How EMIL SCHMID MASCHINENBAU designed a high-speed battery assembly plant with Visual Components
Facing the challenge of designing a fully automated battery assembly plant for a customer, EMIL SCHMID MASCHINENBAU turned to Visual Components. With 3D simulation and an extensive library of factory components, Visual Components helped them achieve precision and speed in designing a space-efficient production system that meets the rapid cycle times required for e-mobility battery assembly.
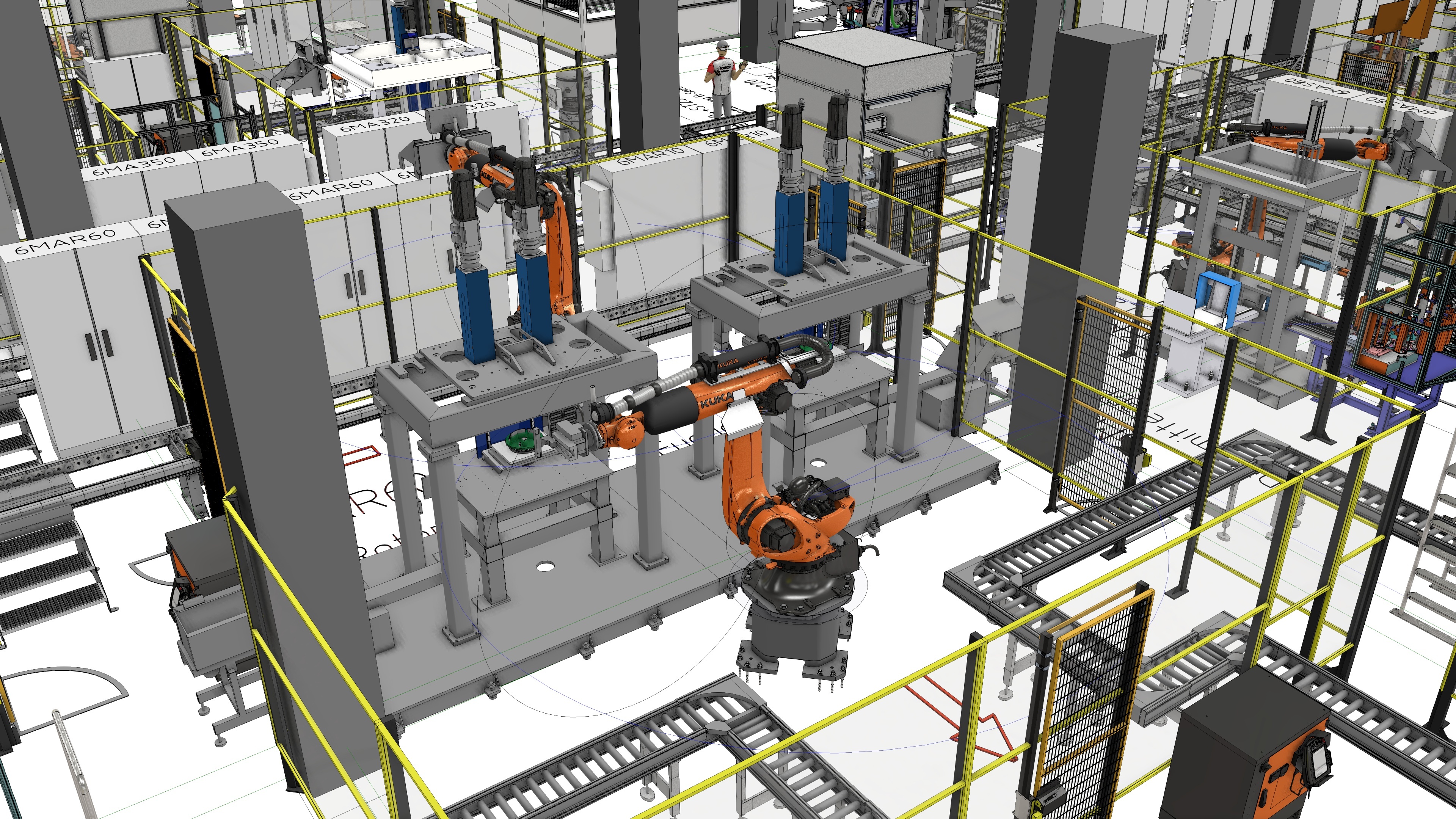
EMIL SCHMID MASCHINENBAU optimizes the production of vehicle batteries with Visual Components
Baden-Württemberg in Germany is one of the strongest economic regions in Europe. In addition to well-known international corporations, there are many medium-sized “hidden champions” in the automotive industry, in electrical engineering and in mechanical engineering. One of these companies is EMIL SCHMID MASCHINENBAU, a manufacturer of special machinery and plant equipment.
