How robot offline programming drives efficiency in high-mix, low-volume production lines
Frequent changeovers and small batch sizes can slow down production, but they don’t have to. With robot offline programming (OLP), manufacturers in high-mix, low-volume production can program robots 10 times faster without stopping production. See how companies are using OLP to keep up with demand, reduce downtime and stay competitive.
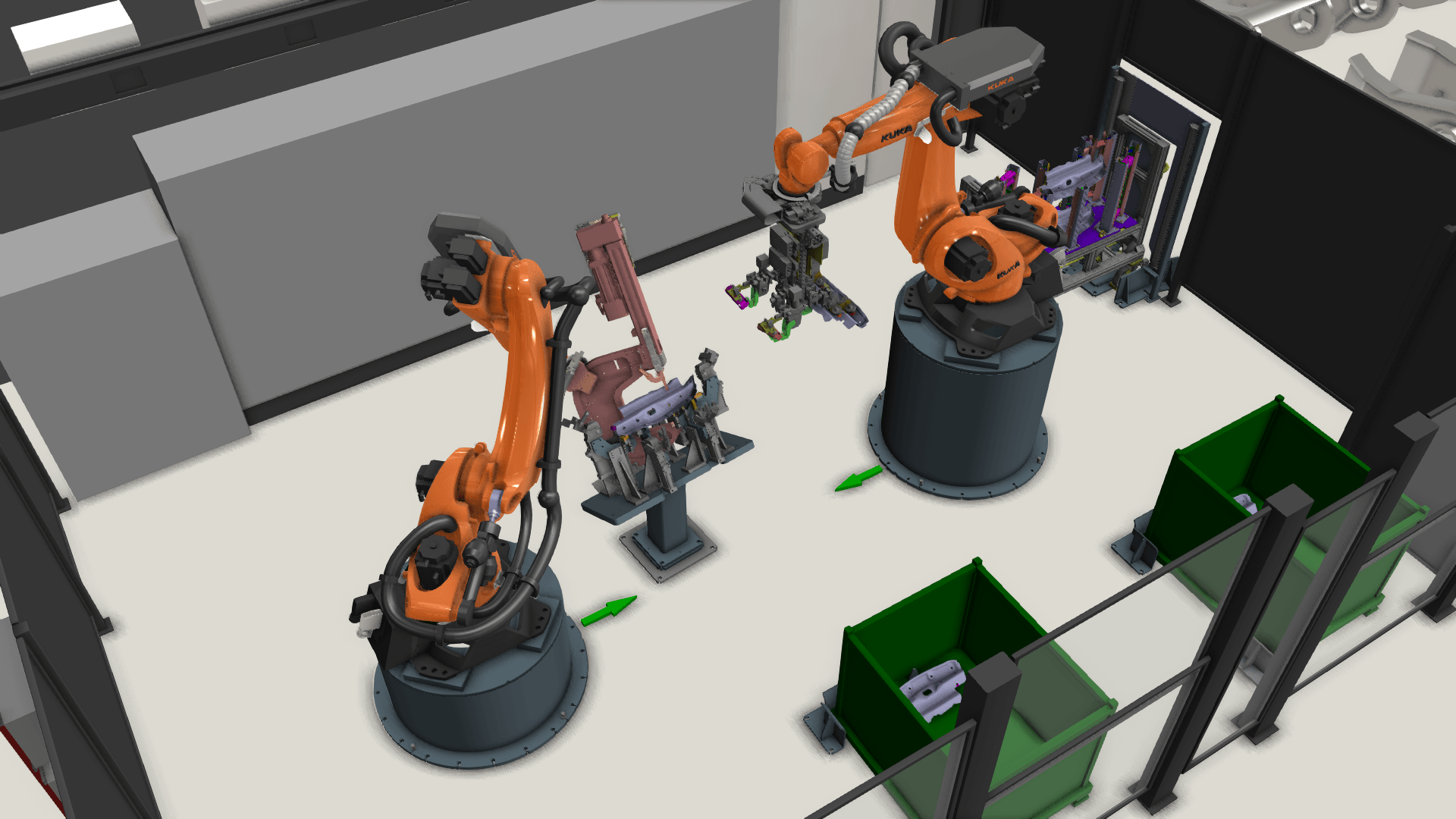
In high-mix, low-volume production, the ability to adapt quickly can make all the difference. Frequent product changes, unpredictable demand and complex workflows make traditional robot programming slow, expensive and hard to scale. Manufacturers need a way to keep operations moving smoothly, respond to new orders faster and make better use of their resources.
