Smarter warehouse planning starts with simulation
How can businesses design warehouses that operate efficiently from day one while keeping labor costs and other expenses in check? The key is smart planning and validation with simulation tools like Visual Components.
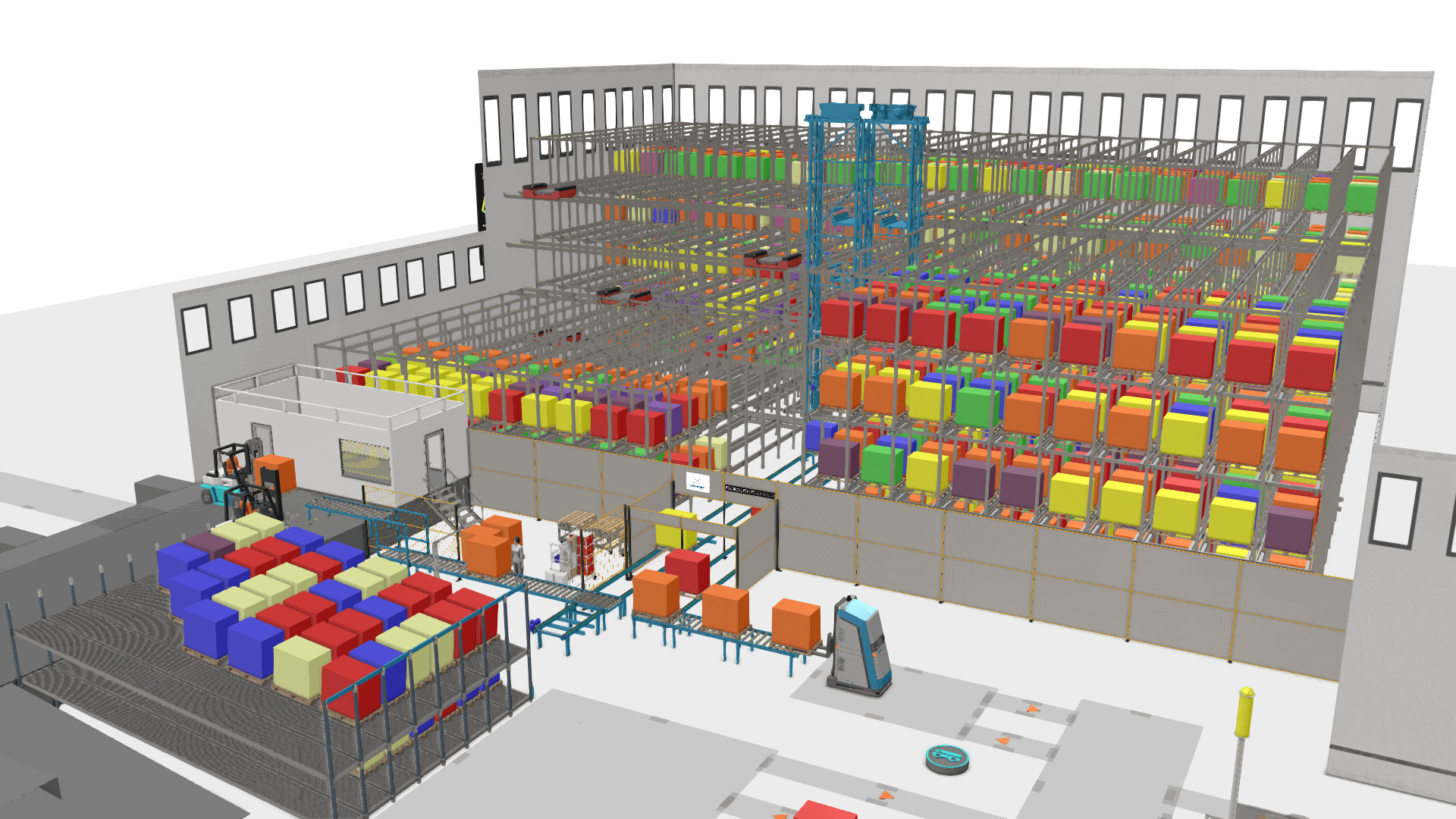
A warehouse that isn’t planned properly is a warehouse that doesn’t work properly.
That might sound obvious, but without proper planning, you could be missing out on a 20% productivity increase. A poorly designed warehousing or logistics layout might force workers to take unnecessary steps, with shelves positioned too far from picking stations. Fast-moving products could end up buried behind slow-moving ones, wasting valuable time. And if automation isn’t integrated correctly, instead of streamlining operations, it can create new bottlenecks and inefficiencies.
