How FiRAC helped automate manual sub assembly processes in PSA Group’s plant
In this case study, we’ll show you how FiRAC, a company of Groupe SNEF that specializes in the design and integration of robotics and automation used Visual Components simulation to automate a manual sub-assembly process at a car manufacturing plant in France.
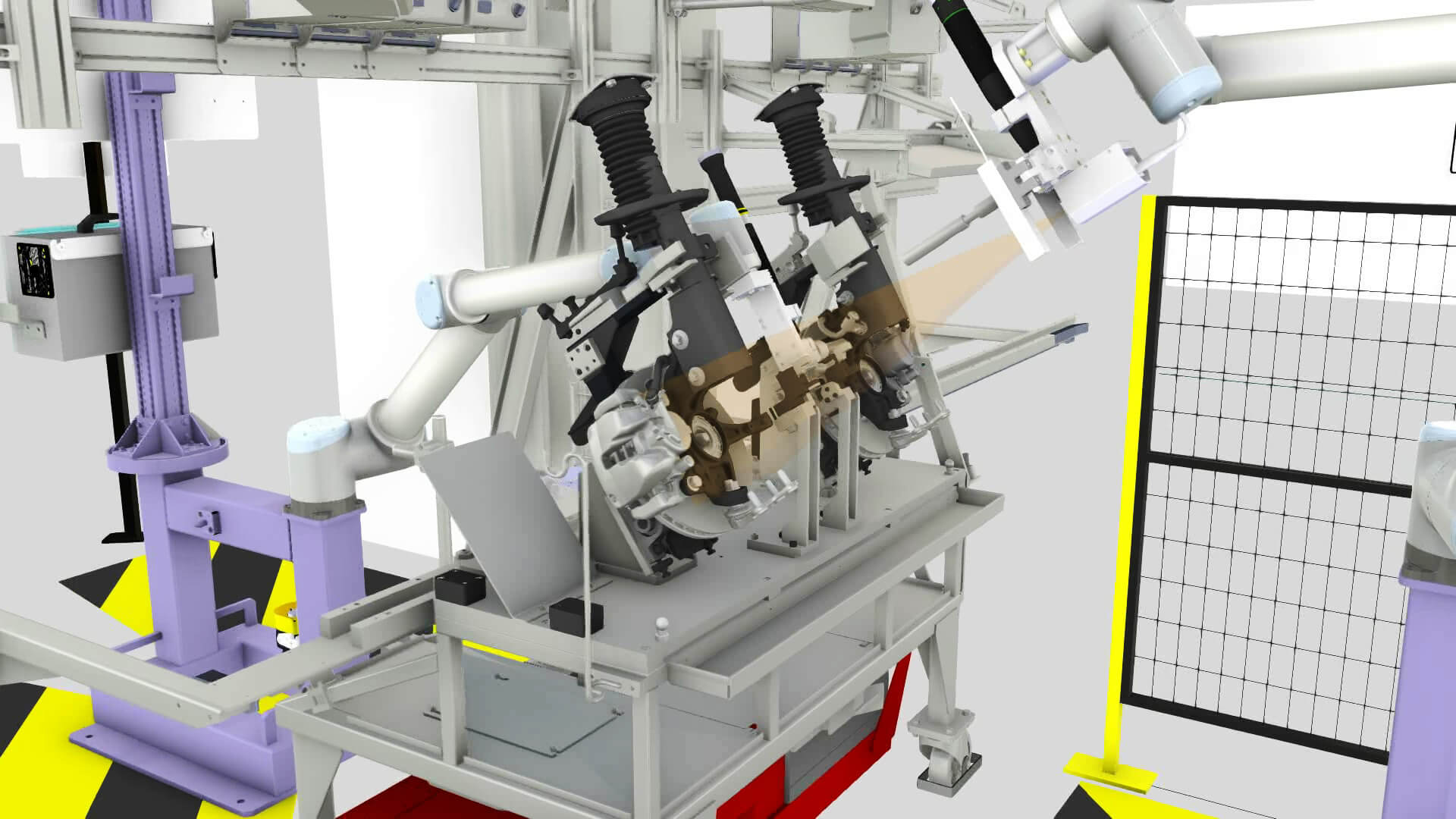
FiRAC, a company of Groupe SNEF, is a leading firm that specializes in the design and integration of robotics and automation, specifically in streamlining industrial equipment and processes with intelligent technical solutions. It often relies on Visual Components simulation technology to help show its clients just how much more efficient it can take its processes should it adopt a greater level of automation. This was the case with one of their projects with PSA Group, which produces automobiles of renowned global brands including Peugeot and Citroen. The firm was looking for a way to improve quality but keep its cycle times consistent with a specific screw tightening task on the assembly line. Utilizing Visual Components’ production simulation technology, FiRAC was able to provide an efficient solution that struck the perfect balance between cost and productivity. Here’s a closer look at how:
About the project
In automotive manufacturing, production times are vital and so is the quality. In this case, the PSA Group’s automotive manufacturing plant in Sochaux, France, was looking to optimize front-wheel screw tightening to accelerate cycle times and improve the production quality. FiRAC utilized Visual Components