The company’s success, which has grown from a one-man shop to over 300 employees, is based on quality awareness, innovative spirit, and foresight. EMIL SCHMID MASCHINENBAU plans and builds customized production systems and special machinery for many industries, particularly the automotive industry. In recent years, innovative projects, particularly in the field of e-mobility, have become a specialty of the company.
Fully automated system for the assembly of vehicle batteries
One of EMIL SCHMID MASCHINENBAU’s most ambitious projects was building a fully automated plant to assemble cell-to-chassis vehicle batteries. Each battery contains around a thousand cells, grouped in clusters of about 100 to meet the voltage needs of electric motors. The process starts with aligning individual cells and separator layers on the assembly line. Each cell is quality-checked, glued, and stacked into clusters. The cells are then connected by welding, followed by another check. Finally, the clusters are fitted into the battery housing, along with the control electronics, resulting in a battery ready for electric vehicles.
This complex process came with unique challenges. The assembly required extreme precision and speed, with less than one second available per cell for feeding and assembly. Additionally, the limited workspace called for optimal robot placement and carefully calculated paths to avoid collisions.
Although the company has extensive experience assembling combustion engines and gearboxes, designing a system for round battery cells was a new challenge. EMIL SCHMID MASCHINENBAU needed software that could help optimize space and manage complex robot programming. After reviewing their options, they chose Visual Components for their factory planning and design.
Speeding up project planning with ready-to-use libraries
The battery cell assembly line was EMIL SCHMID MASCHINENBAU’s first major project using Visual Components. Their goal was to create a layout for battery cell assembly that maximized space and proved feasible. With Visual Components’ eCatalog, with 3000+ simulation-ready components, and their own SCHMID program library, they quickly built a detailed system model.
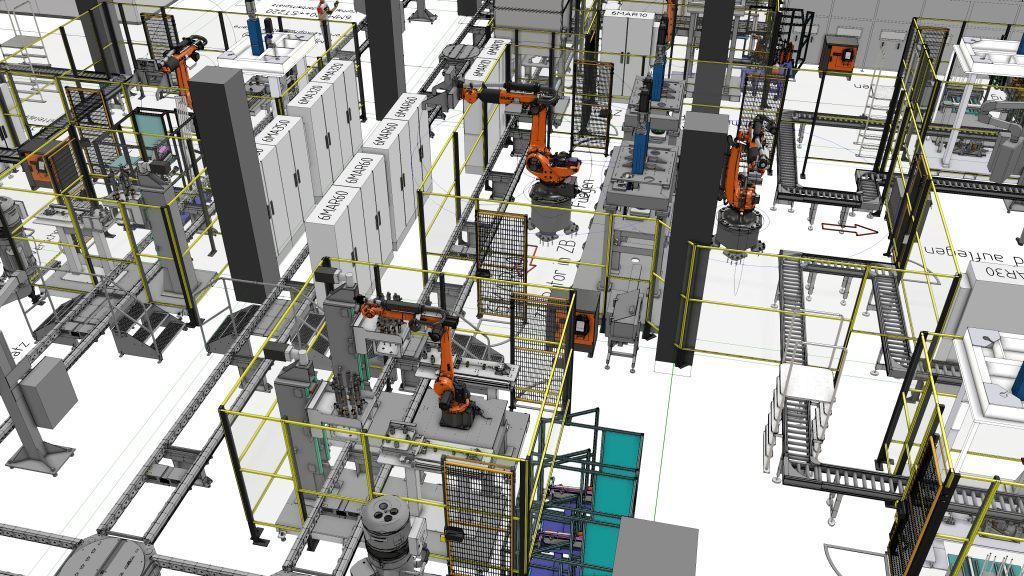
The CAD interface was invaluable, allowing them to transfer battery housing models directly into Visual Components. The geometric models of the battery housing were transferred directly from the existing CAD data into Visual Components via its CAD interface. The individual stations of the system were fully kinematized, i.e. the movements of the entire system could be simulated to optimize the cycle times of the individual stations. The software also helped with offline robot programming, reducing collision risks and ensuring they met the tight one-second-per-cell cycle time.
