An introduction to virtual commissioning
Virtual commissioning is reshaping the manufacturing landscape by employing computer simulations for testing and optimizing production systems before they’re physically built. This approach not only simplifies the setup process and reduces expenses but also boosts efficiency, elevates worker proficiency, and enhances factory output. Let’s dive deeper into what virtual commissioning involves and how you can utilize this technology to advance your manufacturing operations.
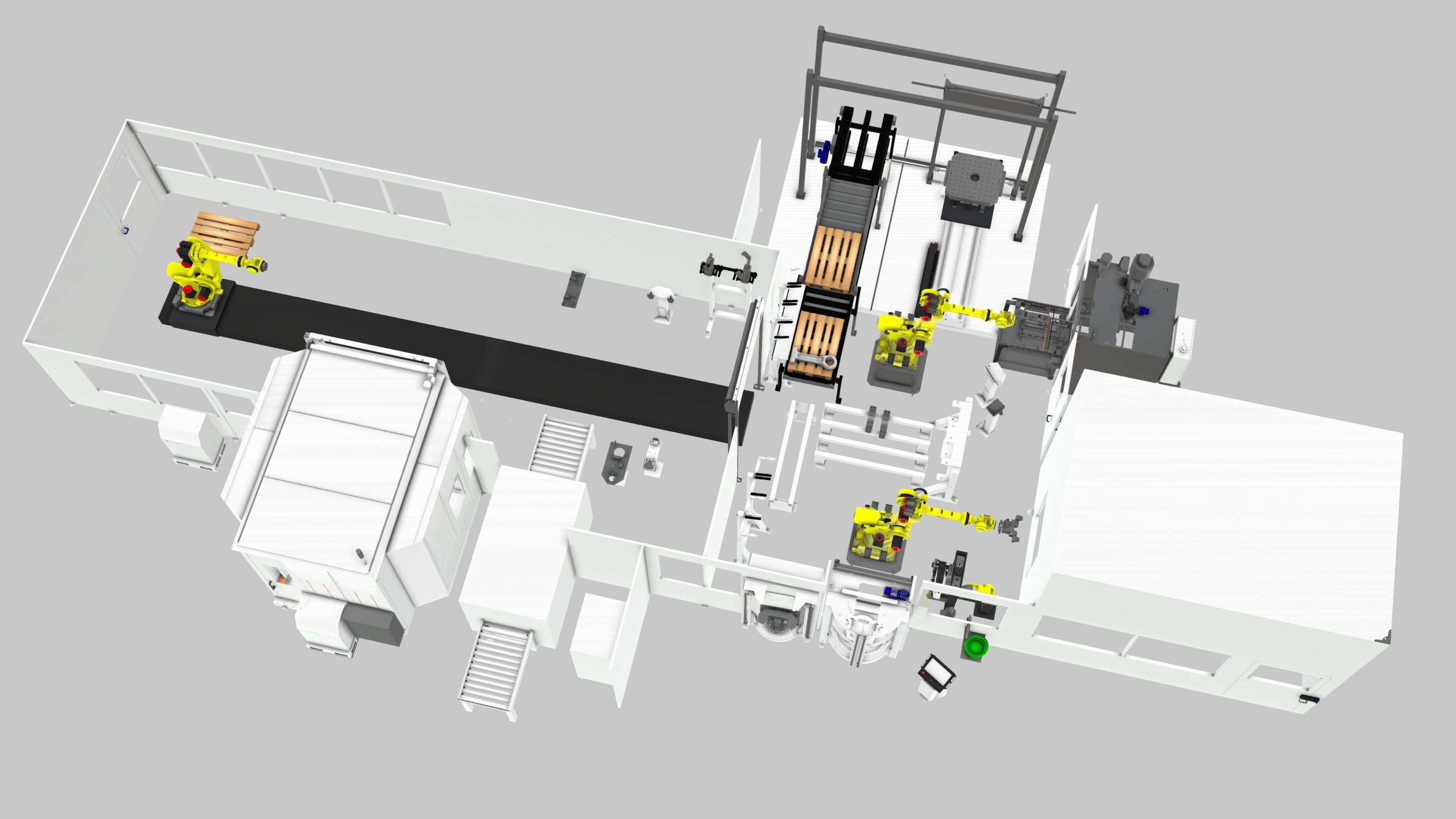
Virtual commissioning not only helps manufacturers meet the factory acceptance testing (FAT) date outlined in the project plan, but also ensures that they pass the FAT, and in some cases, even enables Virtual FAT. Often determined by plant shutdown schedules or product launches, missing the FAT deadline leads to costly delays and extensive blame-shifting. It’s a situation all project stakeholders strive to avoid, frequently necessitating extended working hours and performance trade-offs.
