How are manufacturers preparing for Industry 5.0? (Survey Results)
Industry 4.0 heralded an age of interconnectedness. Talk of the Internet of Things (IoT) became commonplace. The concept of “smart manufacturing”, or the “smart factory”, saw an increased interest in a future that lay in big data analytics, cloud computing, and the Industrial Industry of Things (IIoT), where manufacturers can make informed decisions to improve and optimize processes. Now with Industry 5.0 looming over the horizon, there has been much talk on what exactly will shape this new era of the manufacturing industry.
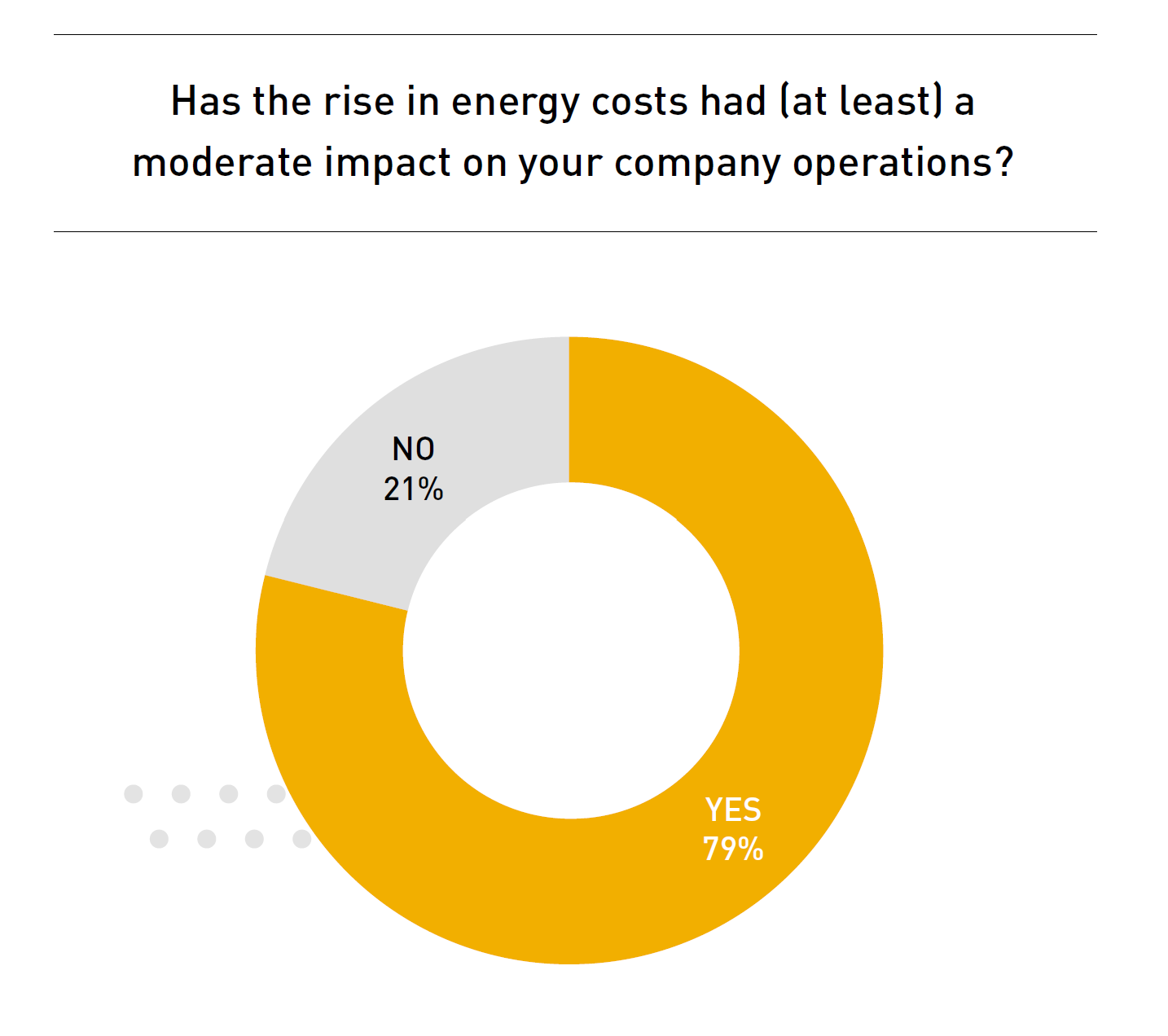
The common consensus amongst many manufacturing industry experts has been that 5.0 will put the worker’s well-being at the center of the production process, focusing on human-centric and sustainable innovation.
