Optimizing production lines the smart way with simulation
Manufacturers are always looking for ways to improve, whether it’s increasing throughput, reducing bottlenecks, or making better use of resources. But optimizing production lines can get complicated without the right tools. That’s where simulation comes in, letting manufacturers test, refine and communicate process changes in a virtual environment before making real-world adjustments.
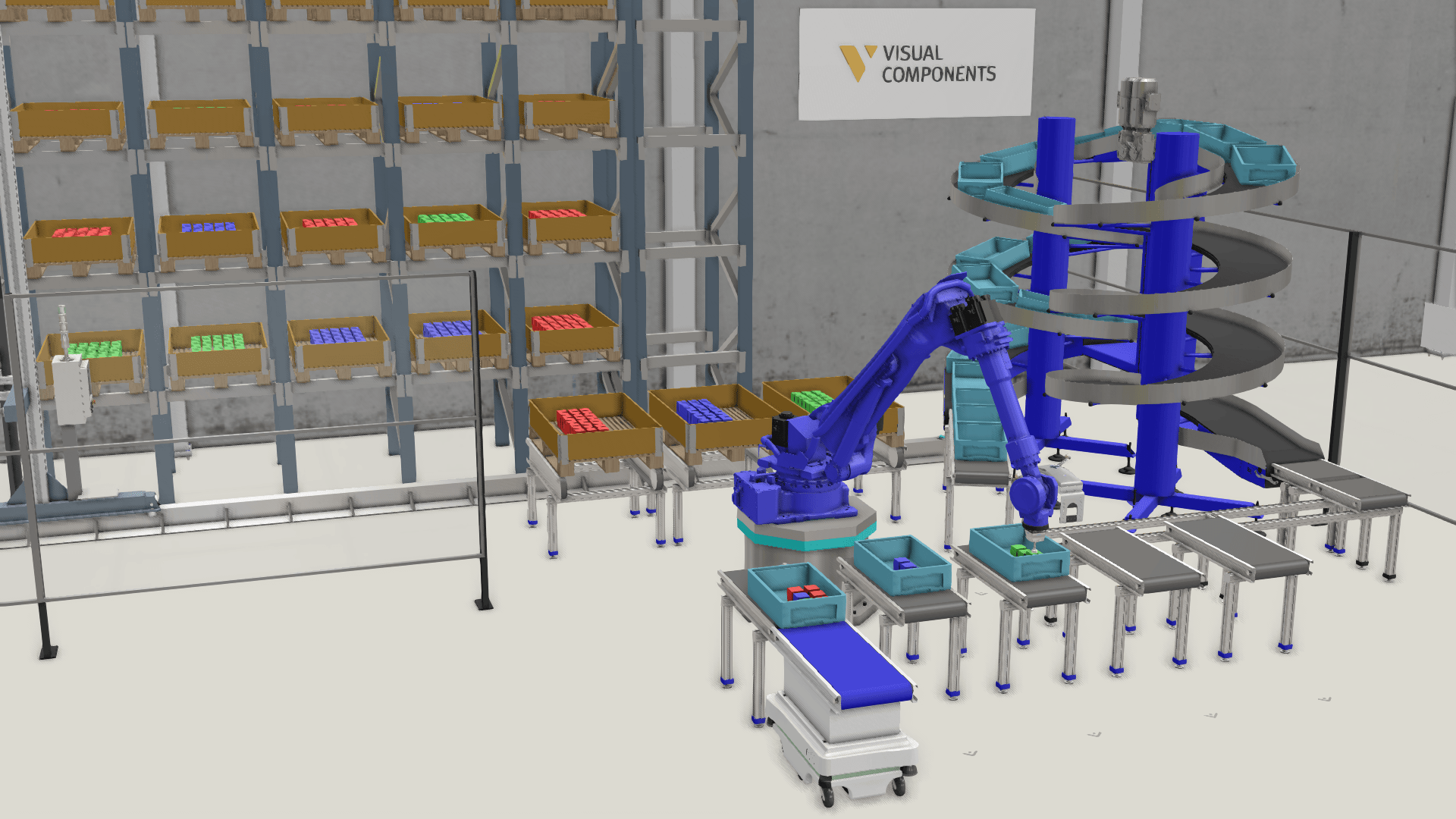
Optimizing production lines the smart way with simulation
Every manufacturer knows the pressure to produce more, waste less, and keep operations running smoothly. But anyone who’s tried to optimize a production line knows it’s rarely that simple. Adjustments often feel like a high-stakes gamble, a change that should improve efficiency might instead create bottlenecks, cause downtime, or spark resistance from employees accustomed to existing workflows.
