Trends in Packaging and Palletizing 2021
In this article, we’ll cover the latest trends affecting packing and palletizing operations and the use of production simulation to tackle the challenges in adapting to these changes.
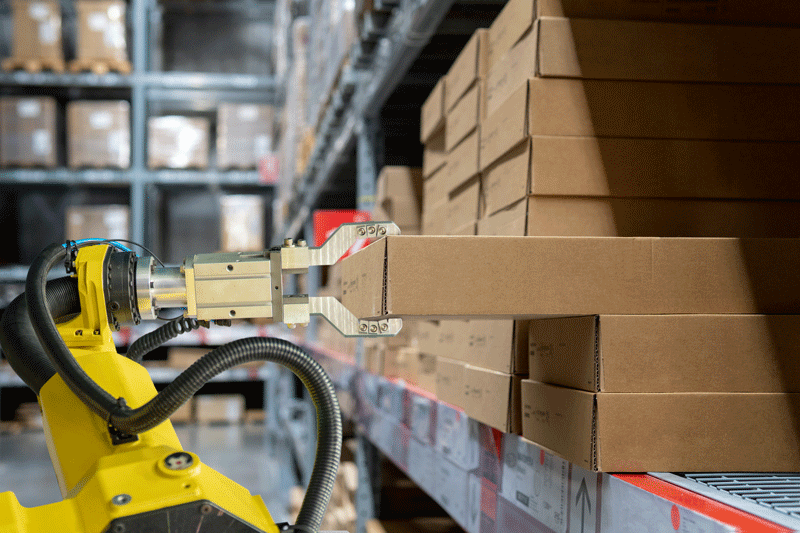
Plastics are out, recycling is in. Cardboard is good, or is it bad? It’s always been hard to keep up with the dynamic world of packaging, but in 2021 it seems to be moving faster than ever. We know increased consumer focus on packaging is likely to drive shifts in how product is packed, palletized and wrapped. At the same time, the way products are bought and delivered is changing faster than anyone might have predicted just a few years ago.
For manufacturers, integrators, and users of packaging and palletizing equipment, this environment is a recipe for uncertainty and indecision. How are they to ensure equipment installed this year won’t be obsolete in 18 months? How do they provide flexibility, and what can they do to increase packaging and palletizing velocity without increasing costs?
Visual Components doesn’t have the answers to these questions, but we do have tools that equipment designers, integrators and operators can use to find them. Our CEO, Mikko Urho says,
For [the] packaging/palletizing industry to keep up with the competition and to make sure they are on top of the trends that are happening in this industry, the ability to design and validate new production solutions confidently is becoming more crucial.
Mikko Urho, CEO of Visual Components
Our simulation tools give users the ability to do just that. But before diving into solutions, let’s start by understanding the major trends affecting packaging and palletizing. We’ll do this under the headings of:
- eCommerce
- Sustainability
- Packaging Formats
- Competition
- Technology
Although underway before 2020, the pandemic has clearly accelerated the shift towards online shopping and home or workplace delivery. In response, distribution centers (DCs) are multiplying across the country, and especially in population centers.
Inside these DCs, despite heavy investment in automated warehousing systems, these operations still depend on armies of pickers. Equipped with picking lists, totes and carts, these hard-working individuals cover miles each day gathering items, consolidating orders and packing boxes for transport and delivery.
Eager to increase the velocity with which product moves through these facilities, operators are investing heavily in autonomous mobile robots and tools that increase picking speed and accuracy. Meanwhile, development of automated picking systems continues apace.