As this transition occurs, we at Visual Components collaborated with research house OnePoll to gauge the thoughts of 360 manufacturing decision-makers in the UK, US and Europe (Germany and France). Questions discussed their ongoing challenges, the levels of progress in facilitating cost savings, the state of play in adopting efficient and resilient processes and their current position in sustainable policies.
You can access the full report here that goes over all the results.
Continue on in this blog post, as we uncover some of the key findings from the study.
Almost half of manufacturers facing significant cost rises due to investment in people
47% of manufacturing decision makers say that their costs have risen by over 20% due to greater investment in people, while almost one-in-five (18%) say it is between 41%-80%
The ongoing Great Resignation, starting in early 2021 in the wake of the Covid-19 pandemic, has had a major part to play in these rising costs related to people. An average of nearly four million people in the US left their jobs monthly, and a record number of job openings still remain in 2022. The scale of the skills shortage issue was reflected by over a quarter (27%) of the respondents stating that between 21% and 60% of the workforce have departed the business since July 2021, in addition to normal levels of turnover.
Cost pressures are also materializing from elsewhere, with almost eight-in-ten (79%) saying that the rise in energy costs has had at least a moderate impact on their operations. As a result of these continued cost pressures, 44% say that between 21%-60% of their operations are being held back from being updated with new technologies.
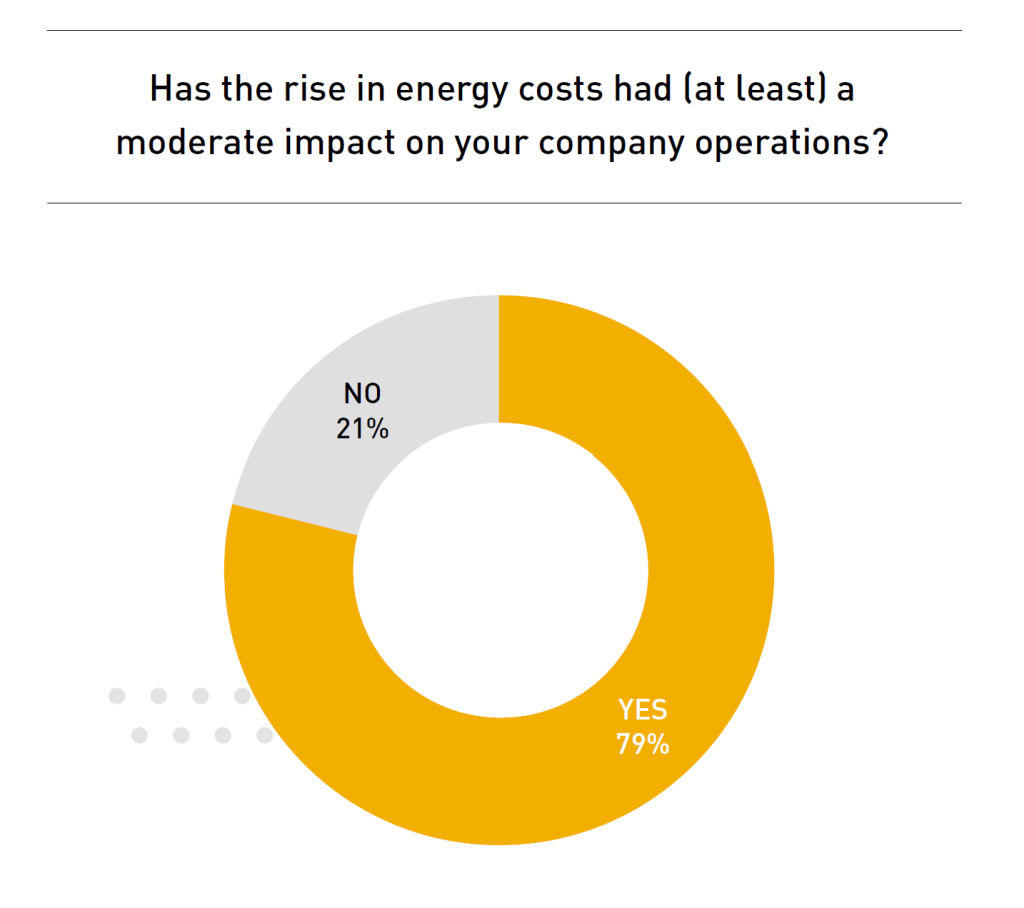
Technology training lacking for over half of manufacturers
In terms of technology adoption and use in the manufacturing environment, 71% of the respondents to the survey are at least fairly confident that their business has embraced Industry 4.0 concepts such as automation, artificial intelligence, and real-time data, while 72% believe their current solutions allow workers to be at the centre of the production process.