Traditional approaches like Lean Manufacturing and Six Sigma have provided structured ways to eliminate inefficiencies, but they still rely on real-world implementation, which means there’s always some level of uncertainty. The real challenge is how to refine processes without disrupting production or making costly mistakes.
That’s where simulation technology can come in handy. Instead of optimizing processes through trial and error, manufacturers can test changes virtually first, refining layouts, workflows, and automation strategies in a digital environment before committing to real-world adjustments.
Why optimizing existing processes is still so difficult
Even with today’s digital tools, many manufacturers still rely on static, outdated methods when planning process improvements.
Take a common scenario: installing a new conveyor system to transport materials between workstations. If the layout turns out to be inefficient, fixing it isn’t as simple as moving things around. You may need to halt production, rewire control systems, or even modify structural elements. The stakes are high, and mistakes are costly.
Beyond physical challenges, manufacturers face organizational obstacles
- Uncertain ROI – Leadership is often hesitant to approve process changes without clear evidence of measurable benefits.
- Lack of alignment – Engineers, operators, and management may have different definitions of what “optimization” looks like, leading to conflicting priorities.
- Resistance to change – Employees who have worked with the same processes for years may be skeptical of new methods, especially if the benefits aren’t immediately clear.
According to McKinsey & Company, manufacturers that successfully implement and scale data-driven process optimization and automation can achieve significant improvements, including up to a 30% increase in labor productivity. However, many companies struggle to move beyond small pilot projects because they fail to get widespread stakeholder engagement, leading to stalled initiatives.