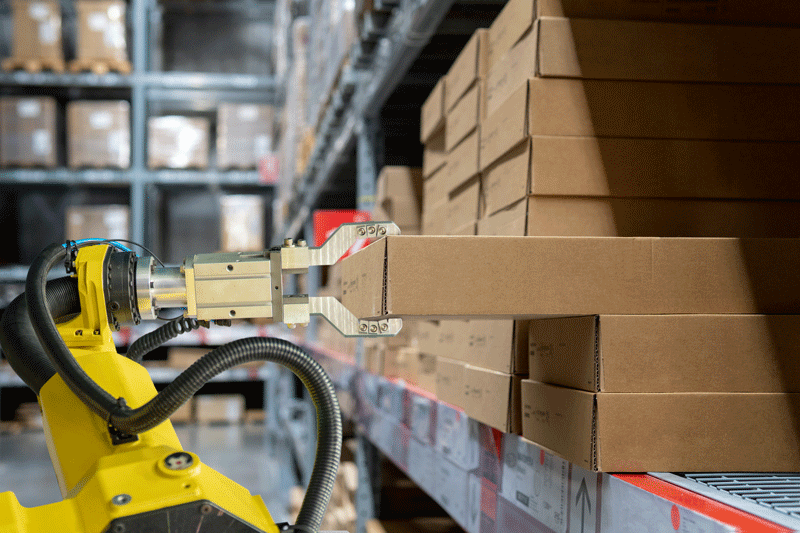
Sustainability
Amid rising concern over the impact of plastic and Styrofoam on the environment and the introduction of Extended Producer Responsibility (EPR) regulations, designers are looking for more environmentally friendly packaging options. Glass bottles, aluminum cans, and biodegradable cardboards are increasingly in-vogue, presenting challenges for packaging equipment designers.
A closely-linked aspect of packaging is the drive to reduce weight and increase volume utilization while still performing the core function of product protection. Rectangular boxes rather than glass bottles, pouches instead of boxes. From the “green” perspective these raise transport energy efficiency, and from the product manufacturers viewpoint they mean lower costs. For those in packaging and palletizing though, they create challenges: how to configure equipment for these different formats?
Packaging Formats
Clearly, growing interest in sustainability is having a big impact on packaging, but so too is marketing. Retailers want different formats to support a variety of display and sales methods, from unit quantities to cases. Marketeers want the ability to bundle product for campaigns or offer different formats, and the role of packaging itself is expanding.
Modern packaging is increasingly a marketing tool as well as a means of protection and identification. Unique colors and shapes communicate brand “values” which may boost sales but creates challenges for those designing the equipment to move these containers.
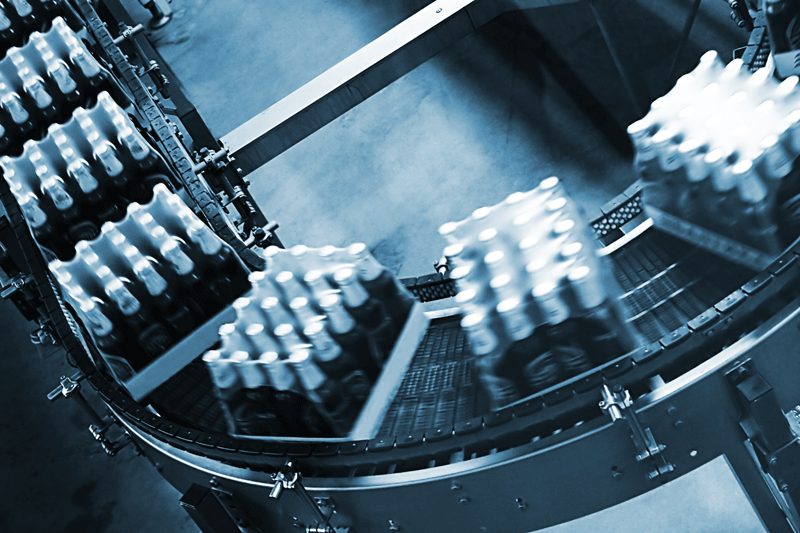
Competition
Pressure to reduce costs has businesses that package and palletize seeking ways to get more from less. Floor space and resource utilization must be increased while at the same time improving flexibility and reducing lead times.
Equipment manufacturers face the same pressures. Their customers want the lowest cost solutions to their packaging and palletizing challenges, along with reliability and flexibility.
In fairness, these competitive pressures aren’t new, and they aren’t exclusive to those who are packaging and palletizing. What is clear is that they are not getting any easier.
Technology
The good news is, the number of solutions to these challenges keeps growing as packaging and warehousing technology advances. The flip side of course is that there are more options to evaluate, but let’s focus on the emerging tech. This includes:
- Automated storage and retrieval (ASR) systems for warehouses
- Autonomous mobile robots for moving totes, packages and materials through warehouses, DCs and factories
- Advanced picking technology – pick-to-light and pick-to-voice
- Robotic kitting, packing and palletizing systems. (Advanced systems can build mixed pallets for delivery to retail outlets)
- Real-time data collection via connected sensors, (the “Internet of Packaging” or IoP,) coupled with AI-enable analytics that present valuable information via dashboard displays
- Virtual and augmented reality (VR and AR) for showing 3D environments and overlaying information on real-world scenes. (This supports both development of new solutions and remote support of existing equipment.)

