AFRIT production runs faster than ever, thanks to Visual Components Robotics OLP
Read how a trailer manufacturer from South Africa improved the manufacturing efficiency by using Delfoi Robotics Offline Robot Programming solution (Now known as Visual Components Robotics OLP).
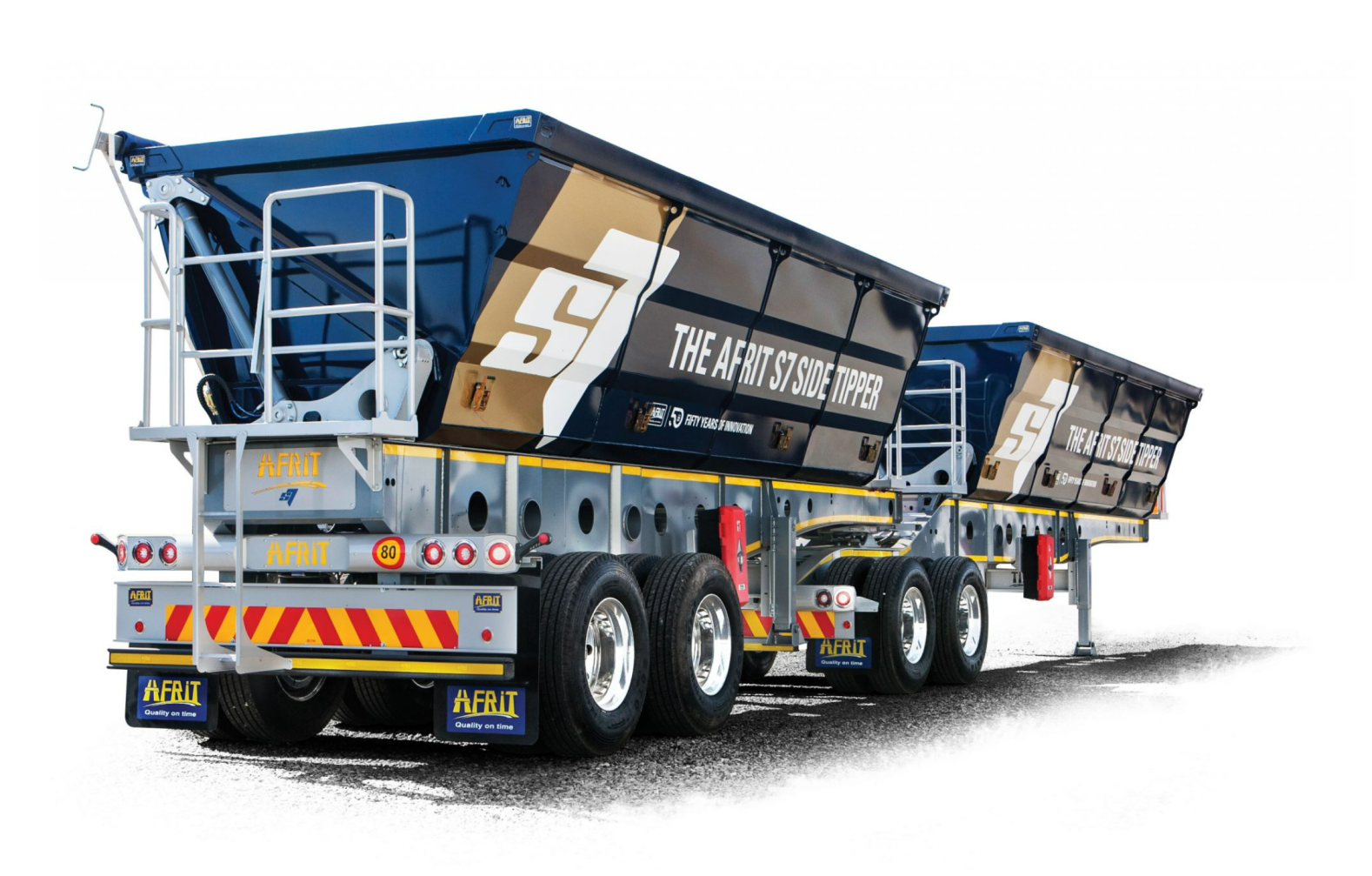
AFRIT is one of the most respected and innovative trailer manufacturers in South Africa. Key to the success of AFRIT has been the pledge and commitment by management, employees, and partners to live by the AFRIT promise that has earned the trust and respect of clients since 1968: Quality on time. In order to stay on top of the digitalization trends and ensure the quality on time promise in the years going forward, Afrit decided to take Visual Components offline programming (formerly Delfoi) and simulation solution in use. Since offline programming has been in use, there have been significant benefits in production. Ferdi Beukes, Mechatronic Engineer at Afrit has been very happy about the improvements:
Since the implementation of Delfoi Robotics (now Visual Components Robotics OLP), our parts are more consistent as well as the repeatability of welding has improved significantly. We have more time improving welding and other systems because of the time saved by not needing to do manual programming and touch ups on the programming. Delfoi Arc has proven to be a very versatile software, our robot systems have seam tracking functionality, Delfoi was able to implement the macros for the seam tracking. With the assistance of Delfoi Robotics’ counterpart Apexiz the commissioning could be done with great precision,
Ferdi Beukes, Mechatronic Engineer at Afrit
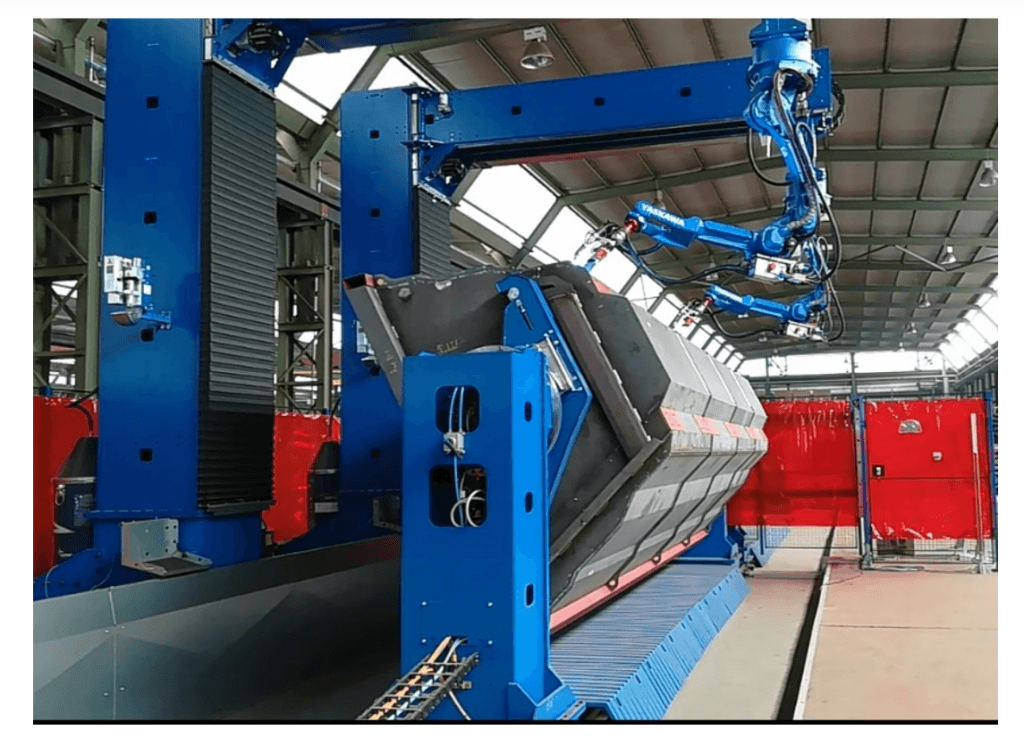
Delfoi’s robot offline programming has improved the quality furthermore and streamlined the processes. Time savings have been significant though the software has been in use only a relatively short time.