Manual programming methods often fall short in addressing these challenges, causing delays and disrupting workflows. This is where robot offline programming (OLP) steps in, offering a faster, more flexible approach that allows manufacturers to program robots without interrupting production.
Challenges of manual robot programming in high-mix, low-volume production
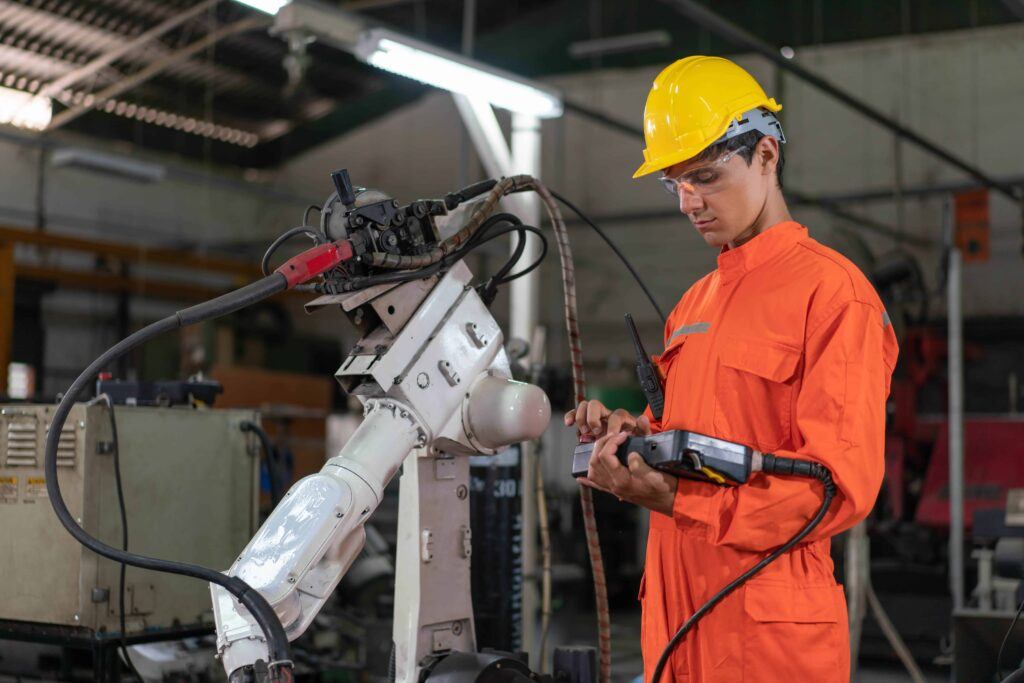
While traditional robot programming has long been the industry standard, it struggles to keep up with the demands of high-mix, low-volume production. Manufacturers in industries like heavy machinery, welding and metal fabrication must frequently adjust robot programs to accommodate new product variations, but manual methods are slow, costly and inefficient.
Each new part or variation requires fresh programming, often taking hours or even days to complete. Since robots must be taken out of operation for teaching, these delays add up, disrupting workflow and slowing down deliveries. Scaling production is another challenge, as manufacturers often rely on a limited number of skilled programmers, creating bottlenecks that hinder flexibility.
Additionally, manual programming becomes increasingly time-consuming as product designs evolve. Adjusting robot paths and parameters for new layouts or product changes can lead to production downtime, lost revenue and higher labor costs.