Industry Implications
Recognizing the trends impacting the industry is only the beginning. Industry leaders need ways on which to act on and take advantage of these trends to grow their businesses. Some particular challenges they face are:
- How to make more effective use of existing floor space
- How to increase utilization of manufacturing assets
- How to identify and implement optimal automation solutions
Adding space is expensive and locks-in high fixed costs for the future. Far better to increase the velocity with which goods move through the existing space. This requires first understanding flows and complex dynamic behaviors and then identifying and implementing changes that bring about improvement.
Every factory and processing or packaging line has one or more bottlenecks that constrains total output. Opening this up increases total capacity and lets asset work harder. The challenge is first to find the constraint and then to determine the changes needed to optimize workflow.
Presented with an array of automation solutions, it’s no easy task to work out which offers the best ROI. Complicating this calculation are factors like floor space utilization, impacts on flow velocity and maintenance and support requirements. Then finally, there are hard-to-quantify factors like the future impact of sustainability trends and incorporating flexibility for future packing and palletizing formats.
Simulate to Understand and Educate
If it seems that reacting to and taking advantage of these packaging and palletizing trends involves a lot of “what-if” questions, that’s because it does. In the past engineers and managers used spreadsheets, drawings, physical models and more recently, CAD to answer these by modeling various scenarios.
Each tool or model provided part of the picture but was never able to encompass the full complexity of workflow through manufacturing, packaging and warehousing operations. In addition, the time and effort they took to create and use made it impractical to model more than a handful of favored options. As a result, reaching the truly optimal layout, equipment configuration or level of automation and asset utilization was a matter of luck and in practice probably never achieved.
Today there is a tool that enables comprehensive modeling and analysis of the most complex production situations. This tool is 3D production simulation.
With production simulation it’s possible to build a virtual representation of an existing production line, kitting operation or palletization area, a digital twin, if you wish. Validation against existing real-world operation is straightforward: feed the simulation actual production data and see how closely model results match the performance observed. Then, following any necessary finessing of the model, add in changes being considered, evaluate alternative production scenarios, explore the impact of different layouts and workflows.
Simulation capability like this enables the creation of more accurate models and the evaluation of more scenarios than ever before feasible. This benefits both the operators of factories and warehouses, and those in the business of selling them solutions.
For operators the benefit is the ability to more completely optimize workflows, layouts, manning and automation without the risks of relying on trial and error and expert judgment. For those in the packaging and palletizing equipment sector, production simulation benefits them in two ways. First, it’s a tool with which to determine optimal solutions (and perhaps identify gaps in product offerings or where improvement opportunities exist.) Second, it lets them communicate those solutions to their clients in a visual, and thus extremely powerful, way. If seeing really is believing, simulation helps them believe!
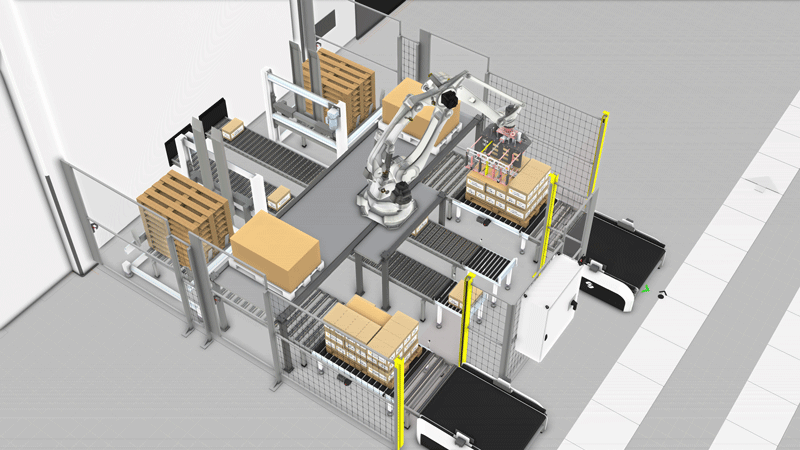
Reducing Risk and Seizing Opportunities
For leaders in manufacturing, packaging, palletizing, warehousing and distribution operations these really are challenging times. A convergence of trends requires changed and improved equipment, layouts and working methods, but getting it wrong will impair competitiveness for years to come. Making decisions about what to change is not for the fainthearted!