The foundations of a well-planned warehouse
Not every warehouse is built the same, but all share a common goal: maximizing efficiency while staying flexible. Some facilities prioritize bulk storage, others rapid order fulfillment, and many act as distribution hubs. Regardless of function, a warehouse must be designed to support smooth operations and adapt to changing demands.
To improve layout and performance, businesses first need to identify inefficiencies. Common issues include wasted space, long picking times, and congestion in key areas, all of which drive up costs and slow productivity. Many warehouses struggle to maintain efficiency year-round, especially during peak demand periods, making a structured planning process essential.
Data from Warehouse Management Systems (WMS) and movement tracking tools can pinpoint problem areas, such as frequent congestion points or inefficient travel paths. But identifying issues is only the first step—solving them requires a well-designed strategy that aligns layout, automation, and workflows.
Initial steps in warehouse planning
Warehouse planning is both an art and a science. A well-designed warehouse makes the best use of space, keeps operations flowing smoothly, and can adapt as needs change. That means finding the right balance between storage density and accessibility, optimizing movement, and ensuring automation actually improves workflows rather than complicating them. For example, robotic picking systems can improve order accuracy up to 99.9% and reduce reliance on manual labor. However, these systems need to be integrated correctly, placing robotic picking zones too far from packing stations or failing to account for congestion can negate their benefits.
With that said, even with careful planning, it’s difficult to predict how a warehouse will function in the real world. A layout that looks great on paper might not perform as expected once operations are underway. That’s why businesses should start to increasingly rely on simulation to test, refine, and validate their designs before making physical changes.
Why use simulation for warehouse planning
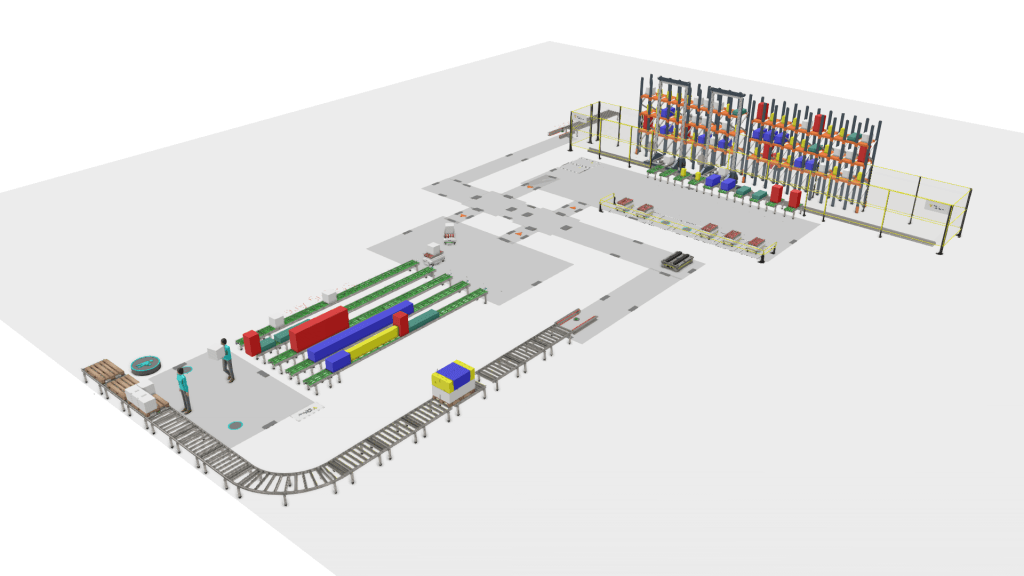
Rather than learning lessons the hard way, businesses can use simulation to test and refine their designs before implementation.
With simulation, businesses can:
- Analyze different storage configurations and their impact on retrieval times.
- Test workflows to identify congestion points before they cause real delays by simulating interactions between people, machines, forklifts, products, and other moving elements.
- Assess automation efficiency by validating AGV, conveyor, and robotic system performance.
- Model demand fluctuations to ensure the warehouse can handle peak loads effectively.
- Optimize inbound and outbound logistics by simulating loading and unloading zones, truck movements, and inventory flow.
By simulating warehouse operations, companies can reduce costly trial-and-error, make better design decisions, and confidently move forward with changes that will actually improve efficiency. This is especially important as automation increasingly influences real estate decisions with automated warehouses often requiring higher ceilings and structural support for AS/RS systems and robotics, meaning layout and space planning must be optimized upfront.