To overcome these inefficiencies, manufacturers are adopting digital solutions like robot offline programming to optimize robot programming, maximize automation and stay competitive in a rapidly evolving market.
How robot offline programming transforms high-mix, low-volume production
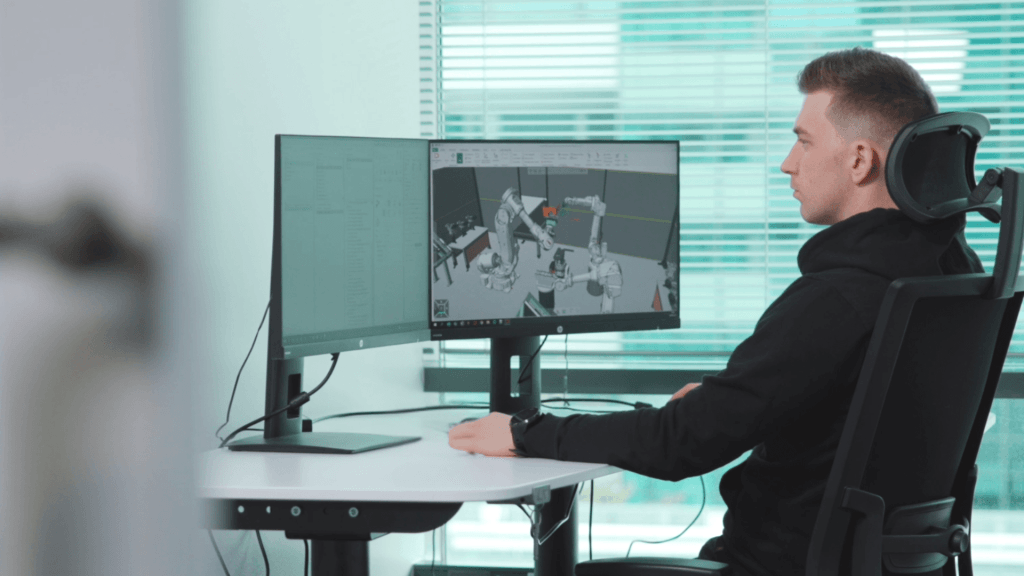
Robot offline programming (OLP) allows manufacturers to develop, test and refine robot programs in a virtual environment without stopping production—that’s where the “offline” comes from. Unlike traditional programming methods, where robots are manually taught on the shop floor, OLP shifts the process to a digital space, enabling manufacturers to create and validate robot programs before deploying them.
By simulating real production conditions, OLP helps manufacturers optimize robot paths, catch potential issues like collisions early and maintain consistency across production runs. This improves accuracy in applications like welding, assembly and material handling while making it easier to update robot programs for new product designs, process improvements or layout changes.
By maximizing robot utilization, robot offline programming improves productivity, lowers costs and makes high-mix, low-volume production more scalable and efficient in a fast-changing manufacturing environment.
Real-world applications of robot offline programming
Manufacturers worldwide are leveraging Visual Components OLP software to improve efficiency in high-mix, low-volume production. Here are some success stories:
Duun Industrier pre-programmed a robot cell to maximize efficiency
Duun Industrier, a Norwegian heavy machinery manufacturer, pre-programs its welding robot cells using Visual Components OLP software. This approach ensured their new robotic welding station was operational from day one with minimal rework, delivering rapid ROI.
It is important for us to get started as soon as possible with programming for this new robot cell and not to disturb the existing robot cell system. The physical robot will be delivered here in about one month and we have a desperate need to start programming the Yaskawa ArcWorld robot cell, so it is up and running from day one.
Rolf Even Duun, CTO at Duun Industrier
AMI Attachments reduced programming time by 70%
AMI Attachments, a North American heavy equipment attachments manufacturer, reduced programming time by 70% with Visual Components OLP software, increasing production efficiency while addressing labor shortages.
