Design for Manufacturability
Find out how avoidable mistakes can be minimized with better coordination and communication during the planning phase of new manufacturing projects.

We all make mistakes. It’s part of the experience of being human. But it can be painful to watch avoidable mistakes come to life, such as the manufacturing engineer who walks into their production area one morning to find a worker carrying boxes from one end of a stationary conveyor belt to the other, boxes of inventory piling up in a walkway, and QA workers disassembling parts by the hundreds. For product design and production teams, avoidable mistakes can be minimized with better coordination and communication during the planning phase.
The View From the Factory Floor
Visiting a factory helps most product teams to understand how their designs translate into production and the huge amount of work and resources that go into making their product. It also helps them to understand the pressures that production teams face and operational realities of a plant floor.
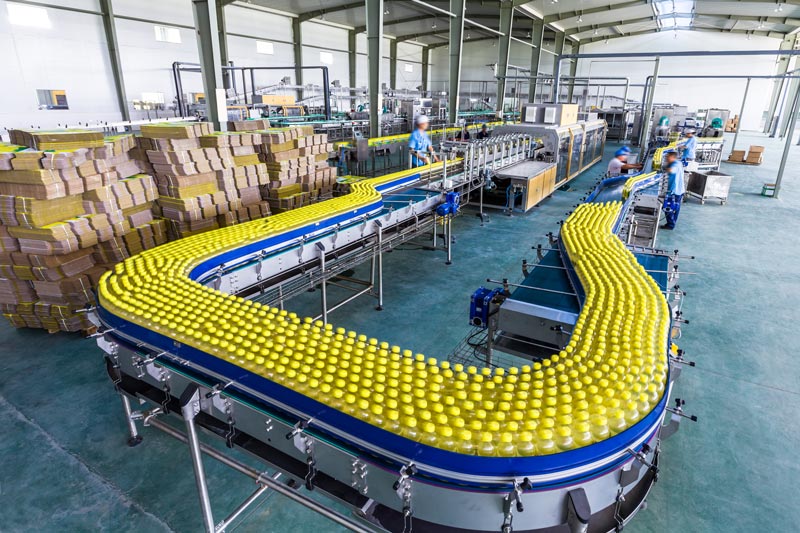
A plant manager’s job can vary from putting out fires to looking for ways to improve throughput, reduce costs, and eek out 2% performance improvement in daily capacity. Some of the questions that plant managers ask themselves daily include:
- Are we spending too much time sorting sourced components?
- Why is boxing and packaging 35% of our process?
- Why is our total capacity only 90% of what we planned?
Most production facilities manufacture many types of products and have several ongoing production runs, with a constant cycle of new lines starting and old lines ending. Producing a new product with a new design isn’t a trivial task for production teams. In addition to making sure they can manufacture the new product to quality, cost, and volume requirements, they need to ensure they can meet their commitments for the other productions. It gets to be a pretty challenging task.
The Impact of Product Design on Production
To illustrate this, let’s review the effect that a complex new packaging design can have on the manufacturing process. For many consumer-packaged goods, the packaging is almost as important as the product itself. Packaging plays a critical role in branding, differentiation, and moving products of the shelf. Package designers and marketers expect a lot out of their packaging and put a lot of thought and effort into developing innovative packaging concepts with unique package die lines, printed graphics, and unboxing experiences. These complex designs also require a lot of effort from the production team to implement.
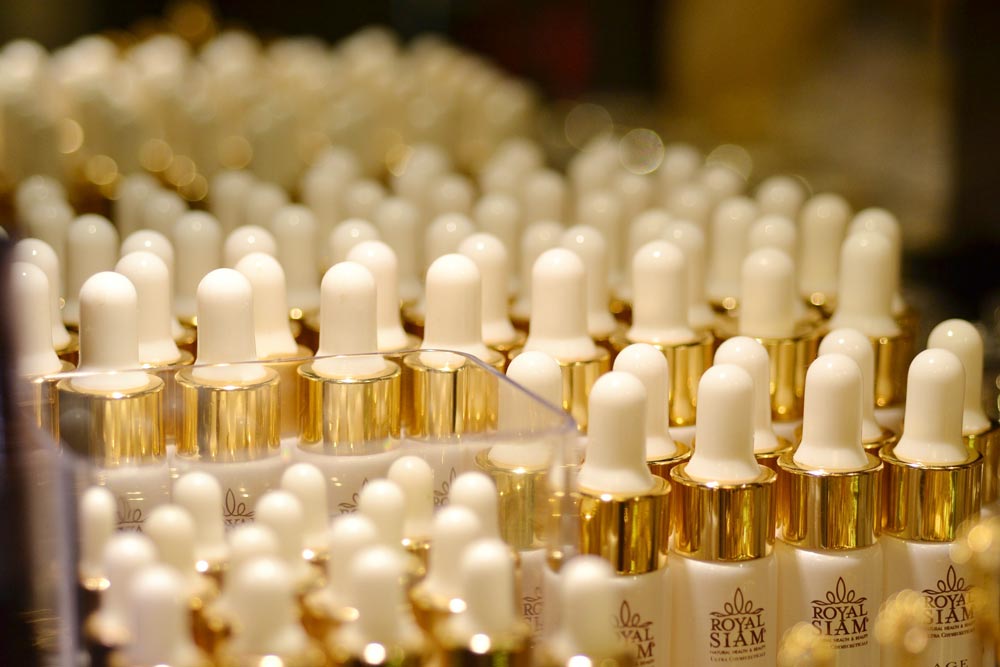
- On the production floor, this can mean a custom vacuum gripper, a capital expense to open the box. It might also require additional stations to manually load the items to ensure a flawless unboxing experience.