simulation technology to demonstrate how the process could be automated. Screw tightening at the plant was previously being performed manually, so in addition to creating an automated solution, cycle times had to remain fast and consistent to ensure overall productivity goals were met.
Specifically, this sub-assembly requires five screws to be tightened for the vehicle’s front wheels, four of the screws (M6-8 Nm) which are on the front side and one (M8-20 Nm) on the backside of the panel. This assembly was previously performed by a worker across four shifts, however, this individual’s skill level largely dictated performance cycle times, which varied from 30 to 60 seconds. The inconsistency of this task often made it challenging to stay in line with the main assembly.
“Any second lost during this process means a loss of productivity in the mainline considering a car is produced about every 60 seconds,” says Corentin Monnot, Project Manager at FiRAC.
Automating the process
FiRAC utilized Visual Components 3D manufacturing simulation to conduct a variety of scenarios to help PSA Group automate the process. Scenarios consisted of using just one robot, two robots facing the product and two robots face-to-face, among others.
The first scenario that was tested included just one robot performing the screw tightening task, which it performed in just over a minute.
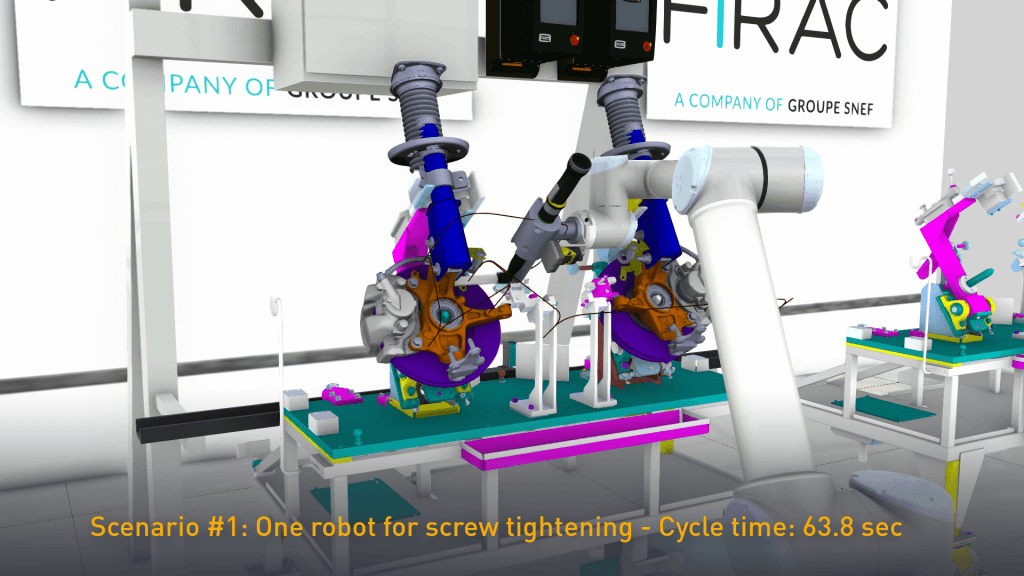
The second scenario included simulating two robots side-by-side, one that was tightening the four M6 screws and the second that was tightening the M8 screw. This cycle time clocked in at 54.8 seconds.