Creating and verifying a program completely from scratch on the shop floor would take at least two weeks. I can do this offline in a few days. After sending it out to get verified and touched up, we’re looking at a total of about four days. This means we gain about a week and a half. It’s a lot more repeatable, accurate and efficient. The program is clean, easily readable by everyone and everything is a lot cleaner and straightforward.
PJ Muker, Robotics Supervisor and Lead Programmer at AMI Attachments
Bunorm Maschinenbau optimized welding quality and efficiency
Bunorm Maschinenbau, a full-service welding supplier, uses Visual Components OLP software to program and optimize complex parts before production. This leads to faster programming and improved weld quality, even for small batch sizes.
You can see that with these 3 statements, I just created 41 lines of program. Without Visual Components OLP, we wouldn’t consider it to be efficient enough with the robot if we were to program it by hand on the controller.
D’Angelo Michael, Strategic Welding Solutions Manager at Bunorm Maschinenbau
Berlin Gardens improved efficiency by 80%
Berlin Gardens adopted Visual Components OLP software to streamline robotic welding, cutting programming time by 80% while improving quality and accuracy.
The biggest difference was the amount of points programmed by simply selecting a joint in the software. When programming point to point with the pendant before everything was very repetitive. With the software everything can be controlled with the same movements each time.
Derrick Yoder, Aluminum Production Manager at Berlin Gardens
Ponsse achieved 10 times faster robot programming
Ponsse, a Finnish forestry leader, reduced robot programming time from ten days to one by implementing Visual Components OLP software, significantly boosting productivity.
Offline programming makes things much faster and easier when robot programming can be done outside of production system without stopping production. Before, we had to make the necessary adjustments during the weekend before the production continued on Monday.
Asko Haataja, Head of Robotics Team at Ponsse
VOLVO Construction Equipment maximizes manufacturing flexibility with jigless welding
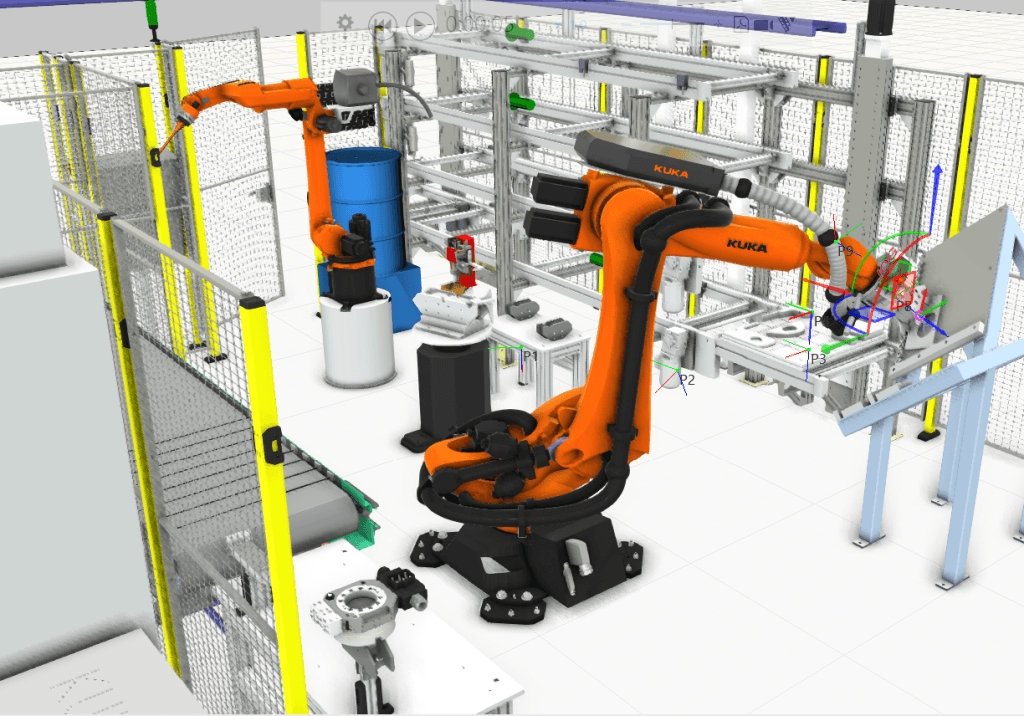
VOLVO Construction Equipment uses Visual Components OLP software to quickly generate robot programs, enabling jigless welding for 30 low-volume items in a continuous one-piece flow.
