Understanding digital twins in manufacturing
Digital twins go far beyond static models or simulations. They bridge the gap between virtual and physical systems, offering real-time insights and control. But with so many definitions floating around, it’s easy to see why there’s confusion. This article breaks down what digital twins really are, how they’re being used in manufacturing today, and why they’re set to play a bigger role in the future.
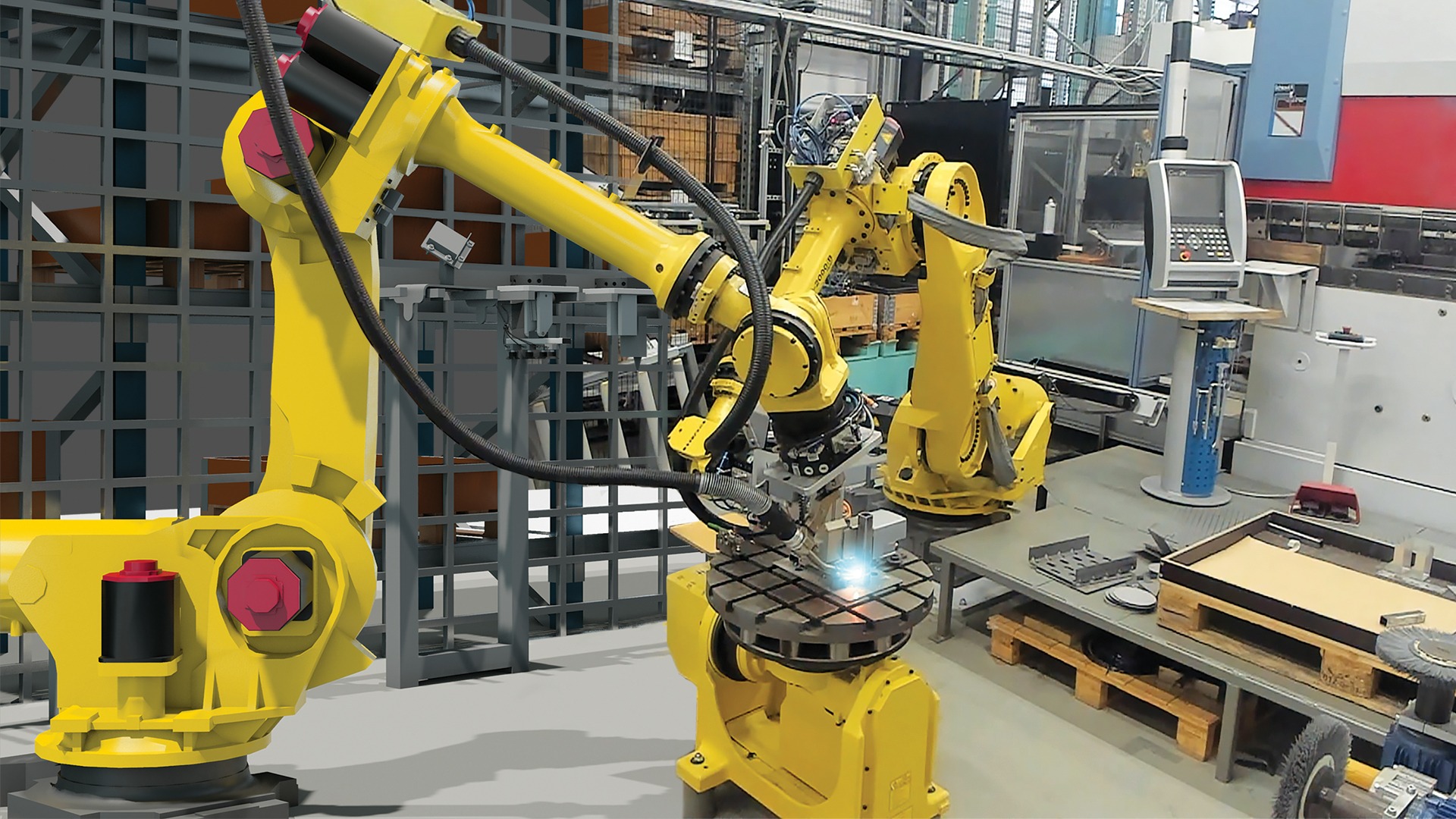
Understanding digital twins in manufacturing
What’s a digital twin and what’s not
Digital twins are one of the most talked-about technology trends in manufacturing, but what are they, and what do they actually do? Are they just advanced 3D models, or do they have the potential to fundamentally reshape manufacturing?