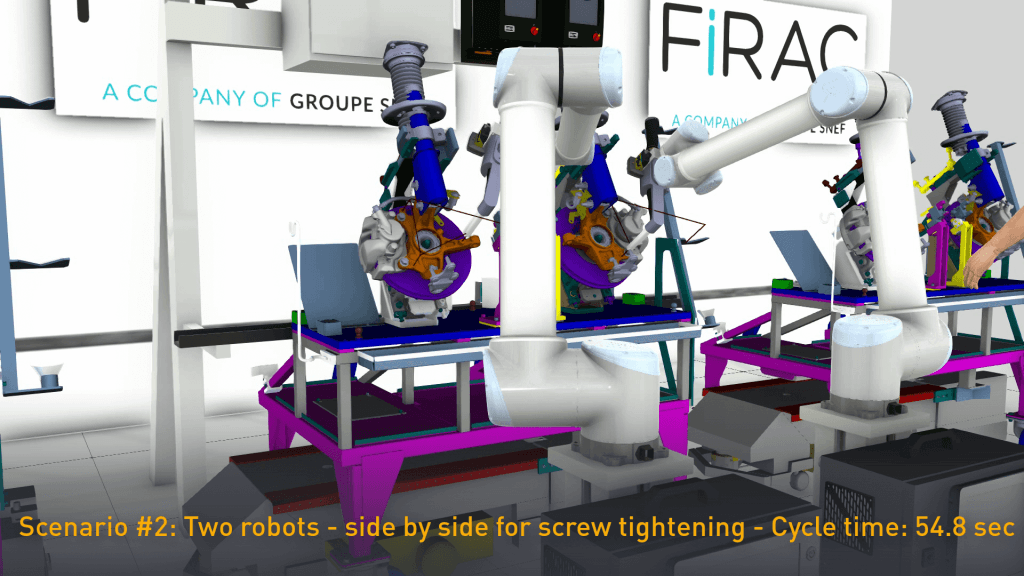
The final third scenario was designed with two robots, but in a face-to-face setup. This proved to be the most optimal solution and the fastest simulation of the process, completing the task in under 53 seconds. This was the simulation that was accepted by PSA Group, as it proved to be the ideal compromise between cost and performance.
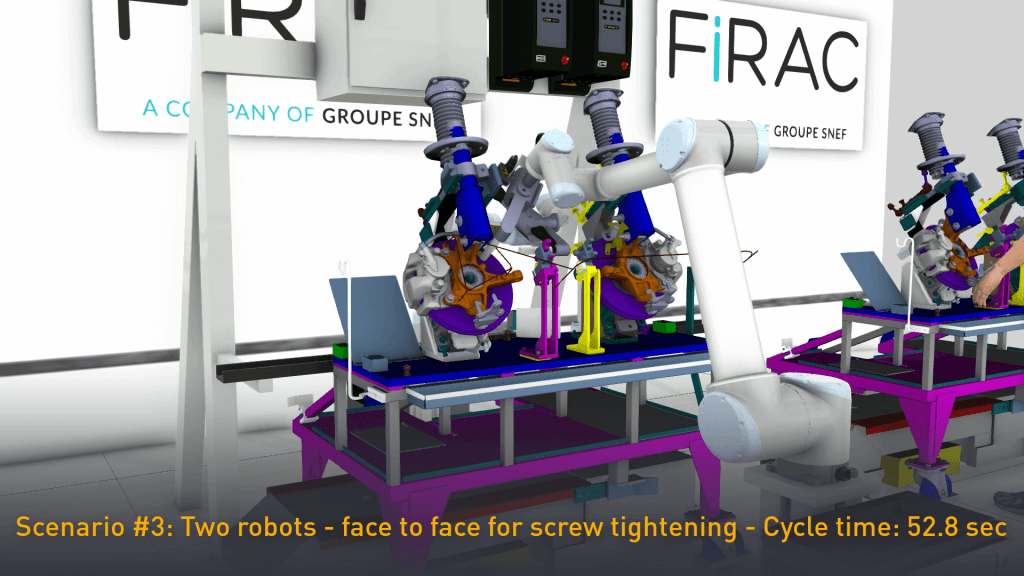
“Visual Components is so versatile that it was very easy to implement the different configurations and view their effect on the cycle time,” says Corentin Monnot, Project Manager at FiRAC. “Once we found the best simulation, we were able to edit a video of the process and provide quantified and visual reasoning to support our final solution.”