We wanted the best technical solution and software that is compatible with as many robot brands as possible. Visual Components OLP software is very visual and intuitive to program.
Erik Åstrand, Welding Optimization Specialist at VOLVO Construction Equipment
HT Laser boosted productivity in complex, high-mix metal fabrication
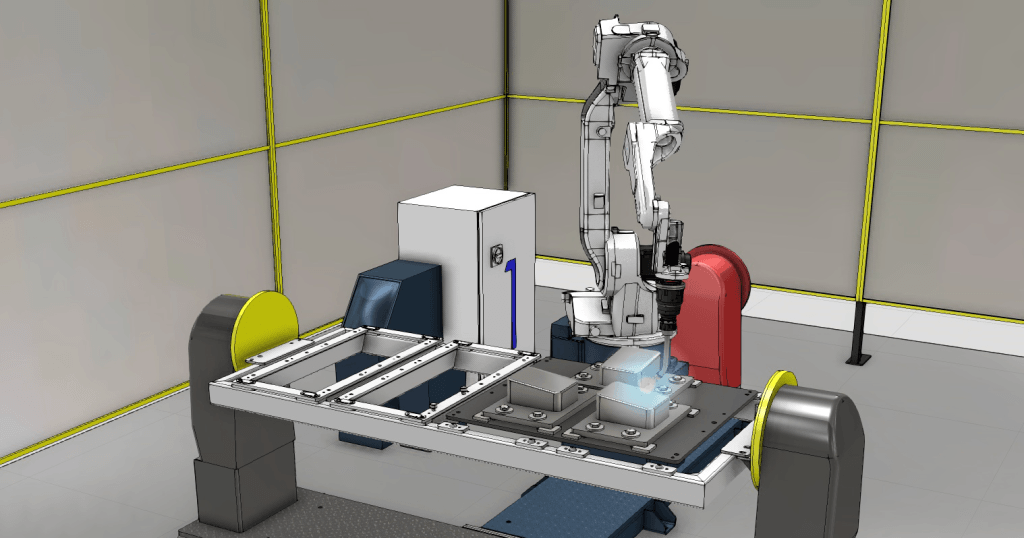
HT Laser realized significant time savings with Visual Components OLP software, eliminating production stoppages and enabling safer, more efficient welding operations.
The biggest benefit is time-saving as programming can be done without stopping production and expensive machines. Timesaving is also achieved by certain software macros that speed up the programming process. Offline programming also solves the problem if the welded piece is large or located in a place where it is difficult or unsafe to climb.