How Visual Components helps businesses simulate and optimize warehouse planning
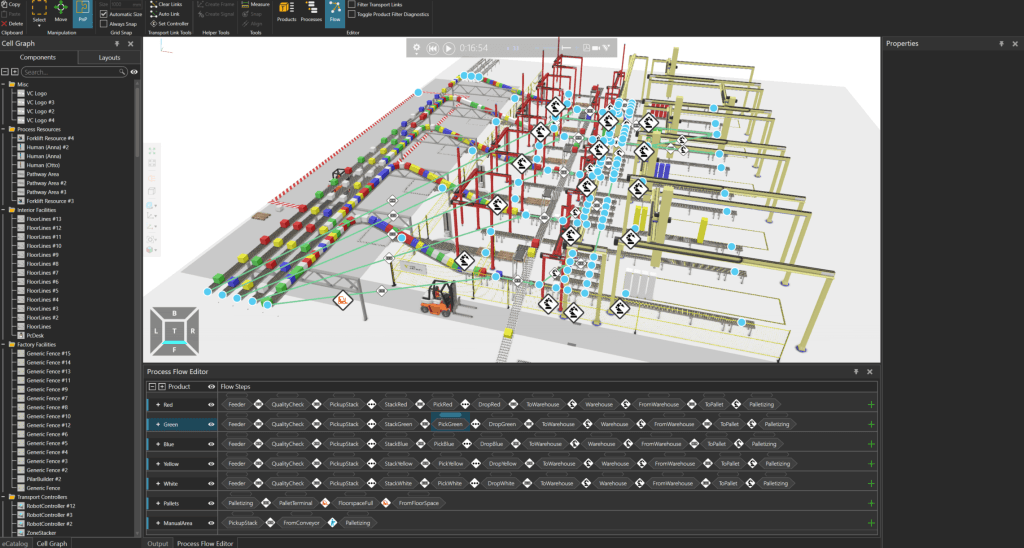
While the advantages of simulation are clear, implementing it effectively requires the right tools. Visual Components simplifies this by providing an intuitive platform to design, test, and optimize warehouse layouts in a virtual environment.
3D layout configuration for accurate warehouse planning
With Visual Components’ 3D layout tools, businesses can quickly build and modify warehouse designs. Users can drag and drop components with plug-and-play functionality from the extensive eCatalog of over 3500 simulation-ready components or import CAD files to create accurate warehouse models. This makes it easy to test different configurations and validate how space is used before making real-world changes.
Process modeling for workflow optimization
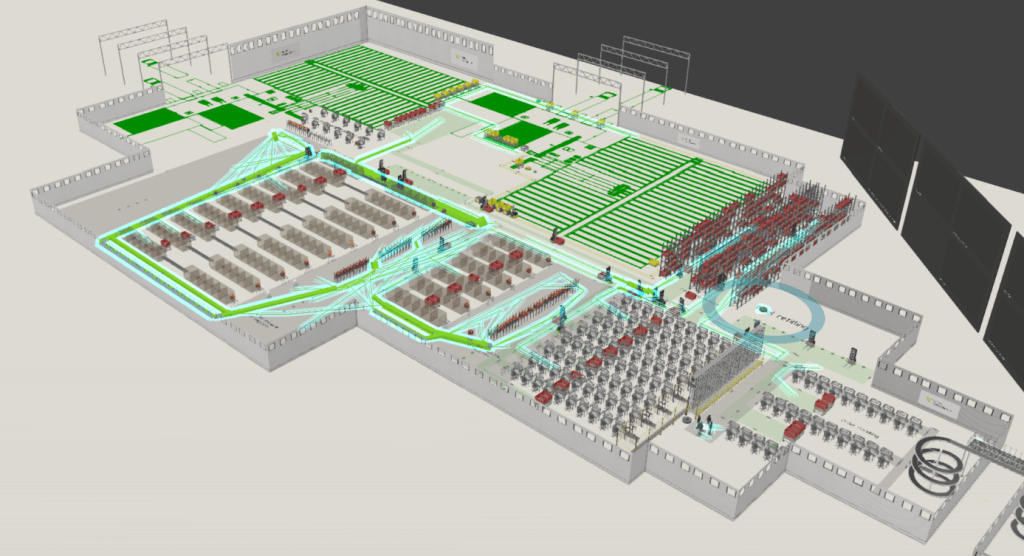
Warehouse efficiency depends on how well workflows are structured. With Visual Components’ process modeling tools, businesses can simulate material flow, test different picking and storage strategies, and identify bottlenecks before they impact operations.