At Visual Components, we’ve heard all kinds of things when it comes to digital twins. As a strong platform in manufacturing simulation, robot offline programming, and digital twin use cases, we feel informed enough to give our two cents on what they are, how they can be used best, and why simulation might be a good place to start.
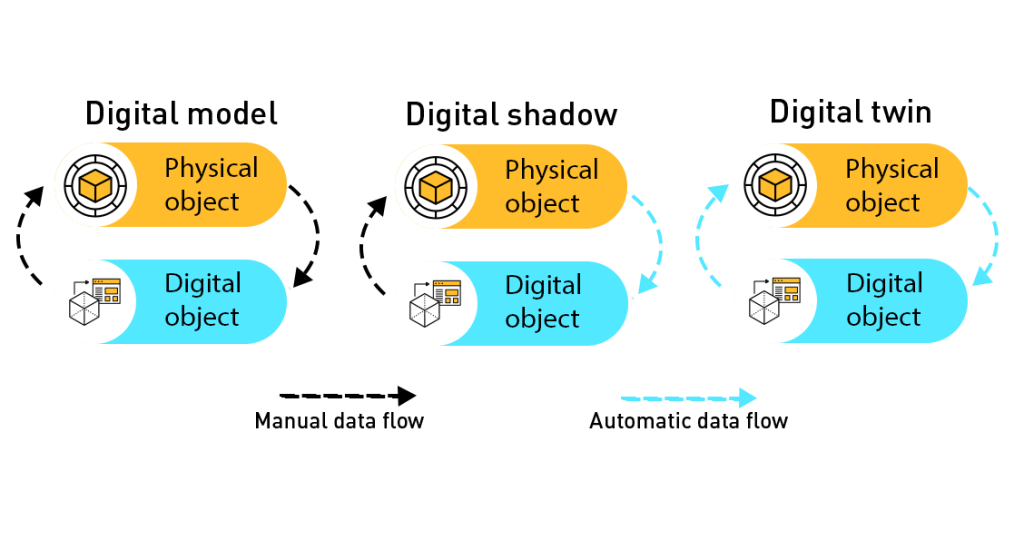
When talking about digital twins, we have to start by clearing up some common misconceptions. People might often find that they hear the term “digital twin” used interchangeably with things like advanced digital models and digital shadows, but they’re not the same thing, there are some key differences.
A digital model is a 3D representation of a product, system, or factory layout. It can be static or a simulation, but it is not connected to real-world production data or interactions in any shape or form.
A digital shadow is a virtual model that automatically receives real-time data from its physical counterpart. This one-way data flow keeps it up to date for monitoring and analysis, but it doesn’t influence or control the physical system.
A digital twin is a real-time digital counterpart of a physical system that continuously exchanges data in both directions. This dynamic connection allows manufacturers to monitor performance, predict issues, and optimize processes based on live data.
Now that we’ve clarified what a digital twin is—and what it isn’t—let’s look at how manufacturers are putting this technology to work.
Where digital twins deliver the most value in manufacturing
At Visual Components, when we talk about digital twins, we mainly refer to Plant and Process digital twins—digital counterparts of factories and factory processes that go beyond simple visualization by bringing simulation and real-world data closer together.
So, where do these digital twins deliver the most value in manufacturing today?