Analysis of the delays in these projects consistently points to commissioning as the main culprit. The problem is that historically it’s been impossible to test and debug control software until the hardware is physically complete.
Modern manufacturing simulation tools provide the answer. Here we’ll explain what virtual commissioning is, how to successfully perform it, and the benefits of doing so. In this article, we will cover the following:
- Software and commissioning
- The advantages of virtual commissioning
- A step-by-step guide to virtual commissioning
- Case studies
- Why virtual commissioning is the future
Software and commissioning
Since the advent of the programmable logic controller (PLC), manufacturing machinery and automated equipment have relied on software. Software reads sensors and sends signals to actuators, taking the machine through the required operation sequence.
Testing that software has always needed a machine to run it on, so only after the machine is physically complete can the process of getting the machine operational begin. As is always the case with software, there will be bugs, errors and omissions, and timing problems that all need fixing. This takes time and is very hard to estimate for the project plan. Almost inevitably, unexpected issues arise, and project progress slips.
Virtual commissioning reorders this sequence, reducing the impact of commissioning on the project critical path. In this section, we’ll explain what virtual commissioning is. Then we’ll explain how it relates to traditional commissioning and the Industry 4.0 concept of digital twins.
What is virtual commissioning?
A textbook would describe it as, “the act of setting up, testing, and validating a system’s design and operation in a virtual environment on a computer.” A more practical explanation is that it entails using software to test and validate control software before the physical machine is built.
The reason for doing this is to ensure that software and hardware are correctly set up and will function as intended once deployed in the real- world. Doing it before the machine is built removes the bulk of commissioning work from the project critical path, as it can happen in parallel with build or even earlier in the project.
Most providers of automation solutions will still have a commissioning phase to prove-out machine operation. However, much of the risk and uncertainty is removed by finding and addressing software problems earlier.
Creating the machine in software
A static representation of the machine is created using 3D CAD. However, to operate as the physical machine will, it needs the addition of kinematics – the motions it will perform – and a control system – the inputs, outputs, and timing or sequences.
Robots provide a particular challenge for kinematic modeling as they typically have five to seven axes and can move through space without the constraints of guideways and rails. Robot simulation and offline programming (OLP) software is available to help with these challenges.
Virtual machine or digital twin?
Those familiar with digital twins will note that this sounds like a description of such a virtual machine. There are however some important differences:
- The machine has not been physically built, so there is nothing to be a digital twin of: the virtual model stands alone
- A digital twin has data connections to the physical system it models or represents so real-world values can pass into the virtual system
- The goal of virtual commissioning on a virtual machine is to find errors and problems before the machine is built, whereas the goal of a digital twin is to replicate the physical system for testing and scenario evaluation
Once the machine exists and has been commissioned it’s possible to turn the virtual commissioning layout into a digital twin, or the digital model could be considered to be the original and the physical machine the twin or replicate of the virtual layout. This would increase the return on the time and effort invested by enabling virtual experimentation and testing even further. The digital twin could be used to test alternative ways to schedule a product or test different package sizes through a system. Our blog post on “Digital Twins and Virtual Commissioning” has more information.
The advantages of virtual commissioning
We have already touched on the reasons for performing virtual commissioning. Now we’ll take a deeper look at the benefits to machine builders and automation solution providers.
These include:
- Early detection
- Decreased lead time
- Cost saving
- Flexibility in design and implementation
- Training
- Improved safety
Early detection
A sensor in the machine detects the presence of a part. Until this happens the machine won’t cycle. However, a PLC can miss a pulse sent at the wrong time, leaving the machine sitting in a “wait” state.
A problem like this will be found and resolved during traditional commissioning. However, multiply by the number of sensors, actuators and lines of code it becomes clear significant time could be needed to get the machine fully operational.
