BENTELER rolls out the production technology of tomorrow with the help of Visual Components
Together with BENTELER Automobiltechnik, Karlsruhe Institute of Technology uses modern factory planning software from Visual Components to develop innovative production technologies.
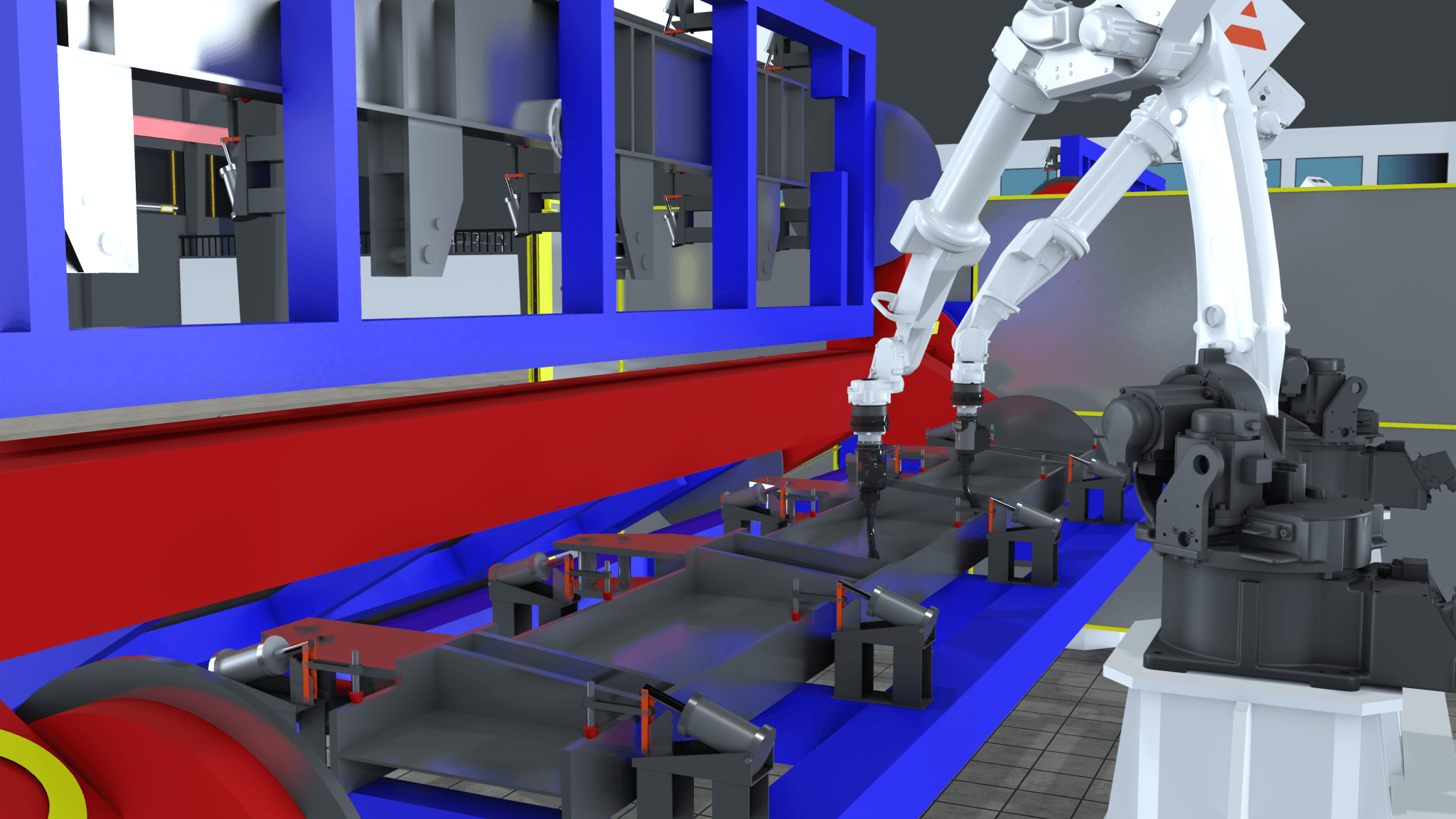
Karlsruhe Institute of Technology (KIT) is a technical university in Baden-Württemberg, Germany, and the largest German research institution. KIT was established in 2009 as a merger of Technical University of Karlsruhe with the former Karlsruhe Nuclear Research Center. In various university rankings, KIT is listed as the leading German university in terms of research in engineering and natural sciences.