Traditional tools fall short
For decades, manufacturers have relied on a few standard tools for process planning:
- CAD drawings & 2D schematics – Useful for rough layout planning but lack real-world interactivity.
- PowerPoint presentations & reports – Commonly used to communicate changes but fail to provide a practical sense of how a process will function.
- Manual time & motion studies – Valuable for identifying inefficiencies but labor-intensive and often incomplete.
While these tools can highlight potential improvements, they don’t allow manufacturers to experiment safely or effectively communicate changes across teams. That’s why many companies are turning to 3D manufacturing simulation; a way to test, refine, and visually demonstrate process changes before implementing them in the real world.
Using 3D simulation to reduce risk and improve efficiency
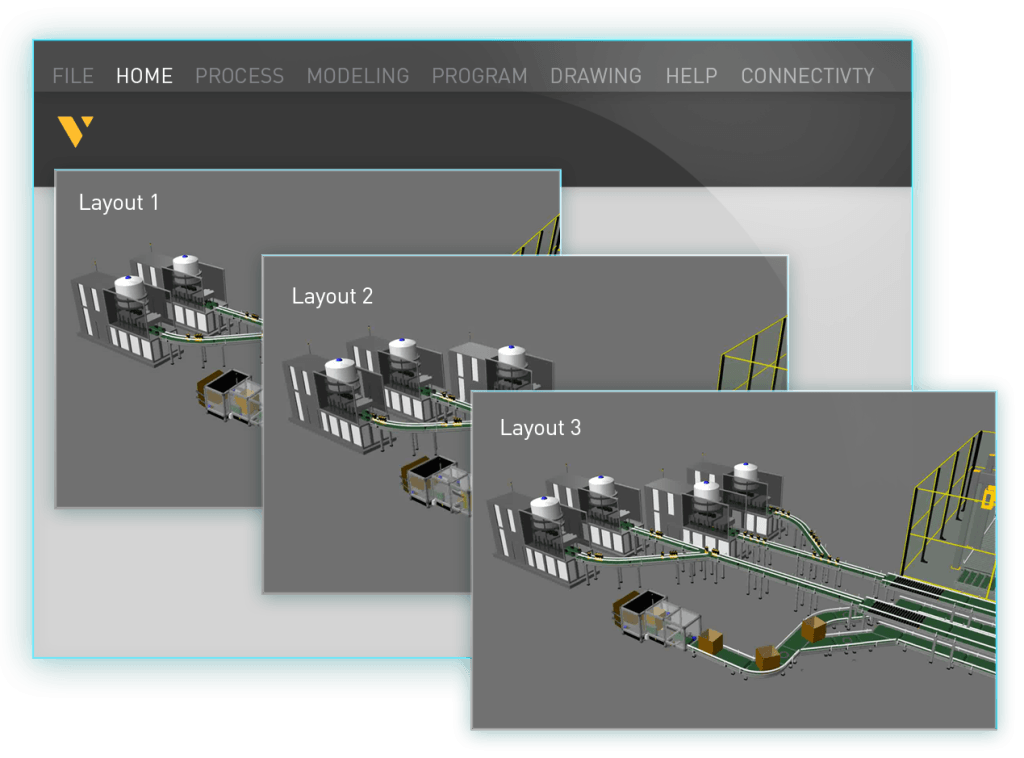
Rather than making process changes with uncertainty, 3D manufacturing process simulation allows manufacturers to evaluate multiple scenarios in a controlled digital environment, ensuring that every stakeholder is on board with the changes being made. Virtual commissioning with tools like Visual Components goes a step further by enabling manufacturers to test and validate automation systems, including PLC logic and robot programs, before deploying them on the factory floor. Whether testing a new production layout, integrating automation, or adjusting workflows, simulation makes it possible to predict outcomes before making real-world adjustments.
Key benefits of 3D manufacturing process simulation
- Improved collaboration – Engineers, operators, and management can visualize changes together, ensuring alignment before implementation.
- Minimized production risk – Testing occurs in a virtual setting, preventing costly disruptions to live operations.
- Data-driven decision-making – Process changes are evaluated based on real performance metrics, not just intuition.