Reducing risk with 3D simulation
Using Visual Components to create a 3D model of the factory floor significantly lowered risks in the project’s implementation phase.
“The Visual Components library and EMIL SCHMID MASCHINENBAU’s many years of automation experience enabled us to create a meaningful concept in the shortest possible time.”
Patrick Ruoff, Sales Engineer at EMIL SCHMID MASCHINENBAU.
The software’s export options, like 3D PDFs, 2D DWG files, and virtual reality models, were also valuable. These options enabled EMIL SCHMID MASCHINENBAU to provide stakeholders with clear visual representations, making communication easier across departments.
“This allowed us to discuss everything with the customer at a much higher level of quality at an early stage of the project.”
Improving communication and teamwork
Using Visual Components significantly improved internal and external communication. The digital factory model was easily shared with all involved teams, increasing transparency and efficiency. Once the customer had approved the proposed layout, a detailed quotation was prepared using the factory model in Visual Components.
“Visual Components allows us to optimize and validate our layouts and concepts more quickly. Thanks to the various export options such as 3D PDF, 2D DWG and even virtual reality models, we can provide all departments from logistics to the customer’s operator with comprehensive information,” explains Jens Lengerer, Sales Engineer at EMIL SCHMID MASCHINENBAU.
This feature streamlined customer quotations, enhanced by visuals like 3D models, images, and videos. Presenting the factory model in this way supported the sales process and gave clients greater confidence. Showing the system concept in detail helped customers understand it clearly and make decisions more effectively.
Boosting efficiency and profitability
This project demonstrated the strong combination of EMIL SCHMID MASCHINENBAU’s engineering skills and Visual Components’ simulation capabilities. The software helped cut down the time needed for critical tasks, such as optimizing cycle times and robot ranges, making these processes quicker and more precise.
Internally, the 3D model fostered a shared understanding across departments, leading to smoother project management and higher profitability. The benefits went beyond this project, setting up the company for future success. EMIL SCHMID MASCHINENBAU plans to continue using Visual Components for layout and assembly concepts, confident in its ability to meet changing industry needs.
Aiming for ongoing innovation
Visual Components has equipped EMIL SCHMID MASCHINENBAU to meet the demands of the fast-changing e-mobility market. As the company faces new challenges, their partnership with Visual Components will remain essential to their strategy, helping them stay competitive in the custom machinery field.
In an industry where precision, speed, and innovation are crucial, EMIL SCHMID MASCHINENBAU’s use of Visual Components shows how the right technology can turn big ideas into reality. This partnership not only supports their current projects but also positions them to seize future opportunities, strengthening their reputation as an innovative leader.
About EMIL SCHMID MASCHINENBAU
EMIL SCHMID MASCHINENBAU in Baden-Württemberg, Germany, is a manufacturer of special machinery and systems that are used in various industries, mainly in the automotive sector.
Mr. Ruoff and Mr. Lengerer work at EMIL SCHMID MASCHINENBAU as sales engineers and create layouts and system concepts based on customer specifications. They also provide support for feasibility studies, system project planning and the preparation of quotations.
About Visual Components
Founded by a team of simulation experts and amassing over 20 years in business, Visual Components is one of the pioneers of the 3D manufacturing simulation industry. The organization is a trusted technology partner to a number of leading brands, offering machine builders, system integrators and manufacturers a simple, quick and cost-effective solution to design and simulate production processes and offline robot programming (OLP) technology for fast, accurate and error-free programming of industrial robots.
