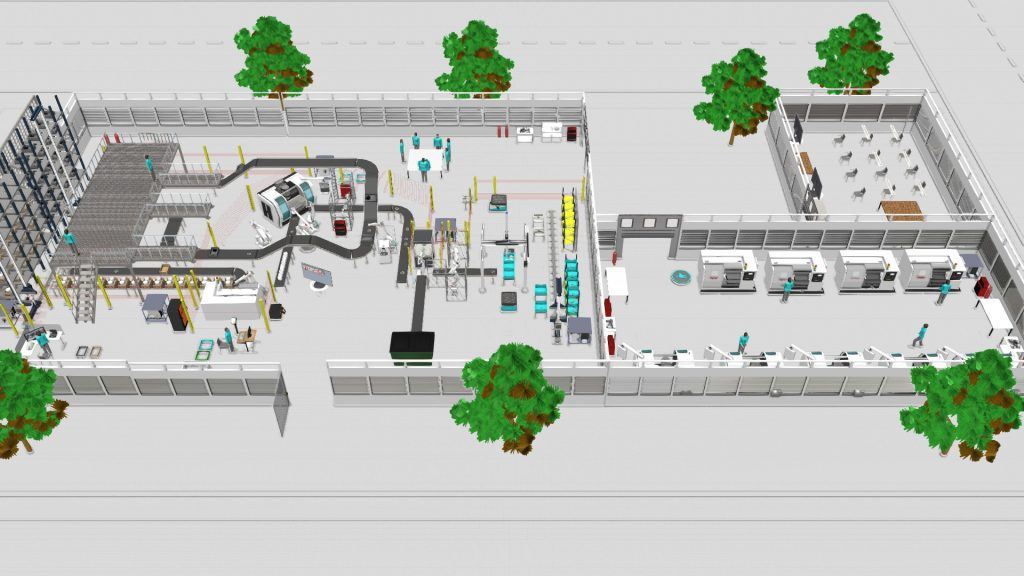
The simulation model of the plant consists of three parts.
- Processing Area
- Practice Area
- Explanation Learning Area
This full-fledged smart factory project mainly used these features of Visual Components,
- Process flow simulation
- Signal connectivity module
- Robot teaching/programming
- Statistical analysis
Factory layout simulation flow