Virtual commissioning will find this kind of problem too, but the time needed to modify lines of code will not delay the project: build can continue while the programmer finds and implements a fix. Moreover, by removing the time pressure, a better fix might be found that doesn’t add to cycle time.
This simple example serves to illustrate the point: virtual commissioning reveals problems sooner than would otherwise be the case.
For a more complex example, consider a project where robots are being installed on a production line. A small miscalculation of robot placement could leave it with insufficient reach for the allotted task. In this case solving the problem would take extensive rework and perhaps a new robot, delaying the project and increasing costs. However, virtual commissioning would enable detection before the robot was ever installed in the wrong location.
Decreased lead time
Commissioning can account for 25% of total project duration. Lead time can be reduced by performing a portion of this in parallel with build or even earlier when the mechanical design only exits virtually. In addition, early problem detection and resolution greatly reduces uncertainty in the project lead time, allowing builders to more accurately forecast delivery.
An additional benefit for the builder is that the equipment spends less time on the floor prior to FAT and shipping. This increases capacity, which if utilized, can mean significantly higher profits.
Cost savings
Rectifying problems with assembled hardware is always expensive. New parts may be needed, along with overtime working for their installation. If these problems are addressed at the design stage instead, significant cost overruns can be avoided. (This also improves accuracy in the budgeting process with less being allocated to ‘contingency’.)
Flexibility in design and implementation
Virtual commissioning increases opportunities for manufacturing innovation. Here’s how this comes about.
During traditional commissioning the team often sees ways in which the design could be improved. This might be to reduce cycle time by changing gripping sequences, to relocate components to shrink the equipment footprint, or to improve access for setup and maintenance. However, as the machine has been built, making such changes would be costly and cause delays.
When commissioning virtually, the impact to the project of incorporating new ideas into the design is much smaller. They will probably result in improved performance and/or maintainability and could even lead to cost savings.
Training
Maximizing ROI from a capital equipment project requires getting the machine or system running on the plant floor as quickly as possible. An important step in achieving this is training engineers, the maintenance team, and the equipment operators how to use and look after it.
In the traditional process, this training happens after the machine has been commissioned. (It usually takes place after the FAT.) In virtual commissioning, training can begin on the digital model of the hardware. While some hands-on training with the physical hardware is still usually desirable, if those involved are familiar with the logical sequences, locations of actuators, feeding and unloading systems, and so on, they are already some way up the learning curve.
Later, if the digital model was transitioned into a digital twin, it can be used for skills development and onboarding of new operators.
Improved safety
Equipment that moves, especially robots, can be very dangerous. In normal operation workers are protected by guards and interlocks but commissioning often requires these be open and overridden for visibility and access.
By proving out motion paths, and verifying sequences, timing, and exception handling virtually, less running in these conditions is needed and the risks are reduced.
A step-by-step guide to virtual commissioning
Having become very familiar with virtual commissioning, we suggest there are ten steps to go through.
- Understand why an accurate model is needed – The team must understand why model accuracy is paramount and commit to providing the required information. Errors or discrepancies will result in virtual commissioning not yielding less useful information. In such a situation any conclusions might be inapplicable or misleading when transferred to the real world.
- System analysis and definition – Start by gaining a clear understanding of the production system’s objectives and functionalities. Then all available technical documentation, specifications, and requirements related to the machinery and control systems.
- Model building – Create an accurate 3D model of the production system using a combination of CAD data and models from the Visual Components e-Catalog. (More than 3,000 components are available in our Visual Components e-Catalog.) Then integrate kinematic, electrical, and other relevant data to create a detailed digital representation of the planned machine or equipment.
- Control logic integration – Connect the PLC and the robot controller to the digital model. This allows virtual testing of control sequences, reactions, and overall system behavior. (In Visual Components, we provide connectivity to most widely used robot brands and PLC systems, like, KUKA, DOOSAN Robotics, ABB, Fanuc, OPC UA, Beckhoff, Siemens SIMIT and Siemens S7.)
- Simulate and test – Run the model through various operational scenarios to test its performance, and where possible, validate against real-world data. This should include testing both regular operations and exception or error situations to ensure the system can handle unexpected issues.
- Refinement – Use the results of the simulation runs to identify, and rectify any discrepancies or inefficiencies in the control logic. Then run the tests again to verify the model is more accurate. Repeat until the virtual model performs as desired.