Janne Tuominen, Product Development Manager at HT Laser
AFRIT doubled production output
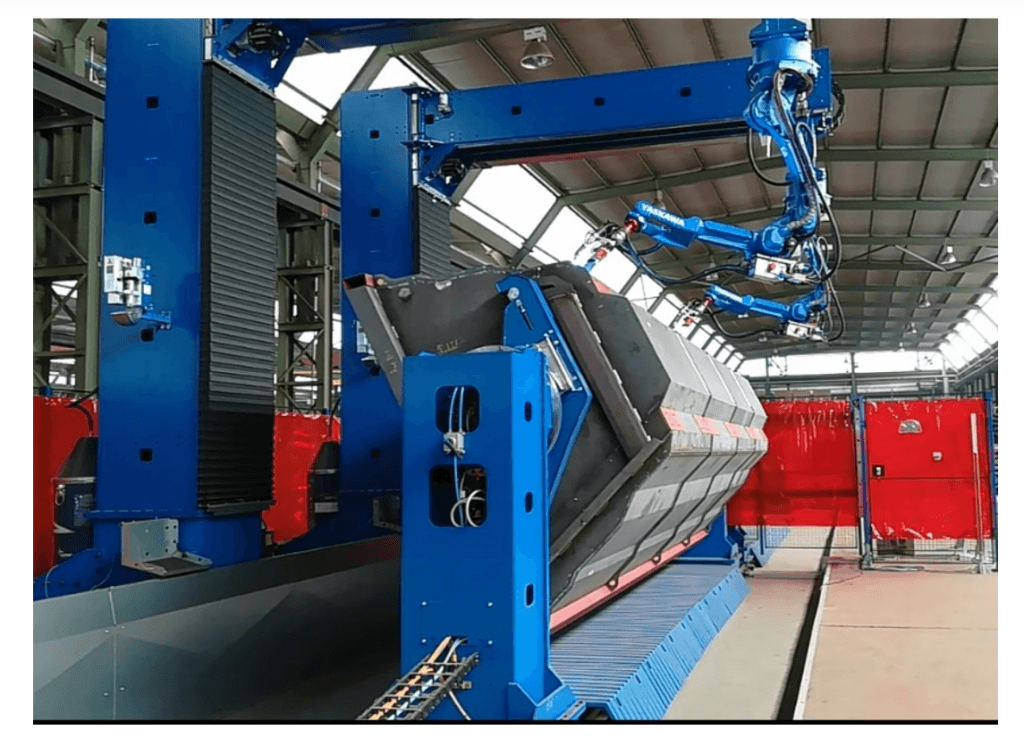
AFRIT, a South African trailer manufacturer, reduced manual programming labor hours by 80% and increased output from 8 to up to 20 bins per day using Visual Components OLP software.
Our parts are more consistent as well as the repeatability of welding has improved significantly. We have more time to improve welding and other systems because of the time saved by not needing to do manual programming and touch-ups on the programming.
Ferdi Beukes, Mechatronic Engineer at Afrit
Why OLP is the future of high-mix, low-volume production
OLP isn’t just a tool for reducing downtime, it also plays a key role in improving overall production adaptability in the broader context. By integrating OLP into manufacturing workflows, companies can create a more streamlined, data-driven approach to automation that extends beyond programming.
One key advantage is better coordination between engineering and production teams. Since OLP software allows programs to be developed and validated in a virtual environment, engineers can collaborate on robot tasks before they reach the shop floor. This reduces last-minute adjustments and ensures that robot operations align with production schedules, minimizing disruptions.
OLP also supports data-driven decision-making. Many modern offline programming tools integrate with simulation and analytics software, providing insights into robot performance, cycle times and process efficiency. This data helps manufacturers fine-tune robotic operations, balance workloads and identify areas for improvement before issues impact production.
Another benefit is the ability to scale automation more effectively. As manufacturers introduce new product lines or expand production capacity, OLP makes it easier to bring additional robots online without lengthy programming delays. Standardized and reusable robot programs allow businesses to replicate proven processes across multiple facilities or production cells, ensuring consistency at scale.
Additionally, OLP complements other digital manufacturing technologies, such as AI-driven optimization and IoT-enabled predictive maintenance. By integrating offline programming with real-time production monitoring, manufacturers can continuously refine robot operations based on actual performance data, improving long-term efficiency and reliability.
By adopting OLP as part of a broader automation strategy, manufacturers don’t just solve immediate programming challenges, they create a more agile, scalable and data-driven production environment. This helps businesses stay competitive in high-mix, low-volume production while preparing for future advancements in robotics and digital manufacturing.
Ready to improve your production efficiency? Contact us to learn more about implementing OLP in your production workflow.