- A limited supplier base for the printed design means the boxes are delivered in pallets, which forces a change to intake procedures and requires additional floor space for storage.
- What if that same printed design included a custom coating? That treatment is subject to scratching on the final conveyor belt, which means either turning it off, or risk increasing rejects by 10% and reducing capacity.
If not properly planned, a package designed to increase sales by 2-3% can have a disproportionately negative effect on production – increased capital costs, constraints on the plant layout, and more stress on plant managers and production teams. This doesn’t make the design bad, but perhaps inefficient in achieving the overall goal.
Better Planning for Better Outcomes
This is an example of a real list of issues identified during a plant visit by a design team. They all have fixes that vary in cost and complexity; however, when making changes to a running production line, your options are usually limited, as is the impact of most fixes on total production.
That’s why it’s important for product designers and marketers to work closely with the production team during the design and planning phases – so they understand how product design will effect production decisions and operations.
For product design and production teams, avoidable mistakes can be minimized with better coordination and communication during the planning phase.
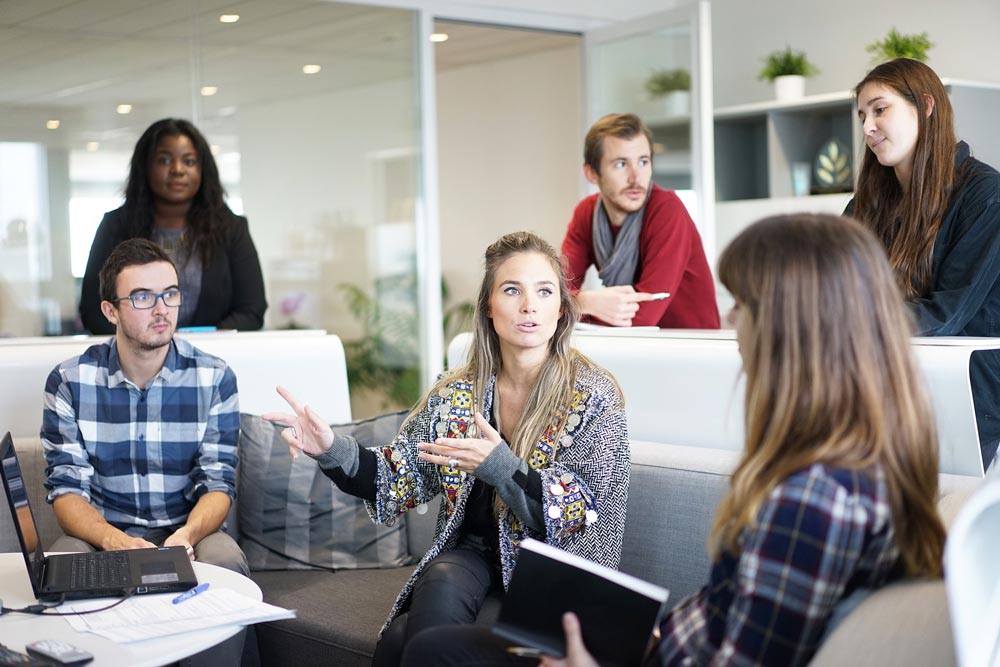
For the package design, the factory will ultimately make the design given to them. However, as was the case in this example, if the design team knew during the planning phase that their design would account for 30% of their production labor costs, they may have reconsidered the packaging, perhaps using a more standard design and instead focusing on the copy and graphics to reduce production costs.
A purchasing agent could take one look at the storage of incoming goods and know that their next RFP would have to include different shipping layouts. Instead of choosing a vendor based on a fraction of a cent part cost difference, the ability to integrate into the production process becomes more critical to new bids. A quick description and 2D drawing attached to a purchase order defining the packing and shipping constraints can reduce the required floor space by 10 sq. ft.