However, despite this adoption of Industry 4.0 concepts and technology, over half of manufacturing decision-makers admit that their organization is failing to invest in training on the use of new technologies (55%).
Economic climate holding back sustainability strategy for seven-in-ten manufacturers
Looking ahead, decision makers identify supply chain issues (44%) and the challenging economic environment (42%) as the biggest current challenges. This reveals how the industry is now moving away from Covid-19 and Brexit-related hurdles and is instead more concerned with growing issues in 2022.
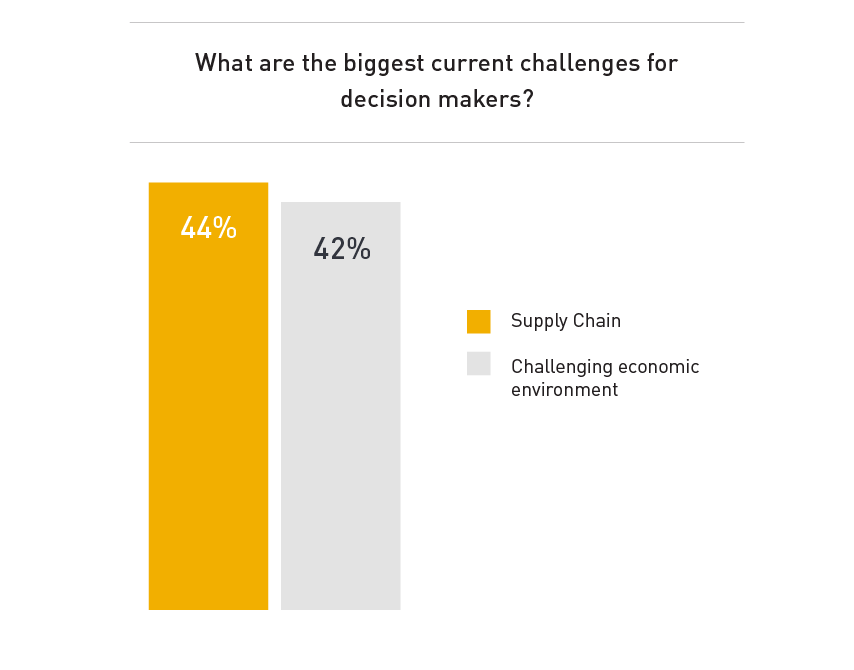
69% of manufacturing decision makers agree that their sustainability strategy has been restricted due to cost pressures, while 72% of respondents say that less than 50% of the materials used in the manufacturing process are sustainable.
79% also say that less than 50% of their manufacturing process is currently powered by renewable energy. This is despite 71% of decision makers being confident that their business will play a role in the global drive for net zero carbon emissions. Employees are also holding greater power in terms of driving sustainability strategies, with almost two-thirds (63%) stating this.
Find more results by accessing our full report.