Want to learn more about the benefits of our solutions for your business? Contact us today!
Further reading
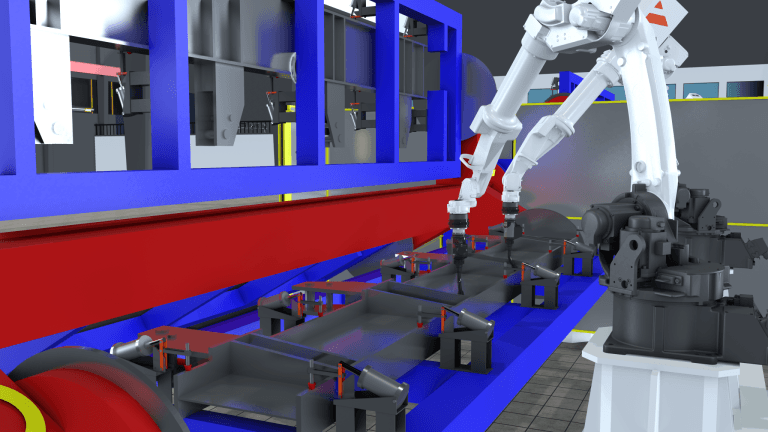
BENTELER rolls out the production technology of tomorrow with the help of Visual Components
Together with BENTELER Automobiltechnik, Karlsruhe Institute of Technology uses modern factory planning software from Visual Components to develop innovative production technologies.
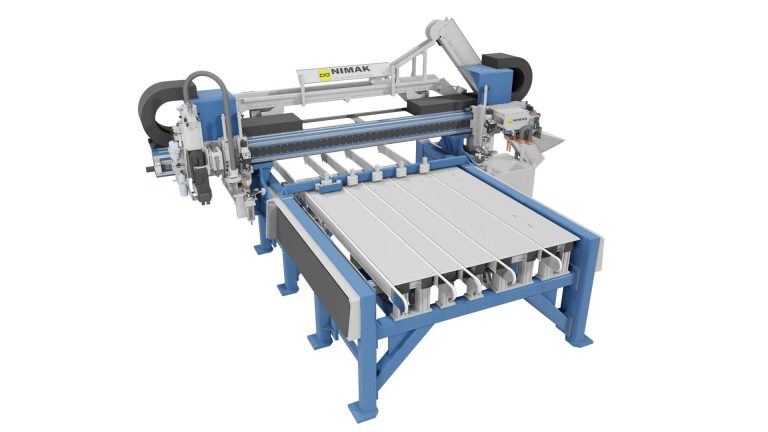
NIMAK Case Study: There Would Be No Cars Without This Company
In this case study, we’ll show you how NIMAK GmbH, the inventor of the robot welding gun and a leading manufacturer in the field of industrial joining technology, uses Visual...
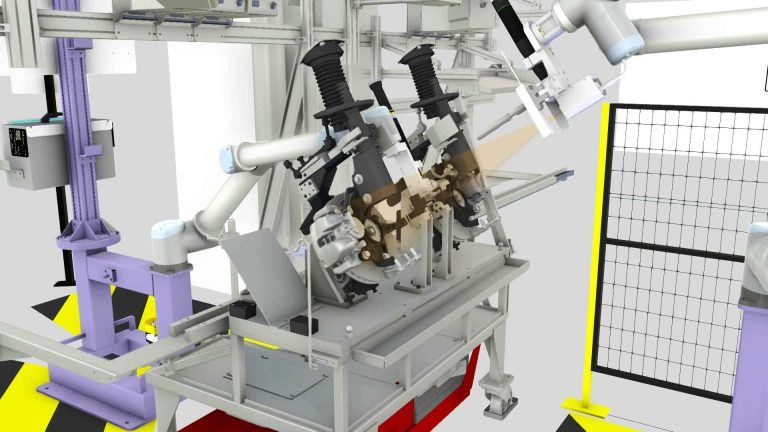
How FiRAC helped automate manual sub assembly processes in PSA Group’s plant
In this case study, we’ll show you how FiRAC, a company of Groupe SNEF that specializes in the design and integration of robotics and automation used Visual Components simulation to...