This was the material and process flow of the impeller smart factory,
– Two parts per box pulled from the warehouse for the machining process (milling, lathe, etc) and in parallel the conveyor on the side has two parts per box that come from the warehouse that includes a fixture, base, and a clamp nut to mount the in-process impeller on it before its ready. The CAD geometries of the impeller, fixture, base, and clamp were designed in SolidWorks and were imported into the simulation model.
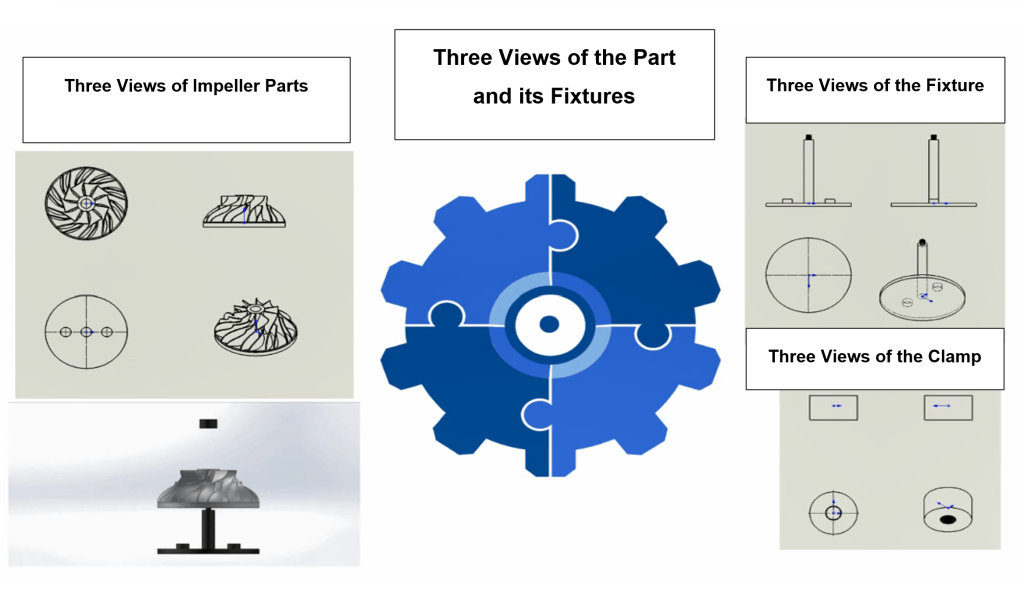
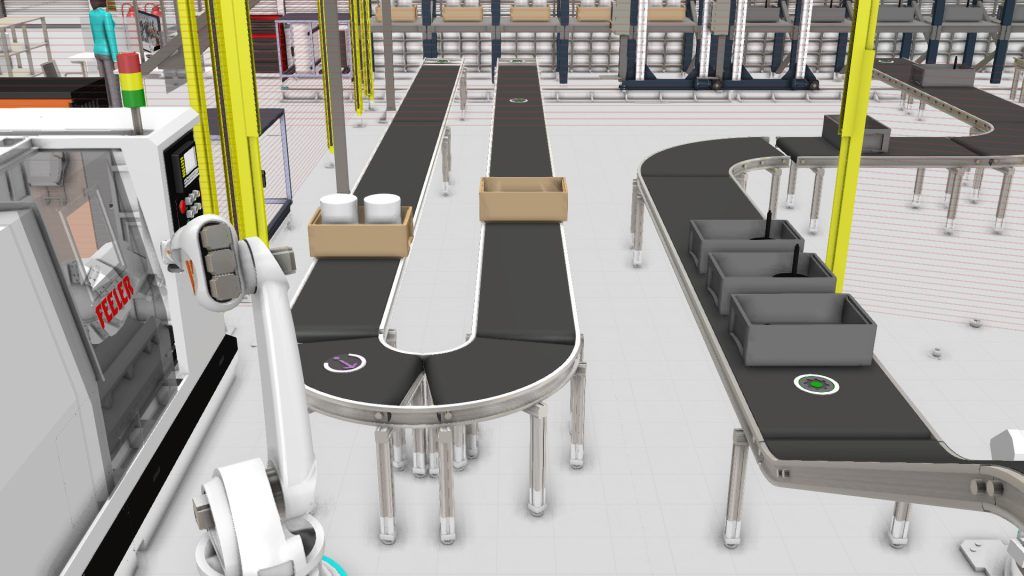
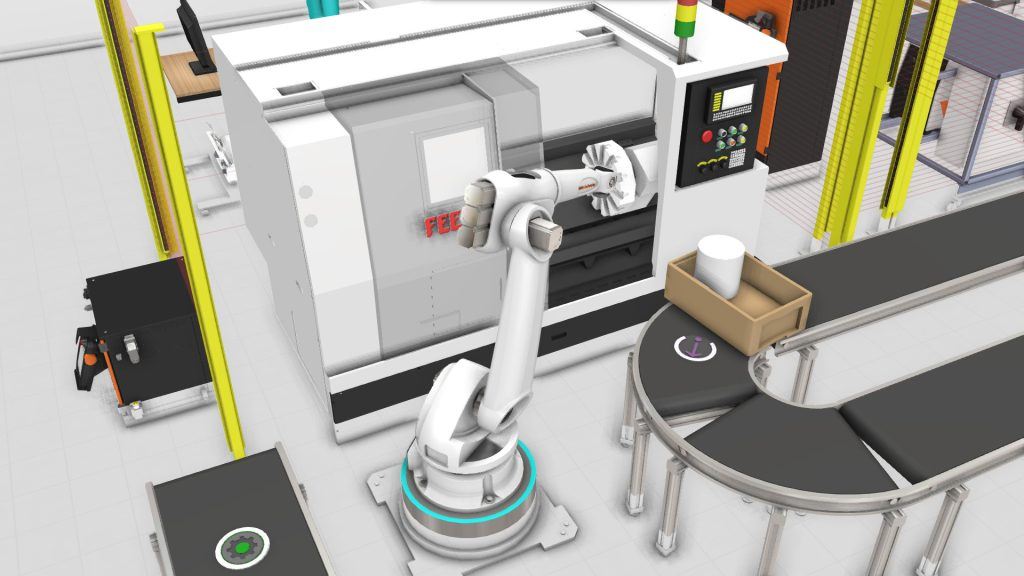
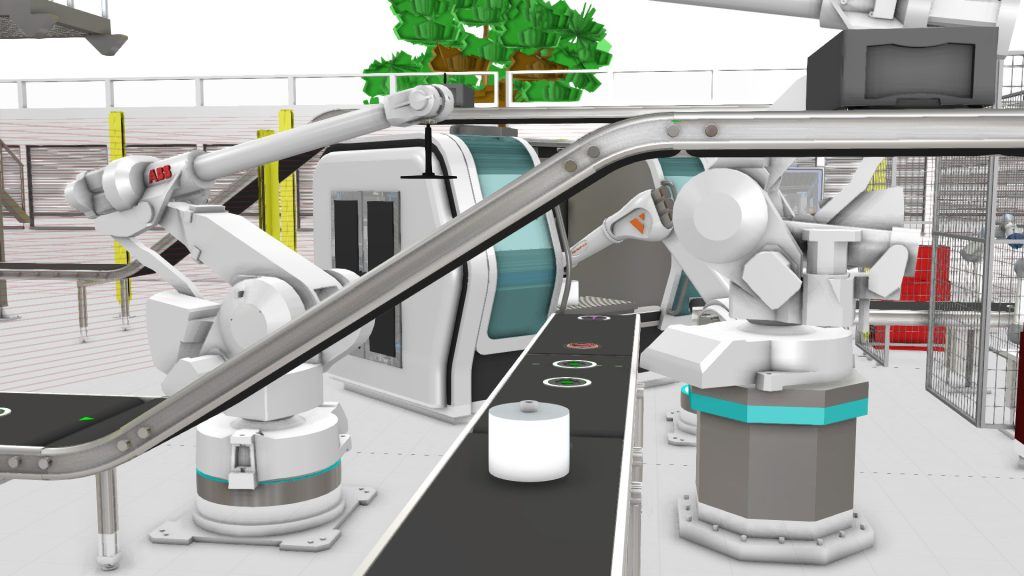
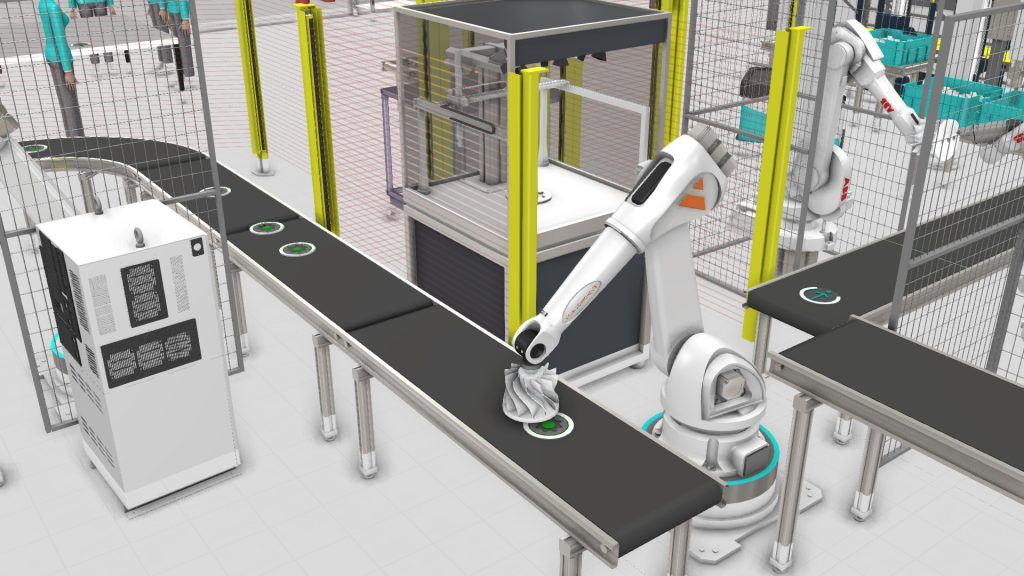
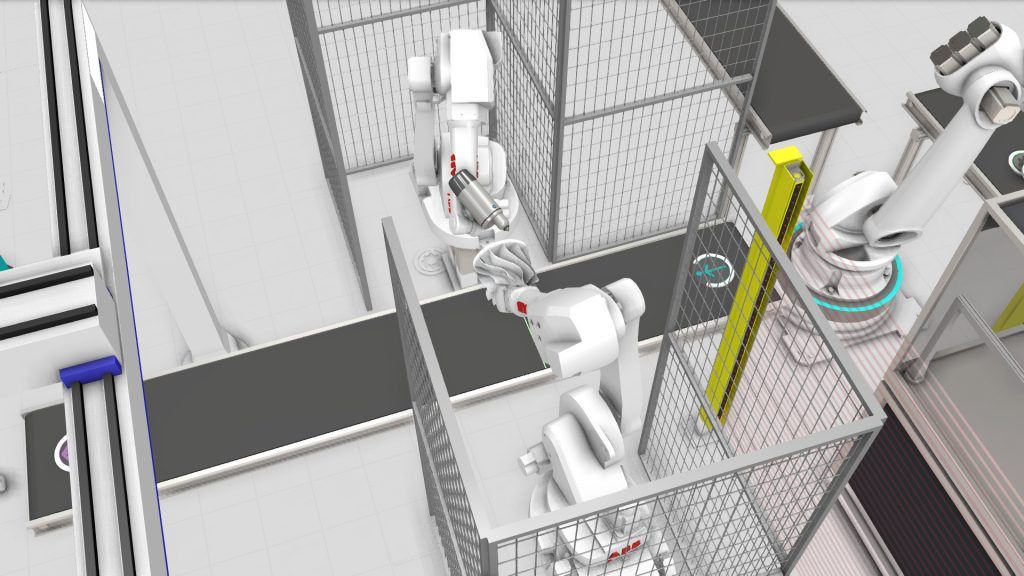
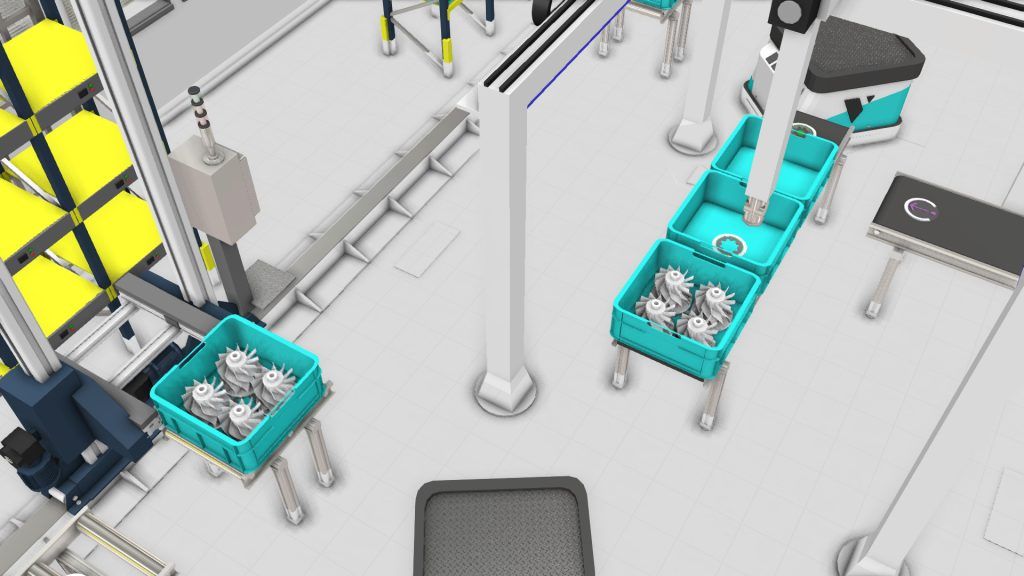
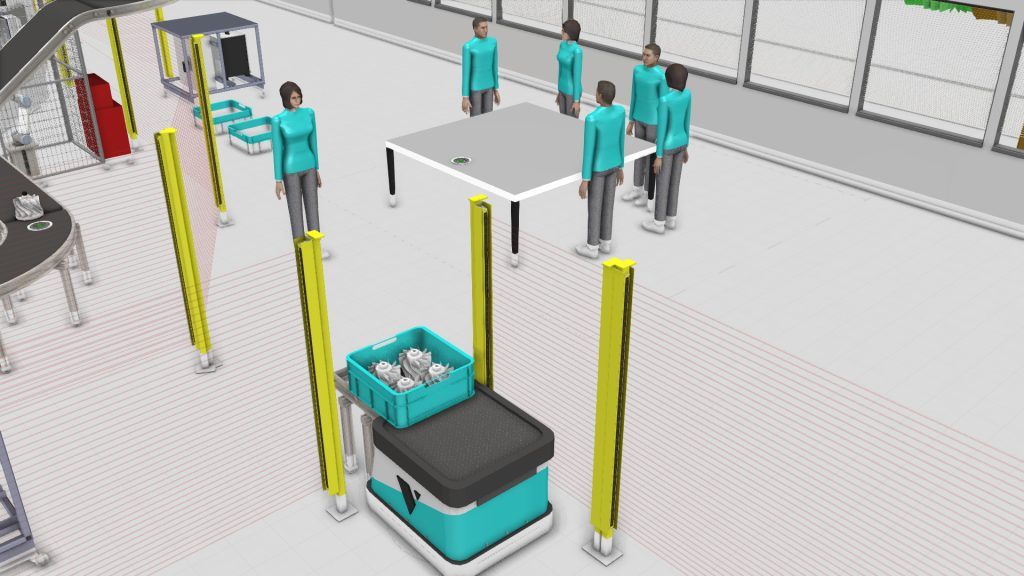
After another Worldwide recognition of the event, MeiCloud will continue these kinds of competitions in the future, perhaps also in other regions of the World. The competition shows the advantages of using Visual Components technology in an education setup, allowing the students to quickly master powerful simulation technology to create digital twins, practice virtual commissioning, and prepare them for the challenges they will experience once they graduate.