- Faster iteration and experimentation – Teams can quickly modify layouts, introduce automation, and fine-tune workflows without the delays and risks of physical changes.
For manufacturers who have been hesitant to implement large-scale process improvements due to the fear of costly mistakes, simulation provides a low-risk, high-accuracy approach to decision-making.
From concept to reality, without the guesswork
The real power of simulation lies in its ability to bridge the gap between concept and reality. Instead of relying on theoretical models or best guesses, manufacturers can build realistic digital models that reflect their actual production environments.
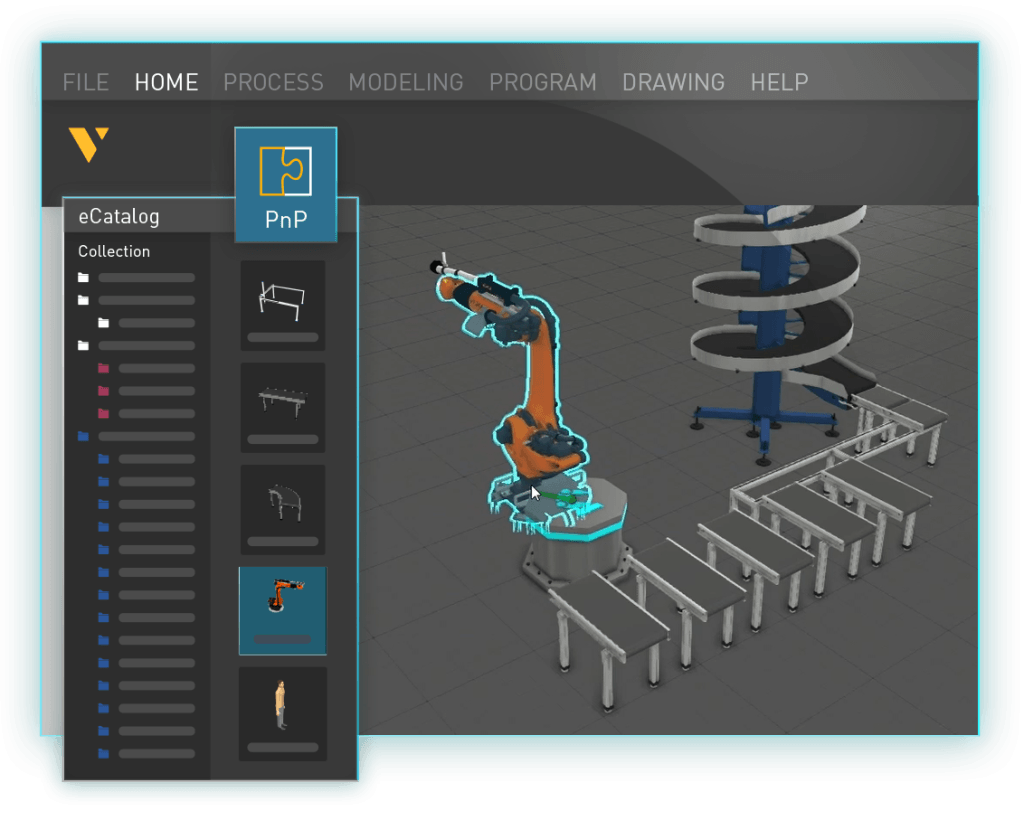
Using pre-built libraries (like the Visual Components eCatalog) of industrial robots, machines, and automation components, teams can construct virtual production scenarios and test different setups in minutes. These simulations allow manufacturers to see how equipment interacts, identify potential bottlenecks, and refine processes before investing in physical changes.
Beyond simple visualization, process modeling enables teams to:
- Map out workflows and material flows.
- Define rules and constraints for automated systems.
- Simulate movement and interactions within the production line.
Additionally, factory layout tools allow engineers to import 2D drawings, point cloud data, and CAD models to create highly accurate digital twins of production spaces. This enhances spatial planning and resource allocation, ensuring that changes fit seamlessly into the existing facility.
Turning data into action
Simulation isn’t just about visualizing changes, it’s about quantifying their impact. By capturing and analyzing key performance metrics, manufacturers can make more informed, data-backed decisions about process improvements.
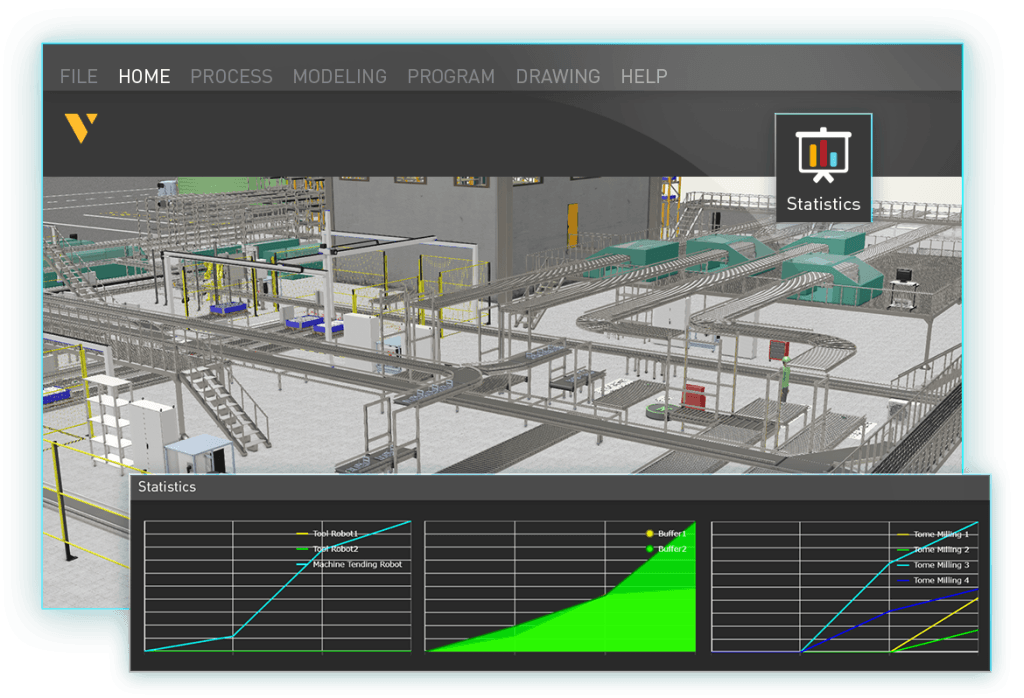
Some of the most valuable insights simulation provides include:
- Cycle times – How long does each step in the process take?
