How Hollander Techniek designed an automated custom meal packaging system with Visual Components
When Uitgekookt set out to automate its meal packaging process, they needed a system that could handle custom orders with speed and precision. Hollander Techniek used Visual Components to design and test the solution before building it. With 3D simulation, they optimized layouts, fine-tuned workflows, and ensured everything ran smoothly. See how they brought it all together.
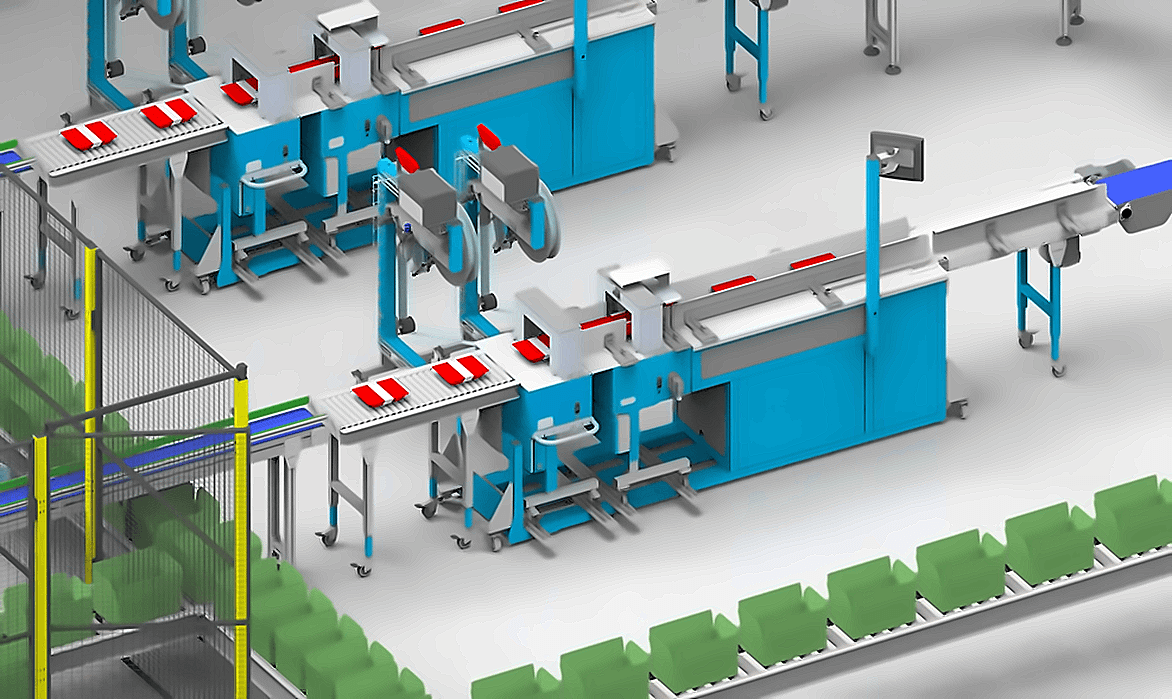
From family business to automation leader
Founded in 1974, Hollander Techniek has grown from a small family business into one of the Netherlands’ leading system integrators. With over 600 employees, the company specializes in automation across utility, home-building, retail, and manufacturing sectors.
When Uitgekookt, a Dutch ready-made meal provider, set out to modernize its meal assembly and packaging process—moving from labor-intensive manual work to automation—they turned to Hollander Techniek. The goal was to design a streamlined, high-efficiency system that could handle customized order fulfillment with minimal human intervention. To help plan this highly complex system, Hollander Techniek used Visual Components’ powerful 3D simulation tools.
The challenge: automating a complex process
Uitgekookt needed to design a reliable, scalable system to efficiently assemble, package, and dispatch meals, while accommodating individual customer orders. Since the process was previously all done manually, this meant reimagining everything from storage to end-of-line packaging.
Traditional warehouse shelving was also a no-go, as it created bottlenecks with excessive forklift traffic slowing productivity. They needed a smarter, bolder approach. But with greater ambition came the need for a clear visual model to ensure everyone understood the concept and to secure stakeholder buy-in.
