FFG Feeler Case Study
Discover how FFG Feeler creates effective layouts for their clients with the help of Visual Components.
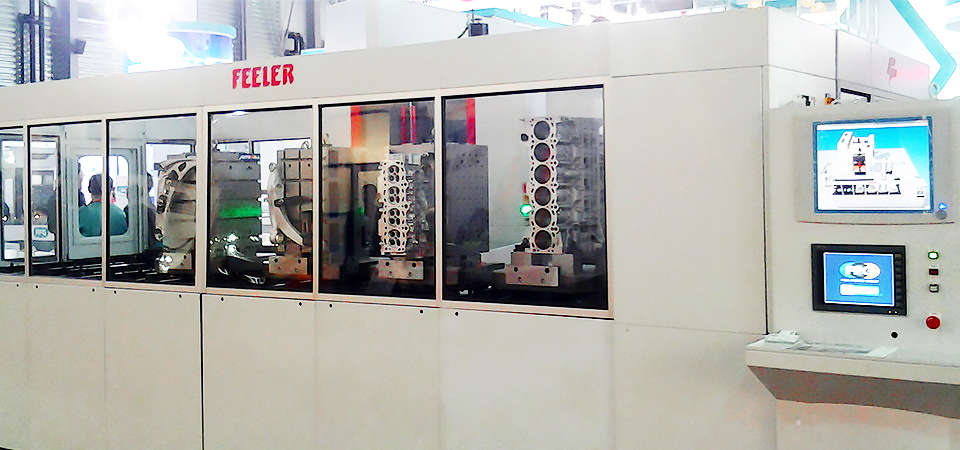
The challenge of communicating your vision
In today’s business environment, it’s not enough to just have a great idea or a coherent solution. You also need to be able to communicate them clearly. For machine builders, being able to demonstrate the future manufacturing system or cell for a customer in a captivating 3D simulation is often the beginning of a successful customer relationship.
FFG Feeler is one of the several companies already utilizing 3D simulations in their work. Meng-Shen Chen, Assistant Manager of the Taichung, Taiwan based company gave us his views on why and how they’ve moved from drawing 2D layouts to simulating their machines in 3D.
The main benefits of using Visual Components software for sales and planning purposes have been clear:
Easier communication. Better visualizations.
Meng-Shen Chen, Assistant Manager, FFG Feeler
Gaining an edge over your competitors
Chen also states that their choice of switching to 3D simulation has undoubtedly given Feeler competitive advantage in the market. Not only is creating the layouts faster in 3D, but the clarity in presentation also simplifies the customers’ evaluation work.
Having a 3D PDF or video at their disposal means that customers now spend less time evaluating proposals and their response has been highly positive.
“We get much faster responses from our customers. Also the customers trust us more as they are able to see their layout in operation,” Chen elaborates.

Besides being able to demonstrate their ideas more clearly, the software has also helped Feeler validate their programmable logic controllers (PLC’s) before the actual commissioning of a facility. This has decreased ramp-up times considerably.
Visual Components has a global network of resellers, which has also benefited Feeler as they’ve been collaborating with their regional Visual Components reseller CMS. According to Chen, their help in resolving open questions and providing project services has been vital in their adoption of the Visual Components software.
We get much faster responses from our customers. Also the customers trust us more as they are able to see their layout in operation.
Meng-Shen Chen, Assistant Manager, FFG Feeler
On a recent exhibition they set up a FMS system with an integrated Real PLC MITSUBISHI MELSEC controller. The FMS system was simultaneously visualized with an integrated simulation of Visual Components.
Not only has CMS created our complete customized simulation models, they have also trained our personnel and have an open ear for all questions from our side.
