How Pharmabotix streamlines medical implant production with Visual Components
Since adopting Visual Components, Pharmabotix, a Swiss leader in robot-assisted automation for the pharmaceutical and medical technology industries, has enhanced how it designs and builds systems for producing textile implants. By using simulation, they’ve been able to fine-tune layouts, ensure precise cycle times, and create flexible, modular robotic systems tailored to their customers’ needs.
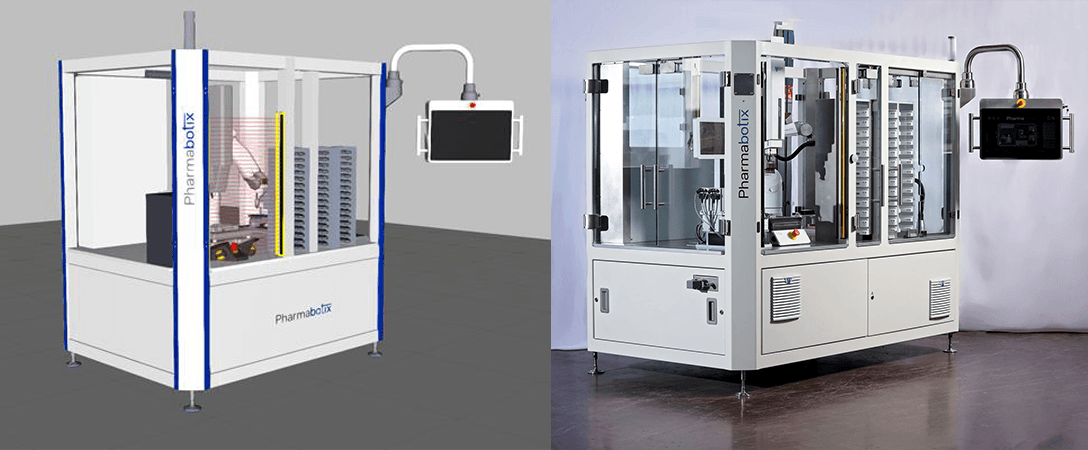
Human life expectancy has seen remarkable growth over the past 150 years, driven largely by advances in medicine and technology. In 1871, the average lifespan was 35.6 years for men and 38.5 years for women. By 2021, these figures had risen to 78.5 and 83.4 years, respectively. Alongside medical breakthroughs, innovations like implants have played a pivotal role—not just in extending life but also in improving its quality.
When people think of implants, dental prosthetics often come to mind, but modern medicine offers a wide array of “spare parts” for the human body. These include hip and knee implants, vascular stents, pacemakers, and more. Each implant is a testament to precision engineering, with specific materials and designs tailored for durability and biocompatibility. For example, orthopedic implants use cobalt-chrome alloys and polyethylene, while textile-based implants require intricate processing under stringent conditions.
Tackling complex production with automation
Pharmabotix, based in the canton of Aargau, Switzerland, specializes in meeting these kinds of production challenges. The company is a leader in robot-assisted automation for the pharmaceutical and medical technology industries, offering solutions from initial concepts to fully operational systems.
For the production of textile components for implants, Pharmabotix relies on robotic automation. The company also uses robots in other systems, such as those for depalletizing, filling, and packaging pharmaceuticals or handling cell cultures for the growing field of cell and gene therapy. To support these demanding projects, Pharmabotix chose Visual Components as its software solution for production system planning and robot programming.
Modular production with robots
For the textile implant production system, the process begins with operators fixing the fabric onto workpiece carriers. A robot then moves each carrier—marked with a serial number and unique code for traceability—from a magazine. The textile is scanned and sent to two needle plotters on linear axes, which punch 180 holes in just a few seconds. A robot removes the processed material, which is then cut with an ultrasonic punch and placed in the finished parts magazine.
At the core of this system is a Stäubli 6-axis robot, which handles components across stations with different cycle times. The system’s modular design allows each station to be activated or deactivated independently, offering flexibility. This flexibility is further enhanced by Pharmabotix’s modular software and the use of robots.