Simulating success before implementation
Before committing to any big decisions, the Hollander Techniek team turned to Visual Components’ 3D simulation to test their ideas in a risk-free environment. Between July and November 2022, they used the software to:
- Experiment with different layout configurations to ensure everything fit just right.
- Simulate production flows and validate capacity based on weekly demand projections.
- Import real customer production data to design a system that could handle actual workloads.
- Identify bottlenecks early and fine-tune workflows before anything was physically built.
This upfront testing meant they could avoid over-engineering, cut down on wasted resources, and keep costs under control, all before a single piece of equipment was installed.
Engineering an efficient process—starting from the end
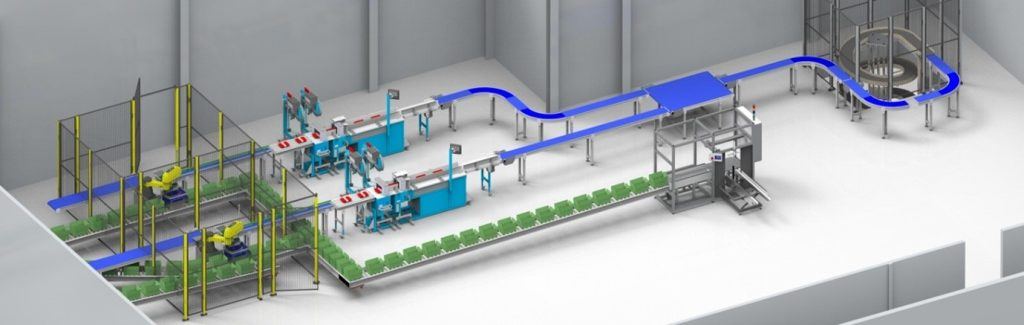
With the confidence gained from simulation, the team rethought the entire process from the end goal backward. Instead of starting with raw materials, they optimized every step by beginning with order fulfillment first, ensuring that packing, stacking, and labeling were all streamlined before moving upstream.
By designing in reverse, Hollander Techniek was able to:
- Visualize the entire automation system, ensuring a seamless flow from one step to the next.
- Perform precise capacity calculations, preventing production slowdowns.
- Import real customer production data, aligning the system with actual workloads.
- Identify potential bottlenecks early, enabling dynamic production planning and efficient order processing.
- Optimize storage and conveyor dimensions, ensuring the right balance between capacity and cost-effectiveness.
With a simulation-first design approach, Hollander Techniek and Uitgekookt eliminated inefficiencies before they became a problem, without the need for costly physical testing.
Delivering results with precision and confidence
With over 300 hours of simulation work, the project team fine-tuned the automation strategy down to the smallest detail. One of the biggest advantages of using Visual Components was the ability to speed up time in simulations. What would take a full week in real life was tested in just one hour thanks to accelerated playback.
All-in-all, the impact of Visual Components was clear:
- Uitgekookt gained a reliable capacity forecast, ensuring their production lines could meet demand without bottlenecks.
- Order processing for custom orders became faster and more precise, eliminating unnecessary manual handling.
- Hollander Techniek delivered a validated, fully optimized automation solution, backed by data and real-world insights.