Virtual commissioning
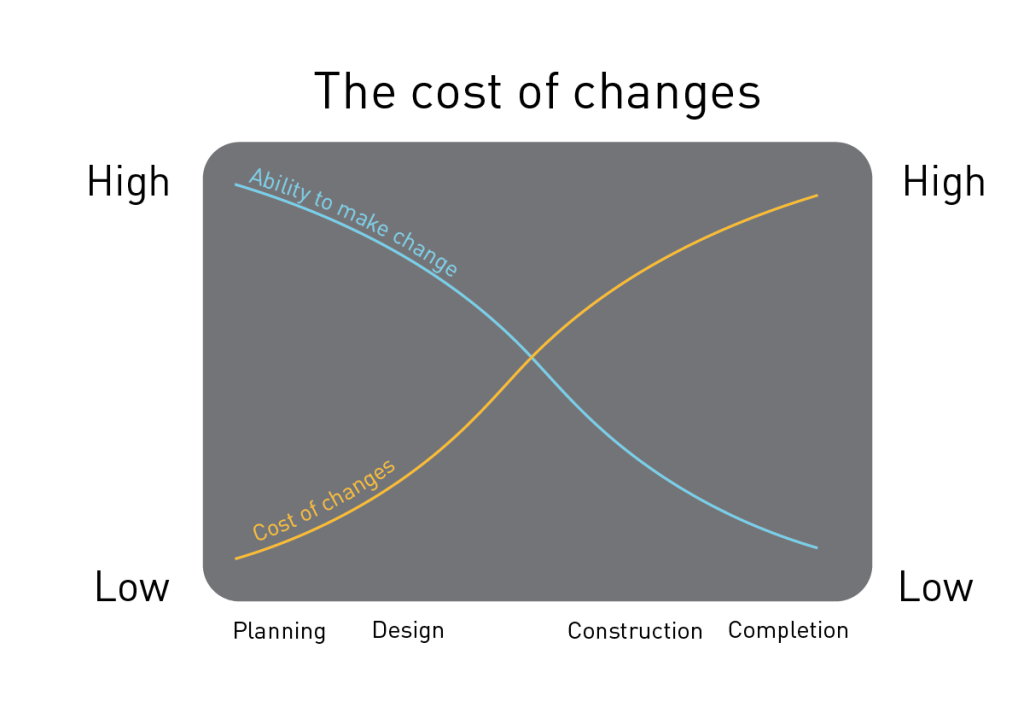
Virtual commissioning helps manufacturers catch issues early, but virtual commissioning with a digital twin takes it further. Traditional virtual commissioning relies on specialized simulation environments, where automation logic is tested in a virtual model before deployment. While this helps validate system designs, it remains a one-way process—once the system is live, the simulation doesn’t reflect real-world changes.
With a digital twin, virtual commissioning becomes an ongoing process rather than a one-time test. Think of it like the onboard diagnostics system in a modern car. Instead of just testing a vehicle before it hits the road, the system continuously monitors engine performance, predicts potential issues, and suggests optimizations. Similarly, a digital twin doesn’t just validate automation systems before deployment—it enables real-time monitoring, predictive maintenance, and ongoing performance improvements.
This level of connectivity is also helpful for compliance and safety regulations. By having a digital twin with live operational data, manufacturers can ensure their automation systems meet industry standards under real-world conditions, not just in pre-set test scenarios.
Optimization of different processes
Manufacturing processes are rarely static—what works one day might not be as efficient the next.
Unexpected bottlenecks, fluctuating demand, machine wear, and changing product mix can all disrupt carefully planned workflow. Digital twins help manufacturers continuously fine-tune their operations, adapting to real-world conditions rather than relying only on predefined scenarios.
Take a packaging facility, for example. A well-designed conveyor system might function smoothly under normal conditions, but shifts in production volume or supply chain delays can cause congestion in certain areas. A digital twin provides real-time insights into product flow, allowing manufacturers to adjust conveyor speeds, reroute items, or optimize batch sizes as needed—ensuring steady throughput and minimizing disruptions.
Workforce training and knowledge retention
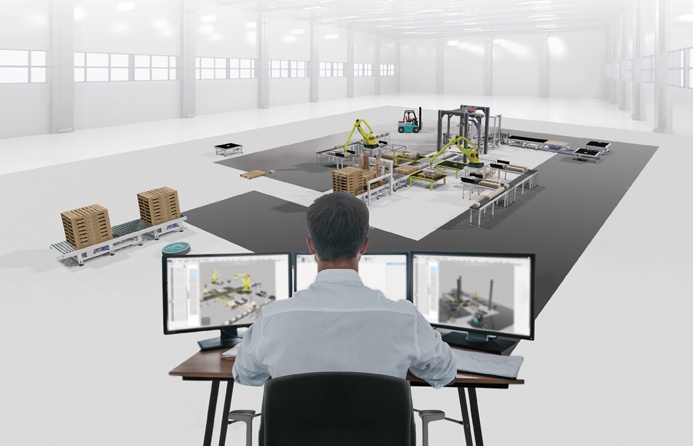
Training new employees in manufacturing environments can be challenging. Complex automation systems, safety risks, ongoing production, and production demands often limit hands-on learning opportunities. Digital twins offer a more effective approach, allowing workers to train in a risk-free virtual environment that mirrors real-world operations.