The Institute of Production Science at KIT focuses on application-oriented research of the production of tomorrow: from global, resilient production networks to the breathing factory with highly productive plants and innovative business models to quality assurance. Specifically, practical tools are developed for industry, which are then translated into entrepreneurial success.
BENTELER Group, a metal process specialist, produces safety-relevant products, systems, and services for the automotive, energy, and machinery industries worldwide.
BENTELER Automotive is a development partner of leading automotive manufacturers. With 19,000 employees and around 70 plants in over 20 countries, the division develops customized solutions: Components and modules for chassis, body, engine, and exhaust systems as well as innovative solutions for electric vehicles.
Automatic assembly and welding of a car axle from sheet metal parts
As part of a research project, an assembly line from BENTELER Automotive was to be analyzed. In this assembly line, a passenger car axle is assembled from sheet metal parts. The production of the sheet metal parts, i.e., pressing and punching, is not considered here; the focus is solely on the assembly and welding of the sheet metal parts.
The assembly line consists of 5 welding cells and one cell for laser cutting. The cells are connected by handling robots; the line also includes the supply of the sheet metal parts and the removal of the final product.
In each welding cell, a different number of sheet metal parts are welded into an assembly. This intermediate product is transferred to the following cell and then welded with further components to form a new assembly. With the help of rotary tables, processing, loading, and unloading partly take place simultaneously.
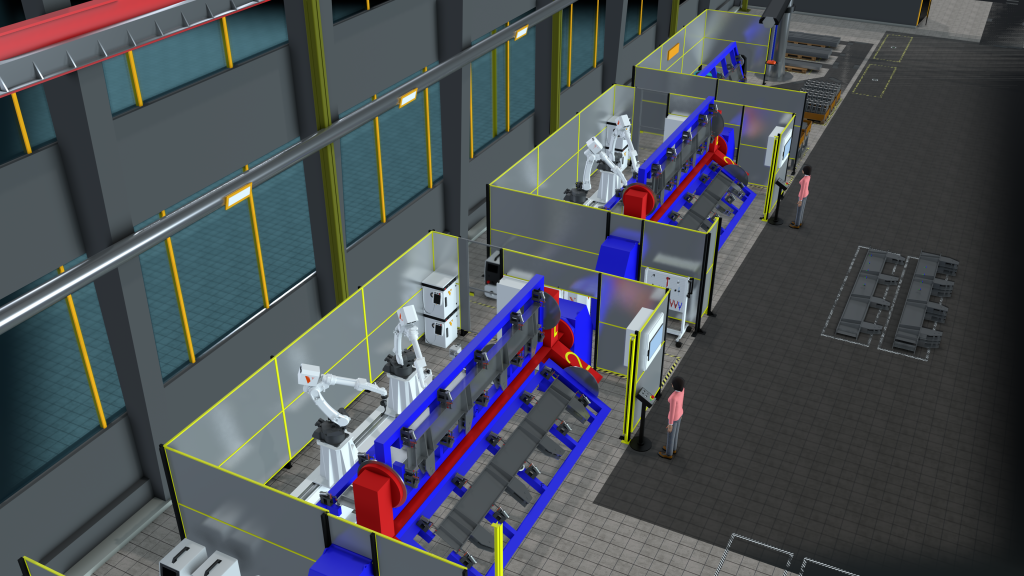
Assembly lines of such complexity cannot be planned manually
When planning such an assembly line, numerous requirements must be considered. The rotary tables and handling robots must be arranged in such a way that optimum accessibility is ensured, i.e., that the distances and thus the cycle times are as short as possible. Collisions must be avoided at all times. In addition, the processes must be coordinated in such a way that processing and loading/unloading can be carried out in parallel. Finally, the welding line must be supplied with the sheet metal parts and the end products must be removed.