Visual Components is so versatile that it was very easy to implement the different configurations and view their effect on the cycle time. Once we found the best simulation, we were able to edit a video of the process and provide quantified and visual reasoning to support our final solution.
Corentin Monnot, Project Manager at FiRAC
The Visual Components advantage
FiRAC competitors that were also consulted for this project insisted that the process could be automated using only one robot. However, these competing firms failed to show any visualization to truly demonstrate how it could be done quickly and efficiently.
In addition to the visual representation of the process, Visual Components allowed FiRAC to consider multiple external time-consuming factors and anticipate their effect. Thus, the AGV moving time, the screw tightening time, or even the camera process time were taken into account very early stage, therefore providing a strong engineering background to the proposal.
That was one of the big advantages of using the Visual Components software that the visualized and validated proposal could be effectively communicated to PSA Group.
Visual Components also helped FiRAC solve optimization challenges with the robots so it could better understand and design the best way to reach the client’s desired cycle times. For example, in the simulation where both robots were positioned on the same side, one robot would have to wait for several seconds for the other to finish its task before it could begin its respective task. In some simulations, the two robots would collide with one another, further stalling the process. It’s part of the reason why the two robots in face-to-face positioning proved to be the most efficient solution.
“With simulation, it was clearly demonstrated why it was impossible to fit the process in the required cycle time with only one robot,” said Corentin Monnot, Project Manager at FiRAC. “The customer was really impressed with the visual implementation of the process – and that’s how FiRAC got the competitive edge to win this project.”
And Visual Components role didn’t stop after FiRAC won the job. After the project was awarded, FiRAC continued to utilize the technology to validate the mechanical design of all the elements to ensure accessibility, proper clearance and factory implementation. The solution was implemented within about 6 months, with FiRAC spending a few months on-site to fully test and integrate the solution on the shop floor.
The customer was really impressed with the visual implementation of the process – and that’s how FiRAC got the competitive edge to win this project.