Meng-Shen Chen, Assistant Manager, FFG Feeler
Further reading
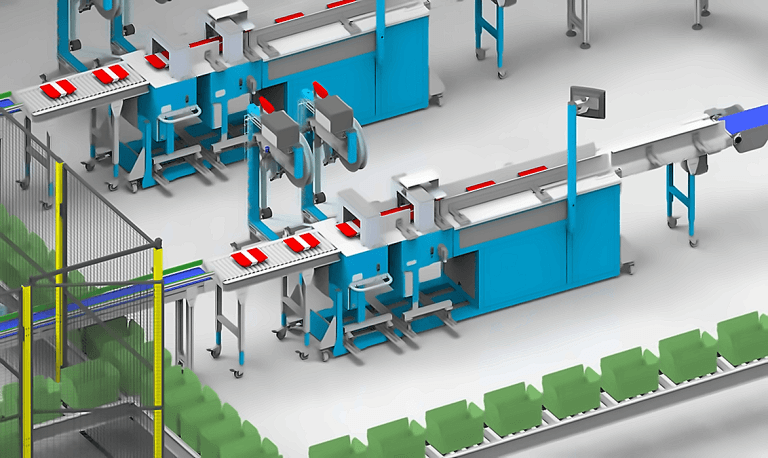
How Hollander Techniek designed an automated custom meal packaging system with Visual Components
When Uitgekookt set out to automate its meal packaging process, they needed a system that could handle custom orders with speed and precision. Hollander Techniek used Visual Components to design...
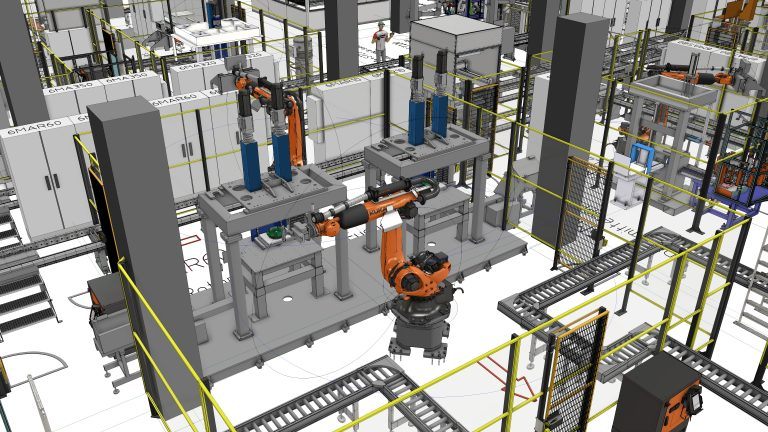
How EMIL SCHMID MASCHINENBAU designed a high-speed battery assembly plant with Visual Components
Facing the challenge of designing a fully automated battery assembly plant for a customer, EMIL SCHMID MASCHINENBAU turned to Visual Components. With 3D simulation and an extensive library of factory...
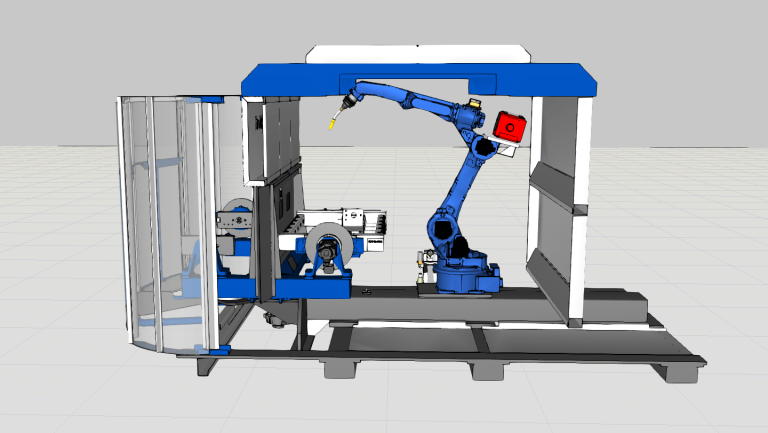
Maximizing efficiency and ROI from day 1: Duun Industrier pre-programs a welding robot cell with Visual Components OLP
Duun Industrier, a leading Norwegian heavy machinery manufacturer, installed the Nordics’ largest robotic welding station in 2013. Utilizing Visual Components for robot programming since 2014, they commissioned a new robot...