Virtual commissioning for automation integration
Automation is a key part of modern warehouse design, but implementing AGVs, conveyors, and robotics without testing can be risky. Visual Components’ virtual commissioning feature lets businesses connect their simulation to real-world control systems, ensuring everything works as expected before deployment.
Businesses can use these tools to design smarter warehouses, optimize automation, and reduce costly trial-and-error.
From virtual model to real-world execution
Once a warehouse plan has been tested and refined through simulation, the next step is making it a reality. But even a well-planned design won’t deliver results if changes are rushed or disrupt daily operations. Large-scale improvements should be introduced carefully to minimize disruptions while maximizing efficiency gains.
Rather than overhauling everything at once, businesses should focus on the changes with the biggest impact—adjusting picking zones, reorganizing storage layouts, or optimizing conveyor placements. These refinements often improve efficiency immediately without requiring a complete reset of daily operations.
Tracking performance over time is just as important as getting the layout right in the first place. Order fulfillment speed, congestion points, and material flow metrics should be continuously monitored to ensure the warehouse is operating as expected. And when adjustments are needed, simulation provides a way to test solutions before implementing them in the real world.
The future of warehouse planning
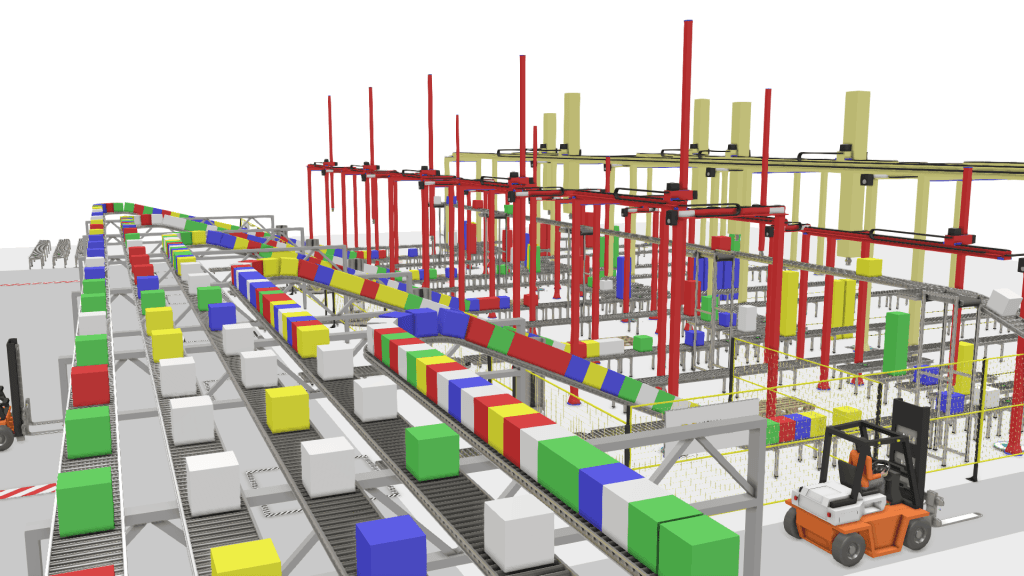
As warehouse technology advances, planning methods need to keep up. Digital twins, real-time digital models of warehouses which connect to things like WMSs, are going to make it possible to monitor and adjust layouts dynamically. Meanwhile, sustainability and automation through new technologies like AI will become more central to warehouse design, requiring smarter strategies for energy efficiency and workflow optimization.
A smarter way to plan your warehouses
Warehouse planning is the foundation of efficiency, scalability, and cost management. Without a solid plan, operations become disorganized, fulfillment slows down, and expenses pile up.
Simulation transforms warehouse planning from guesswork into a data-driven process. To quickly summarize, using simulation, businesses can:
- Design layouts that maximize space and improve material flow
- Reduce risks by testing plans before implementation
- Continuously adapt warehouse operations as business needs evolve
At Visual Components, we believe simulation is a strategic advantage. Whether you’re optimizing an existing facility or designing a new one, simulation gives you the clarity and confidence to build a high-performing warehouse from the start.
Want to see how simulation can improve your warehouse? Get in touch with us today.