Unlike traditional training methods, where workers learn through static manuals, classroom instruction, or limited hands-on practice, a digital twin provides an interactive, real-time learning experience. Employees can explore machine operations, run through production scenarios, and even simulate troubleshooting processes—all without interrupting actual production. This helps reduce onboarding time while ensuring workers are better prepared before stepping onto the factory floor.
But training doesn’t stop at onboarding. As factories introduce new automation systems, robotics, or production workflows, employees need to upskill without disrupting operations. A digital twin allows companies to continuously refine training programs, adapting them to reflect the latest technologies and best practices.
By making workforce development an ongoing, adaptable process, digital twins help manufacturers try different ways to battle the ongoing labor shortages in the manufacturing industry.
Why simulation is the best starting point
The idea of a fully integrated, real-time, bidirectional replica of your factory sounds great in theory. Still, most manufacturers aren’t ready to connect every process, machine, and data stream. It all seems a bit too expensive and complicated to take on.
That’s where simulation comes in. Platforms like Visual Components provide users with a controlled environment to test, refine, and optimize systems before committing to full-scale digital twin integration. Manufacturers can experiment with layouts, process flows, and automation strategies without the complexity of real-time data exchange.
With Visual Components’ eCatalog, you also get access to a huge library of simulation-ready, true-to-life 3D components covering all kinds of manufacturing assets. That means you can start building and testing your simulations right away, without needing to model everything from scratch.
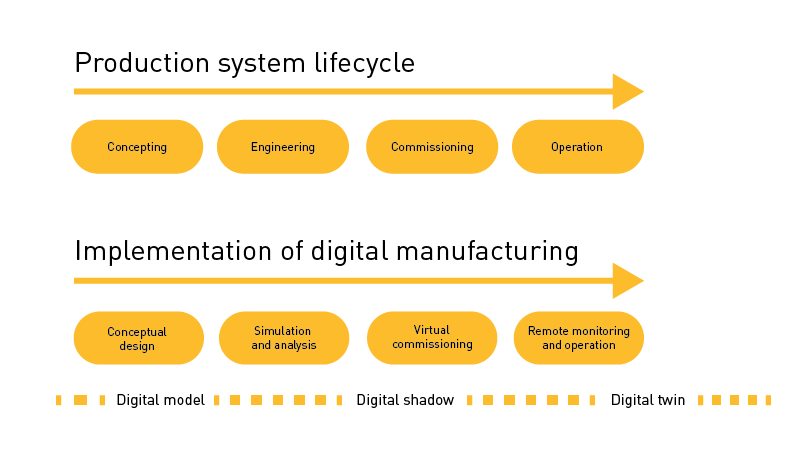
Rather than overhauling an entire factory at once, companies can start small—simulating a single process, starting with conceptual design, validating improvements, and scaling gradually. Digital transformation doesn’t happen overnight, and simulation offers a practical, low-risk entry point that paves the way for digital twins to become a natural part of manufacturing operations.
Digital twins, AI, and the future of manufacturing
The future of digital twins is looking exciting with some key trends to watch. AI-powered digital twins are just on the horizon, enhancing predictiveness and self-optimization. Imagine a system that not only alerts you when something is about to fail but also recommends the best way to fix it before the issue occurs. AI-driven predictive analytics will play a major role in optimizing inventory levels, reducing waste, and ensuring production meets demand efficiently. By combining AI with digital twins, manufacturers can achieve true data-driven decision-making.
Full factory twins will become more common as technology becomes more accessible, providing real-time monitoring and optimization across entire plants. Sustainability gains will also be a big driver, helping cut waste, optimize energy use, and drive greener manufacturing.
Why manufacturers need to act now
Manufacturers that embrace digital twins today will gain a significant competitive advantage.
Visual Components offers a comprehensive platform and products that support manufacturers at every stage of this journey, from initial simulation and process validation to advanced robot programming and full-scale digital twin implementation.
