Hyperautomation for Manufacturers and The Role of Simulation
The road to hyper-automation in manufacturing requires strategic planning and decisions however, it is also important to realize that manufacturing simulation is critical to the successful implementation of hyper-automation.
The concept of Industrial Automation has been around for several years and continues to be the main agenda for manufacturers globally. With the help of machines, robots, conveyors, AGVs, controls, sensors, and more modern equipment and digital solutions, repetitive work is being automated. When it comes to Automation, it is not just about automating the processes on the production floor but also other tasks around it performed in the office. This is mostly referred to as Robotic Process Automation (RPA) which takes on high-volume, routine transactional tasks that are mundane for humans.
The question however is… What’s next? It seems that the next step is to make sure that all these processes and sub-processes that are automated but remain unsynchronized are well integrated and closely knitted. The term used for this process defined by Gartner is ‘Hyperautomation’.
According to Gartner, Hyperautomation is a business-driven approach to identify, vet and automate as many business and IT processes as possible. It requires the orchestrated use of multiple technologies tools and platforms, including RPA (Robotics Process Automation), low-code platforms, and process mining tools.
Hyperautomation is being seen in customer service functions, Human Resources activities, and wherever else there are routine calculations to perform, forms to complete, or records to update. In manufacturing its role is not only in the office but also out on the factory floor.
Manufacturing Industry – The Journey to Automation
Manufacturing has been adapting the principles of the fourth industrial revolution, often abbreviated to Industry 4.0. This wave of change is characterized by advanced and inexpensive sensor technologies, communications platforms, and powerful analytics tools. Together, these tools have been providing deeper insights into manufacturing operations, in turn boosting productivity, raising quality, and improving the utilization of resources.
In most factories implementation of manufacturing automation proceeds unevenly. Typically, robots, CNC machines, and automated lines occupy part of the factory while elsewhere machines and handling systems still rely on human workers. Manufacturers must prioritize their investments to maximize returns but finding and making improvements is never easy.
Into this patchwork environment, comes manufacturing simulation and digital twins. Manufacturing simulation is a tool for modeling factory operations. It can be applied to just a single production cell or the entire shop floor with the warehouse. The goal of manufacturing simulation is to either digitally recreate the current layout, which can guide optimization decisions, or help evaluate new equipment proposals.
A digital twin can grow out of a simulation. A digital twin is a complete recreation of part or all of a manufacturing operation. It can be fed with real-world data to aid decision-making, guide scheduling, and identify improvement opportunities, and it’s kept current with direct links to the physical factory. This gives managers and decision-makers a tool with which to evaluate how and where to make improvements and to measure the impact they will have.
Applying Hyperautomation to Manufacturing
How often do you see spreadsheets, printouts, and even handwritten lists being used in the factory? Almost certainly, too often. The very fact these tools are needed shows gaps exist in information flows.
As with RPA, hyperautomation is a way of pulling together disparate streams of automation and eliminating gaps in how information moves.
The factory probably has CAD for product design, CAM for CNC machine programming, ERP for procurement and production scheduling, plus a Quality Management System, a traceability system, a maintenance management system, possibly also tooling inventory systems, and asset utilization/OEE reporting systems. But how well do they work together, if at all, and how much human intervention is needed to provide those information “bridges”?
This is where hyperautomation is targeted. It’s about providing an overarching structure that connects and integrates the tools listed above and more. And once connections are identified and established, implementing tools like AI/ML will lead to yet further gains and improvements.
Enabling Hyperautomation in Manufacturing with Simulation
Hyperautomation can’t be implemented without a clear understanding of the operations, processes, and workflows being addressed. In manufacturing that requires visualizing, identifying, and recognizing problems such as bottlenecks created by how things are done now.
Thinking this can be done through simple observation – “managing by walking around” if you will – is a mistake. While some problems may be present continuously, many are transient: they result from specific combinations of orders, at particular times of day, or in response to combinations of other events. Hoping to detect all such conditions simply by taking a snapshot of what’s happening can only lead to errors and omissions in the hyperautomation initiative.
A better approach is to analyze the current, and possibly also proposed, operations with a manufacturing simulation tool like Visual Components. Raising the level of understanding of what’s actually happening, reduces risk and provides peace of mind. Leaders can then feel comfortable knowing that all possible conditions have been considered and that their plans are realistic and practical.
The road to hyperautomation in manufacturing is not simple. It requires strategic decisions, a clear framework, and defined steps… Here are the principal steps stakeholders should consider:
1. Identification – Understand why hyperautomation should be part of the future strategy and start planning the identification process. Break this into phases of hyperautomation for the whole production process. Begin by identifying which processes are more critical for automation and prioritize those.
2. Conceptual Designs and Iterations – After identification and planning, talk to relevant stakeholders. Use conceptual simulations for deeper insights into the automation of specific activities and the subsequent effects on the rest of the production system.
3. Simulations – Once initial concepts are set, begin visualizing the digital models in detail and verify/validate that automation is optimizing the flow. (It’s critical to ensure the automation plans are streamlining the processes and not slowing them down.)
4. Virtual Commissioning – Integrate the virtual simulations with physical controls, ensuring the digital models function as real setups. The time needed to do this is justified by producing models that accurately replicate the real work, enabling the identification of bottlenecks and other issues.