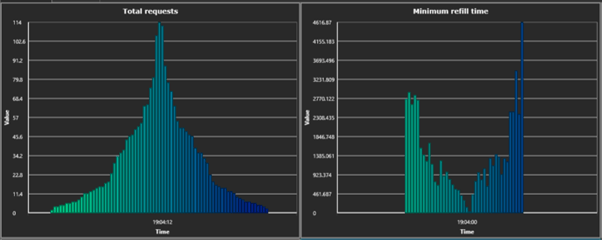
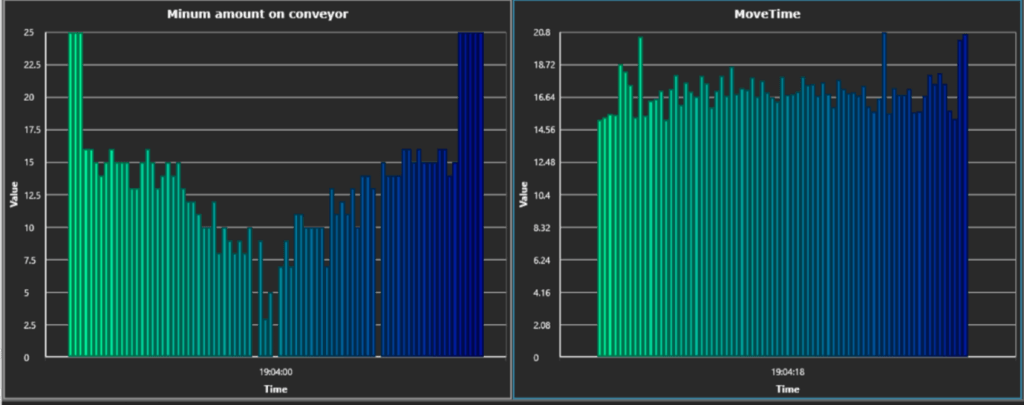
A new standard in system integration
The success of this project made Visual Components a mainstay for Hollander Techniek’s future system integration projects. More than just a planning tool, it has become a go-to resource for testing control software, making sure everything runs smoothly from concept to reality. It also helped with virtual reality (VR) demonstrations, giving customers a way to step inside their automation projects before a single machine was installed.
The collaboration between Hollander Techniek and Uitgekookt highlights the value of simulation-driven planning for automation. With the help of Visual Components, Hollander Techniek transformed an outdated workflow into a modern one.
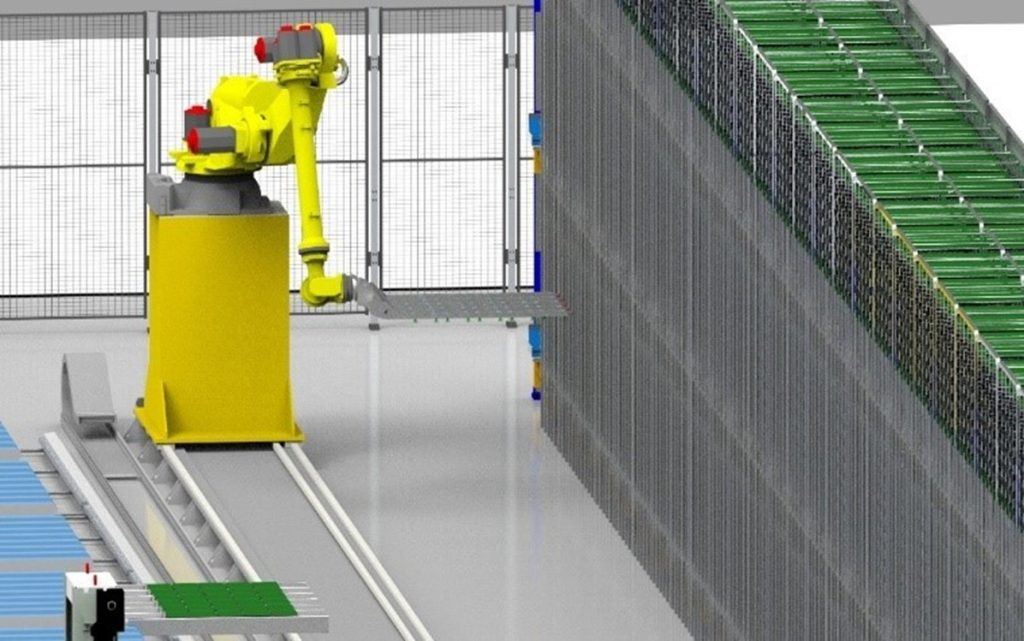
About Visual Components
Founded by a team of simulation experts and amassing over 25 years in business, Visual Components is one of the pioneers of the 3D manufacturing simulation industry. The organization is a trusted technology partner to a number of leading brands, offering machine builders, system integrators, and manufacturers a simple, quick, and cost-effective solution to design and simulate production processes and offline robot programming (OLP) technology for fast, accurate, and error-free programming of industrial robots.
Contact us today to explore how our solutions can help your business.