In the past, such assembly lines were planned manually and with the help of Excel spreadsheets. However, such complex production systems cannot be modified or adapted in a short time; moreover, a realistic representation of the assembly line and its processes is missing.
To enable more precise planning of production systems and to reduce the time-to-market, it is necessary to use modern software for factory planning and simulation. The Institute of Production Science has chosen Visual Components for this purpose.
Professional software for factory planning and simulation
At Visual Components, we are proud to be recognized as one of the world’s leading providers of 3D factory design and simulation solutions. Our software includes an extensive library of predefined factory components, empowering planners to design, plan, and simulate production facilities efficiently. Users can create digital twins of everything from individual machines and production lines to entire factories. These digital twins are essential tools that facilitate meticulous planning, optimize production processes, and enable virtual commissioning, ensuring that our customers are well-prepared for real-world implementation.
Based in Espoo, Finland, our solutions have a global footprint and are utilized across a diverse range of industries, including industrial machinery, automotive, packaging, and logistics. Our software is available in various versions that cater not only to large corporations but also to smaller enterprises through both purchase and rental options. This flexibility helps businesses of all sizes leverage our advanced simulation capabilities.
Furthermore, we offer particularly attractive conditions for educational institutions, supporting the next generation of engineers and industry professionals in gaining hands-on experience with industry-leading simulation technology.
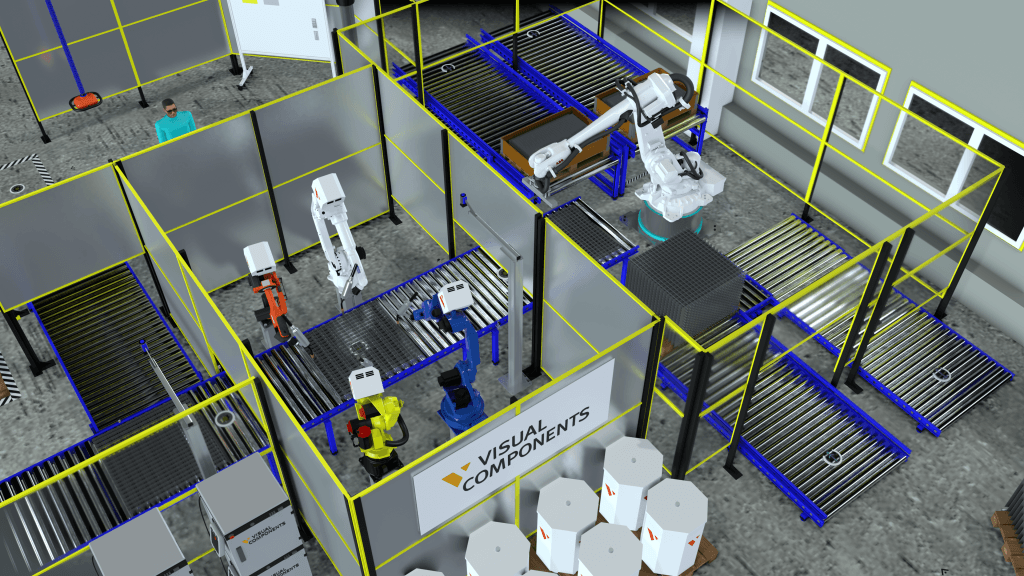
Numerous CAD interfaces and a comprehensive catalog of factory components
The models of the components to be welded can be imported into Visual Components in native CAD format or as JT or STEP files. The data of numerous robots from all leading manufacturers, including detailed kinematics, are available in the library, the eCatalog of Visual Components. In total, our eCatalog contains more than 3,000 predefined components, such as machines, conveyors, and racks which can be used out-of-the-box to create factory models. If a component should not be available in the eCatalog, e.g., a special robot gripper, it can simply be modeled in Visual Components, including its kinematic properties, and then used by any robot.
