Increasing control software quality with virtual commissioning
Virtual commissioning helps develop better software and save time. Read more!
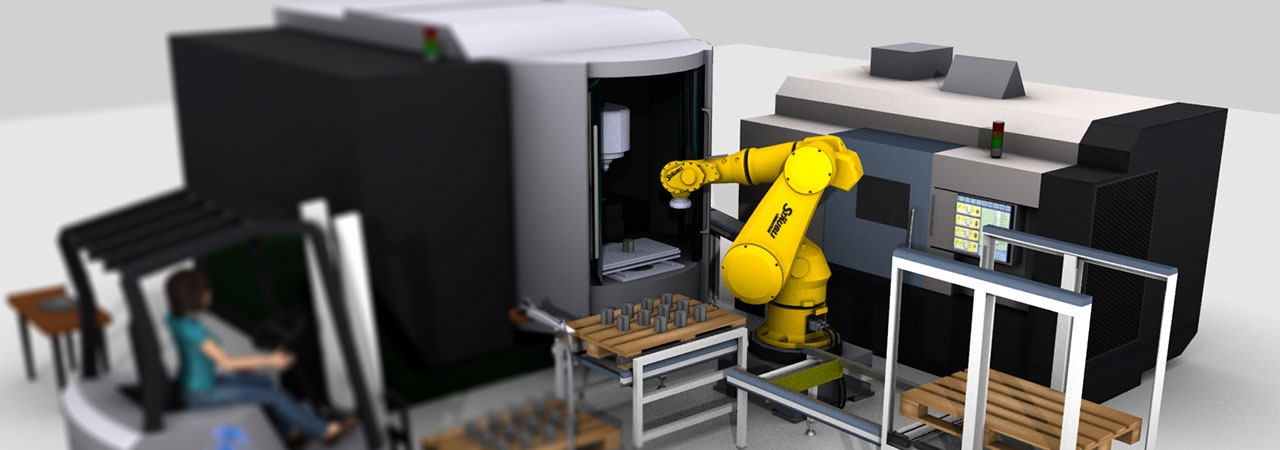
What is virtual commissioning?
Commissioning, usually the last step in the engineering process, can take up to 15-20% of the total delivery time of an automation system project. Unfortunately, nearly 2/3 of the time spent in commissioning is spent on fixing software errors*, since the control software usually goes through proper integration testing only after all the hardware has been procured and assembled.
Because commissioning is usually carried out under nearly impossible deadlines, the development of custom control software is often rushed, even so that debugging it at this stage may cause hardware damage. Resolving these problems earlier on in the process can thus save a great deal of time and effort, which in turn could be spent on optimization or earlier delivery of the project.
Virtual commissioning provides a solution for moving a significant portion of commissioning tasks to an earlier phase of the project, away from the critical path. In virtual commissioning, a simulation model of the system is created to replace the real factory. The virtual factory is then connected to the real control system, so that the simulation can be used simultaneously with the procurement and assembly to verify the design and test the control system. This allows for quicker detection of possible errors.
Figure 1: Engineering project with and without virtual commissioning.
Virtual commissioning provides a solution for moving a significant portion of commissioning tasks to an earlier phase of the project, away from the critical path.
You can also apply virtual commissioning to just a sub-system, such as one work cell or a single machine at a time, whatever suits the use case. The simulated and real machinery can also be used in parallel (a method known as hybrid commissioning), allowing the process to transition from virtual to real-life gradually.
The simulation reacts to the control system’s outputs and provides simulated inputs just like the real system would. This enables the engineers or even the customer to see how the system actually behaves through interactive 3D visualization, not just variables in the control programs. Compared to common more primitive testing of the control software the interactive visualization is a big advantage, since such tests are usually made just with code or manually setting inputs or outputs according to the programmer’s understanding of the real machinery. Also, tests that are difficult or even impossible to execute in reality without risking damage to the machines or the personnel can be executed in the simulation, resulting in better software quality and, most importantly, increased safety.
The benefits of virtual commissioning
There are many benefits to using virtual commissioning throughout the entire engineering process: the total engineering time and prototype waste are reduced, the errors are less expensive to correct since they are detected earlier and the software quality is greatly increased. As an example, in a field study conducted with a small PLC controlled system with 17 sensors and 10 actors (active components), virtual commissioning was found to increase quality (defined as fulfilment of requirements) from 37% to 84%, while simultaneously reducing the real commissioning time by 75% and total time-to-market by 15%**.
By creating visualizations of the proposed system already in the quotation phase, and then building a progressively more comprehensive simulation model during design, you can also achieve far greater synergy between both engineering teams and project stakeholders simply because an interactive 3D simulation conveys the ideas and behavior much better than a stack of design documents ever can. This will help to reduce miscommunication of design goals, desired system behavior, and information requirements between engineering teams as well as the customer.