5. Procurement – When buying automation equipment, take hyperautomation goals into account. Consider what data would be beneficial and how it could be captured. Look also at interfaces to tools like ERP, traceability systems, and QMS, and ensure these systems are well-integrated with a clear two-way communication stream.
6. Physical Commissioning – This is the activity of installation and integration to ensure the setup runs like simulations. The more effort that is invested in virtual commissioning the faster this step will be completed.
7. Delivery – Start production with automation links established and operational.
Simulation: An Essential Element of Hyperautomation
Reviewing the implementation process and steps detailed above, it’s clear that simulation is integral to steps 1 through 4. Given this reality, it seems reasonable to state that hyperautomation in manufacturing requires simulation if it is to be successful. Visual Components was a pioneer in the field of 3D simulation, using it to help manufacturers and automation equipment integrators find new ways to improve efficiency, productivity, and utilization. Today Visual Components is helping these customers implement virtual commissioning and build digital twins of their operations. Looking ahead, as companies begin to adopt hyperautomation, Visual Components stands ready to help.
Further reading
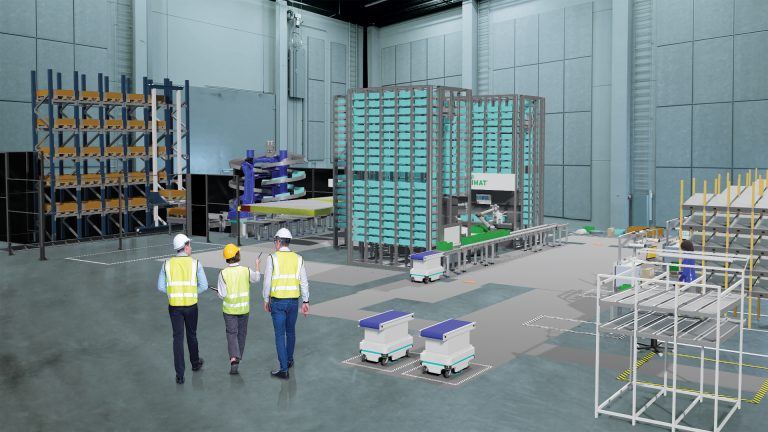
The future of automated manufacturing (and why humans still matter)
Automation in manufacturing has been evolving for decades, but its true impact isn’t in replacing people, it’s about making them more capable. We spoke with Mika Anttila, one of Visual...
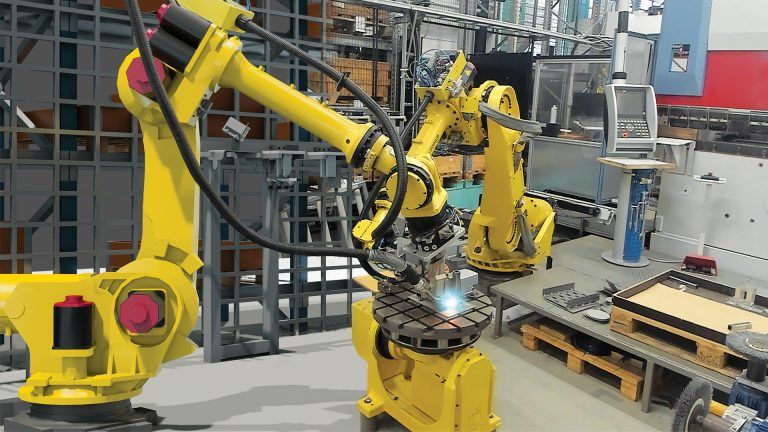
Understanding digital twins in manufacturing
Digital twins go far beyond static models or simulations. They bridge the gap between virtual and physical systems, offering real-time insights and control. But with so many definitions floating around,...
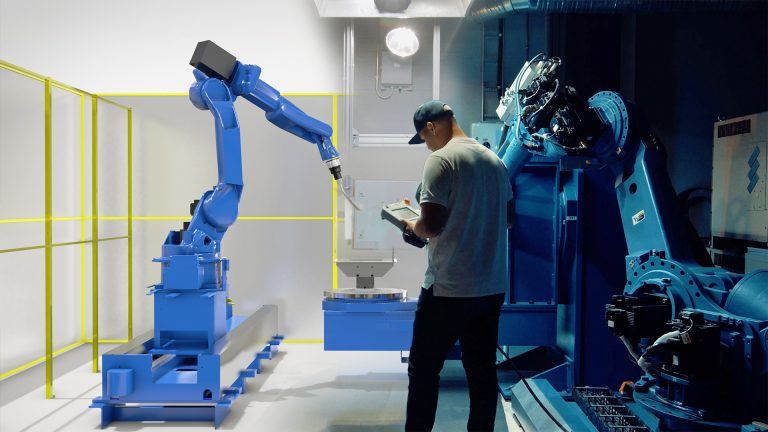
Tackling the manufacturing skills shortage with simulation and robot offline programming
The manufacturing industry is grappling with a significant skills shortage, exacerbated by the pandemic and an aging workforce. According to The Manufacturing Institute, 78% of companies are concerned about this...