Contact us if you’re ready to explore how simulation and virtual commissioning can bring new life to your operations. The future of manufacturing is digital—let’s get you there.
Further reading
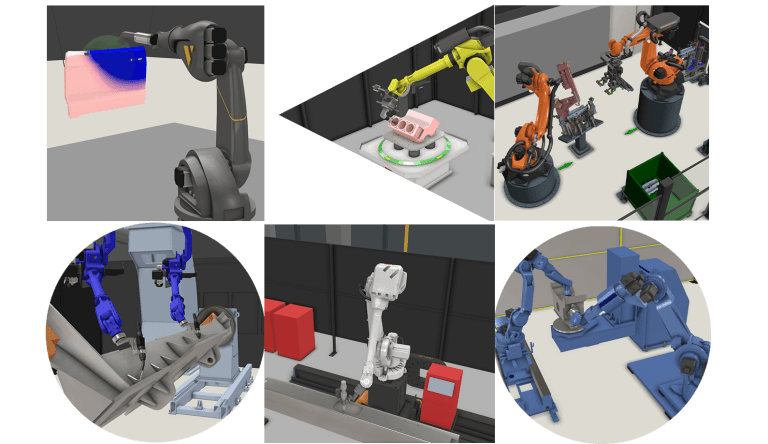
Robot programming for industrial processes with Visual Components OLP software
Robot programming is advancing with offline programming, enabling manufacturers to optimize robotic tasks virtually without disrupting production. This minimizes downtime, improves accuracy and streamlines processes like welding, spraying, processing and...
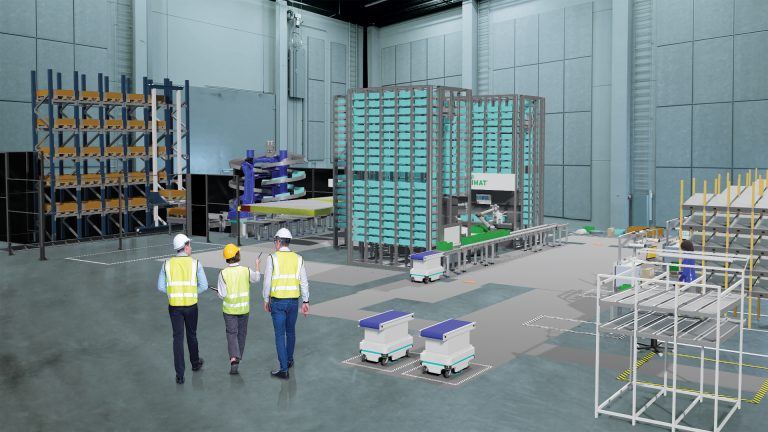
The future of automated manufacturing (and why humans still matter)
Automation in manufacturing has been evolving for decades, but its true impact isn’t in replacing people, it’s about making them more capable. We spoke with Mika Anttila, one of Visual...
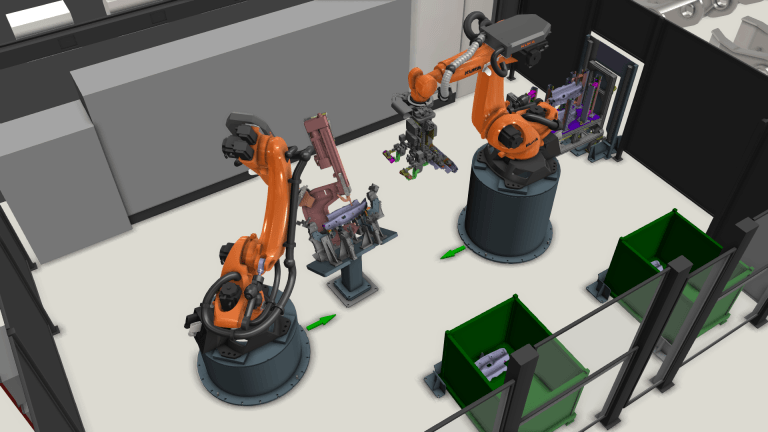
How robot offline programming drives efficiency in high-mix, low-volume production lines
Frequent changeovers and small batch sizes can slow down production, but they don’t have to. With robot offline programming (OLP), manufacturers in high-mix, low-volume production can program robots 10 times...