Virtual commissioning and simulation software
Virtual commissioning places great requirements on the simulation software. It needs to support accurate simulation of a variety of systems, from simple sensors and actuators to conveying systems, robot applications and MES-level control of production facilities. Furthermore, the time spent on creating the simulation models needs to be as little as possible to achieve the goal of reducing overall engineering effort. This requires a software package that is easy to use, and allows your engineers to leverage their existing knowledge and skills. Visual Components’ family of 3D manufacturing simulation products has been created to do just that.
The simulation model needs to accurately emulate the real system’s behavior, but it is also crucial that the same exact control system and control software can be used with both the simulation and the real automation system. In practice, this means that the same PLC or robot controller hardware or software selected for the real system should be used for virtual commissioning as well.
However, any changes to the control software should be avoided so that automation engineers can use the familiar controllers, associated software and development workflow to develop the control software, and then to be able to connect it to the simulation engine.
Sources
* Liu Z, Diedrich C, Suchold N. Virtual Commissioning of Automated Systems [Internet]. INTECH Open Access Publisher; 2012 [cited 2015 Jul 13]. Available here.
** Reinhart G, Wünsch G. Economic application of virtual commissioning to mechatronic production systems. Prod Eng. 2007 Nov 8;1(4):371–9
Further reading
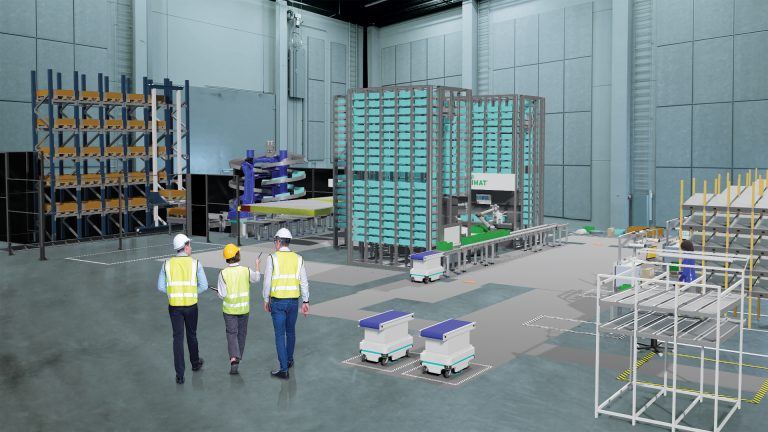
The future of automated manufacturing (and why humans still matter)
Automation in manufacturing has been evolving for decades, but its true impact isn’t in replacing people, it’s about making them more capable. We spoke with Mika Anttila, one of Visual...
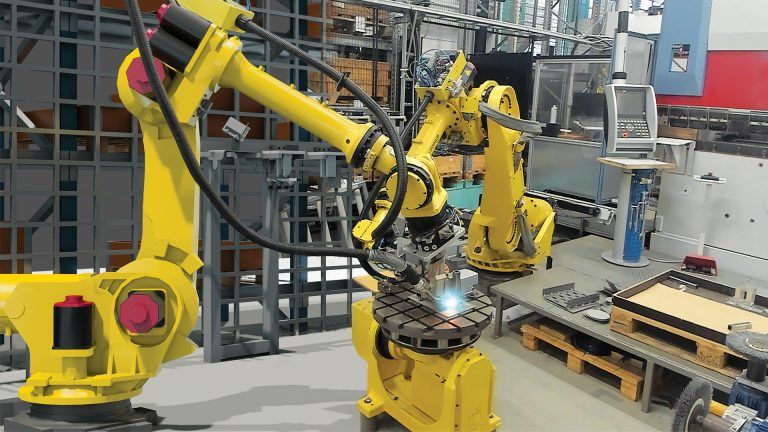
Understanding digital twins in manufacturing
Digital twins go far beyond static models or simulations. They bridge the gap between virtual and physical systems, offering real-time insights and control. But with so many definitions floating around,...
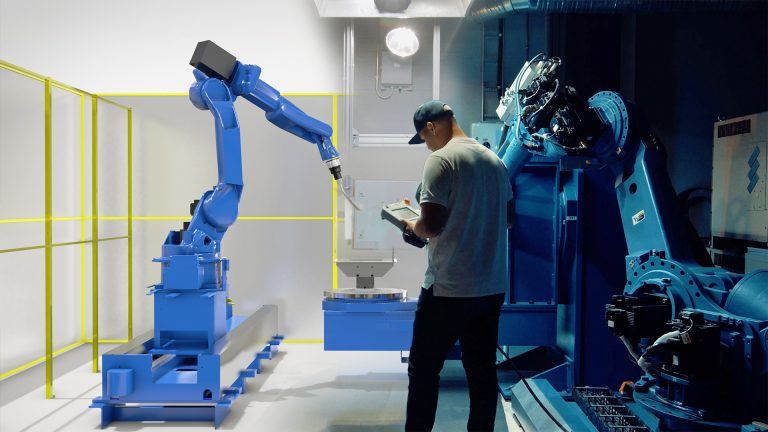
Tackling the manufacturing skills shortage with simulation and robot offline programming
The manufacturing industry is grappling with a significant skills shortage, exacerbated by the pandemic and an aging workforce. According to The Manufacturing Institute, 78% of companies are concerned about this...