- Safety and compliance checks – Ensure the control logic and system design function as needed and meet relevant industry standards and safety regulations. (Robot safety is an area that needs especially close attention.) These checks and tests are particularly important in industries with stringent safety and compliance requirements.
- Physical commissioning – Although it shortens it dramatically, virtual commissioning does not negate the need for this step. Tasks here are to: Transfer the tested and verified control logic from the model to the real-world system; Monitor the system closely during initial operations to ensure it behaves as expected.
- Continuous improvement – After the physical system has been running for a while, gather feedback and operational data. Compare this with the predictions from virtual commissioning and perform a post-implementation review to identify any gaps or areas for improvement. Use insights from this to further refine the model/digital twin and control logic.
- Documentation – Remember that virtual commissioning is not a one-off process. It can be revisited whenever changes are made to the physical system or when there’s a need for optimization. Document every step of the virtual commissioning process, from initial design to final implementation. This will support troubleshooting, future system upgrades, or scaling.
Case studies
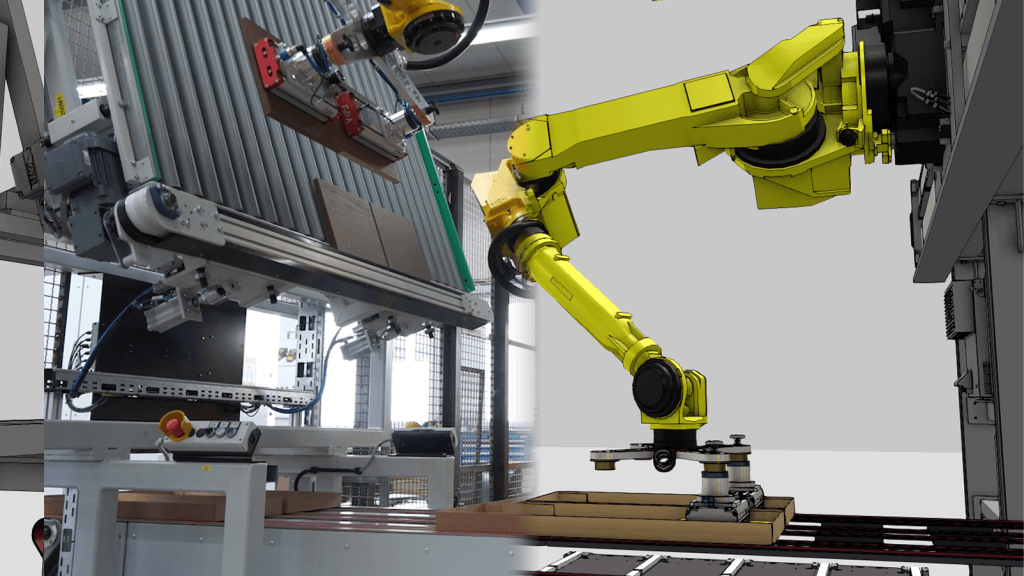
For readers interested in learning more, here are four real-world examples of companies that have successfully implemented virtual commissioning using Visual Components.
- Using simulation to identify automation opportunities in the manufacture of drive-thru windows
- Creating an accurate digital model of a factory
- Building a digital model of an automated cell
- Simulating packaging operations
Why virtual commissioning is the future
A digital transformation is underway in manufacturing, and that includes how machines and equipment are designed and brought to fruition. Sensors, controls and software are integral to this Industry 4.0 advance, and they will make future machines faster, more accurate and repeatable, and more versatile.
As these next-generation capabilities offer manufacturers opportunities to reduce waste and increase margins, the pressure for faster implementation will only grow. Virtual commissioning is therefore a key element in staying ahead of competitors and maximizing ROI from capital expenditure.
If you’re already creating digital twins, but not using that work for virtual commissioning, it might be time to rethink. If you’re still commissioning on the assembly floor, and still missing FAT deadlines, it’s time to rethink what you’re doing.
In both cases, Visual Components has the tools and expertise you need. Our Learning Path on “Using Visual Components for Virtual Commissioning” has detailed information, or contact us to learn more.