Our engineers say that manual programming man work hours have been reduced by 80% and programming time reduced by 60%, from two weeks manual to four days offline, and we have increased our output of 8 bins a day to between 16 and 20 bins a day.
Gerhard van der Walt, Continuous Improvement Manager at Afrit
Examples of improvements:
• Manual programming man work hours reduced by 80%
• Programming time reduced by 60% (from 2 weeks manual to 4 days offline)
• Production lead time improved by 62% for not being required to do manual programming
• Number of parts lost by manual programming reduced from 60 to 0 (each part consists of ±120m of welding)
Commissioning and calibration of this AFRIT’s robotic cell were done by Delfoi Robotics’ partner in India, APEXIZ.
We are sure that the programming time will be further reduced after they get more experienced. Features such as cloning, multi-layer, automatic axes optimization, vision system integration, templates and weld databases allows the users to increase their productivity enormously, especially in big systems such as AFRIT’s. For us it is very important that the user is confident to copy and run the programs created offline without any touch-up and we are able to achieve it using Delfoi Arc
Hari Nidamarthy, the founder of APEXIZ
About AFRIT
AFRIT is one of the most respected and innovative trailer manufacturers in Africa. With more than 50 years of experience in the industry and a product built on a constant drive for optimization and innovation, they remain the number one choice for customers who are looking for a more efficient payload and a high return on investment.
About APEXIZ
APEXIZ offers digital manufacturing solutions such as 3D simulation and robot offline programming. APEXIZ and its partner companies have many years of experience in developing simulation and robot offline programming software.