Further reading
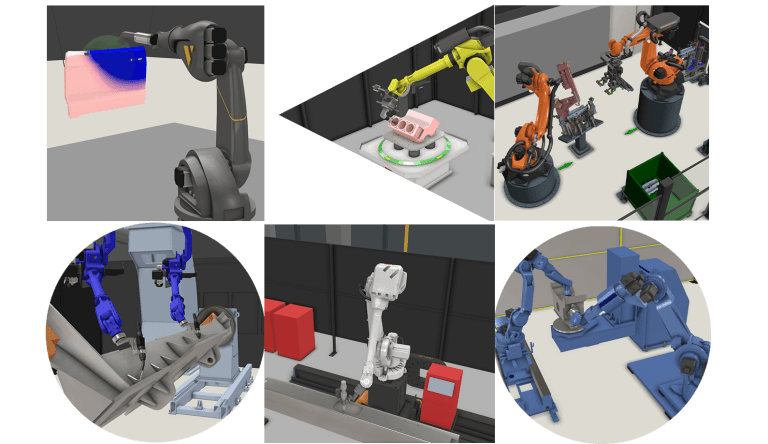
Robot programming for industrial processes with Visual Components OLP software
Robot programming is advancing with offline programming, enabling manufacturers to optimize robotic tasks virtually without disrupting production. This minimizes downtime, improves accuracy and streamlines processes like welding, spraying, processing and...
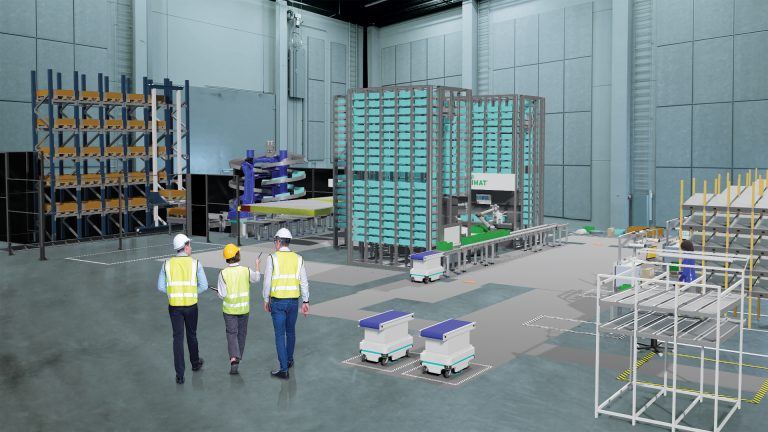
The future of automated manufacturing (and why humans still matter)
Automation in manufacturing has been evolving for decades, but its true impact isn’t in replacing people, it’s about making them more capable. We spoke with Mika Anttila, one of Visual...
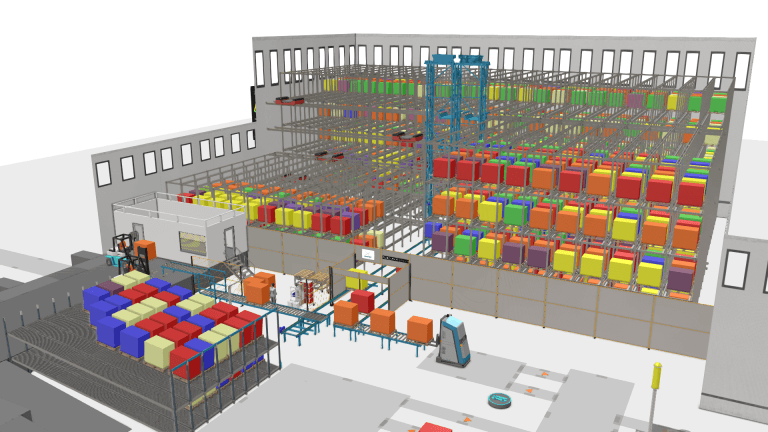
Smarter warehouse planning starts with simulation
How can businesses design warehouses that operate efficiently from day one while keeping labor costs and other expenses in check? The key is smart planning and validation with simulation tools...