Visual Components very accurately represents the components and processes, including all details. BENTELER Automotive is enthusiastic about the many possibilities that Visual Components offers for factory planning.
Mr. Louis Schäfer, M.Sc., academic assistant at the Institute of Production Science
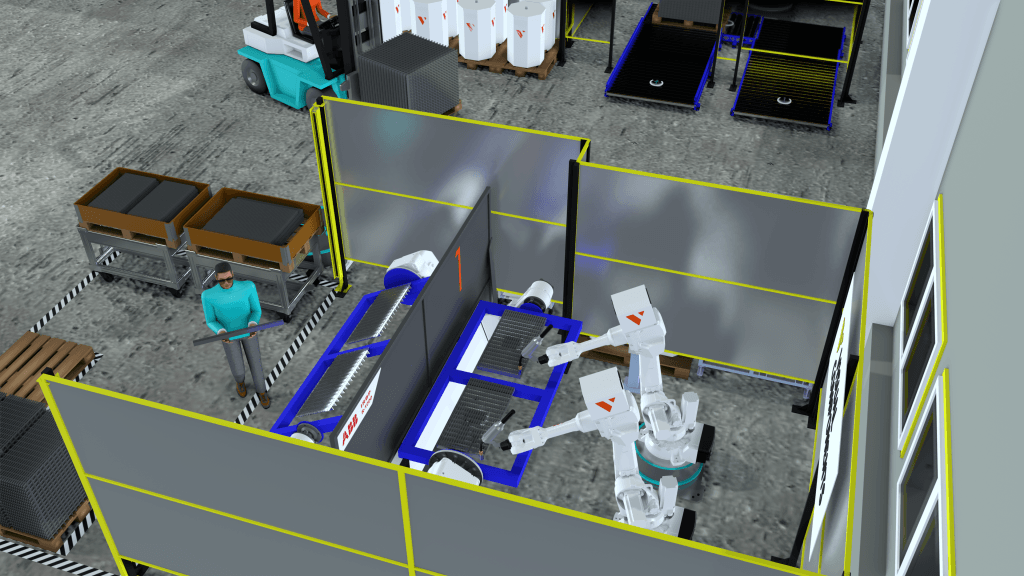
The stations can be linked as desired by simple drag-and-drop
All stations of the welding system were set up in Visual Components. The modular structure facilitates future modifications because new concepts of the welding system can easily be set up and quickly tested and optimized via simulation. It is also possible to extend the model into a digital twin after the physical welding line has been built. Such a digital twin behaves exactly like the real system. A digital twin saves a lot of time and costs in development, optimization, and commissioning.
Validation of robot programs in terms of reachability and axis values
According to Mr. Schäfer, the Institute of Production Science also intends to use Visual Components for the validation of robot programs in terms of reachability and axis values. The modularization allows new versions of the production line to be set up accurately in a short time. Other problems can also be solved via simulation, e.g., the identification of bottlenecks in the production flow or the evaluation of differences between automatic and manual handling. A digital twin is also being considered, i.e., the integration of real process data into the model.
In summary, Mr. Schäfer states that Visual Components offers enormous potential for a wide variety of simulation-related tasks. The user-friendly system allows a detailed analysis, as one can represent even very complex issues. In addition, working with Visual Components is a lot of fun. The user forum provides a lot of support: In case of questions, helpful solutions are quickly provided by the large user community.
About Visual Components
Founded by a team of simulation experts and amassing over 20 years in business, Visual Components is one of the pioneers of the 3D manufacturing simulation industry. The organization is a trusted technology partner to a number of leading brands, offering machine builders, system integrators, and manufacturers a simple, quick, and cost-effective solution to design and simulate production processes and offline robot programming (OLP) technology for fast, accurate, and error-free programming of industrial robots.
Want to learn more about the benefits of our solutions for your business? Contact us today!