If your company wishes to organize similar events and needs support from Visual Components, get in touch with us today!
Further reading
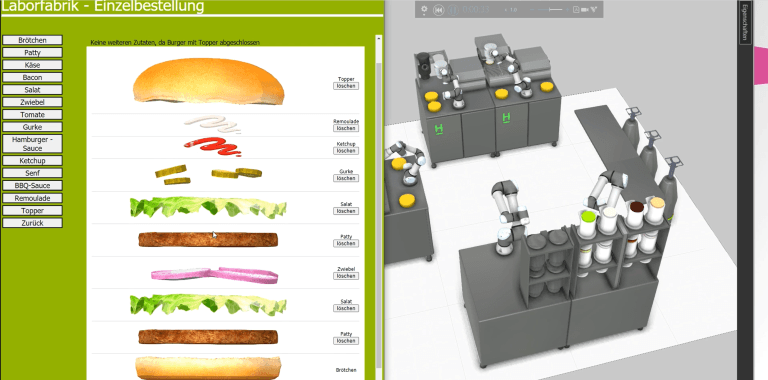
Helping students accurately simulate production environments in real-time
How can simulating an automated restaurant-like environment help students understand the power of simulation?
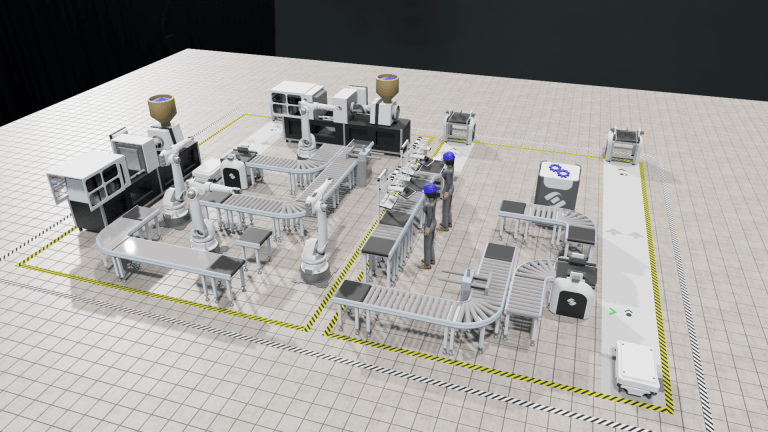
CU Coventry Case Study: Sparking Students’ Creativity When Designing Real-life Industrial Scenarios
A look at how students in Coventry University's Electro-Mechanical Engineering use Visual Components' 3D simulation software to carry out factory floor simulation.
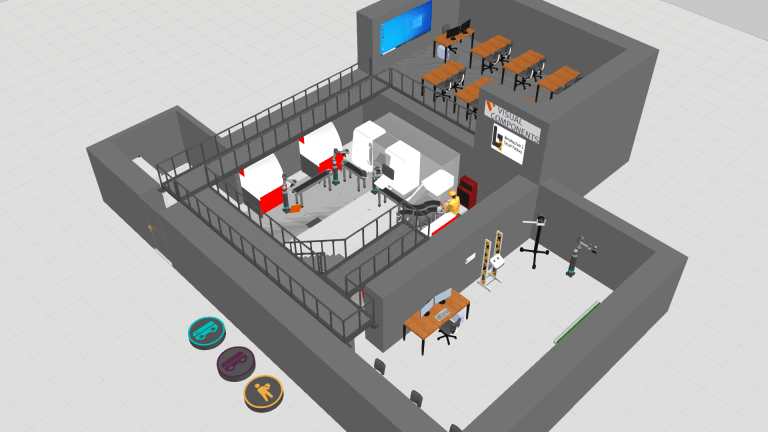
RDF Nuremberg Case Study: With Enthusiasm Towards Digital Transformation
With a digital twin of a smart factory, a technical college in Nuremberg, Germany makes its students fit for the digital transformation.