Further reading
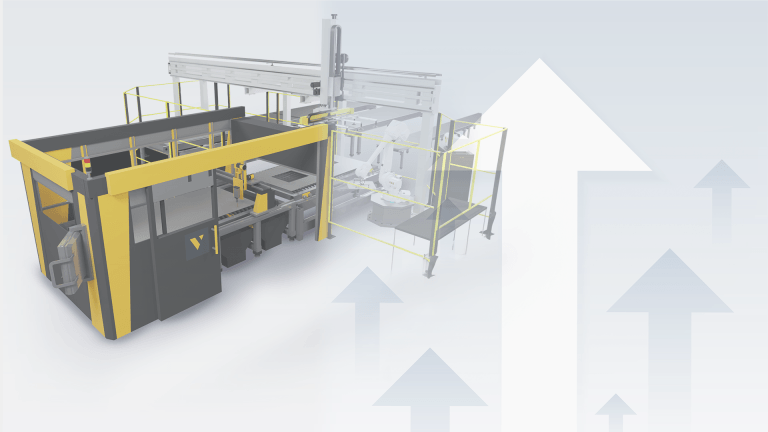
Boosting production line efficiency: a guide on improving production output
Production efficiency is the cornerstone of success in manufacturing. It measures the effectiveness of resource utilization in the manufacturing process, aiming to maximize output while minimizing costs and waste. The...
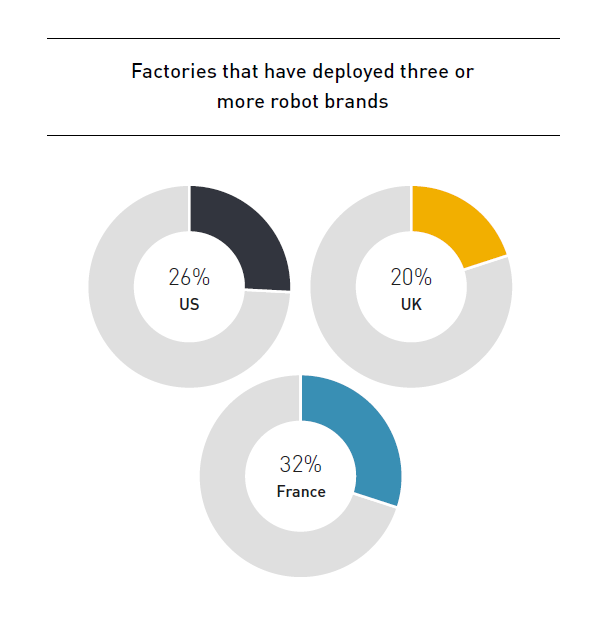
Are manufacturers really ready for the digital era? (survey results)
Legacy equipment and outdated practices can seem like relics from another age, especially as the world zooms ahead with digital innovations. Yet, they're more prevalent in the manufacturing sector than...
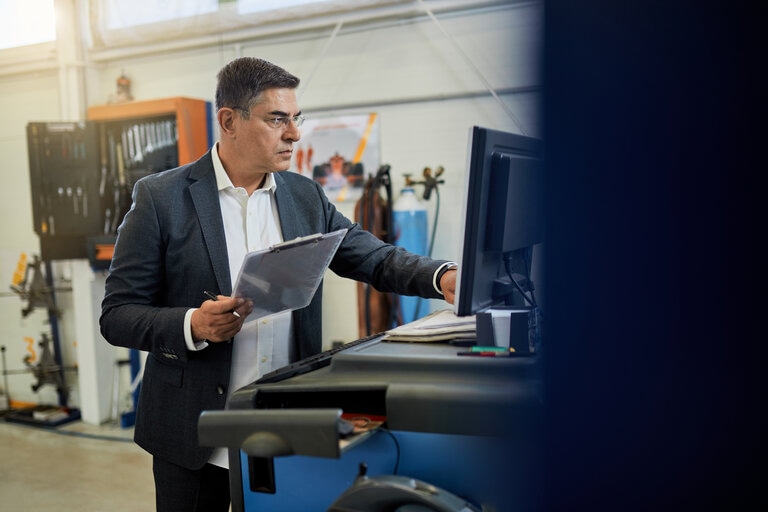
Considerations for CIOs in 2023: navigating sustainability, resilience, and human needs
In today's rapidly changing manufacturing landscape, Chief Information Officers (CIOs) face the challenge of navigating cost pressures while balancing human needs, the supply chain, and new production strategies and technologies.