- Bottlenecks – Where do slowdowns occur, and how can they be resolved?
- Resource utilization – Are machines and workers being used efficiently?
By running multiple simulations, manufacturers can compare different configurations to determine which delivers the best results, without the risks and costs associated with real-world trial and error.
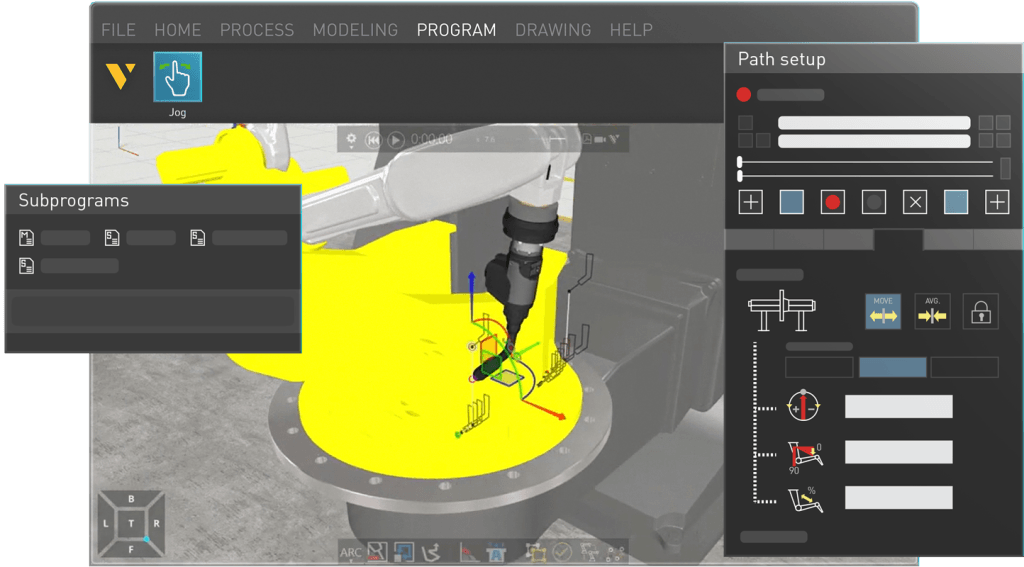
For manufacturers integrating automation and robotics, robot offline programming (OLP) takes it one step further toward real-world execution. Instead of programming robots directly on the factory floor—where errors can cause downtime—OLP enables manufacturers to fine-tune robotic operations in a virtual environment first. This ensures faster, more accurate programming with minimal disruption.
Simulation as a smarter approach to process optimization
From Henry Ford’s assembly line to today’s automated smart factories, manufacturing efficiency has always depended on continuous improvement. While traditional optimization methods have helped, they often fall short in predictability, speed, and risk management.
Simulation removes the guesswork from process optimization, ensuring that every change is backed by data, tested in a virtual environment, and aligned across departments. It allows manufacturers to:
- Plan and test improvements without production downtime.
- Optimize automation strategies before deploying them.
- Make process changes with confidence, knowing the results are backed by real data.
For manufacturers looking to stay competitive, the real question isn’t whether to use simulation—it’s how soon they can start.
Ready to explore the benefits of simulation?
If you’re interested in seeing how simulation can help your business, we’d be happy to walk you through real-world applications and potential ROI. Contact us today to learn more.