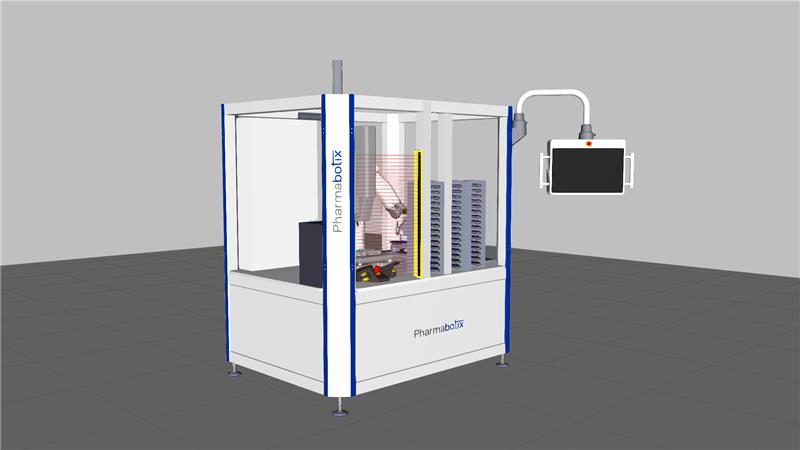
How simulation supports success
Mr. Stutz, founder and managing director of Pharmabotix, shares how Visual Components supports their work:
“We use Visual Components as a fast and easy tool to model plant concepts for our customers. The library included in Visual Components contains many factory components, which makes our work much easier. For our customers, Visual Components offers the added value that they can see the solution we propose as a 3D model and understand it more easily. In this example, the customer was able to ensure that the required cycle time was met thanks to the simulation. The creation of such a detailed simulation only took about 2 days. The simulation also helped us to optimize the layout of the individual stations.”
Checking accessibility and optimizing cycle times
The extensive robot library in Visual Components has been a key resource for Pharmabotix. “This allows us to simulate complete robot systems in order to check reachability and optimize cycle times,” Mr. Stutz explains. “And when we use mobile robots, Visual Components helps us to determine the number of robots required or to identify potential bottlenecks in production at an early stage. We can also program the robots and even carry out virtual commissioning of the systems with Visual Components. The software supports us throughout the entire process—from the simulation of the initial concepts to the handover of the turnkey systems.”
The use of robots not only reduces the risk of human error but also frees employees from monotonous tasks, improving both efficiency and product safety.
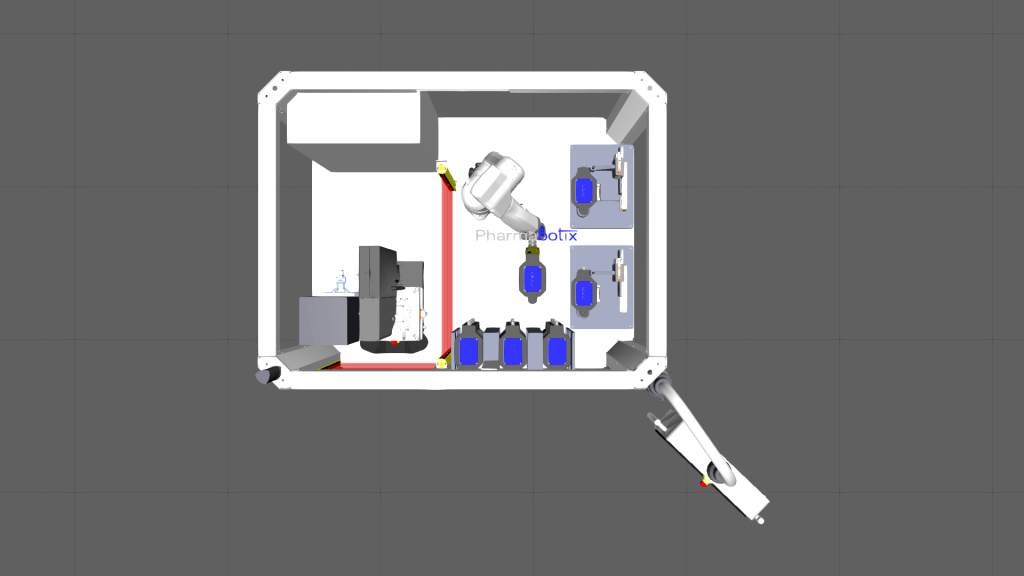
Early detection of production challenges
Summarizing the benefits, Mr. Stutz says: “We want to offer our customers optimal solutions. Visual Components helps us to do this because, thanks to the software, we are able to identify potential bottlenecks in production and difficulties with accessibility even before the actual engineering phase. The software makes a decisive contribution to our ability to successfully turn our ideas into reality.”
About Pharmabotix
Headquartered in Seengen, Switzerland, Pharmabotix specializes in advanced automation solutions for the pharmaceutical and medical technology sectors. With a team of 10, the company offers engineering, software development, and consulting services, empowering their customers with innovative systems that redefine efficiency and precision.
About Visual Components
Visual Components is a leading 3D factory planning and manufacturing simulation software provider. With its extensive library of pre-built factory components, Visual Components helps businesses design, simulate, and optimize production systems. Based in Espoo, Finland, the software is used worldwide across various industries, including automotive, packaging, and logistics.
Visual Components has a dedicated program for start-ups, which has played a key role in Pharmabotix’s growth—from just two founders to a team of 10 employees. Check it out!