Further reading
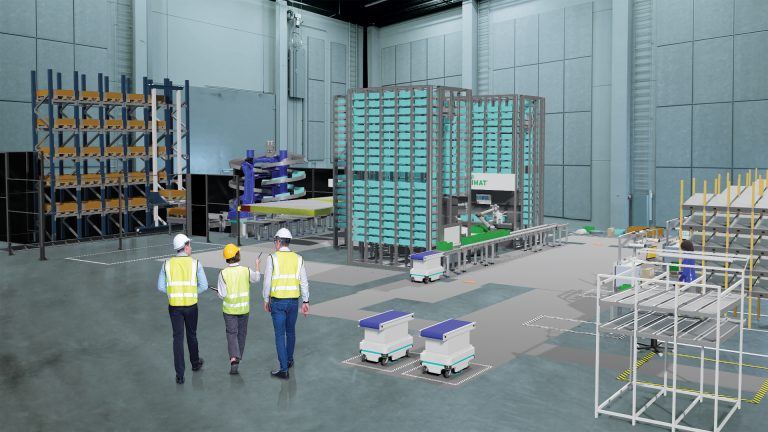
The future of automated manufacturing (and why humans still matter)
Automation in manufacturing has been evolving for decades, but its true impact isn’t in replacing people, it’s about making them more capable. We spoke with Mika Anttila, one of Visual...
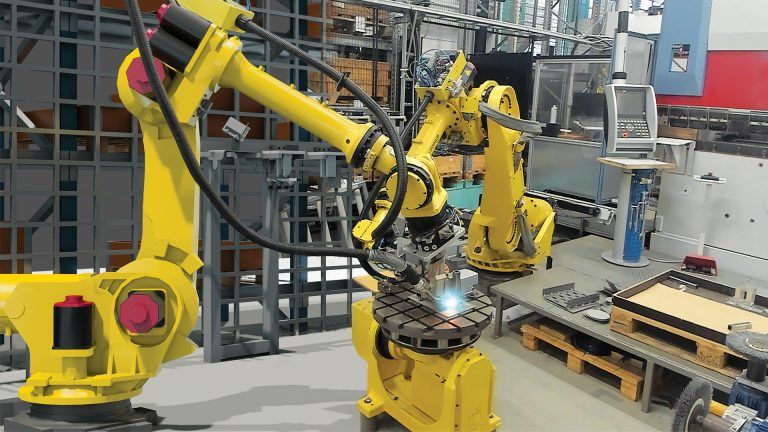
Understanding digital twins in manufacturing
Digital twins go far beyond static models or simulations. They bridge the gap between virtual and physical systems, offering real-time insights and control. But with so many definitions floating around,...
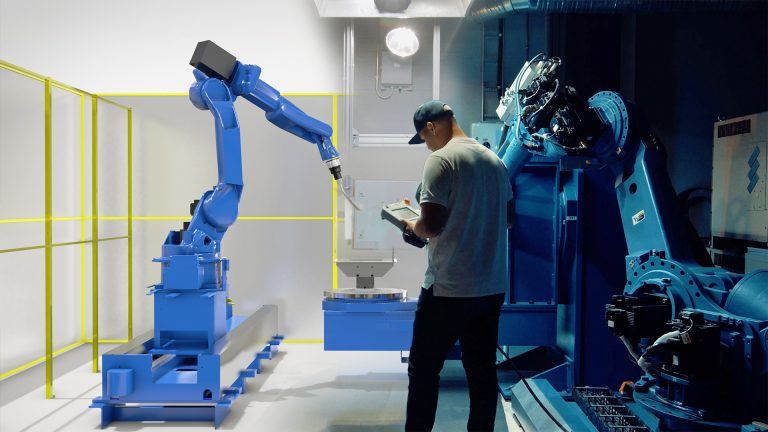
Tackling the manufacturing skills shortage with simulation and robot offline programming
The manufacturing industry is grappling with a significant skills shortage, exacerbated by the pandemic and an aging workforce. According to The Manufacturing Institute, 78% of companies are concerned about this...