Further reading
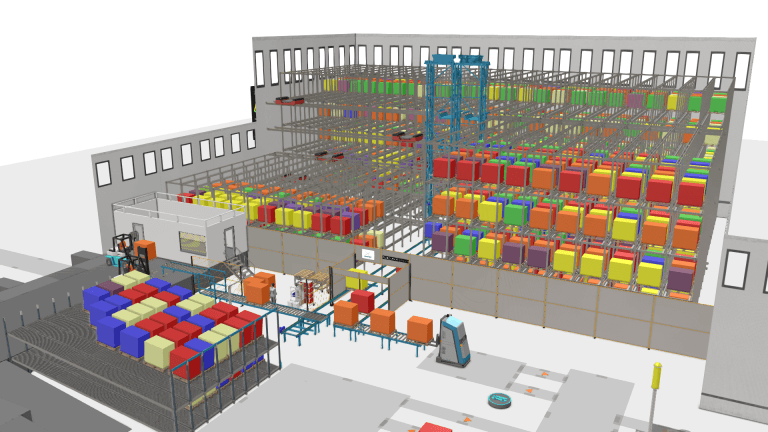
Smarter warehouse planning starts with simulation
How can businesses design warehouses that operate efficiently from day one while keeping labor costs and other expenses in check? The key is smart planning and validation with simulation tools...
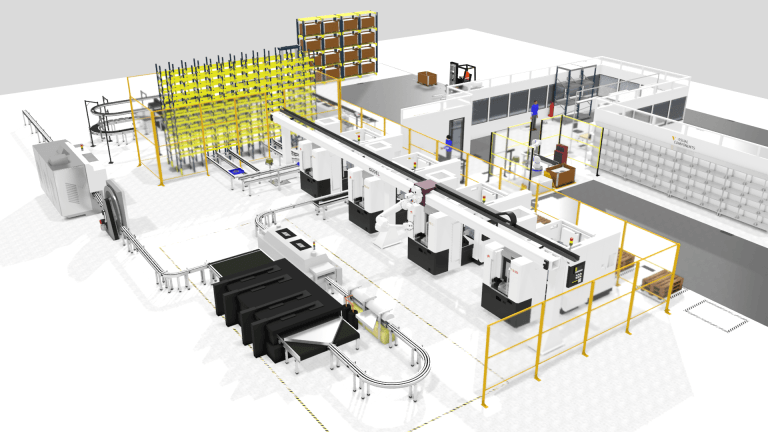
Comprehensive guide to input data for 3D manufacturing simulation (examples included)
If you're new to 3D manufacturing simulation, you're in the right place. This comprehensive guide will help you understand the essential input data needed to create effective simulation models. Whether...
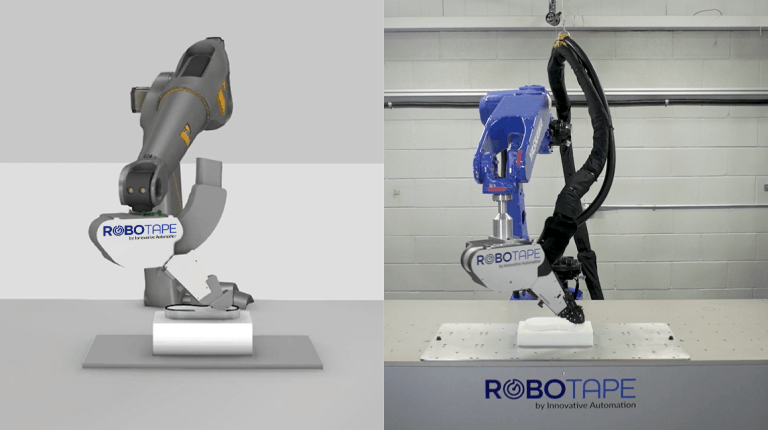
Benefits of using 3D manufacturing simulation software for planning RoboTape applications
3D manufacturing simulation software improves RoboTape planning and execution by providing detailed visualization, optimizing processes and robot movements and ensuring consistent quality. Discover how you can save time and costs,...