The answer is to model current and proposed operations and equipment using production simulation software. This enables more accurate modeling and faster, more complete evaluation of alternatives. When faced with difficult problems, production simulation can reveal answers that may otherwise have remained hidden. It can’t tell you what’s going to change in the future but it can help you prepare.
Further reading
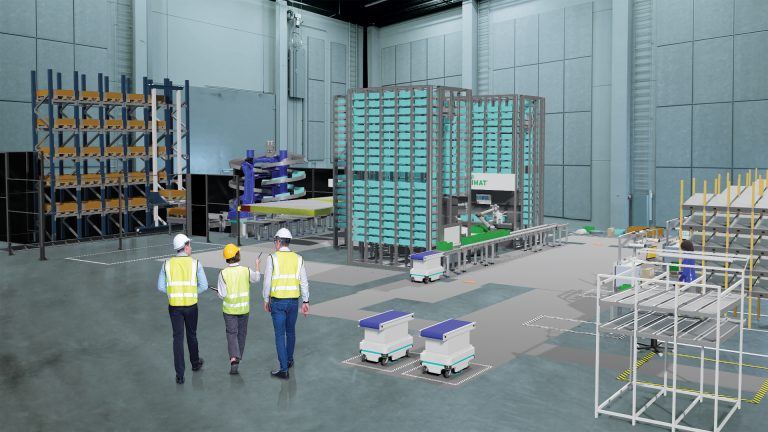
The future of automated manufacturing (and why humans still matter)
Automation in manufacturing has been evolving for decades, but its true impact isn’t in replacing people, it’s about making them more capable. We spoke with Mika Anttila, one of Visual...
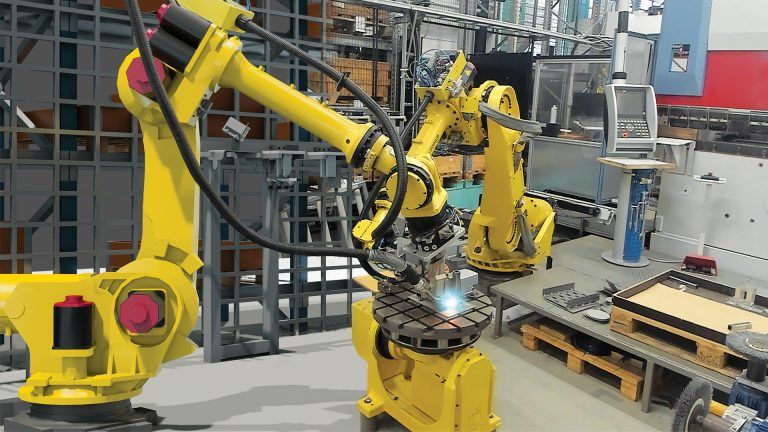
Understanding digital twins in manufacturing
Digital twins go far beyond static models or simulations. They bridge the gap between virtual and physical systems, offering real-time insights and control. But with so many definitions floating around,...
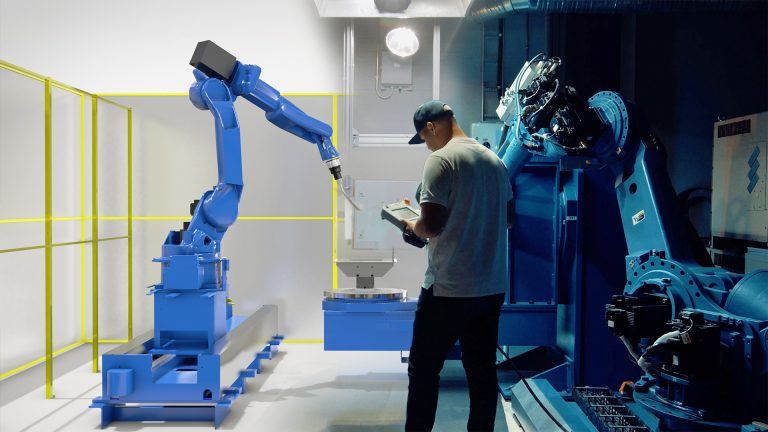
Tackling the manufacturing skills shortage with simulation and robot offline programming
The manufacturing industry is grappling with a significant skills shortage, exacerbated by the pandemic and an aging workforce. According to The Manufacturing Institute, 78% of companies are concerned about this...