As for the scratches on the exterior of the package, this is a concern whenever moving things around. In this case, choosing a belt with a less abrasive surface or ensuring the belt did not make a 90-degree turn are both options. This may require a little more investment, but could result in a meaningful reduction in rejections.
Of course, with a running production line and the pressure to make daily quotas, your best option may be to go with what you walked into this morning. Have a worker pick up boxes and walk them to the other end of the conveyor belt.
Improve Your Planning With 3D Manufacturing Simulation
It’s not always possible to get the product team to visit the production floor, which is why 3D manufacturing simulation software is a great tool for product and production teams to collaborate and plan. Visual Components 3D manufacturing simulation software is purpose-built for manufacturing professionals to design, simulate, and communicate production designs and processes. It makes it easier for production teams to communicate production plans and helps product teams to visualize how their designs impact production decisions.
Further reading
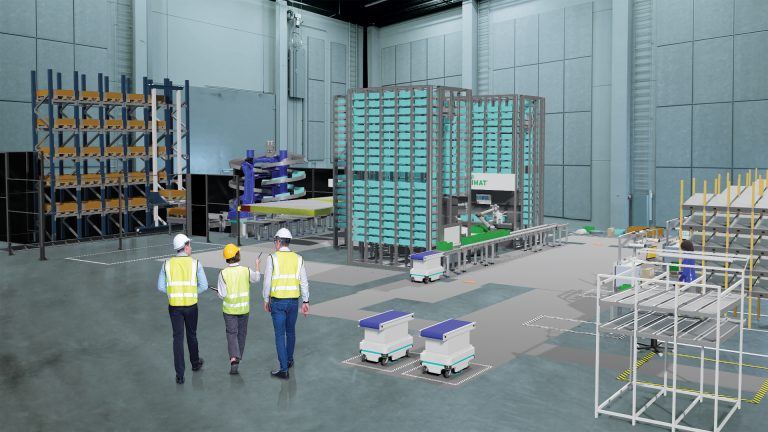
The future of automated manufacturing (and why humans still matter)
Automation in manufacturing has been evolving for decades, but its true impact isn’t in replacing people, it’s about making them more capable. We spoke with Mika Anttila, one of Visual...
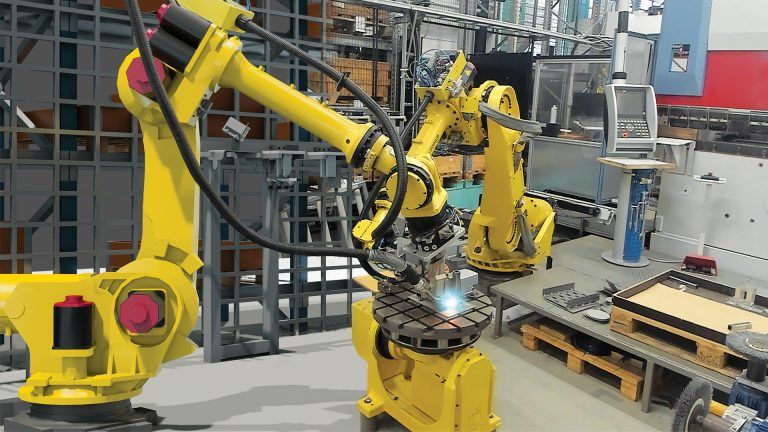
Understanding digital twins in manufacturing
Digital twins go far beyond static models or simulations. They bridge the gap between virtual and physical systems, offering real-time insights and control. But with so many definitions floating around,...
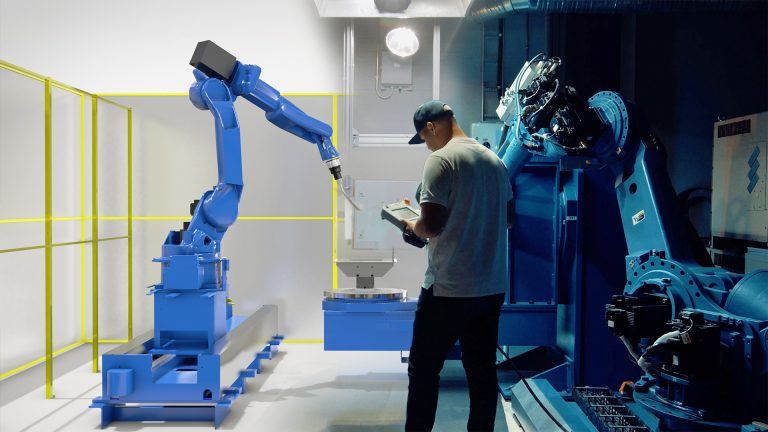
Tackling the manufacturing skills shortage with simulation and robot offline programming
The manufacturing industry is grappling with a significant skills shortage, exacerbated by the pandemic and an aging workforce. According to The Manufacturing Institute, 78% of companies are concerned about this...