About Visual Components
Founded by a team of simulation experts with 25 years in business, Visual Components is a pioneer in 3D manufacturing simulation. Visual Components is a trusted technology partner to over 2 400 leading brands and 40 partners globally, offering machine builders, system integrators and manufacturers a simple, quick and cost-effective solution to design and simulate production processes and robot offline programming (OLP) technology for fast, accurate and error-free programming of industrial robots.
Further reading
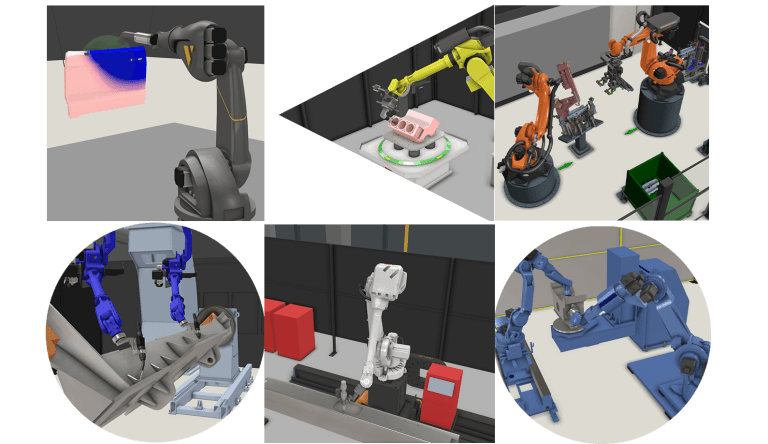
Robot programming for industrial processes with Visual Components OLP software
Robot programming is advancing with offline programming, enabling manufacturers to optimize robotic tasks virtually without disrupting production. This minimizes downtime, improves accuracy and streamlines processes like welding, spraying, processing and...
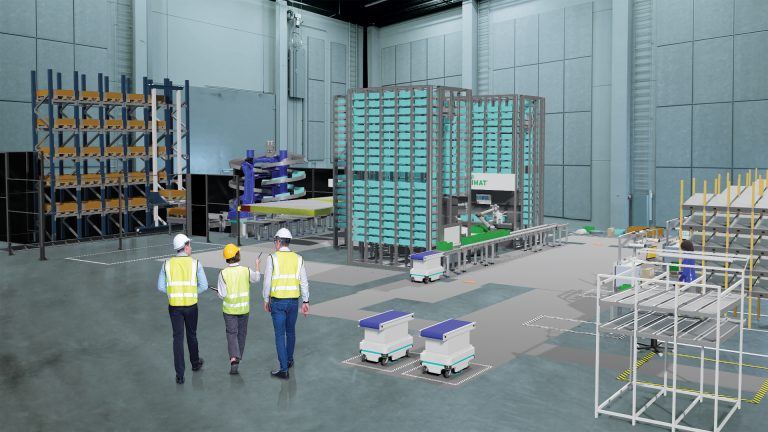
The future of automated manufacturing (and why humans still matter)
Automation in manufacturing has been evolving for decades, but its true impact isn’t in replacing people, it’s about making them more capable. We spoke with Mika Anttila, one of Visual...
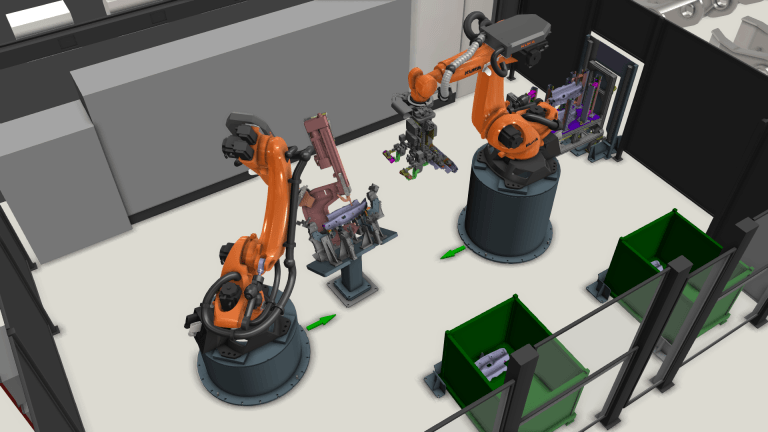
How robot offline programming drives efficiency in high-mix, low-volume production lines
Frequent changeovers and small batch sizes can slow down production, but they don’t have to. With robot offline programming (OLP), manufacturers in high-mix, low-volume production can program robots 10 times...