About Delfoi Robotics
Delfoi Robotics is a pioneer company and trailblazer in offline robot programming worldwide and a world-class expert in production simulation and production scheduling and execution. As of October 2022, Delfoi Robotics is a part of the Visual Components Group.
Further reading
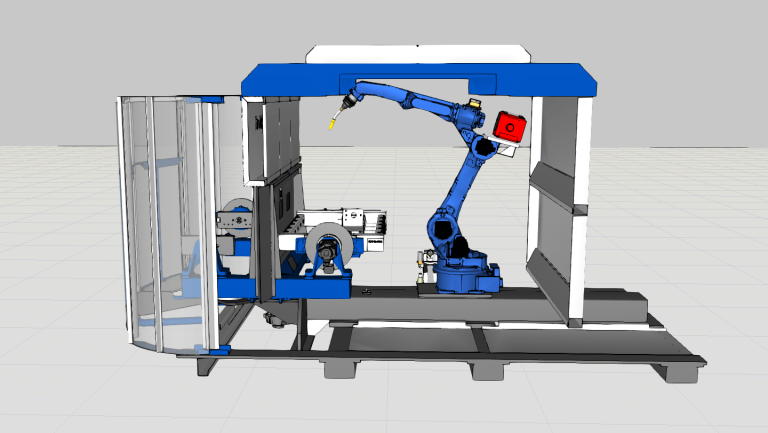
Maximizing efficiency and ROI from day 1: Duun Industrier pre-programs a welding robot cell with Visual Components OLP
Duun Industrier, a leading Norwegian heavy machinery manufacturer, installed the Nordics’ largest robotic welding station in 2013. Utilizing Visual Components for robot programming since 2014, they commissioned a new robot...
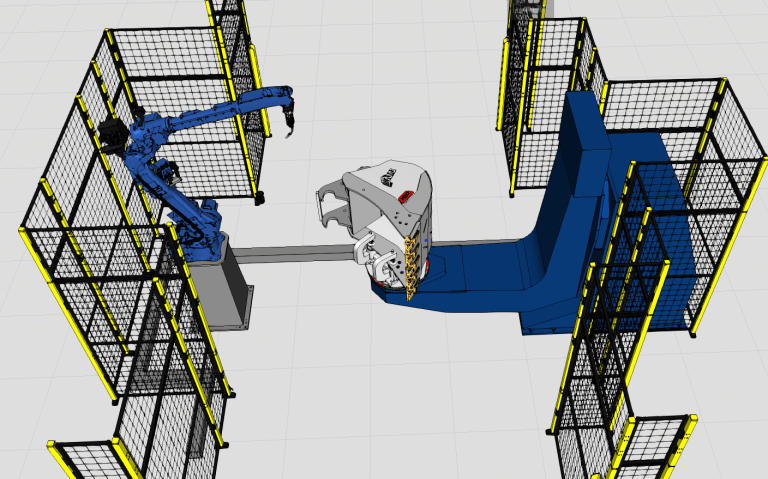
Combatting the welder shortage: how AMI Attachments enhances production efficiency with Visual Components OLP
AMI Attachments, a leading North American manufacturer of heavy equipment attachments, sought to improve product throughput and meet evolving market demands while navigating a welder shortage. By implementing Visual Components...
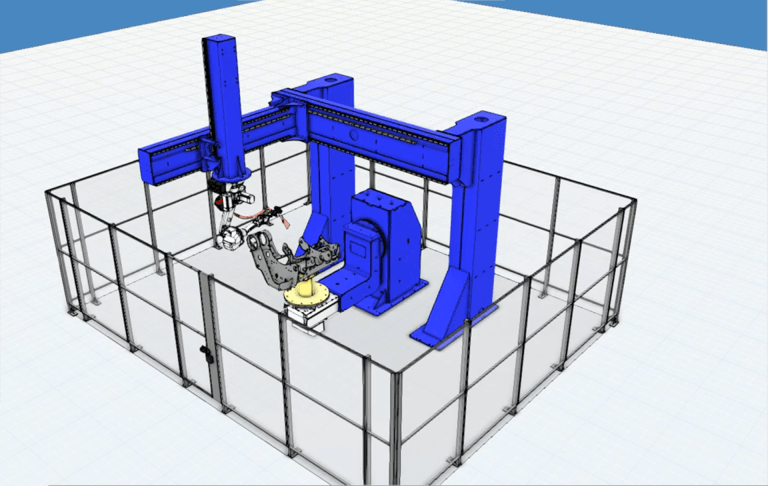
Ponsse is driving forest machine innovation and improving productivity with Visual Components Robotics OLP
Ponsse Plc., a global leader in forest machine manufacturing, has transformed its production process by leveraging Visual Components Robotics OLP.