Further reading
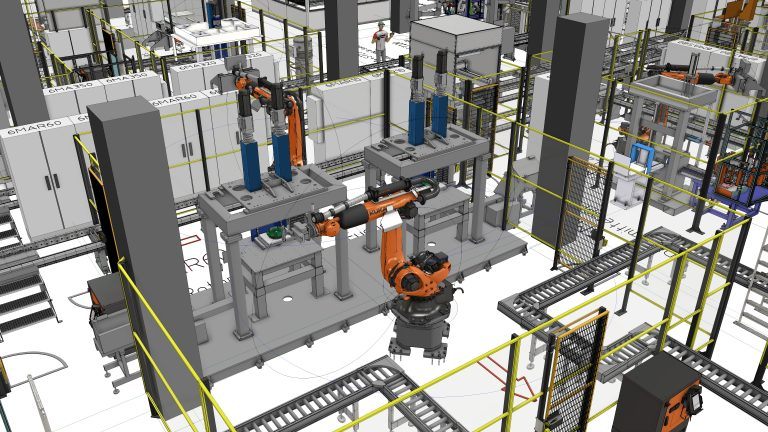
How EMIL SCHMID MASCHINENBAU designed a high-speed battery assembly plant with Visual Components
Facing the challenge of designing a fully automated battery assembly plant for a customer, EMIL SCHMID MASCHINENBAU turned to Visual Components. With 3D simulation and an extensive library of factory...
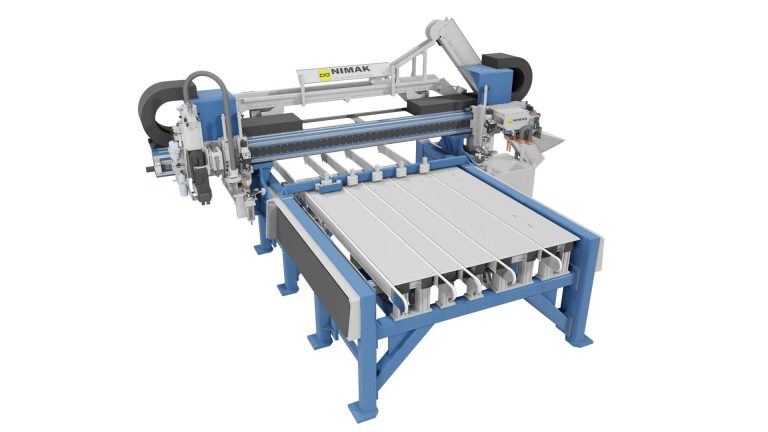
NIMAK Case Study: There Would Be No Cars Without This Company
In this case study, we’ll show you how NIMAK GmbH, the inventor of the robot welding gun and a leading manufacturer in the field of industrial joining technology, uses Visual...
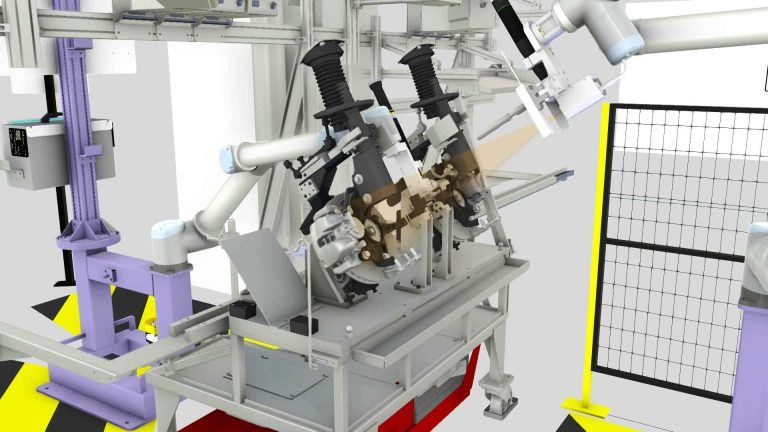
How FiRAC helped automate manual sub assembly processes in PSA Group’s plant
In this case study, we’ll show you how FiRAC, a company of Groupe SNEF that specializes in the design and integration of robotics and automation used Visual Components simulation to...