Corentin Monnot, Project Manager at FiRAC
Project facts
Project Timeline | October 2018: RFQ received October 2018 (2 weeks, not spent 100% on simulation): Pre-study November 2018 – May 2019: Technical reframing and negotiations May 2019: Project Awarded July 2019: Design Acceptance September 2019: Factory Acceptance Testing (FAT) October 2019: Commissioning / Site Acceptance Testing (SAT) December 2019: End of ramp-up, final acceptance |
Industry | Automotive – Manufacturing |
Project | Automating a manual sub-assembly process in a car manufacturing plant |
Customer | PSA Group |
Location | Sochaux, France |
System Integrator | FiRAC |
Contact | Corentin Monnot, Project Manager at FiRAC |
Further reading
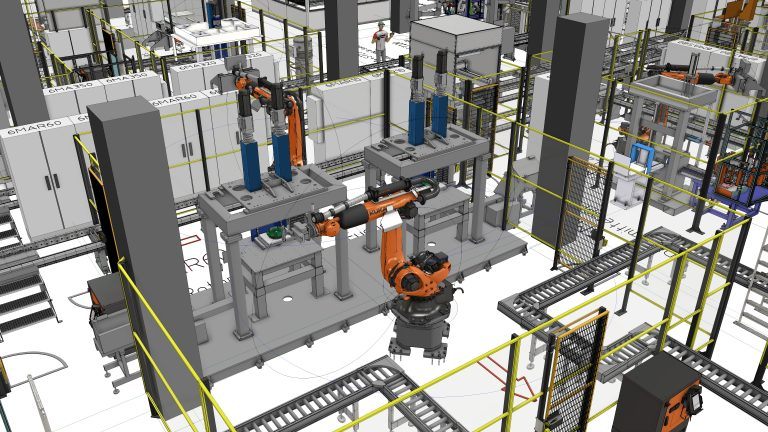
How EMIL SCHMID MASCHINENBAU designed a high-speed battery assembly plant with Visual Components
Facing the challenge of designing a fully automated battery assembly plant for a customer, EMIL SCHMID MASCHINENBAU turned to Visual Components. With 3D simulation and an extensive library of factory...
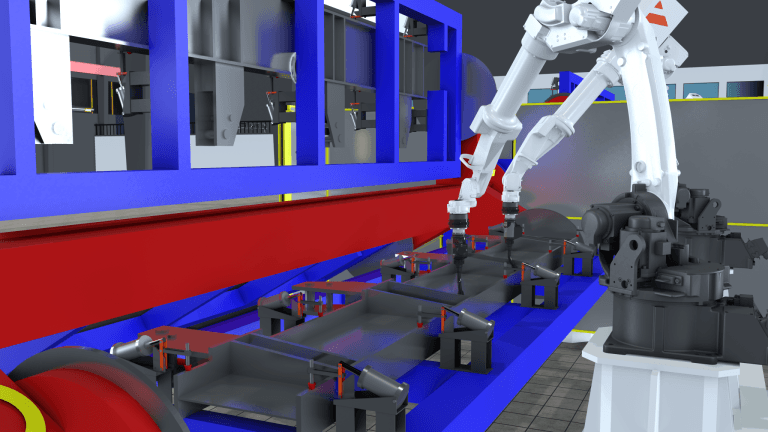
BENTELER rolls out the production technology of tomorrow with the help of Visual Components
Together with BENTELER Automobiltechnik, Karlsruhe Institute of Technology uses modern factory planning software from Visual Components to develop innovative production technologies.
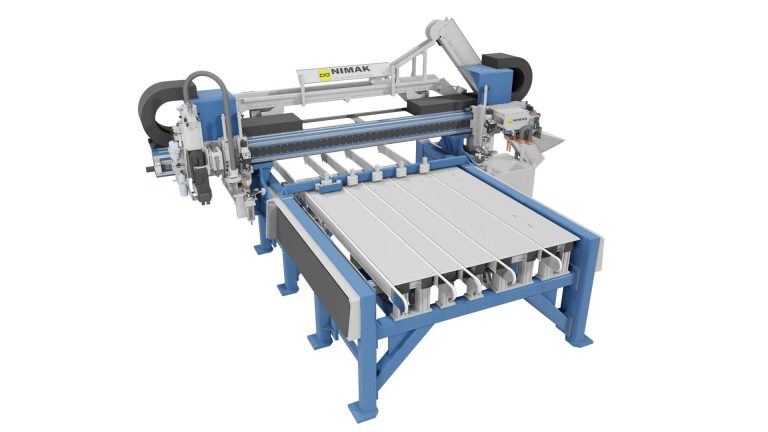
NIMAK Case Study: There Would Be No Cars Without This Company
In this case study, we’ll show you how NIMAK GmbH, the inventor of the robot welding gun and a leading manufacturer in the field of industrial joining technology, uses Visual...